The Impossible Is Possible: 30,000 Assets in 90 Days - A PMO Success Story
Introduction
In the 21st century, companies that focus on just design and operations will be left behind. Intelligent, efficient and optimized systems must keep evolving and need to be integrated into the ethos of how people work and think. This same thinking must be supported by management and designed to evolve based on proven intelligence, changing market demands and with the adoption of new equipment and technology. To achieve this, companies must initiate a proper asset performance management (APM) program to assess the operational performance and define a path to success.To develop a sustainable APM program requires a level of understanding and expertise. This article explores a case study that uses elements of the strategy management domain from one MSAT provider’s APM sustainability model to show the importance of preventive maintenance (PM) optimization in the development of a successful APM program. This company, Nexus Global, supports the Uptime Elements Framework to map the key areas of improvement within their five APM domains: leadership, work management, strategy management, investigation management and data management.
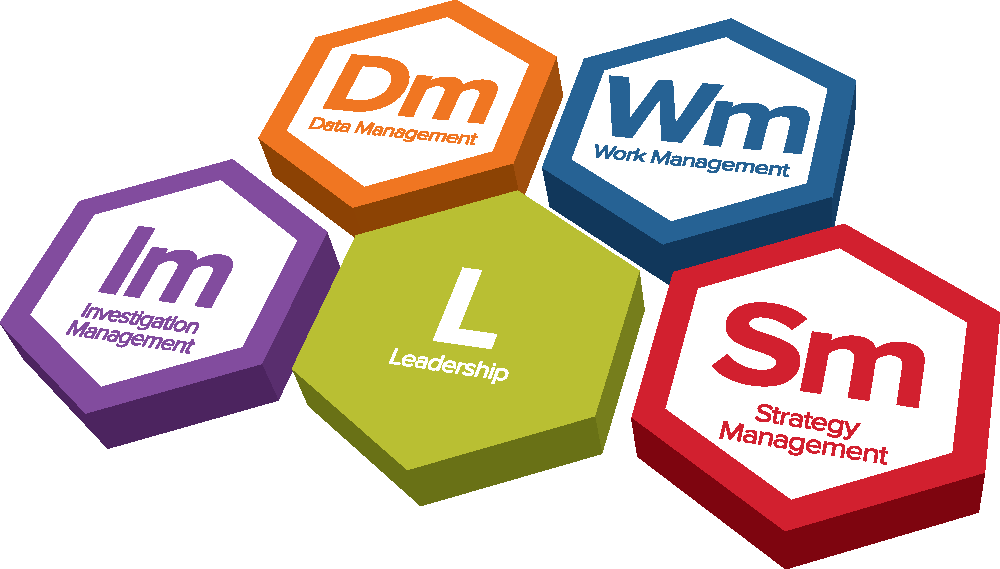

Background
In 2012, two investors funded the commissioning of two new 300MW steam turbines that use pulverized coal combustion technology in the Philippines. As part of the project, a key objective was to set up an improvement-driven work culture during the development and implementation phase of the asset management strategy. The new power plant design had close to 30,000 assets and an overall schedule that provided only 90 days to complete the project. Timely implementation of smart systems and investing in capable people were critical to setting the cultural direction for improvement.
Challenge
From the very early stages of the project, the investors wanted to avoid what many maintenance organizations face all too often – an excessive level of reactive or breakdown maintenance. This is expensive in both maintenance cost and downtime consequences. Excessive reactive maintenance also contributes to a negative performance spiral that, at best, counters other valuable improvement initiatives and, in the worst case, leads to an almost completely reactive environment.
When breakdowns occur unexpectedly, resources are deployed to reactive work at the expense of preventive maintenance. PMs are missed due to scarce resources being consumed by breakdowns. As PMs are missed, more preventable failures occur, expanding the level of reactive maintenance. In many cases, the situation is compounded by band-aid maintenance and morale is adversely affected by long working hours under high pressure and continual “firefighting.”
Approach
During the commissioning phase, work began on the asset management strategy development and continuous improvement systems. The window to complete the work was narrow and expectations were high. Consultants and engineers worked with operators and maintainers on the basics of reliability-centered maintenance strategy development. Terms like hidden, evident, value adding, cost effective, potential to function failure (P-F curve) and return to service plan became second nature to all involved. The project manager had one rule: Complication creates confusion. Focus on fundamentals; give clear direction with simple instructions.
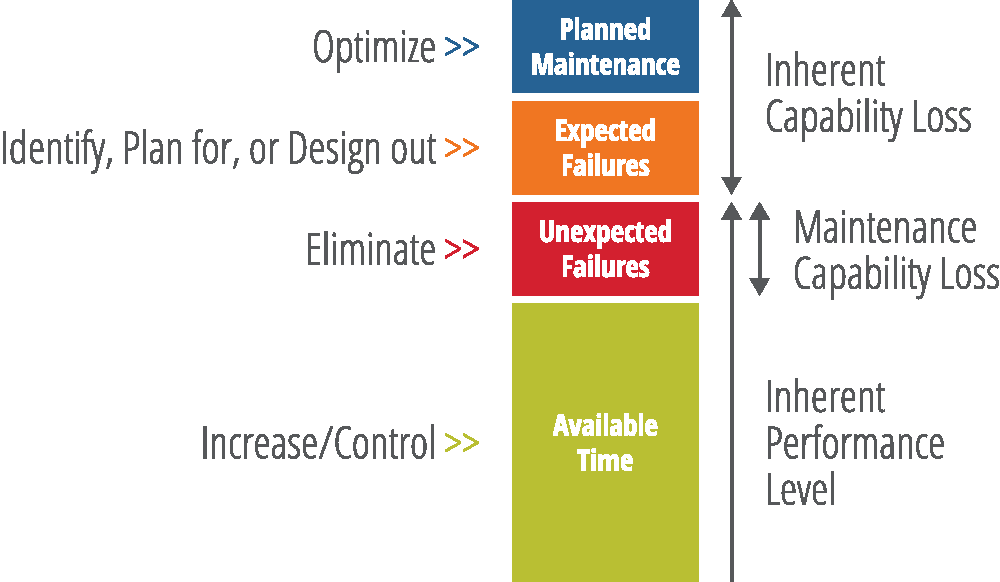

Solution
Step five is key because grouping data by failure mode easily identifies task duplication. Task duplication is where the same failure mode is managed by PM conducted by more than one section or task. It is most commonly found between operators and trades and trades and condition monitoring specialists. In this step, the team reviews the failure modes generated through the failure mode analysis and adds missing failures to the list. The list of missing failures is generated through an analysis of failure history, if available, technical documentation, or the experience of the team.
During each step, recommendations for strategy improvement were made. While all this was happening, tools and systems were being developed and implemented in parallel to collect data to validate the effectiveness of the PM strategy. Continuous improvement as a key change management process had begun.All events, including breakdowns, PMs and planned outages that occurred during commissioning and thereafter, helped tune the strategy. Each occurrence was assessed as: Expected – no value adding/cost effective action could be done to minimize or eliminate the event; or Unexpected – event consequence was preventable or could be mitigated with good installation, maintenance, or operations practices. Unexpected events were not acceptable.
After an unexpected event, typically equipment failures, the strategy for that component is reviewed and all relevant equipment variants are updated. This simple action forms the basis for a continuous improvement culture. Every failure is assessed by maintainers and operators during commissioning and continues on today.
Results
The goal of implementing a computerized maintenance management system (CMMS) based asset management plan for 30,000 assets was achieved in 90 days. This included almost 5,000 PMs, plus 60,000 tasks and failure modes. Best of all, the business is currently focused on achieving best in class performance supported by a robust continuous improvement program.
Yes, the project had typical challenges, like missing or inaccurate asset information, personnel language barriers (e.g., English, Chinese, Tagalog) and delays due to other priorities, that affected staff availability and weather. However, these challenges were no match to the vision and objectives of the management team that extended its support to quickly overcome each individual hurdle.
Conclusion
There are always going to be a number of factors contributing to the difficulties faced by asset managers in the current business environment. Many maintenance organizations are caught in a vicious cycle of reactive maintenance that leaves them exposed to unknown risks of safety, environmental, or loss profit opportunities, like low plant performance, high maintenance costs and a workforce with low morale and motivation. To break this vicious cycle of reactive maintenance, experience has shown an effective approach is to focus on both equipment and labor productivity, while meeting the risk tolerance of the organization.
The manager of the business once said: “Improvement is about working smarter, not harder. I’ll take a smart and lazy employee that gets the job done over a person who blindly follows instructions.” Simple and effective systems to support and make work easier are like a smart, lazy employee. In this project, information management using a database with integrated continuous improvement systems was one of the smart, lazy employees on the team!