In lubrication, the Pareto Principle also applies. Studies indicate as many as 60 percent to 80 percent of mechanical failures can be attributed directly or indirectly to lubricant contamination. And while this statistic will vary based on application, machine type and industry, what cannot be disputed is that without precision control of the contaminant, machine reliability can be seriously compromised.
It’s All About the Small Stuff
For the purpose of this article, consider the two primary contaminants found in most plants: particles and moisture, though other contaminants, such as air, chemicals, fuel and glycol, also can have deleterious effects on equipment. Most companies recognize that dirt and moisture are bad, but fail to recognize how small amounts of contamination can have a very serious effect.
For particle contamination, the primary concern needs to be silt-sized particles in the one to 10 micron size range. While small in nature – less that 1/20th the thickness of a human hair – three micron silt-sized particles that are no bigger than a red blood cell are as much as five to 10 times more likely to induce a failure. The reason for this is twofold: many filters are not designed to remove such small particles and dynamic clearances (the separation between moving parts under operating load, speed and temperature) are typically in the one to five micron size range for most common equipment classes (see Table 1). Controlling contaminants in this range is critical since dynamic-sized particles can easily enter oil-wetted pathways, yet are large enough to cause cutting (abrasive) wear, premature fatigue failure and valve stiction issues.
Table 1
Typical Dynamic | Clearances |
Ring to cylinder (engine) | 0.3-7 um |
Journal bearing | 1-100 um |
Rolling element bearing | 0.1-5 um |
Gears | 0.1-2 um |
Servo valve (spool to bore) | 1-4 um |
Hydraulic vane pump | 0.3-5 um |
Particle contamination is usually expressed according to the ISO4406:99 standard. This standard reports particle concentrations in hydraulic fluids in three size ranges: particles > 4 microns, particles > 6 microns and particles > 14 microns. Based on the ISO4406:99 standard, Table 2 shows recommended target cleanliness levels for different types of common plant equipment.
Aside from particle contamination, water is the second most insidious contaminant. Present in most fluids, even in the most pristine environments, water can increase failure rates 10 to 20 fold, depending on the circumstances. Water causes problems in a number of ways. First, any iron or steel surface in contact with water will start to rust. This can induce premature failure due to corrosion, as well as introduce rust particles into the fluid. Second, water performs very differently to lubricating oils under operating loads and speeds.

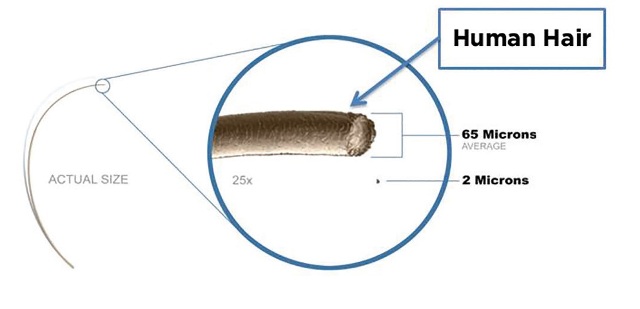
Figure 1: Silt particles in the one to 10 micron size range are only less than 1/10th the thickness of a human hair, but cause five to 10 times the amount of damage as larger particles
So how much water is too much? To a large extent, the answer depends on the type of equipment, the age of the fluid and the operating temperature. The reason for this pertains to the form that water takes in lubricants. Most fluids will hold a certain amount of water in the dissolved phase. For the most part, as long as the water remains dissolved, most water-induced problems will be minimal. However, as soon as the water comes out of solution and becomes free or emulsified, it becomes a very real concern. While highly temperature dependent, the saturation point of most conventional oils ranges from 100 ppm to 200 ppm for lightly additized oils, such as turbine oils, to as much as 500 ppm to 800 ppm for more heavily additized oils, such as gear oils. As such, water levels should be set accordingly to try to ensure that any moisture present is below the saturation point at all in-service temperatures.
Developing a Contamination Control Strategy
For those who believe in lubrication’s own Pareto rule – 80 percent of problems are caused by the 20 percent of contamination issues – developing a plant or corporate-wide contamination policy should be a priority. While more complicated to execute, establishing the policy is very simple.
Step 1: Know how clean the oil needs to be
The first step is to know how clean and dry the oil needs to be. This is analogous to setting speed limits on a highway. Depending on ambient conditions and operating context, set target cleanliness and dryness levels that provide a reasonable surety that contamination-induced failures are unlikely to happen. Just like setting lower (tighter) speed targets (limits) in critical traffic zones (e.g., busy highway intersections, school zones, etc.), targets for oil cleanliness need to be adjusted based on the type of equipment, its criticality and the environment in which the machine is functioning. While driving at 5 mph over the limit is unlikely to induce a speed-related accident in a 55 mph zone, the further from the posted limit a car goes, the more likely a failure will occur and, in the case of driving, the greater the likelihood for a speeding ticket! Likewise, the probability of a contamination-induced failure increases dramatically the further away from the optimum target level for particles and moisture.
While Table 2 is a good starting point, targets should be set for each machine class based on the aforementioned factors, with the goal being to not exceed the limits set for particle or moisture contamination.
Table 2 - Recommended Cleanliness Levels for Different Equipment Classes
Machine Type | Particle Level Target | Moisture Level Target | |
Hydraulics | With servo valves | 15/13/11 | 125 ppm |
With proportional valves | 16/14/12 | 150 ppm | |
Variable volume piston pump | 17/15/12 | 150 ppm | |
With cartridge valves or fixed piston pump | 17/16/13 | 150 ppm | |
With vane pump | 18/16/14 | 150 ppm | |
Gearbox | 19/16/13 | 300 ppm | |
Paper Machine | 18/14/11 | 200 ppm | |
Steam Turbine | 18/14/11 | 100 ppm | |
Pumps | 17/14/12 | 150 ppm |
Step 2: Control contamination to levels below the target
Just like having the ability to control speed while driving, having a “brake” to control contamination is vital. To do this takes a twopronged approach: exclude contamination at the source, then work to remove any contaminants if they get into the machine. To exclude contaminants, look at the total pathway that a lubricant takes from storage to handling and application to the machine. This includes pre-filtration of new oils, lubricant transfers using quick connects to avoid exposure to the ambient plant environment, and tanks and reservoirs that are properly sealed and using appropriate particle and desiccating breathers to prevent contamination ingress from air exchange between the machine head space and the ambient operating environment. Once everything has been done to exclude contaminants, filters and filtration systems need to be evaluated to ensure they are capable of maintaining the contamination control targets established for each machine. In doing so, it is necessary to try to balance filtration needs, making sure vents, breathers and filters are selected to achieve the established targets. Trying to maintain a critical hydraulic system to 15/13/11 or better with a standard original equipment manufacturer vent cap and 10 um filter is never going to happen!
Step 3: Monitoring contaminants
Trying to effectively control contaminants without good data from oil analysis is like trying to drive within the speed limit without a speedometer. It’s simply guessing (or hoping!) that the contamination control strategy is working. Good data requires taking proper oil samples from the correct location and having the lab perform the correct tests capable of detecting contaminants at low levels. This is particularly true for water contamination since many of the common tests used by labs to look for water are not able to detect water down to the levels identified in Table 2. Care should be taken to ensure that sample results indicate compliance with the target levels set and where no compliance is found, corrective action is taken to determine the root cause of the problem.
Putting It All Together
Based on the above, contamination control is as simple as 1-2-3, but even this simple approach can have a very dramatic effect on equipment reliability. Using a real-world example from a stamping press in an automotive plant, based on a high level of contamination in the stamping presses, the plant set about creating new targets for particle contamination. By installing proper breathers, sealing up reservoirs and installing kidney loop filtration, the plant was able to reduce overall contamination levels by an average of 93 percent to 97 percent within a few days!
Based on failure reporting, analysis and corrective action system (FRACAS) data, the plant was able to track downtime rates for lubrication-related issues before and after filtration with dramatic results. On average, the plant witnessed a 54 percent reduction in annualized downtime in the first six months after deploying new contamination control measures, compared to its average annual lubrication-related downtime for the three previous years. For this plant, the savings exceed $1 million dollars and getting there was as simple as 1-2-3!