With this ease of accessibility and expanded choice in camera systems, it is often difficult to decide exactly which infrared camera system is right for you or your company.
The best place to begin in the process of choosing an infrared camera is to have a firm understanding of the requirements of your proposed application. Determine first whether your application is qualitative or quantitative in nature. Qualitative applications are those where thermal patterns are the definitive principle in your application. In this type of application a thermal imager is all that is required. These include applications such as security and surveillance as well as many process control and quality assurance applications. When accurate temperatures are a requirement of your application, you need to consider an imaging radiometer, which is a quantitative instrument. Table 1 is a guide to some of the principles that should be considered when looking at the purchase of an infrared camera.

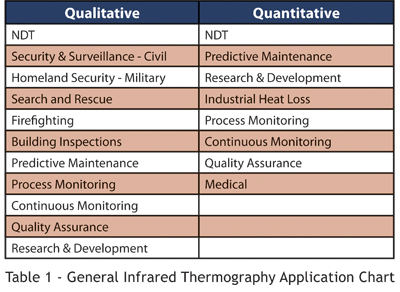
The only way to determine which camera is the right one is to consider all of the requirements of your application, and then see which camera fits. For example, if you are going to do electrical inspections and require accurate temperatures, you need to determine the smallest object you will require a temperature of and the farthest distance you will be from that object. Using the information in the IFOV and IMFOV section of this article, you can calculate the value you need for an IFOV number and compare this to the manufacturer’s specifications. If you need to be able to measure 400°C, a camera which only measures up to 250°C will not be suitable, no matter what the price.
Price
Although many infrared camera purchases are driven by price, price should be a secondary consideration after the camera’s specifications and features have been considered. The price of infrared systems vary from approximately $4,000 US to in excess of $100,000 US. Sometimes budgetary restrictions are a determining factor when choosing an infrared system.
It must be realized that the saying “you only get what you pay for” is true when considering an infrared camera. There is no sense in buying a camera based strictly on price if the camera is not capable of performing the application it was purchased for. On the other hand, there is no benefit in paying for features and functions in a system that will never be used in the application the system was purchased for.
Specifications
Before even beginning to look at the purchase of a specific infrared camera, it is wise to first define the parameters of your application, and then research the available cameras. You should draw up an application matrix in which you will enter all of your needs including specifications, usability and ergonomics, accessories, software, and after-the-sale support.
Most manufacturers publish a standard set of specifications. Some of these specifications can be valuable while others are not, depending on your application. Some of the specifications may or may not apply to your specific application, but we will try and include the main considerations. There are two types of resolution: Thermal Resolution and Spatial Resolution. Thermal resolution defines the ability to see and/or measure energy/temperatures, while spatial resolution defines the ability of the system to see physical detail.
Thermal Resolution
These are fixed values given by the manufacturer.
Temperature Range – What will be the highest and the lowest temperatures of the objects you will be trying to look at? This is the first question you must consider. Many of the newer, simple, low-cost cameras only view objects from ~20°-40°C to 150°C. Some of these cameras measure up to 250°C. These temperature ranges are usually suitable for many building science, electrical, or mechanical applications, but often not suitable for process, NDT or many R&D applications. There are a great number of more complicated, higher priced systems, that can inspect objects in excess of 2000°C.
Accuracy – Many of the infrared cameras on the market today publish a temperature accuracy of + or – 2°C or 2% of the range, whichever is greatest. In general, they are much more accurate than the published figures. These accuracy figures are given for blackbody references and do not take into account errors introduced by factors such as emissivity and background reflected energy. This accuracy can be greatly increased by comparing a known temperature close to the temperature of the object of interest. In most predictive maintenance and NDT applications, these values are acceptable. R&D applications often require greater accuracy and a blackbody reference source can be a viable option.
Thermal sensitivity – While temperature accuracy might seem to be fairly rough, thermal sensitivity has become very fine. There are cameras on the market today that are capable of detecting a thermal difference as low as .05°C or less. In general, there are two tests to determine the thermal sensitivity of an infrared camera. The NETD (Noise Equivalent Temperature Difference) tests only the temperature difference required to raise the signal from the detector, to a measurable level above the electrical noise of the system. This is an instrumentation test only. It is not a good test of overall system performance.
The MDTD (Minimum Detectable Temperature Difference) test is the best test to compare the sensitivity of the entire system as it takes the entire system into consideration. This test requires a technician to be able to see a temperature difference using the visible image of the camera. When comparing systems, one must be sure that the figures given by the manufacturer are from the same type of test. Your application will determine which test is the best to help you choose the right camera system.
Spatial Resolution
These values are given by the manufacturer but are dependent on the lens used on the camera. Some cameras do not offer interchangeable lenses, which means that the values are fixed. With other camera systems, there are a variety of interchangeable lenses available. Each camera/lens configuration has a separate set of spatial resolution specifications. These specifications describe the performance of the entire system. Manufacturers often stress the size of the detector, which is only a piece of the information necessary to determine what the system can see. A camera with a 320 X 240 focal plane array may or may not be able to see better spatial resolution than a 160 X 120 detector, depending on the optics of the specific system.
Field of view (FOV) – The total area that our camera sees is defined by the FOV value given by the manufacturer for each specific lens/camera system. This value is determined by a combination of detector size and lens optics as well as camera design. This specification is usually given in degrees. Various applications may require that the technician can view a certain object in its entirety at a set distance. Once the FOV requirements of your specific application have been defined, you can compare various camera FOV specifications to determine the right camera/lens combination for your application. As an example, in an ongoing NDT test, the technician must look at a 2m by 2m composite panel and be able to image the entire panel in one field of view for later analysis. The camera being considered has a field of view specification of 20° X 20°. This camera does not have interchangeable lenses. The distance available from the panel is 4.5 meters. The formula to determine the area viewed by this camera is:
Area = FOV in radians X Distance
To change the field of view in degrees to radians you must multiply the angle in degrees by .0175 (1 degree = .0175 radians, so, in this example, 20° = .35 radians).
The area viewable at the available distance is:
Area = .35 radians X 4.5 meters = 1.57, so
Area = 1.57 meters X 1.57 meters
This camera cannot view a 2m X 2m panel in one frame at a distance of 4.5 meters. Another camera must be chosen or the distance to the object must be increased.
Instantaneous field of view (IFOV) – The IFOV value describes the smallest spot that your system can geometrically resolve, or see the size and shape of. It is given by the manufacturer as an angle defined in milliradians.
It is called either the IFOV or Spatial Resolution specification. It is determined by not only the size/angle of the lens, but also by the number of pixels that make up the field of view. Other parameters, such as the fill factor of the detector elements, also come into play in determining this number.
The smaller the IFOV number, the better the resolution your camera/lens combination will have when examining small objects in the field of view. In your application requirements, you must determine the smallest object you will need to image and the maximum distance you will be viewing the object from. Once this is decided, you can examine the specifications of various cameras to determine which one will perform best for your application needs. The formula to determine this spot size is:
Size of Spot Resolvable = FOV in radians
X Distance
The IFOV value is usually given by the manufacturer in milliradians. To change the given specification to radians, simply move the decimal place 3 positions to the left (so, for example, 1.4 milliradians = .0014 radians).
An electrical maintenance technician needs to look at a conductor 2cm (.02 meters) in diameter. Due to safety regulations, the closest the technician can get to the conductor is 1.25 meters. For the camera with an IFOV of 1.4 milliradians, the smallest spot the technician can resolve the size and the shape of is as follows:
Size of Spot Resolvable = .0014 radians X 1250 cm, so
Size of Spot Resolvable = 1.75 cm
In this case, the camera considered above is capable of seeing or imaging this 2cm conductor at 1.25 meters.
The IFOV specification is an important consideration when evaluating an imaging camera.
Instantaneous measurement field of view (IMFOV) – When evaluating an infrared camera where temperatures are required, the IMFOV is a more valuable specification than the IFOV. This is really a combination of spatial and thermal resolution.
The IMFOV defines the smallest area or object size that you can evaluate, and still accurately measure the radiated energy from that area or object, at any specific distance. If the area or object is not large enough, the energy the camera sees from the spot will be eclipsed by energy from the background and the camera will not calculate the actual temperature of that object or area. The IMFOV is defined by an angle that is usually given in milliradians because of its small size. Many manufacturers do not publish this value despite its obvious importance when trying to calculate the temperature of small objects in the field of view.
In the past twenty years, I have conducted literally thousands of experiments to determine this value. Generally, I’ve found that the size of an object necessary to achieve accurate measurement is usually 3–4 times larger than the size calculated by using the IFOV value published by the manufacturer.
Size of Spot Measurable =
IMFOV in radians X Distance
Using the example in the section above on the IFOV, we will consider a spot size of 2cm at a distance of 1.75 meters. Let’s assume that this camera is better than average and the IMFOV is only 3 times that of the IFOV. This gives us an IMFOV for the above camera of 4.2 milliradians.
Size of Spot Measurable = .0042 radians X 1250 cm, so
Size of Spot Measurable = 5.25 cm
This reveals that the above considered camera cannot accurately determine the temperature of a spot any smaller than 5.25cm at 1.25 meters.
Wavelength
Today there are basically three different wavelength camera systems generally available. The longwave system uses a band width of approximately 8–14 microns. The shortwave or midwave system utilizes approximately the 2–6 micron window. The nearIR camera views approximately the 0.9–1.75 micron range. There are a number of specialty applications that require a camera system which utilizes a specific narrow wavelength band. An example of this is the “gas camera,” which has the ability to see fugitive emissions in petrochemical plants. This application requires a shortwave, cold shielded, filtered camera.
There are a number of application specific cameras and filters available utilizing specific wavelength regions. Theoretically, a longwave system is better for normal, near-ambient temperatures, whereas a shortwave system works better on above-ambient temperatures. The nearIR system will only work on objects with emitted or reflected temperatures above approximately 250°C. In practice, there are a number of other considerations such as the low maintenance with a longwave, uncooled camera, that are more important than the wavelength issue.
Frame Rate
While the frame rate is not usually an important consideration in PdM type applications, it can be a very important specification in many NDT and R&D applications, as well as some quality assurance situations. A frame rate of 30Hz or 60Hz is the standard on many handheld systems. For most electrical, mechanical and even process applications, this difference is not usually significant. Today there are systems available, that when windowed, can capture over 1000 frames per second. In a research application, where the burn-in time on a component is only .25 seconds, frame rate can be a primary consideration.
This also requires specialized, auxiliary hardware and a software package that is capable of capturing images at this rate and analyzing them using a number of various software functions. The requirements of your application concerning frame rate and analysis issues must be clearly defined before starting a consideration of any infrared camera system.
Usability and Ergonomics
There are a number of considerations when trying to determine the usability of a camera in a specific application. Some of these are as follows:
Camera Controls – For almost all applications, an infrared camera must have manual focus level, and span controls. Without being able to control the level and the span manually, many thermal anomalies will not be seen in the infrared image, especially in electrical inspections where there are often hotter objects, such as transformers and resistors. In AGC (automatic gain control) with no manual override, the camera looks at all the energy levels in the field of view and automatically adjusts the level and the span in the camera, constantly changing the settings on the image. This means that whenever the field of view changes, you cannot really compare anything from image to image. In an electrical inspection with a small hot transformer in the image, you will lose all of the thermal detail on the connections and conductors. Manual focus allows the operator to get a good image of the object of interest in the field of view. Most infrared cameras have a very shallow depth of field.
Weight – If the camera is to be used in a portable application such as electrical inspections, then the weight of a camera is an issue. If the camera is to be used in a fixed mounted application, weight is not an issue in general.
Battery Life – The life of the battery, and the cost of extra batteries, can be important considerations in a portable application.
Inputs – Depending on the application, the allowable power inputs can be an important consideration. Many cameras can accept voltages from +6 to +16 VDC. For some R&D type applications, controls such as an external synchronization can be an important consideration.
Outputs – In portable, PdM applications, the presence of various outputs is not usually an important consideration. In many other applications, outputs such as video, USB and FireWire™ can be important.
Image Storage – The ability to store images in the camera is usually accomplished by the use of onboard memory or a removable memory card. In some applications, the ability to exchange memory cards when there are multiple users can be an important consideration.
Display – In many applications, the technician must view the screen to evaluate the object being viewed. Considerations such as being able to rotate or angle the screen, an eyepiece for bright light conditions, or a remote view screen could be important.
Remote Control Capability – Today there are some systems available with remote wireless image capture and camera control. This can be a crucial consideration in some applications where a hostile environment is present.
Environmental Specifications – There are many environmental considerations such as operating temperature, storage temperature, and IP rating to be taken into account according to application requirements. These specifications can be acquired from the manufacturer.
Accessories
Many infrared camera systems have a wide selection of accessories available. Items such as an AC power supply are not included as part of the camera purchase with many handheld cameras, while battery power sources are not usually supplied with fixed mounted systems. In some instances, accessories such as a solar power supply can be purchased through a third party.
There are a number of specialized applications which require unique accessories such as narrow wavelength filters. With some camera packages there are a number of different lenses that can be purchased as accessories. On the other hand, there are less expensive cameras that do not have any available alternative lenses. Before selecting a camera package, list all of the requirements of your application and match them to the accessories available for each system.
Software
Infrared camera software can perform three basic functions. Software can control camera/data acquisition functions, image analysis, and reporting. Most handheld cameras come with analysis and reporting type software only. Today many higher-end cameras can still be portable, but allow for functions such as sequence image capture, and acquisition triggering to be controlled through a laptop computer. Most manufacturers have demo software or will have a sales person come to your location with a functioning copy of the software on their computer. Before purchasing a camera, make sure that you test the software to ensure that it performs the tasks necessary for your application easily and expediently.
It is important in some applications to have a software package that will export and import data from programs such as Excel. One of the key issues with infrared software is the ability to install the software and use it on a number of different computers. Some packages can only be installed and used on one computer per license. This becomes very awkward if there will be a number of technicians working with a camera.
For PdM applications, the software must be able to produce templates to ensure that your reports can be produced accurately and efficiently in a minimum time frame. This ensures continuity over time.
There are also a number of third-party software packages available in the market today for most types of applications. In many process control/continuous monitoring applications, only the camera head will be purchased from the IR camera vendor. The control portion of the application, including other necessary hardware and software, will be provided by a third-party integrator.
Warranty and Support
Warranty and support considerations are also application driven. There is also a “gut feeling” factor that should come into play.
Warranty – Warranty is fairly clear. Most cameras have a one-year standard warranty with extended warranties available at a set price. More important than the warranty time period is what the warranty includes and how warranty work will be conducted. Before buying a camera system, you should have these issues clearly defined and on paper as part of the camera purchase. An important question that must be answered is, “Does the warranty cover all parts and labor?” There is also the issue of shipping charges and where the system must be shipped to for warranty work.
The other part of the warranty principle is how long can you be without your infrared camera working in your specific application? It has been known to take over six months to get a camera repaired due to a number of complicated issues. The manufacturer would not supply a loaner camera, and the only option the camera owner had was to rent a similar camera at an exorbitant price. The buyer should be realistic in his expectations, but should not settle for less than is necessary. If the longest you can operate without a camera is two weeks, then part of the purchase agreement should include a clause that, in the event of warranty issues, the unit is either replaced within two weeks or a free loaner is supplied until your camera is repaired. With some specialty cameras this is often not a viable expectation. You should then look at all of the options suggested by the various manufacturers and select the one most appropriate for your application.
In determining how important the warranty issue is, you should also consider the rigors of the application itself. If your application requires a fixed-mounted, long-wave, microbolometer, Focal Plane Array camera, in a gentle environment, then warranty may not be a large issue. These cameras have basically no moving parts, and if they do not fail during burn-in times, then they have been known to operate flawlessly for years.
On the other hand, if your application requires a camera that is a handheld, short-wave, sterling cycle cooled camera that will be handled by a number of individuals with various skill levels in a rough harsh environment, warranty is a very important issue. With these cameras, the cooler has a limited life no matter what the warranty, due to the moving parts and the components which make up a compressed gas system.
Support – Support is often something that can be attributed to the “gut feeling” factor. Some manufacturers treat their customers fairly and openly while others can be difficult to deal with and offer very little support after the sale. More importantly than the manufacturer, is the representative who will be personally looking after you. Usually you can tell by the general character and knowledge of the sales person and their support team while you are evaluating cameras, the type of support you will receive after the sale. This is not something that a dollar value can be specifically placed on, but in some cases, can make or break the success of your infrared project.
Summary
To choose the best infrared camera for your application, you must have an intimate knowledge of the thermal requirements of your specific situation. The camera specifications must match the application requirements. If they do not meet these needs, despite an attractive price or incredible warranties, the camera should not be considered. Do not be lured by promises of future upgrades or features that are not available today, unless a money-back, time-dependent, written guarantee is provided. The second variable that should be considered is the practicality of a specific camera due to its design and functionality. A camera that is hard to use, and difficult to attain results from, will often spell disaster for your application. Although important, price is the last consideration in purchasing an infrared camera. If all other factors are even, then price may be the determining factor, but it should not be the driving force behind your choice.
Wayne Ruddock has been involved in Infrared Thermography and Infrared Thermographic Training since 1979. He is a seasoned veteran of hands-on infrared inspections, giving him the ability to teach real-life thermography. He has been conducting Level 1 training courses throughout the world since 1980. Wayne was the North American Director of training for an established infrared company from 1990–1999, at which time he became the owner/director of Advanced Infrared Resources (www.infraredthermography.com) Wayne has written training curriculums for various infrared equipment manufacturers and is currently the chairman of the Mexican Institute of Infrared Thermography. He now presents unbiased, manufacturer independent Level 1 and Level 2 training courses throughout North America, Australia, New Zealand and Mexico, as well as specifically tailored in-house training programs throughout the world. The material in these courses adhere to the guidelines set out in ASNT-TC-1A. These courses are also recognized by AINDT in Australia and New Zealand. He makes learning easy for individuals from all backgrounds and with all educational levels. You can reach Wayne at 250.682.0515 or wayne@infraredthermography.com.