This article shows how Sembcorp, in partnership with change management consultants Reliable Manufacturing, rose to the challenge and galvanized its leadership to engage the whole workforce out of narrow workgroups and into delivering outstanding results through proper teamwork. It is a story of ‘the blood, sweat and tears’ that were shed to overcome a huge range of challenges and legacy issues to restore performance and pride in the operation.
Background
Sembcorp provides steam, power and other utilities to all of the major manufacturing companies on the Wilton International site in Teesside, United Kingdom. The site was built by ICI in the 1940’s, but by the 1990’s a change in strategy by ICI brought about the gradual sell off of the ICI bulk chemical businesses on the site. This brought with it the prospect of the ultimate closure of the aging Wilton Power Station. In 1999, Enron bought the power station along with the rest of the site’s utilities and services operations, and began a growth strategy which was cut short by the company’s global collapse in 2001. After 18 months of operating as a stand-alone business, the business was bought by Singapore-based Sembcorp Industries in the spring of 2003 and it now operates as Sembcorp Utilities (UK) Ltd. Since then, Sembcorp has invested more than £150 million in its assets and further enhanced its reputation as a dependable supplier of high-quality utilities and services.
At the same time, the underlying business has been put on a sound financial footing. However, good business performance has been aided by the ability to import steam from a third party utility. This backup supply was used whenever Sembcorp’s own assets were unable to deliver the required steam demand to its customers. Ironically, due to the commercial nature of the contract, the use of third party steam was often more profitable than running Sembcorp assets, a situation which led to a reduced need to maximize the capability of the existing asset base.
With this favorable long term third party contract due to end, by 2005, Sembcorp management had concluded that in order to maintain its business position, strong action was required to turn around the performance of its assets. The company needed to become self sufficient in terms of its ability to supply steam to the Wilton Site. Without this change the business could face an uncertain future.
The Challenge
The challenge is described by Jane Atkinson, Vice President Utilities Operations, “I joined Sembcorp in late 2004 and quickly became aware of the massive challenge I had inherited. Morale was at an all time low, a “make do and mend” culture had set in, and plant and equipment that was the best available at the time of construction, was aging and unreliable. Although we had large volumes of procedures covering every last detail, they weren’t being applied in the same way and many were, frankly, out of date.”
“I also became aware that this wasn’t the only area of concern. We had neglected some equipment, and our buildings required significant restoration,” Jane continued to explain, “But most of all we had neglected our people. With the ICI Divestiture and resulting uncertainty, the work force had become depleted as people secured careers elsewhere. Many of those remaining seeming to accept that they had ‘a job for life’, and were content that they would be financially secure as they moved into retirement.”
“Our whole culture was one of ‘run it and fix it’. Departments were working in ‘silos’ with little obvious co-operation. Maintenance and Operations were content with blaming each other, and were not engaging with other supporting functions such as stores, purchasing, HR and IT,” Jane added, “In addition, I personally had to deal with comments like ’What does a manager from outside the power industry know about running a power station?!’”. But, with the realization that the outsourced steam contract was to end, there was a desperate need to turn things around”.
Jane was tasked with leading and delivering the change.
Strategy and Change Process
Given such a huge task, where do you start? In 2005 Reliable Manufacturing Ltd, a reliability based change management consulting firm, facilitated a Manufacturing Excellence Master Class for the Utilities Management Team. The Master Class was led by their principal consultant Ron Moore, an internationally recognized expert on Manufacturing. Participating with Jane and her direct reports were first line supervisors and union representatives. The event began the process of engagement and enabled Jane and her co-workers to make an initial benchmark of their practices and performance against world class parameters. The Master Class highlighted the task ahead and the need for urgent action. Above all was the recognition that restoring pride in doing a good job and winning the hearts and minds of those working on the site was a fundamental requirement if the change was to succeed. It was going to be a massive challenge, but one that had to be taken on.
Jane was also keen to expose her team to organizations that had faced similar challenges. One of the visits was to BP Grangemouth to learn about their site-wide Operations Excellence Program. Jane and her boss Tom Davidson were impressed by the stories told by the BP staff of how they had transformed their performance by engaging their first line people in the change process. Following this visit, Reliable Manufacturing was engaged to develop and lead a two year Change Management Process for Sembcorp, which would incorporate the engagement principles as seen at Grangemouth.
At the heart of the Change Process, which was led by Reliable Manufacturing’s Andrew Fraser, were two main elements. Andrew described them, “The first element was a ‘bottom-up’ cultural change process at shop floor level aimed at engaging people and developing cross-functional working throughout the organization. This was followed by a ‘top-down’ process focused on aligning the management team and analyzing critical plant equipment and work practices.”
From The Bottom Up
The initial, and the biggest, priority was changing the organizational culture. Jane explained, ”We needed to communicate the requirement for change to people who, from previous experience, had little trust in management. So, in early 2006, we launched a series of engagement workshops, running two workshops a month, for all of our employees”. These workshops featured The Manufacturing Game, which was developed at DuPont Chemical Company in 1991 by Winston Ledet, Ph.D. and others as a tool to facilitate organization change. “The Manufacturing Game was an excellent way of engaging our workforce in the Change Process. The Game demonstrated the complexities of running our assets, how the decisions and actions in one area impacted on other departments, the value of cross functional working and the importance of eliminating thousands of seemingly insignificant defects from our operation.”
During the workshops the participants discovered for themselves why there was a need for change and heard directly from Jane her vision for the site. “In addition to Maintenance and Operations staff, we included regular Contractors and staff from HR, Purchasing, Stores, Accounts and even IT. People were generally receptive to what I had to say and actively participated in discussions about the things we collectively needed to change.”
Toward the end of each workshop, small cross-functional Action Teams were formed with the purpose of converting the discussions into concrete actions to eliminate defects from equipment and work practices. Since the start of the process, well over 200 Action Teams have been formed (see Figure 1, note data ends Nov 2007).
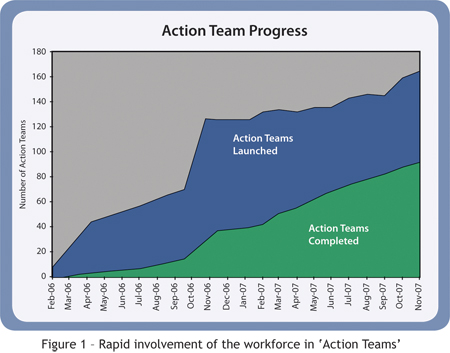
This approach encouraged a sense of personal responsibility for making the changes, and fostered ownership and pride in the new standards being implemented. These three components - responsibility, ownership and pride – are critical to achieving cultural change in any organization, and Sembcorp proved to be no different.
Many of the teams have successfully tackled repetitive problems, which has delivered improved availability, cost reductions and improved Health, Safety & Environmental (HSE) performance. In addition, the improvements released manpower that had previously been repairing equipment, which now could be redirected to focus on more improvements. For example, An Action Team, led by mechanical fitter Dave Scope met about improving boiler availability by targeting coal mill feeder issues. One of the major causes of feeder failures was the unreliability of the chain tensioning unit.
Dave came up with an innovative re-design of the tensioning unit that addressed the problem, and as a result, reduced boiler downtime by 13 days per annum. Another Action Team, led by E/I Supervisor John Haveron, was frustrated that their daily plans were being disrupted by requests to provide temporary 110-volt supplies for portable tools used by contractors. Only fixed 50-volt supplies were available in the plant. The team purchased 110-volt transformers and positioned these at strategic positions throughout the plant. The result was a saving of over 400 man hours, as well as a reduction in hire costs. These and other Action Team successes required very little up front analysis and enabled Sembcorp to almost instantly put some ‘rubber on the road’. Crucially as well, the creativity of the workforce was beginning to be tapped.
Following up on the workshops, a series of bi-monthly Reliability Forums were held. Attendees represented all aspects of the business, including frontline Maintenance and Operations people. The Forums helped to build momentum by providing people with recognition and encouragement as they presented their Action Team success stories. The Forums also provided the opportunity to identify and take action on barriers that needed to be removed to encourage more defect elimination. One such barrier discovered early in the process was the lack of communication regarding Action Team successes to those that were still not engaged in the change. A team set up for this purpose concluded that the best way to publicize successes would be by creating a reliability website. The website was established on the Company intranet and was positioned adjacent to the safety website to emphasise the importance of reliability and defect elimination. People can update progress on their Action Team directly. In addition to reading success stories, all staff can view which defects are being tackled, and who’s involved.
As the Change Process gathered pace, further workshops were held to build organizational capability. These ‘Supervising the Change’ workshops were open to leaders and indeed anyone, irrespective of their position, who wanted to get more deeply involved. The workshops were particularly effective in helping to redefine the first line leader’s role; moving from just coping with problems to identifying recurring defects and launching further Action Teams.
From The Top Down
Once the bottom up cultural change was well underway, the next stage of the Change Process was to align the management team and identify critical systems and practices that needed improvement. Like many businesses, Sembcorp had limited resources to devote to improvement. In fact, many experienced personnel had been lost in a voluntary redundancy exercise in 2000, leaving the business significantly depleted. The current resource base was already stretched as it began to prepare for two back-to-back six yearly overhauls of the main boilers, which were scheduled to take three months each. So it was vital that the limited time that management had at its disposal was not wasted on secondary issues but was directed at addressing critical priorities.
In order to flush out the critical areas, a series of Criticality Studies and Practices reviews were facilitated. First, the site was divided into several areas and criticality studies carried out. The resulting information from one area of the site is shown in Figure 2.
“The criticality studies were a simple and effective method of identifying problematic equipment,” Operations Plant Manager Steve Purvis explained, “The studies took into account both past performance and any potential changes to the condition or use of the equipment that could affect future performance. They helped us to allocate resources to the equipment that was having the biggest impact on the business.”
In parallel with the criticality studies, a detailed review of Operations and Maintenance practices was conducted. This provided an in-depth understanding of how work was currently being carried out. This was compared to best practice standards, and priorities for action were identified. Unlike the Action Teams that were numerous and relatively small in nature, the improvement tasks emanating from the studies and reviews were larger in scale, typically requiring more management involvement and funding.
A series of Project Improvement Teams (PITs) were formed, each team with a specific charter (see Figure 3), sponsor, leader and team members. The teams were required initially to report progress on a monthly basis. However, although some teams made good progress, other teams struggled to balance meeting day-to-day needs and finding time for improvement.
It was recognized that resourcing was a critical issue, and this led to an external recruitment campaign to find additional key resources and skills for the business. However, obtaining new recruits and bringing them up to speed was, at best, going to be a six to nine month process, and in some cases much longer. In the mean time, a short interval control process was introduced to accelerate the delivery of results.
Everyday at 8:00am, Jane held a one-to-one update session with one or more of her direct reports, each of whom was sponsoring a PIT. Initially this commitment added more strain to those that were already fully loaded, but it helped to crystallize issues that were impeding progress and ensured that a documented action plan for the next seven day period was put in place. This proved to be a crucial step in delivering the results. As the bottom-up and top-down processes began to kick in, a Reliability Steering Group was formed to manage the overall improvement process. The steering group provided a key role in monitoring progress, identifying any gaps and ensuring the correct priorities continued to be worked on.
Improvements
Sembcorp followed the Reliability Model shown in Figure 4 as an underlying core philosophy in tackling its performance issues. The model demonstrates that the root causes of reliability issues can be a result of factors in design, purchasing, stores, installation/start-up, operations or maintenance practices. Sembcorp has made substantial improvements to its operating processes using this model. Described below are a few examples:
Coal Quality – Contamination of coal supplies with metal objects and poor quality coal were found to be key root causes affecting mill reliability and boiler performance. Improvements to the coal specification, screening, metal detection and changes in supplier have been made.
Mill Overhaul Procedure – The quality of maintenance work on mill overhauls has significantly improved since the introduction of a detailed overhaul procedure complete with digital photos and hold points for engineering verifications and inspections.
Lubrication – External expertise was engaged to help make a step change in Lubrication standards. As well as improved quality of lubrication, the number of machines under a supervised lubrication regime has risen from 60 to well over 600.
Feedpump Operation – There was a widely held view that the poor performance of boiler feed pumps was wholly due to the age of the pumps. However, upon closer inspection, a PIT team found they were able to improve performance by tightening up the operations procedures, particularly around start up and shutdown of the pumps. The value of cross-functional team working was demonstrated by the quick removal of a long-standing performance issue on one of the pumps. It came from one of the team members, who had not been previously involved, asking “a silly question”.
No defect, no job! – It was common-place for work to be done on the basis of verbal requests. This often resulted in “who shouted the loudest” getting work done as opposed to what was most important. A key turning point in behavioral change occurred when the decision was made that no work would get done without a properly written and authorized request.
Defect Tagging – Many people were frustrated that repairs, particularly to steam and water leaks, were not getting fixed as quickly as expected. The fact that it wasn’t obvious whether a leak had been reported to maintenance was part of the problem. Following a visit to INEOS CHLOR, one of the major chlor-alkali producers in Europe, a visual defect tagging system was introduced. In addition to raising an electronic request for maintenance, the operator would tie a defect tag on the equipment. The tag description includes date, brief statement of the problem and name of the person who raised the request.
Problem Solving Skills – A standard system for root cause analysis was adopted across Utilities to provide a common language and process for problem solving. Criteria have been established which trigger when an investigation is required.
The Results
Three years into the process and the huge effort expended by all of the team members, and other personnel, is more than paying off.
The culture has now changed, with everyone recognizing that they have a part to play. “At the beginning of the journey, we had a 30/70 split between people who were involved and supportive of the change and those that were not,” Jane said, “Now the split is around 70/30, which not only makes my job easier, but is helping us to make much faster progress than we were in the early days.”
Mick Trodden, a shift manager who left the company for a year, saw a definite change when he returned. “Things had certainly improved, there was a more positive atmosphere and pride seemed to have returned. You could tell that some serious work had been done on the reliability of the plant and equipment,” said Mick, “The way it was operated and maintained had improved and procedures were once again being followed. Many areas had become cleaner and tidy work areas had returned.”
Plant performance has also been transformed. Coal mill availability on one of the two main steam boilers increased by over fifty percent in a year (See Figure 5), along with a commensurate reduction in maintenance costs. At the plant level, overall steamboiler availability has increased by thirty percent. The process has also recently been applied to Sembcorp’s new Biomass Power Station (Figure 6) - with spectacular results. In less than six months after applying the process, availability of plant more than doubled. (See Figure 7.)
With the combined bottom-up and top-down approaches to improvement, the application of the reliability model and a massive amount of effort by all staff involved, Sembcorp has taken a monumental step forward toward their overall goal of becoming self sufficient in steam supply to its Wilton Site customers. And almost as impressively, in spite of undertaking a huge amount of change, Sembcorp has continued to improve its excellent service levels to customers.
People Perspectives
This major transformation effort has centred on the involvement of people. Here are some of the perspectives of key individuals who were involved in the change:
Ron Moore, Reliable Manufacturing’s principal consultant, describes his initial impressions in 2005. “It was like ‘stepping into a void’. There was a lack of drive, energy and leadership. There were huge challenges to deal with, which were compounded by the use of multiple power generation technologies, and multiple fuels including oil, gas, coal and wood chips. There were leaks of air, water and steam everywhere and a seemingly general acceptance of the chaos that was the normal day; many people were actually enjoying ‘firefighting.’”
Jane Atkinson remembers shedding “blood, sweat and tears” during the process. She could see the major challenge they had in front of them. Although she was confident it could be achieved, it was going to take a huge amount of dedication and hard work. And time was pressing. They were fast approaching the cut-off date for the end of the contract for importing steam. Her days were full – opening and closing workshops, followed by de-briefing and dealing with resistance from those who didn’t understand the benefits and the process. She also had to cope with the skeptics who thought it was all a waste of time and it was probably only a ‘flavor of the month’ initiative. Sheer determination, and the fact that the alternative was neither acceptable to her, nor to the business, kept her going. She knew she had to make changes in the culture in order to move forward.
“As people were given responsibilities to lead key improvements, it became clear that the ability and enthusiasm of some people had been overestimated and so had the support of some of the senior management team, whom I needed to lean heavily upon in order to deliver the objective,” she said, “As we learned more about people we made adjustments in the process to compensate.” It was important to keep focusing on the positives. Seeing people change, and the way they were embracing the change, gave Jane and the team much needed encouragement.
Andrew Fraser, Reliable Manufacturing’s Change Manager, reflects on the complexity of the challenge. “The strategy we developed for the project essentially remained the same throughout the change process. A key element of the implementation, however, was the discipline to review progress at regular intervals and take into account new information that had emerged since the last review. Some of this learning related to a better understanding of individual capability and some of it was the discovery of new and sometimes surprising supporters of the process throughout the organization. We took advantage of this new knowledge to modify our tactical plans as the implementation gathered pace.“
John Haveron, I/E Supervisor, and Andy Fisher, I/E Planner, express how the process impacted them: “We got our Friday nights back! We used to hate Friday’s. When everybody else wants to go home and start the weekend, we were often left trying to sort something out. This is the exception now, which is how it should be. If the business hadn’t changed direction in the way it did we don’t think we would be here today, we would have ‘walked’ or have been off sick. We were over-worked and battle weary from fighting to keep things going.”
John and Andy also found value from getting to know people from other parts of the organization. “We met people like Paul McCann from purchasing who helped us sort out some problems we were having with gas bottles. Meeting people from other parts of the organization and sharing our issues made it easier to find solutions to our problems.”
Paul McCann, Senior Buyer, shares his perspective, “The approach taken by Reliable Manufacturing was familiar to me, as this is an area I had studied at University. The Manufacturing Game got people involved and helped them realize how they were working and how this could improve. They became aware of the need for enhanced reliability at the plant and the impact of what they do on the business. Generally, they just became aware of the bigger picture and how they could make a difference. From my point of view, the forums opened up a huge internal network of people who I had not had the opportunity to meet previously.”
Technical Plant Manager Chris Plews describes how they are having success in applying the reliability model to Sembcorp’s New Biomass plant, commissioned in 2007. “When we saw the effect the process was having on our mature assets, we decided to adopt the process on our £64 million Biomass plant. Within months we were seeing dramatic improvements and it has helped us achieve record performance from the plant. We want to see reliability and defect elimination become second nature and part of the natural way we work. I only wish we had done this earlier, the benefits make me wonder why we didn’t do this three or four years before we did”.
The heart of the change process is empowering people to do a better job and contribute to the business. Dave Scope, Mechanical Maintenance Fitter, describes the change for him, “The whole process has been enlightening for me personally. It has made me aware, for the first time, that I am empowered to make a difference. I now know that I am empowered to turn my ideas into practice and make things happen. I have been exposed to methods of solving problems, flagging them up and having an input into the solution. I have seen the benefits brought about from mixing everyone together from across the different disciplines within the business to deliver benefit. “
“Through the forum, I have been able to show others what is possible and I am determined to keep on “picking fault” and challenging things with a view to pushing forward improvements continuously”.
The Future
The pride and enthusiasm is back in the business, but the journey is not over and will continue well into the future. The emphasis on reliability and defect elimination continues to have a high focus. Sembcorp is committed to strengthening their team at all levels by engaging people with expertise and enthusiasm to drive change. The recent recruitment of new people has brought fresh energy and helped to spread the load. The future is looking bright and Sembcorp UK is looking forward to expanding the use of this improvement philosophy in all of its operations. They have demonstrated how, in partnership with external expertise, they are able to bring an aging, run-down, heading for closure site, back to life. Sembcorp is currently looking at expanding its business by acquiring other major utilities sites in the UK and Europe. Reliable Manufacturing and Sembcorp look forward to using this proven strategy to help transform these sites too.
Judith Charlton is the owner of Judith Charlton Consulting, an independent PR consultancy based in Cheshire, England. She has over 25 years experience in public relations working for high profile blue chip companies, including BNFL and Airtours Holiday. You can visit www.charlton-consulting.co.uk for more information.
Steve Lipscombe is managing director of marketing consultancy firm RONIN Marketing, based in London, England. More information is available at www.roninmarketing.co.uk.
Judith and Steve would like to acknowledge the generous contributions of time and effort of the following folks: Jane Atkinson, Terry Waldron, Steve Bishop from Sembcorp, and Andrew Fraser of Reliable Manufacturing (www.reliable-manufacturing.com).