The idea behind the business-based maintenance approach is that every PdM Program, as well as all the functions of a maintenance organization, must support business goals, work within business-specific parameters and undergo a continuous improvement process.
Predictive Maintenance Program - What is It?
During discussions or while reading technical magazines and papers, we often encounter the term “Predictive Maintenance Program”. What exactly does it mean? If we asked a number of people, we would probably receive several different answers. We define a Predictive Maintenance Program as follows:
A Predictive Maintenance Program is the routine and cost-effective measurement of a number of parameters indicative of machine and equipment condition, which are trended over time, correlated and used to make decisions about the type and timing of maintenance corrective actions within economical parameters of the business.
In addition, Predictive Maintenance Programs provide historical data for root cause analysis. Let’s analyze the definition and explore its implications.
Routine Measurement and Data Trending
The goal of any Predictive Maintenance Program is to assess machine condition and predict any impending failure. This requires data to be collected on a regular basis and results trended. Any deviation from the usual state indicates deterioration of the system. Frequency of data collection is a function of the equipment failure modes, equipment criticality and business parameters.
There are a number of mistakes commonly made in the frequency of data collection including: collecting data too often, collecting data too infrequently, incorrect intervals and rigid, fixed frequency of data collection.
Over collecting, or collecting data too often, is expensive. Time and resources are wasted by collecting data that does not carry useful information. The frequency of data collection, in this case, cannot be justified by equipment failure mode or economics.
Similarly, collecting data at long-time intervals carries the risk of “missing” faults. This may prove costly for the business, as well as the reputation of the PdM Program. There is nothing worse than having a major failure during peak business time. Lost production, lost profit opportunities, and, perhaps, environmental and safety issues are all examples of ”missed” calls. These are usually much more costly than the cost of data collection.
Ideally, the frequency of data collection should be adjustable. It should change during the course of equipment lifetime. For example, a baseline reading should be recorded after installation. This provides a good starting point for trending later on and, more importantly, serves as a quality tool, ensuring that the installed equipment does not have inherent faults and repairs have been performed according to the specifications.
After the “infancy” stage, the frequency of data collection can be extended. However, this again is a business decision, as not all equipment conforms to the theoretical bathtub curve due to many real-life process and maintenance variables. Extending data collection intervals may lead to missing impending and costly failures. A ratio of success rate to cost of data collection/analysis should always be considered. A good PdM Program will be one that collects enough data for trending and analysis purposes and is still cost effective.
Number of parameters indicative of machine condition
There are many predictive maintenance technologies available. Vibration monitoring, tribology (oil analysis), infrared thermography, ultrasonic monitoring (both contact and airborne) and motor circuit testing are the most commonly employed technologies.
Less frequently used (and often not regarded as predictive maintenance tools) are electrical, process and performance measurements. This is unfortunate because these technologies have the potential to provide a wide range of information about equipment, machinery health and condition and, thus, assist greatly in predicting failures.
Which technologies to employ depends on two factors – failure mode and economics. Modern predictive maintenance technologies, in correlation with process measurements and other test results, can detect almost any possible impending failure. However, the challenge is to use the most cost-effective ones and to monitor only the minimum number of parameters that will still achieve the goal of detecting failures.
Make decisions about the type and timing of maintenance actions within the economical parameters of the business.
Once we have data from all the predictive maintenance technologies and have correlated the data, we may find there is a fault. If the machine is going to fail, our recommendation as predictive maintenance specialists is to shut it down immediately and replace the damaged part. Now these questions arise: Have we considered the economic aspects of the machine going out of production? Have we considered the economics of the business? Have we considered the possible loss of profit? Is the machine really going to fail? What if the business parameters are calling for an extension of the production cycle due to unexpected additional orders?
The flow chart in Figure 1 shows the business-based approach developed and adopted by Siemens. The significance of the model presented is the decision-making process for the type and timing of maintenance actions. The model introduces business parameters, which influence the final decision.
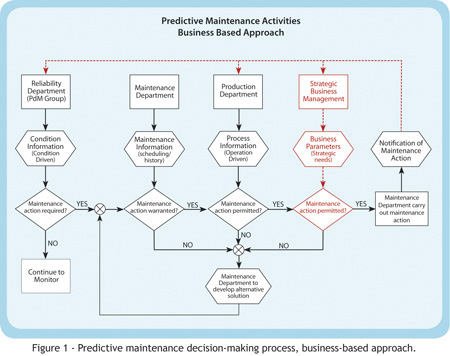
Typical Program Startup Process
There are a number of steps that need to be considered during the startup of a Predictive Maintenance Program. Most of the tasks, however, can be divided into two groups – program design and program implementation. Each of the phases is unique and requires careful planning and execution for success.
Program Design
A good PdM Program should be a result of the maintenance strategy development process. In instances where maintenance strategy has not been developed, a simplified process of designing a PdM Program can be employed. Such a process is described below.
Develop a List of Plant Equipment – In most cases, the list already exists and can be obtained from maintenance departments, operations, etc. It is important to review the list for completeness. This task will most likely require walking through the plant and physically checking each item. Experienced employees with good knowledge of the plant usually provide invaluable help.
Assign criticality of the equipment – There are many factors influencing criticality of the equipment. In many cases, the process will consume plenty of time and resources. For the purpose of designing a PdM Program, a simplified approach should be used. One of the best starting points is to use a single line diagram of the process and input from experienced maintenance and operations personnel. This way, assigning criticality to the equipment can be accomplished quickly and cost-effectively.
Identify equipment suitable for monitoring – So far we have developed an equipment list and assigned criticality. The next step is to select the equipment suitable for monitoring. This decision is based on equipment criticality and failure mode. There is little to be gained by monitoring equipment of low criticality or equipment whose failure modes prevent prediction of a failure (equipment with random failure distribution function).
Select cost-effective predictive maintenance technologies – There are many predictive maintenance technologies available to maintenance practitioners. When properly used, they can provide invaluable information about the condition of the monitored equipment, and many of them are capable of monitoring for different types of faults. In addition, many types of faults can be monitored by the same predictive maintenance technology. The challenge is to select a cost-effective technology that is most suited for a particular type of equipment. The number of technologies used should be limited based on return-on-investment calculations.
Assign data collection/monitoring frequencies – Monitoring frequencies depend on technologies assigned and on failure modes. The optimum frequency is capable of detecting impending failures early enough to allow for effective maintenance action planning while remaining cost-effective. The monitoring frequency should be adjustable, i.e., it should be changed based on equipment condition, technologies applied, criticality, failure modes, p-f function, etc..
Develop standard procedures and work instructions (documentation of the PdM Program) – One of the least understood and most neglected aspects of PdM Programs is documentation. It is often perceived as a waste of time and resources, so documentation is never developed. Well documented, structured PdM Programs provide consistent results. All PdM activities are documented and historical data is available for statistical analysis and program effectiveness. We will discuss this further in “Continuous Improvement Process”.
Program Implementation
We have now designed a PdM Program, or more precisely, developed requirements for equipment condition monitoring including the technologies and frequency of monitoring. The next step is implementation. Even though the design stage is important, the implementation is what makes any predictive program a success or a failure.
There are basically two ways of implementing a Predictive Maintenance Program – outsource all or some of the services or do it in-house. Both ways have advantages and disadvantages, but cost-effectiveness should be thoroughly examined.
The following are the cost elements, which need to be considered when deciding on the program startup and implementation:
a. Purchase of predictive maintenance equipment and software
b. Upgrading and calibrating software and test equipment
c. Personnel training
d. Personnel cost
e. Predictive maintenance database setup
f. Selection and preparation of monitoring points
g. Collection of baseline readings
h. Establishing preliminary alarm levels
i. Development of work instructions/procedures
j. Development of reporting procedures
k. Ongoing cost
l. Personnel replacement cost
m. Availability of suitable personnel
Considerable cost is likely to be incurred with elements a, b, c and d. More importantly, there are the ongoing costs. Table 1 is a template to establish tangible costs associated with a PdM Program startup. It has been developed to help in the decision-making process.
In addition to the tangible costs contained in Table 1, there also are intangible costs that should be considered. These include:
• Response time
• Program ownership
• Geographical location
• Corporate culture
• Demography
Continuous Improvement Process
Every Predictive Maintenance Program is designed based on certain assumptions. They are the result of knowledge and past experience with similar equipment and the current state of predictive maintenance technologies. Equally important, and yet often neglected, are the business parameters, which should also be considered.
As all parameters are constantly changing, it is important that the PdM Program changes as well. To accomplish change, a continuous improvement process must be employed.
A continuous improvement process can be achieved by periodically reviewing and auditing the PdM Program. This process should be governed by written procedures. A Predictive Maintenance Program audit can provide the necessary tool. It is important that the result of the audit is trendable and repeatable, so improvement can be measured over time.
There are a number of areas that should be reviewed. These include:
Program Management – Having a clear management commitment and organizational structure in place is key. Management with clear vision will drive Predictive Maintenance Programs and ensure their success.
Predictive Maintenance Technologies – The Predictive Maintenance Program is designed based on current available technology. As time progresses, new and improved technologies become available on the market. Therefore, it is important to periodically review the technologies for their effectiveness. Consideration should be given to incorporating any new technology available on the market into the program. A correct mix of technologies, correlated with results, is usually the most effective predictive maintenance solution.
Documentation – Each Predictive Maintenance Program should be designed as a process. Hence, every step should be documented. Accurately written work instructions and procedures ensure that the results are not influenced by individuals, and are repeatable. All reports, failure analysis findings and potential savings should be well documented, and documents should be stored for future reference. This will allow an effective continuous process.
A predictive maintenance audit should be conducted on an annual basis, and its finding should form the basis for a continuos improvement program. Table 2 shows results of a typical Predictive Maintenance Program audit. The shaded area represents the actual score.
Summary
Predictive Maintenance Programs have gained widespread acceptance throughout the industry. However, there are still a lot of misconceptions and misunderstandings about predictive maintenance, and its role in the cost-effective asset management process. The described business-based approach to predictive maintenance allows for a seamless integration of the technology into the business process, and close and continuous alignment of the PdM Program with business goals. Furthermore, predictive maintenance specialists need to learn the business language to “sell” the results to the management, which will ensure the future of the program and benefit the plant.
Krzysztof (Kris) Goly has more than 25 years of experience in the field of maintenance and reliability. His experience includes positions as maintenance and engineering manager, reliability manager and, currently, principal consultant for Siemens Industrial Services based in Alpharetta, Ga. Goly is a Certified Maintenance and Reliability Professional. He can be contacted at kris.goly@siemens.com