Cintas Discovers Keys to Organizational Change Through CMMS Rollout
These keys, says James Wagoner, Regional Field Engineer, can be summed up as:
- Tap the field for ideas.
- Encourage 'positive discontent.'
- Tackle the elephant one part at a time.
- Pick your battles.
First, some background. Cintas is a publicly-held company that designs and implements corporate identity programs and other services for approximately 900,000 businesses. It operates out of 430 facilities and employs 30,000 people, with one of the largest contingents focused on uniform manufacturing, rental and cleaning.
The challenge that needed to be addressed back in the fall of 2006 was the lack of a corporate-wide, computerized maintenance management system (CMMS). The chief engineers at each of the 150 production facilities had, over time, developed their own method of tracking which equipment needed preventive maintenance, what parts needed to be ordered when, how much time was lost due to malfunctions, etc. But too often, they relied on paper and pen, and any lessons learned were lost with employee turnover and retirement. Likewise, it was difficult -- if not impossible -- for managers like Wagoner at the regional and national level to be able to accurately assess and compare plants' performance.
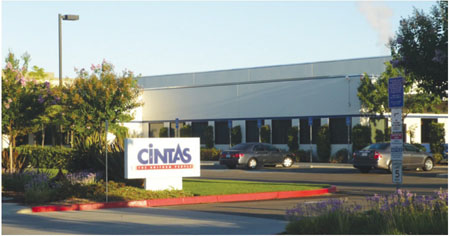
"There was a time when all we did was build new facilities and scramble to expand capacity," recalls Wagoner. "But now, with today's tight economy, it is imperative to preserve and optimize what we have. We need standardized operating procedures based on what we know works most efficiently. And that's not possible if everyone is doing their own thing."
It was clear that Cintas needed a corporate-wide CMMS solution. What happened next, however, is a common pitfall into which many companies stumble, no matter what the task, and that is the tendency to jump too quickly to whatever is familiar. Cintas chose a system made by one of the largest developers in the CMMS space -- the same system used in a previous position by Cintas' Vice President of Engineering.
There was just one problem: It wasn't right for Cintas. It became clear before very long that it would require too much time and money to customize and introduce it to Cintas' 150-plus uniform-laundering facilities. And that flew in the face of one of Cintas' secrets to success: a "spartan (cost-effective) approach." That's when lesson No. 1 saved the day.
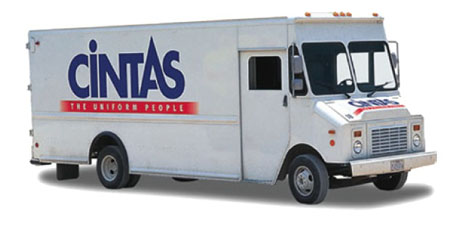
Tap the field for ideas
With the scrapping of the large ERP-type system before it ever got started, the corporate committee charged with selecting a solution did what Wagoner now agrees it should have done to begin with: survey the hundreds of plants to find out what was and was not working "in the trenches." That's when one clear finding trickled up: Although there were a variety of approaches, only one system -- used at a few plants in Alabama -- consistently received rave reviews. The surprise "winner" was X3, a CMMS system developed by eMaint Enterprises, a New Jersey-based player in the marketplace that Cintas' upper management hadn't even heard of.
Among the strengths of the system identified in the survey is its ability to:
- Create a centralized database, facilitating faster implementation of company-wide standardization and providing a broad range of data on the equipment in each and every individual plant.
- Track completion of and compliance with PM requirements at the national, regional and local levels.
- Ensure continuity and unhindered productivity during staff turnover.
- Provide on-demand employee training through "eMaint University."
"My perspective was that if there is one thing I could do right now that would have the most positive impact on my ability to do my job well, it was getting a CMMS system implemented across all of our plants," explains Wagoner.
But most important to customers like Cintas is its high degree of flexibility and functionality at a low cost. "The system is engineered to be fully adaptable. Everything from fields and forms, reports and workflows can be modified to better align to the specific business requirements of customers such as Cintas," says Brian Samelson, eMaint CEO.
Wagoner agrees. "The most attractive thing to us, in addition to the good performance results we heard from Alabama, was its low cost and rapid ramp-up time. All we had to do to begin implementing the system is pay $40 a month per user. That meant there wasn't a massive approval process required on our end."
Not long after the survey's findings were reported, Cintas' Vice President of Engineering attended one of the company's "reliability conferences" in the southeastern region, where I was among the featured speakers. The rest, as they say, is history.
A successful rollout, however, required the practice of a few more "lessons learned."
Encourage positive discontent
After the reliability conference, I was invited to Cintas' Cincinnati, Ohio, headquarters to further demonstrate and discuss the system. The first, immediate decision was to put the word out to all 150 production facilities in the field that X3 was a good option to consider. After more than 20 plants followed through on the recommendation and brought the system on board, Cintas' management decided that if it wanted to standardize implementation, it had better step in sooner rather than later. In 2010, a halt was placed on all new system purchases and the company's CMMS committee was charged with introducing the system across the enterprise.
There was just one problem. Joel Bell, Senior Director for Quality & Engineering at Cintas, who was charged with this responsibility had many more urgent priorities competing for his time. What was initially a one-month window for planning the rollout began to stretch into months beyond that. Fortunately for Cintas, a core operating principle is "positive discontent." In other words, explains Wagoner, "be unhappy with the status quo."
"Every employee at Cintas receives on Day 1 a booklet called 'The Spirit is the Difference,'" he says. "Employees are treated as partners and you learn that if you see something that needs to be fixed, you can't just moan and groan. You must seek a solution."
And that's what Wagoner did. Seeing the committee fall behind on its goal, he first talked to his own direct manager to get his blessing, then stepped up to the plate and made an offer Bell couldn't refuse: He would take on the responsibility of launching a pilot designed to build buy-in, identifying best practices and working out any problems prior to a national introduction of a CMMS.
"My perspective was that if there is one thing I could do right now that would have the most positive impact on my ability to do my job well, it was getting a CMMS system implemented across all of our plants," explains Wagoner. "The system was head and shoulders above any other solution we had looked at. I was given a lot of autonomy to define success within the CMMS implementation committee and to decide when and how to move forward with both the pilot and the full rollout."
Tackle the elephant one part at a time
Of course, Wagoner had a lot on his plate as well; in these economic times, many employees are faced with an ever-increasing workload.
Part of the solution is management prioritization and support. Wagoner and his immediate manager had the necessary conversation and implementing a CMMS became his No. 1 priority; other, non-emergency tasks were handed off to others or delayed.
The other part is how you approach and organize the project.
Figure 1: One of 150 Cintas Wash Alleys located throughout the U.S. and Canada. Tiltable Washers (left), Dryers (right), Movable Shuttle Conveyor (background) and Chute (overhead).
"The job in front of me did seem a little intimidating at first," admitted Wagoner. "There are just so many phases to implementing any major change across such a large number of locations. The key for me was to remember that a journey of 1,000 miles starts with a single step. Don't worry about everything all at once; worry about what is right in front of you -- the first step."
The initial task of the implementation team Wagoner now led was to determine just what information and functions Cintas needed the CMMS software to collect and perform. Although a core strength of the system is that it can be used quickly "out of the box," Cintas also needed some customization to fit the system to its unique needs. For example, Wagoner and his team wanted a checklist of lock-out/tag-out tasks to print out at the same time as a work order, thus ensuring that when engineers repaired a piece of equipment, they also took all necessary steps to protect their own and others' safety.
"The system is already easily customized by adding or deleting fields, creating drop-down menus, etc. But when we needed some adaptations beyond that, the eMaint team was very responsive," says Wagoner. "Every time we've said, 'We want this,' they responded by saying, 'Let's figure out a way to do that.' And they have."
Wagoner and his committee chose a diverse group of 11 production facilities to participate in the pilot, representing veteran CMMS users as well as "newbies." The decision also was made to limit the scope of the rollout initially to work orders and PM tasks, with the possibility of expansion later. After about four months, the pilot was declared complete on March 2, 2012. Now, Wagoner and his team are in the midst of the next challenge -- full rollout to all 150 facilities across the country. And that process is teaching Wagoner a final lesson.
Pick your battles
"I attended a maintenance summit in Texas and I realized that although some chief facility engineers were as excited as I am about the new CMMS process, others are not. They say it won't work at their facility, that they don't have time to hassle with a change, etc.," observes Wagoner. "I know this is bigger than any one individual and, ultimately, it will be coming to every location at some point. As we show success at more and more locations, that will create its own pressure. But we can't mandate it; the system is only as good as the information that goes in. So, I focus my time on facilities that are ready and that want it."
Figure 2: Autosort Garment Sortation Machine. Barcode labels allow garments to be automatically sorted by Cintas Route Truck, Delivery Date, Customer and Employee
As of September 2012, Wagoner and his committee, with the help of Pargas and the larger team, have brought eMaint's CMMS to more than 100 facilities. And Wagoner is already seeing the results he wanted so much when he raised his hand and said, "I'll do it!"
Users at each location have access to online training tools and are certified to ensure they have the knowledge necessary to utilize the system properly. Plant managers now have visibility to the work performed by each member of their staff. Changes to standard procedures are rolled out across all locations with ease, ensuring consistency. With the initial phase of implementation well underway, the committee is turning its attention to what's next, including incorporating mobile and bar coding technology.
Today, management knows the condition of the equipment at each of those facilities, at any moment in time. And with the razor-edge margins of the competitive uniform business, that means a healthier bottom line for Cintas.