
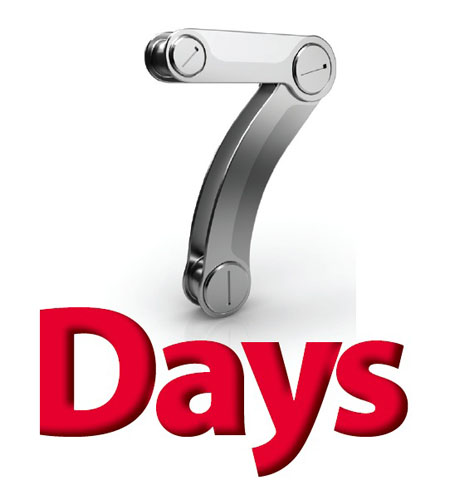
Pre-Work
Meet with all your supervisors, planners, engineers and key maintenance personnel. Let them know what is happening and that you want this to be a department effort to improve everyone's lives. This means you will need everyone to help.

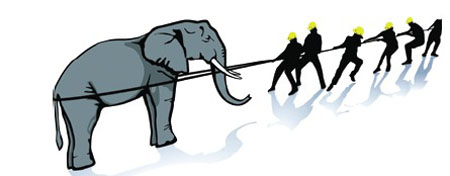
I once learned from a wise man that one man cannot pull an elephant, but if everyone pulls on the rope, we can pull the elephant around wherever we wish. Tomorrow, all hands need to be on the rope.
TIP: For the seven days, bring in donuts each morning. This will help make everyone more receptive to the concepts that will be tackled.

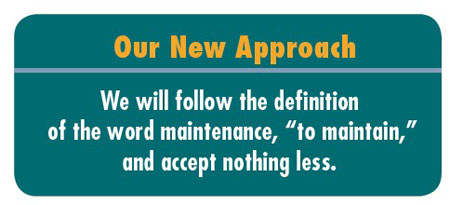
Figure 1: Our New Approach
Day 1
This is the first day of the rest of your life, so let's make a difference beginning today. Have the donuts and coffee ready for everyone. Bring in all-day shift maintenance personnel: planners, storeroom personnel, engineers, supervisors, all of the maintenance crews and leadership.
Let them know you are going to implement a program titled "7 Days to Better Equipment Reliability." In front of everyone, post a simple sign that reads: "7 Days to Better Equipment Reliability." Tell them this is a journey and not a race. Don't worry, they are going to be excited about these seven days.
On the first day, you want to focus on a simple task. Ask everyone to begin focusing their efforts on performing the following task, today and until the earth as we know it ends. Post a banner in the shop that resembles the banner shown in Figure 1.
Remind everyone that they are to perform all work to specification. If a specification is not known, make sure they know to ask their supervisor or engineer for assistance. Also, tell them to keep in mind that they cannot maintain equipment that is not maintainable.
In front of your department, ask someone to post the "Guiding Principles of Maintenance" (shown in Figure 2). State each one for everyone to reflect on.
Figure 2: Guiding Principles of Maintenance
NOTE: To follow Principle 4, you may need to develop a standard for closing work orders.
After this meeting, you must be seen in the field all day, helping people with problems and understanding the true challenges your team faces. Never correct them unless the task will damage equipment or injure personnel. (You can take care of your paperwork after the first shift leaves.)
As the maintenance staff is leaving, thank them for their work and shake each person's hand, including your management team. Your management team is the key to success and they must begin acting as a team with you as their leader.
I know you are thinking that this will be one heck of a day, but feel good knowing that success never comes easy. Simple rewards, such as a mechanic smiling when he or she leaves work, should be enough reward for you.
Day 2
Gather everyone for a five-minute meeting in the morning. (Don't forget the donuts!) Give everyone a universal thread file, including your electricians, or some other token of appreciation to thank them for their efforts yesterday.
Ask how many of them are with you on this journey to maintenance excellence. Notice that a new word is introduced, "maintenance excellence." You are slowly changing the culture in your facility.
All maintenance supervisors, managers, reliability engineers and mechanical engineers should be on the floor assisting maintenance personnel who are having problems grasping the concepts laid out on Day 1. No negative talk; this is a time of reflection, calmness and assistance.
When this meeting is over, you must be seen in the field all day, just like on Day 1.
Your leadership team will likely be feeling uncomfortable at this time. Take them to lunch, but no talking business allowed. Listen to what your leadership team is telling you and do not react, think about what they are telling you. If one person is a problem on the leadership team, take them in your office and talk to them in a calm voice. Think of yourself as a psychologist: good listener, no directive, no threats. Calmness is the key.
Again, as the maintenance staff is leaving, thank them for their work and shake each person's hand.
As Day 2 ends, you will probably be stressed, but don't give up yet! Remember, it's a journey that will lead to great results.
Day 3
Ask storeroom management to take you and your management team on a walk-through of the storeroom. (It will be helpful for you and your staff to catch up on materials management at night. Remember, we are on a seven-day journey; I hope you warned your spouse or significant other that long days may be part of these seven days.) During the walk-through, look at how spare parts are stored, ask what the stockout percentage is, and find out if the storeroom is performing PMs on large bearings and electric motors. Also identify parts that are not stored properly, such as V-belts, and make sure the thread files are set up in the storeroom.
At the end of the walk-through, ask the storeroom manager how long it would take to correct all the problems your team noted.
Let the storeroom manager know that you do not expect success overnight; however, you would like to see a plan within three days for the easy fixes. Assign a reliability or maintenance engineer to be the coach for the storeroom. If you do not own the storeroom, you should take the necessary measures to pull it under your control. Most of the stuff in the storeroom is maintenance; the value may be higher for production, but the volume is maintenance.
Afterwards, do not take a break, rather go into the mode of "All Hands on Deck." The main focus is helping people do the right work at the right time, along with closing out work orders correctly with all the fields completed.
As with the previous days, as the maintenance staff is leaving, thank them for their work and shake each person's hand.
Day 4
Stay in your office until everyone goes to work and then go about your normal day and meetings. Sit down with your engineers, supervisors and planners after lunch to discuss what is working and what is not working. If there is a problem, ask the team for a solution. Go with their idea, even if you do not like it, as long as the idea is legal and ethical.
Set up a small group within your team to focus on work order close out and the metrics you want to track. Ask the group to identify four key performance indicators (KPIs) that they want to measure. Make sure the KPIs will drive the correct behavior. Also, ensure that the inputs in your maintenance software will give you the outputs you want. Establish a standard operating procedure (SOP) for work order close out. This should include a RACI Chart, similar to the one illustrated in Figure 3, that defines roles and responsibilities.
Figure 3: Maintenance Crew KPI RACI Chart
Once again, as the maintenance staff is leaving, thank them for their work and shake each person's hand. As some of the last people are leaving, ask a few of them (about three or four) to stay for a minute or two and ask them how things are going. You may have to make an adjustment based on what you learn. Give them each a high-quality 6-inch electronic caliper or other token of appreciation and shake their hands, looking them in the eye, smiling and saying "thank you" with sincerity.
Day 5
Host a short meeting with your maintenance and leadership teams and tell them what a great job they are doing. Use some examples that you or your staff have seen of their great work. Bring those team members up and give them a handshake, look them in the eyes and say "thank you."
Give each member of the maintenance and leadership team a pack of M&Ms or some other individual treat (make sure you have a variety of flavors and enough for everyone) to distribute to the staff in your department.
Ask your team working on KPIs to begin producing the four chosen KPIs, even if they are not 100 percent accurate. Post them on large line graphs where everyone can see them. People understand line graphs, numbers do not mean anything. If the number looks bad or has high variation, consider it acceptable because this is where you truly are.
Ask your maintenance leadership team to be outside when the staff is leaving to thank them for their hard work and dedication. Shake the maintenance techs' hands, looking them directly in the eye, smile and sincerely say "thank you."
Day 6
Have a meeting with all of the maintenance team, including leadership. Ask the plant or site leader to say a few words (five minutes) about their hard work and dedication in the past few days.
Pass out different sized torque wrenches to each crew based on their needs, whether electrical or mechanical. Give them charts with the torque values listed as well. For each crew, give them a calibration test tool to validate that the torque values are accurate. Make each supervisor sign for the torque wrench and other items.
Next, you, as the maintenance manager, should tell everyone that from today on the team will step up the professionalism to a new level. The team will use the torque wrenches on all fasteners, both electrical and mechanical. After the fastener is torqued to the prescribed level, they should use a paint marker to mark the fastener across the nut and threads of the fastener. This will validate that the fastener has been torqued to standard and if the torque value changes, you will see the paint on the threads cracked.
At the end of the day, say goodbye and shake the hands of the people who stop by to say goodbye and thank them for their hard work.
Day 7
Bring in the crew for Day 7 and ask if anything has changed in the past seven days. Find out if the group believes they are moving toward maintenance excellence. List the successes and the mistakes. Make this a fun experience.
Have an outside lubrication expert or consultant come in and evaluate your lubrication practices and make suggestions for storage, contamination control, best known practices, etc. DO NOT call in the sales person from the oil company or their lubrication engineer. Develop an action plan with one supervisor or engineer as the lead on the project and make it happen, focusing on critical assets first. Lubrication is the number one killer of equipment reliability; all lube techs should be certified and task qualified.
At the end of Day 7, state to everyone that your facility is the best and you will all prove it. Point out that they have already mastered the simple tasks they were challenged with and succeeded in moving towards maintenance excellence. Don't forget to thank them all once again before they leave for the day.
Finally, remember that if it were easy, everyone would be doing it. The smiles on your maintenance techs' faces will show you that it is all worth it. Good luck implementing these ideas within your facility and understand that deviating from this plan at any point could result in failure to achieve your goals.
I would like to know how this program works for you. If you use the approach described here, please let me know what results you see. If you need ideas or more information, send me an email at rsmith@gpallied.com.