With greater pressure to maximize the lifecycle of assets, a significant investment and portion of a site’s budget is spent on the preventive maintenance (PM) program, but fails to deliver expected results and optimal value to the organization.
Inefficiencies in reliability strategies consume valuable resources, emotional layers of “intent” provide little protection while hidden gaps (risk) lower effectiveness, resulting in higher than expected reactive maintenance levels, cost and negative operational impact.
What’s Wrong With Our PMs?
There are many contributing factors in a dysfunctional PM program. Individually, these problems are painful, but when combined, they compound the problem with unforeseen consequences.
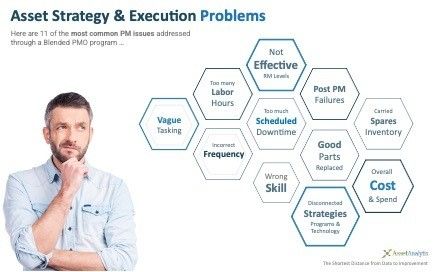
Example: Changing parts because it’s February, not because they are defective.
Effect: Higher scheduled downtime because it takes more time to replace parts than to monitor condition; Elevated parts stocking and cost; Vague tasking requires higher skills with a variety of outcomes, including higher post-PM failures on intrusive activities.
PM optimization (PMO) seems like the logical solution, but PMO is a term loosely used, implying good
intent and overall improved system performance. After all, who wouldn’t want to optimize their PMs? The challenge is defining and deploying the process when there is no shortage of varying opinions, approaches and methods on what is believed to be optimization.
The Solution
Blended PM optimization (bPMO) is a different approach, not just adding “blended” to a common and tired term. bPMO is a full end-to-end process, infused with lean principles for standardization and efficiency. Blending incorporates the absolute best of proven reliability techniques, tools, reporting and analytics, delivering maximum impact in both effectiveness and efficiency across the entire program, no matter the condition of your computerized maintenance management system (CMMS) data.
bPMO works across the Uptime® Elements A Reliability Framework and Asset Management System™. Most believe a PM optimization effort focuses solely on the PM element, but reliability strategy development (Rsd), balanced around criticality analysis (Ca) result in many aspects of the entire asset management program.
The impact of working on the right assets with the right process has a profound step change impact on scheduled and unscheduled downtime and overall asset management performance and cost.
Beyond the reasons in Table 1, there are many additional bPMO program justifications, including:
1. Your PMs are the most controllable constant in your entire maintenance program.
In your day-to-day maintenance activities, there are many moving targets, with things not always going as planned. In all the chaos, your PM program is one of the few constants that should have no surprises. Your PMs come out as scheduled, month after month, containing the same tasks, with the same skills and consuming the same parts. This is a fixed target at which to accurately develop, anchor and execute your plan of attack.
2. ROI is immediate.
Because you are attacking known, routine and scheduled work, the gains from a blended PM optimization program can be immediately realized. The moment you complete the first exercise, you will deactivate the old PMs and replace them with the optimized strategies, unlocking improvements you’ve accomplished.
3. Improvements can be leveraged.
Most improvement initiatives do not have such a profound ripple effect as a blended PM optimization exercise. This program is one of the rare efforts that can be directly leveraged across all like-for-like assets and, with slight adjustments, be applied to other similar assets, resulting in a much larger benefit footprint across your site.
4. Results are perpetual.
It is like winning the lottery each and every year! Because you are improving the constant,
repeatable preventive maintenance unit of work as described in the first point, all improvements realized in the second point are continuously experienced at each interval they are issued. You can think of this as an annuity payback for the small investment made up front.
What’s the Holdup?
If a problem directly affecting delivery, cost, safety, quality and morale has been defined and the business impact the bPMO process can make is known, then why is the site not already optimized?
There are a few issues that limit a site’s optimization solution, including:
Time and Bandwidth – Current alternative methods, such as a failure mode and effects analysis (FMEA) spreadsheet approach, can take a tremendous amount of time and resources.
“The current FMEA spreadsheet approach to optimizing the PMs is an independent, manual and arduous process, restricts leverage ability/scale, does not account for all disparate activities, and takes a tremendous number of resources to execute from both corporate and site staff.”
Matt Erikson
Global Reliability, 3M
Process Intimidation – Complex methods aren’t practical and inefficient. They require subject matter experts (SMEs) to manage efforts and are very complicated, limiting the participation of colleagues.
No Standardization – The manual process is performed differently in each exercise. The only thing standardized is the form used.
Speed of Scale – The current approach isn't leveraging work between sites and is limited to physical support.
Limited Visibility and Central Management – With disconnected spreadsheets and site efforts, it is difficult to coordinate and manage the process, demonstrate value and solicit executive sponsorship.
Cultural Resistance/Headwind – Site maturity does not view reliability with the same mindset and expectations as safety.
The bPMO process is more than simply improving tasking on a job plan; it optimizes the process of optimizing. Front-end strategic asset targeting and program management defines, measures and analyzes the problem. The 10-step tactical optimization improves the strategy. Ongoing process analytics provide insight for control of the PM program for a total and sustainable continuous improvement model.
Once the right assets are selected, follow the 10-step optimization process.
- Develop a reliability hierarchy to maintainable components.
- Collect all legacy activities.
- Baseline current PM performance.
- Confirm criticality.
- Map legacy tasks to the reliability hierarchy.
- Eliminate non-value-added tasks and optimize the remainder.
- Close gaps with risk-mitigating supplementary tasks.
- Develop optimized job plans.
- Balance labor.
- Activate the optimized plan in your CMMS.
The effort solicits engagement from all functional groups in the organization (the pull of employee engagement), delivers efficient reliability, and generates velocity in the volume of work that a team can accomplish. The net result is cultural transformation with a partnership for reliability in half the time.