Combining Route-Based Condition Monitoring and IIoT to Reinforce Asset Condition Management
Introduction
In modern engineering asset management, the minimization of maintenance expenses, maximization of equipment availability and reliability, and reduction of human and environmental hazards are crucial objectives. To achieve these aims, the selection of an appropriate maintenance strategy is necessary, such as corrective or preventive maintenance. In the case of the latter, maintenance tasks are either scheduled in advance, as in the case of systematic preventive maintenance, or performed based on the current condition of the system, as with condition-based maintenance.
The International Organization for Standardization (ISO) has developed a generic standard procedure to be used when implementing a condition monitoring program [1], which encompasses various steps, such as cost benefit analysis, asset auditing, reliability analysis, monitoring method selection, data collection, diagnosis & prognosis, and maintenance decision-making (Figure 1). Adopting a standardized procedure for developing CBM strategy such as the one established by ISO can provide organizations with several benefits [2], adherence to industry best practices in the development of CBM strategies can ensure the flawless implementation of the maintenance program, thus enhancing asset performance and reducing maintenance costs.
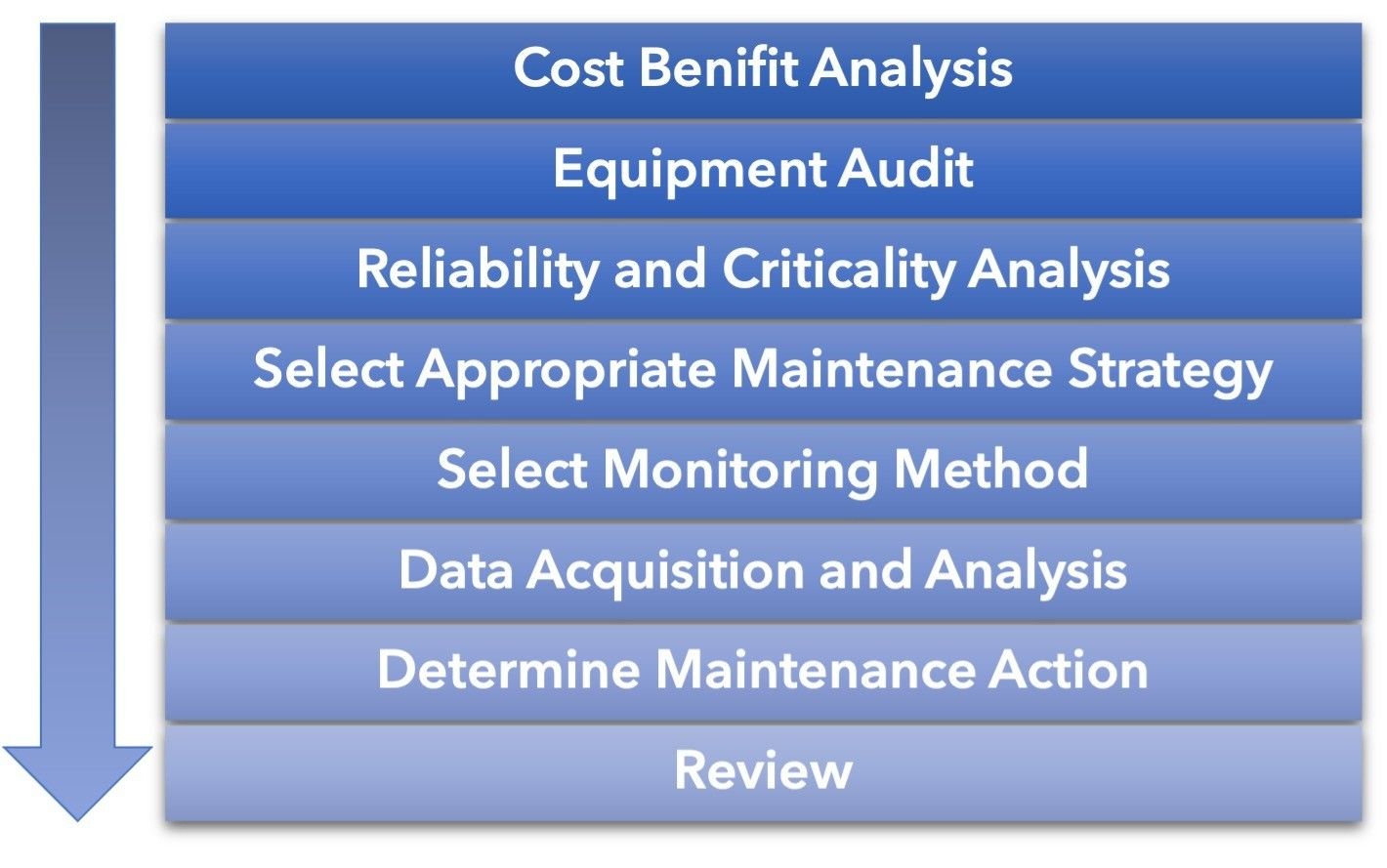
Address The Key Criteria
The ISO procedure relies heavily on the reliability-centered maintenance approach to shepherd condition monitoring activities towards identifying and detecting symptoms of root cause failure modes. RCM introduces criticality analysis, failure modes, and effects analysis (FMEA or FMECA) as core components. The latter is an essential methodology to identify expected faults, symptoms and produce information on the range of potential parameters to be measured as an indication of fault condition, by either an increase or a decrease in the particular or characteristic measured value, a detailed case study developed by Tobon-Mejia eta al [3], where FMEA analysis was conducted to set the right parameters and diagnosis & prognosis model for an electromechanical system.
Reliability and criticality analysis cover one of the primary criteria of CBM [4]. It should be beneficial. The second primary criteria is that it should be feasible. The feasibility of CBM should be clearly defined to find out if it is possible solution. The third criteria is that a CBM solution should be cost-effective, as the solution should be economically justifiable, so that the benefits of CBM outweigh the cost.
Select the Right Monitoring Technique
CBM is considered suitable when all the three criteria mentioned above are fulfilled. Choosing route-based CM or IIoT sensors, the bottom line is the condition monitoring technique must be technically feasible and economically justifiable, busse et al [5] present an approach to analyze the cost-benefit of CBM/PdM, the approach's main goal is to give an indication of the possible cost-savings of CBM/PdM compared to traditional maintenance in order for maintenance managers to decide if condition monitoring should be implemented.
Technical feasibility is a criterion that be fulfilled the condition monitoring to be possible. The technical feasibility of the condition monitoring is dependent on the failure mode characteristics, condition data requirements, as well as the lead time to failure (LTTF or P-F interval).
To ensure the technical feasibility of the condition monitoring technique chosen, a survey shall be conducted to justify the proposed technique:
- Are the failure modes known and are the failure modes detectable? Failure modes and their characteristics must be known to determine if the failure can be detected through condition monitoring. Not all abnormal conditions can be detected using condition monitoring and some failures occur without measurable degradation.
- What difficulties can impact monitoring accuracy? There are several factors must be taken into consideration:
- The condition monitoring should be correlated with the actual operating conditions. If possible, monitoring should be carried out when the machine has reached a predetermined set of operating conditions (e.g., load and speed when measuring vibration in crane hoist gearbox).
- Consideration should be given to the ease of access, complexity, safety requirements when acquiring condition monitoring data, (e.g., sensors can be installed for difficult access and risky monitoring locations).
- Measurement locations should be chosen to give the best possibility of fault detection, and they should be identified uniquely. If there is any risk of inconsistent spot locations, a sensor can be permanently installed in the right monitoring location.
- Consideration should be given to the data type required for diagnosis & prognosis purposes: measured parameters can be simple measurements of overall values or values averaged over time (e.g., RMS), or more complex techniques such as FFT, spectral analysis can be required to reveal changes caused by faults. A combination of both online sensors, to deliver the simple data type, and route-based monitoring for complex data can be adopted as an optimal and cost-effective condition monitoring solution.
- Net P-F interval that is long enough to take appropriate corrective action? For CBM to be technically feasible the P-F interval (Figure 2) has to be reasonably consistent, and it should be long enough to take proactive actions. It is recommended that route-based condition monitoring tasks should be performed at intervals no longer than half the expected P-F interval (LTTF/2). For failure that could impact a crucial system function and has a smaller P-F interval, an IIoT condition monitoring could be adopted to increase the Net P-F interval and leave enough time to plan a corrective action.
- Is the condition monitoring technique proven technology? Choosing handheld condition monitoring or IIoT sensor, the technology should be proven. It is difficult to decide how much experience is enough to call the technology proven. But some experience with the technology is required to assure of quality of CBM.
Combining Route-Based Monitoring and Online Monitoring (IIoT)
The optimal approach for asset condition monitoring is to fulfill the primary criteria of CBM by combining the manual, handheld instrument routines with the digital, condition-monitoring toolbox—such as IIoT, edge computing, and cloud services.
Handheld devices are progressively gaining internet connectivity, enabling technicians to transmit measurements to the same database employed with online condition monitoring sensors (Figure 3), while working in the field.
Exclusively by integrating IIoT sensors and handheld devices, asset condition data combined with other data (Figure3) can be automatically analyzed using edge or cloud computing and deploying machine learning models to identify patterns or forecast asset health [6]. These two methodologies supplement each other, instead of substituting one another. Their integration represents the optimal approach for decreasing CBM program costs and prolonging the life of assets.
References
[1] ISO 17359 :2018, Condition monitoring and diagnostics of machines — General guidelines.
[2] Liu, H., Zhang, Y., Zeng, S., & Wang, W. (2020). A condition-based maintenance approach for industrial equipment: A case study. Journal of Manufacturing Systems, 56, 217-224.
[3] Tobon-Mejia, D. A., Medjaher, K., & Zerhouni, N. (2010). The ISO 13381-1 standard’s failure prognostics process through an example. 2010 Prognostics and System Health Management Conference.
[4] Aker Solutions. (2010). BD01-AK-O-05010: INTEGRATED OPERATIONS STUDY – ELDFISK FEL2, FEL3
[5] Busse, A., Metternich, J., Abele, E. (2019). Evaluating the Benefits of Predictive Maintenance in Production: A Holistic Approach for Cost-Benefit-Analysis. In: Schmitt, R., Schuh, G. (eds) Advances in Production Research. WGP 2018. Springer, Cham.
[6] Ma, Lin (2007) Condition Monitoring in Engineering Asset Management. In Kaneko, S (Ed.) Proceedings of APVC2007 12th Asia Pacific Vibration Conference. JSME, CD Rom, pp. 1-16.