by Stuart Grant
With the advances that science, technology and regulation have brought, many companies today have excellent engineering capabilities, a fantastic technical framework and good governance. In theory, these companies should function reliably and also achieve great value. But often, that is not the case. What is going wrong? DuPont took a cultural journey to find the “missing link.”
Many companies take too narrow an approach when implementing improvement methodologies or become overly dependent on elaborate procedures that do not lead to sustainable results. The clue to extracting maximum value from productivity improvements lies in an integrated approach. Put differently, the key is operational excellence, defined as “the application of principles, systems and tools to engage and focus everyone’s efforts on meeting customers’ needs and continuously improving process performance.”
Figure 1: Market Drivers – Operational excellence is one of the most important issues for CEOs globallyAccording to the 2013 CEO Challenge study conducted by the Conference Board,1 operational excellence is one of the top three most important issues for CEOs globally. It is widely recognized as one of the most important contributors to a company’s sustainable performance and growth.
Businesses today face global competition and are part of global supply chains. Social and environmental regulations and expectations are becoming ever more stringent. Investors expect companies to pursue lower cost and higher value products with existing assets. To survive, organizations have to adapt rapidly and efficiently to changes in market demand and competitive pressures at plant level. They need to find and pursue synergies to drive productivity and efficiency. All these external drivers exert pressure on companies to improve their overall operations performance. Those that manage to do so reap the benefits of a productive workforce, increased value and sustainable growth.
So, what are the key elements to achieving operational excellence? Du- Pont found that one of the key steps is to create an aligned and productive culture.
Founded in 1802, DuPont is a chemical-based manufacturing company. Throughout its history, the company has learned many safety and asset management lessons. Over the years, DuPont has come to understand that the often hidden influence on safety performance – the people part – is also key to operational excellence and asset management. By fixing the safety culture and setting the right mind-sets and behaviors for safety, the company found it not only improved its safety performance in the long run, but also its productivity and operations excellence in asset management. This article outlines the main features of this cultural journey, which can be applied to any organization.
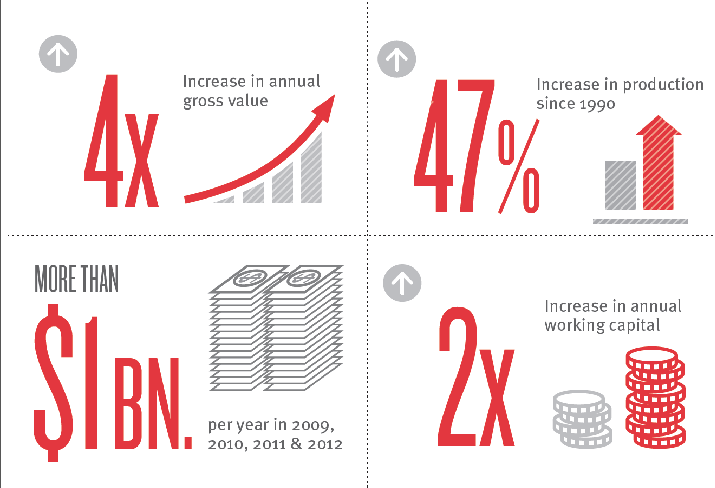

Getting the Balance Right
All companies want to create value: for society, for the customer and for the stakeholders. As companies strive to create value, they have to strike a delicate balance between risk management and driving profit. There are two main strategies for achieving this. The first is to reduce risk to an acceptable level (protecting the asset). The second is to increase profit in a sustainable way (optimizing the asset). Everything DuPont does in asset management stems from those two clear business imperatives.
The ideal scenario is for a company to mitigate risk while achieving ever-rising profits. That may sound utopian, but is, in fact, linked. DuPont recognized this and, therefore, set out to establish a sustainable model, as shown in quadrant 1 of Figure 3. Profit is balanced by risk mitigation to a tolerable and acceptable level.
So far, so good. But how does a company achieve this status?
Like many other companies, DuPont has worked with numerous systems, from Six Sigma to Lean, and other logical tool sets that support technical models. One of the aims, of course, has been to improve asset productivity and eliminate waste. Many of these are excellent tools and DuPont still uses and establishes competencies in them. However, the trap that is easy to fall into is the illusion that these systems alone will transform asset productivity. The same holds true for PAS55 and now ISO55000 or ISO55000 in conjunction with ISO31000 for risk management. These standards provide an excellent framework for asset management and help companies develop their internal strategies and standards to support value creation from an asset. But, as important as these systems are and however much they appeal to those who are engineers and scientists, they are not enough on their own.
In fact, the recently produced International Association of Oil & Gas Producers (IOGP) report2 into asset integrity failures across the industry found that among the top causes of incidents were human factors, competencies and failure to establish technical and capability programs in a sustainable way. As will be discovered further on, these company behavior patterns are set at leadership level. Culture and mind-sets are engendered from the top. As another report by Oil & Gas UK3 in 2009 highlighted, the number one underlying cause for asset management events is poor leadership. Again, culture and mind-sets are engendered from the top.
Promoting Independence
At DuPont, it is recognized that leadership and other human factors influence outcomes. It is, therefore, people’s behavior that is the focus of the company’s safety performance, production system and other management models.
Over the years, DuPont has developed a safety assessment tool called the DuPont Bradley Curve,4 based on the book, The 7 Habits of Highly Effective People by Stephen R. Covey. This model allows DuPont to assess where it is in its safety culture. It has become clear that there is a tipping point in an organization when the culture becomes much more effective and develops its own momentum. This critical point of transition lies between the dependent and independent phases shown on the Bradley Curve in Figure 4. Once employees cross the cultural bridge from compliance (force) to choice, they become supremely motivated, not just for safety, but also for operational excellence.
The reason for this lies in people’s innate attitudes and behaviors. The following explains how employees are likely to act and react in the different phases of the Bradley Curve, particularly as it applies to operations, as illustrated in Figure 4.
Reactive culture
An organization that finds itself in the reactive phase is in a vicious cycle of one action resulting in a destructive reaction. Behavior is based on instinct. Compliance is the goal. People follow the rules because they have to. The “law of the jungle” prevails. The attitude is likely to be, “just get the day in;” do whatever it takes to get through it fast and out the other end. Reactive behavior often manifests in people taking shortcuts, schedule busting, little discrimination in prioritizing work (everything is urgent), little or no schedule backlogs, etc. This is where companies encounter “silos” and a notion of “the enemy,” whereas operations versus maintenance versus reliability. This is the worst place to be and is often reflected in safety performance, too. It is not a good environment to work in!
Dependent culture
Dependence is a little better, but employees will still do things only because they are told to, or because there is an implied threat. Fear and discipline are the motivators. In this organizational culture, people leave their brains behind in the workplace parking lot and let their bosses decide for them. If the boss gets it wrong, there can be big implications. If the boss is not there, employees tend to slip back into reactive behavior. In this environment, there may be a focus on training, but not necessarily on competence.
Independent culture
In this quadrant, there is a subtle, yet significant mind-set change. People follow the rules because they want to and because they see the sense and benefits in doing so. That makes for a much better place to work. In this environment, people know what the right thing to do is and they do it. They often understand their role is directly linked to business results. Applied to asset management, this means the culture of maintenance reliability leadership has changed from a cost focus to a value focus. As a matter of fact, this aligns with the ISO55000 asset management standard. In an independent behavior phase, you begin to see individual recognitions and the adoption of good and best practices because everyone knows the goal. However, there is still room for improvement.
Interdependent culture
Once organizations attain a culture of interdependence, things are done for the greater good. Organizations are in a virtuous cycle of one action affirming a new, better action. Everyone is aligned with a joint goal. Operations work as equal partners with maintenance reliability. People cross boundaries without being asked to do so and proactively help each other. There is collaboration. Knowledge is codified and shared. Mentoring and coaching is the norm. There is team recognition, but not just for heroic efforts, such as those responding to an after-hours production incident. In this environment, a planner or planning team that quietly and methodically extracts value and eliminates waste by superior planning will be recognized and receive acclaim. Thus, the virtue of proactivity trumps reactivity.
The best things about the interdependent quadrant are:
- It is NOT Utopia, it’s attainable;
- It comes with superior safety results because the attitude is the same for safety, reliability, operations excellence, etc.;
- It is sustainable.
The same quadrants of the Bradley Curve used at DuPont to monitor and assess safety culture also apply to other management systems. If employees act independently and responsibly because they see the value for themselves and for the business, that not only benefits safety, but also maintenance, reliability, performance, output and quality, all of which contribute to creating value and improving operational excellence.
But what makes people want to become that interdependent? It is quite a leap from reactive behavior to independence and interdependence. DuPont believes the clue is in visibly demonstrating leadership commitment so people see and feel that senior management is doing exactly what it also expects from all employees.
Achieving Sustainable Asset Productivity
Driven by an imperative for asset productivity sustainability in a period of intense business challenges, DuPont developed its own DuPont Production System (DPS). This system is based on a four-strand approach:
- Managing or Governance Process;
- Technical Model;
- Capability Model;
- Mind-sets and Behaviors.
DuPont has transformed its own business model in the past seven years by working with this four-strand approach. DuPont has found from its work with other companies through its consulting business, DuPont Sustainable Solutions, that companies tend to concentrate on the technical, capability, or governance processes. These are very important. However, in order for a business and asset management processes to succeed and thrive, it is equally important to promote the right culture.
Once DuPont applied its Bradley Curve culture assessment learnings, coupled with the right leading indicators, to operations excellence, maintenance, reliability and other capabilities, they began to flourish. Technical and capability models will not work without understanding the true culture of an organization and what needs fixing. And to fix, you start with leadership.
DuPont has found that a sustainable solution to operations excellence, which includes an asset management program, is only viable if the right governance, technical model, capabilities and, critically, a supportive culture are in place. If any one of these elements is weak, the whole program is likely to fail.
As an owner-operator, DuPont is in a unique position to assess and guide other companies through DuPont Sustainable Solutions using real- time experience. With a toolbox of mind-set and behavior resources, Du- Pont has worked with clients in a variety of industries, including oil and gas, petrochemicals, energy, mining, agriculture and food to assess where they are and to help them move, as DuPont has had to do, to the right side of the Bradley Curve.
References
- The Conference Board. CEO Challenge® 2013: People and Performance. https://www.conference-board.org/retrievefile.cfm?filename=TCB_R-1523-13-RR_CEO-Challenge-2013-Report1. pdf&type=subsite
- International Association of Oil & Gas Producers. Asset Integrity - The Key to Managing Major Incident Risks. Report No. 415, December 2008. http://www.ogp.org.uk/pubs/415.pdf
- Oil & Gas UK. Asset Integrity: An Industry Progress Report, April 2009. http://www.oilandgasuk.co.uk/publications/viewpub.cfm?frmPubID=306
- DuPont. DuPont Helps to Sustainably Improve Safety Performance. The DuPont Bradley Curve Video: http://www.dupont.com/products-and-services/consulting-services-process-technologies/brands/sustainable-solutions/sub-brands/operational-risk-management/videos bradley-curve-video.html