Benchmarking, Best Practices, Standardization… Development or Envelopment?
Though this is common sense, “copy and paste” seems to be the norm, especially in financially woefully times, but this article provides some striking examples. The article uses the multi-level perspective to describe the struggle between “copiers” and “context-conscious” people, and gives examples about some who have provided solutions to mitigate the dominance of blindly following the herd to one’s own detriment.
The Holy Totems of Business
Benchmarking. Best Practices. Standardization. These are some of the more common concepts in business that are regarded holy and untouchable, and which are taught in expensive training sessions and applied in top companies. Thus, you don’t question them and you don’t go against them.
However, in this controversial paper, we will make an attempt to demonstrate that the application of the same concepts, procedures, practices, etc., in different circumstances does not yield the advancement in business by definition. As a matter of fact, this article will go as far to say that this form of “copy and paste” can be even detrimental to business.
We are not against standardization, but we will discuss an important factor (some might even say the most important factor) to be considered when applying standardization. Nothing we bring forward in this article is extremely sophisticated, groundbreaking, or highly scientific. Rather, the main idea here is mainly built on common sense, but, unfortunately, reality shows us that this common sense is often something that is hardly present.
“Copy and Paste”
Concepts, such as benchmarking, best practices and standardization, are all around us. They are used to gain maximum performance, ease comparisons between different entities (e.g., countries, businesses, etc.) and create transparency in the sense that one can know what to expect in different parts of an entity. The latter is of particular importance for relatively large entities, like countries (e.g., standardization between regions and cities, respectively), multinationals (e.g., standardization between business units, locations, etc.) and industries (e.g., standardization between different companies within one industry). Standardization makes the different parts that constitute the entity to work in unison. They understand each other’s language, are adjusted to each other and thus work seamlessly together. This minimizes risk for financial bleeding and poor environmental, health and safety performance.
The application of benchmarking, best practices, standardization, etc., is not only experienced on different levels, but also in different aspects within levels. Examples of these are problem solving, engineering standards and solutions, productivity targets, cost performance/financial indicators, daily management practices, safety standards, etc.
What Is Good for You, Is Not Good for Me, per sé
Of course, many will agree on the abovementioned arguments for adoption and deployment of best practices, performance benchmarking and trickling down standardization in the entire organization. However, caution is required when doing so.
Consider a subsidiary of a multinational in a developing country that is obliged to keep its spare parts stock down to a best practice/benchmark figure established within that multinational. A situation could occur where there is insufficient spare parts during a sudden breakdown because the developing country has no local suppliers/manufacturers of some specific machinery/part and its remoteness makes it logistically difficult (and thus expensive and time-consuming) to deliver parts from abroad. The context in which the subsidiary operates (i.e., no local suppliers/manufacturers and the relative remoteness), makes it detrimental to keep low spare parts levels as is the norm in other contexts (e.g., developed countries with several suppliers/manufacturers nearby and good logistics).
Or take for example productivity figures of several parts (let’s assume factories) of a multinational that are measured up against each other. If one factory has a much older infrastructure and machinery, then consequentially, it is logical to assume that its productivity figures (defined as amount of product produced per full time equivalent or FTE) might differ from its sister equivalent that has a newer and more sophisticated infrastructure and machinery; the older plant might require several machines with low capacity to produce a certain output, whereas the new plant uses only one machine to produce the same output and thus, requires less operational and maintenance personnel. Their context differs and taking into account this context when considering whether the application of a particular standard will be fruitful is nothing else than considering the reality against which you test those standards. If you know where you want to go, the only way to assess the amount of effort required to get there is by knowing where you are now.
And we just can’t leave out Ron Moore’s fantastic work.1 There are some companies that mandate a particular tool must be used for a multitude of diverse problems. However, Ron Moore indicates that this isn’t always the most productive problem-solving method since every tool has its benefits and disadvantages and is particularly suitable in specific circumstances.
Development and Envelopment, Regimes and Niches
Concepts, such as benchmarking, standardization and best practices, should be used for the further development of an organization. In this context “development” means further advancement and sophistication, to grow out of the origins, maturing, improving skills and knowledge, etc. As a matter of fact, in Dutch “to develop” is translated as “ontwikkelen,” which literally means “to unwrap.” Glancing at the examples mentioned in the previous section, we would like to apply a term that was recently coined (http://uptime4.me/crscenter-pdf): “envelopment.” It is the opposite of “development,” and means “to wrap” (like you do with an envelope). When looking again at the earlier mentioned examples, to incorporate an entity in a project that is alien to the entity’s context, this might sound like a scientific xenophobe, but, as stated before, this is all just common sense. What is good for you, is not good for me, per sé.
In an earlier Uptime article2, we discussed the multi-level perspective (MLP). The MLP consists of three levels: landscape, regime and niche (see Figure 1). The landscape level is defined as an exogenous environment that influences both niches and regimes. Regimes are the rule set or grammar embedded in a complex of engineering practices, production process technologies, product characteristics, skills and procedures, ways of handling relevant artifacts and persons, ways of defining problems; all of them embedded in institutions and infrastructures. Niches are the locus where innovative activity takes place and where time-limited protection is offered against dominant selection rules. 3, 4
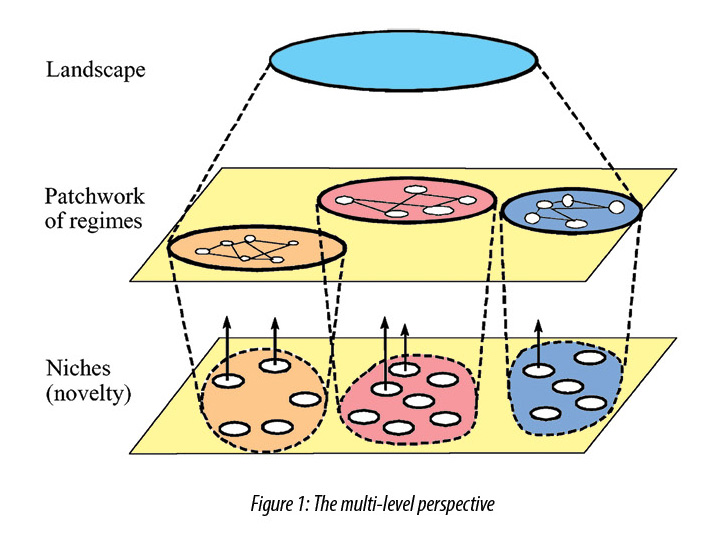
Figure 1: The multi-level perspective
What is currently experienced is the adoption and implementation of benchmarking standards, best practices, standardization, etc. – regardless of context! – is the ruling mindset or regime, which implies that any thinking about the validity of these concepts in a different context belongs to the niche realm and is pushed aside by regimes.
As mentioned before, this is no rocket science, but actual common sense. As a matter of fact, Paul Karl Feyerabend wrote in his masterpiece, “Against Method,”5 that one should not be proficient in the use of a tool, but be proficient in knowing when to use which tool. Also, in IBM’s famous “diversity management” experiment in the 1970s, the researchers noted that groups consisting of different members (race, as was the case of this research) would yield faster and better solutions compared to a homogenous group. It is nothing more than permitting stuff from outside the box to be compared with stuff inside with regard to their applicability in reality.
Conclusion: All Knowledge Is Contextual
As is currently happening with a lot of industries, companies have the tendency in financially crippling times to place an increased focus on financial parameters, which is reflected by placing people in top positions with a strong financial or business management background. These people usually have a bias towards looking at figures, which pushes the notion of context to the background. Standardization measures are put into place without much positive effect: the financial performance is not achieved, the company is not sustainable (financially) when looking at the middle- or long-term, and/or a lot of dismay, frustration, disbelief and distrust exist within the company.
Therefore, it is of the utmost importance that entities do not blindly copy success stories across the entire spectrum. Each and every tool, concept, methodology, theory, technology, etc., should be tested/validated first with the context in mind and needs to be adjusted where deemed necessary, or discarded when deemed unfit/unrealistic for that context. Science, after all, that is not grounded in reality is science fiction.
References
- Moore, R. Selecting the Right Manufacturing Tools. What Tool? When? Burlington: Elsevier, 2007.
- Lachman D. A., Tjoen A Choy R. O. F. Assessing Transitions to Benchmark Performance. Uptime Magazine, June/July, 2012.
- Geels, F.W., Technological transitions as evolutionary reconfiguration processes: a multi-level perspective and a case-study. Research Policy 31 (8/9), 1257–1274, 2002.
- Lachman D. A. A survey and review of approaches to study transitions. Energy Policy 85, pp. 269-276, 2013.
- Feyerabend, Paul. Against Method. Outline of an anarchistic theory of knowledge. Verso, s.l., 1975.