Risk taking was then reexamined and job functions and accountabilities were being scrutinized at some corporations. In line with these commendable endeavors, a major oil producer’s corporate maintenance reliability (CMR) team asked me to respond to some interesting questions. They expressed the hope that I might provide some insight.
To recap the main issue, a few team members were given the title “reliability engineer” while working in an upstream (exploration and production) segment of the corporation. Upon being reassigned to certain corporate downstream (refining and manufacturing) segments, they found out that downstream management considered reliability assurance as simply a function of any discipline of engineering and not a stand-alone or recognizable discipline. That caused puzzlement and some frustration with several team members.
As the CMR team of course knew, a few engineering schools offer reliability engineering curricula. However, in the downstream sectors of industry, discipline engineers---also called subject matter experts later in their careers---are generally focused on projects. They are only occasionally called on to provide assistance in their particular area of expertise. This usually happens when there are serious breakdowns or when in-depth troubleshooting is needed. The point: Except where titled positions exist in a particular industry segment, reliability is rarely a focus (except tracking production losses as a lagging indicator). And even production or operations engineers often do a large amount of small project work.
That then led to the first of two direct questions posed by the CMR team: Is reliability engineer a titled position in the exploration and production (E&P) side of other major petroleum producers/ refiners, or is this job function similarly buried in what a discipline engineer or subject matter expert “might” do on a part-time basis in his or her specific area of expertise?
The second question was only vaguely related, but the team asked if many of the other petroleum producers/refiners recommend or require certification, such as Certified Maintenance and Reliability Professional (CMRP).
ANSWERS START WITH DEFINITIONS
I tried to be brief in my “summary of a short summary” of answers to the two questions. Answers, I believe, must start with definitions:
The definition of maintenance is to maintain equipment in the as-designed and as-built state.
The definition of reliability engineering is to:
- specify equipment and systems so as to design-out maintenance;
- define if failure avoidance through upgrading is feasible;
- if “yes” on the above, define if upgrading is cost justified;
- if “yes” on the cost justification, take charge of implementation planning;
- at all times inculcate a mindset that will not tolerate repeat failures because repeat failures are indicative of not having found the root cause of a problem. Not knowing the root cause will set one up for the next surprise. The next incident could be fatal.
Keeping in mind these definitions, one would find subject matter experts in piping & vessels, machinery, instrumentation and controls, welding technology, metallurgy, etc., within major best-in-class petrochemical companies. Sometimes, these subject matter experts reside at the headquarters of an organization. In other instances, the machinery specialist may reside at and get paid by affiliate “A,” but spends time on issues that affect all affiliates. The piping & vessel specialist may reside at and get paid by affiliate “B,” but spends time on and communicates issues that affect all affiliates, etc.
At best-in-class companies, a subject matter expert spends a huge percentage of time (usually 60%-80%) on failure analysis and prevention. Failure prevention implies intelligent development and application of specifications, authoritative determination of weak links, and systematic upgrading whenever a cost justification exists or a safety hazard must be removed.
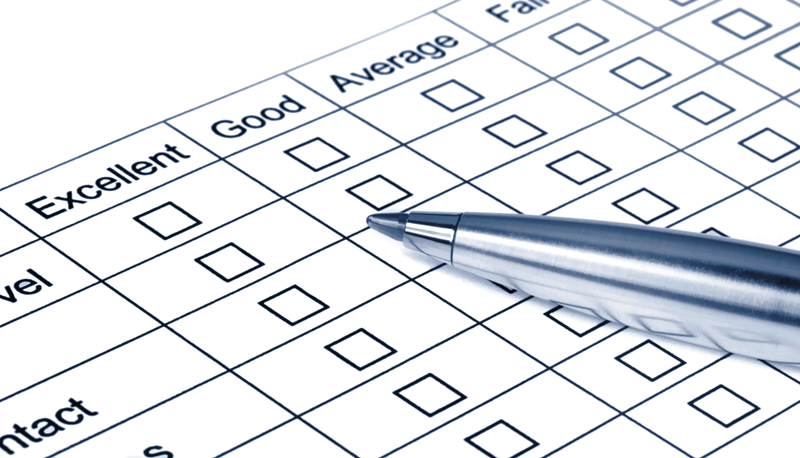

Best-in-class companies consider their subject matter experts so valuable that they cannot be burdened with maintenance involvement. By inference, the involvement of others in maintenance tasks is rather repetitive and routine; it is therefore given to others.
As long as one accepts the above and implements job functions and assignments along those lines, there is no need to use the title, “reliability engineer.” However, it would be implied that each of these subject matter experts is performing exactly as we would expect from a reliability engineer. Their role statement will say so.
In my experience, reliability engineers who are allowed to be fully absorbed in a maintenance department end up compromising under the pressures of maintenance. More often than not, the mandate of maintenance is to fix things quickly. There is little probability the reliability engineer immersed in maintenance tasks will be shielded from the fix it quick pressures. In contrast, reliability professionals with a clear role statement, a clear training plan and a firm resolve to know early in the morning how they will add value to the organization, will not allow themselves to be drowned by maintenance demands. Corporate management will support the reliability professionals’ stance on the entire issue. These successful professionals will have made it known that one cannot solve 20 different major machinery problems in a 40-hour week. Many of the million-dollar issues that beg resolution deserve the expenditure of hundreds of hours of dedicated effort.
ADDRESSING ORGANIZATIONAL MATTERS
This brings us to organizational issues. In an operating plant, the machinery expert would get involved and become the “owner” of, say, process pumps that have failed more than twice in a 24-month calendar period. The assumption would be that performing conventional maintenance has neither uncovered nor cured the underlying root cause of failure. A highly motivated subject matter expert understands the fallacy of encouraging procurement from the lowest bidder on the one hand and expecting to receive equipment designed for high uptime on the other hand.
It is further assumed that the role of the subject matter (reliability improvement) expert has been clearly defined in a solid role statement and the expert’s training plan is like an iron-clad contract. Both the role statement and the training plan represent a shared commitment. As to the training plan, both management and the employee will invest valuable time in targeted and results-oriented training. The full implication of this commitment precludes the standard management reaction of canceling training whenever the economy goes into a downturn.
It follows that the type of subject matter expert discussed here is an individual being groomed and nurtured as a professional by management. That’s where targeted training takes on real significance. In any event, we are clearly referring to “people assets” that are far more valuable than physical assets. The very notion that one could hire such an individual from a contractor is deeply flawed and can be refuted by plain logic and existing facts in the marketplace.
I felt the need to commend this CMR team on the crispness of their two questions and the astuteness of their own observations. In my experience, the designations subject matter experts, discipline engineers and reliability engineers describe the very same individuals. There was, however, a huge difference in the questioners intimating that their experts devoted most of their time to project work. It is my experience-based position that, to be worthy of contributing to a project, a subject matter expert must have plant-related knowledge. Therefore, the importance of actually stationing this professional at facility “A,” “B,” etc., cannot be overstated. A close substitute for in-plant involvement would be frequent and intense exposure to overseas startup assignments. That, of course, is a luxury that few petrochemical companies can offer or afford today.
Finally, a few comments on certification as a CMRP, or membership in the Society for Maintenance & Reliability Professionals (SMRP). I see these and similar certification pursuits as evidence of an individual reaching out and investing time to gain a measure of recognition. Chances are one’s sense of self-worth increases after passing a one-day examination for a professional engineer’s license. Going for certification is quite commendable. However, certification alone is not worthy of reward in and of itself. Regrettably, I do not believe that many of these membership entities are successfully (nor are they intent on) imparting the in-depth reliability improvement knowledge that is sorely needed. Case in point: The home facilities of most CMRPs have repeat pump failures and entire facilities are making few inroads towards eradicating repeat failures. What does this tell us?
In summary and from the above, it follows that the answer to Question 1 is essentially “no,” but the reliability job function at best-in-class companies is clearly and effectively covered in other ways.
Regarding Question 2, an individual should be rewarded on the basis of performance and tangible contributions. These should be discussed during periodic performance appraisals and the person whose performance is being evaluated should list them on a piece of paper. During the yearly performance evaluation session, it will become clear that a CMRP with certification but no motivation is worth much less than a motivated self-starter who reads, networks, implements and applies, but is not a member of SMRP nor holds a state-issued professional engineers license.
Decades ago, one best-in-class company reimbursed its engineers every year for two professional membership fees. In return, the company expected these professionals to share their knowledge by communicating and networking. It was not mandatory to be a member of anything, but it soon became evident that, on average, the knowledge accumulated by those who attended the local meetings of certain selected engineering societies was enhanced. Attendance at some meetings and conferences led to networking in the truest sense of the word. It allowed the member to call fellow members elsewhere for advice. Much of this networking yielded immense returns on the investment.
Finally, at some best-in-class organizations, depending on only the educational backgrounds of employees was deliberately and clearly discontinued as time went on. In one organization, when an engineer with a master’s or doctoral degree was hired, initial advancement was based on salary curves for people with those degrees. However, after seven years with this organization, all salary curves merged and progress was based on nothing but performance rankings. I believe that’s how it should be done throughout the hydrocarbon processing industry. Perhaps it would be one more step towards disaster avoidance.