Conducting Asset Criticality Assessment for Better Maintenance Strategy and Techniques
Conducting an asset criticality assessment (ACA) is the first step in maintaining the assets properly. This article addresses the best maintenance strategy for assets by using ACA techniques. It also focuses on ACA implementation and methodology, and suggests a multi-disciplinary team to set the objective and boundary for each asset and system. Conducting ACA can be very beneficial if done right by following the recommended methodology to accelerate the assessment and maximize the quality of selecting the proper maintenance strategies for each asset.

Introduction
ACA is an initial step for the reliability centered maintenance (RCM) approach, which mainly focuses on enhancing maintenance strategies rather than a single asset. In other words, it is a process of decision-making to reach the optimum maintenance strategies for assets in any industry’s process. Thus, defining asset criticality is a preliminary step that plays a major role in applying the most effective maintenance plan and controlling where and how maintenance efforts are spent.

Purpose and Objectives
ACA results provide a clear judgment of a plant’s priorities, helping to achieve operations’ business goals. It is also designed to ensure that the most critical assets are operating in best-in-class (BIC) condition for a specific period of time. The aim is to extend the lifetime of an asset by applying the most suitable maintenance strategy based on the asset’s condition (Figure 1), whether a predictive maintenance (PdM), preventive maintenance (PM), or run to failure strategy. In general, ACA is a prioritization methodology intended to establish the most effective maintenance strategies for assets considering their importance and contribution to the plant’s business goals.

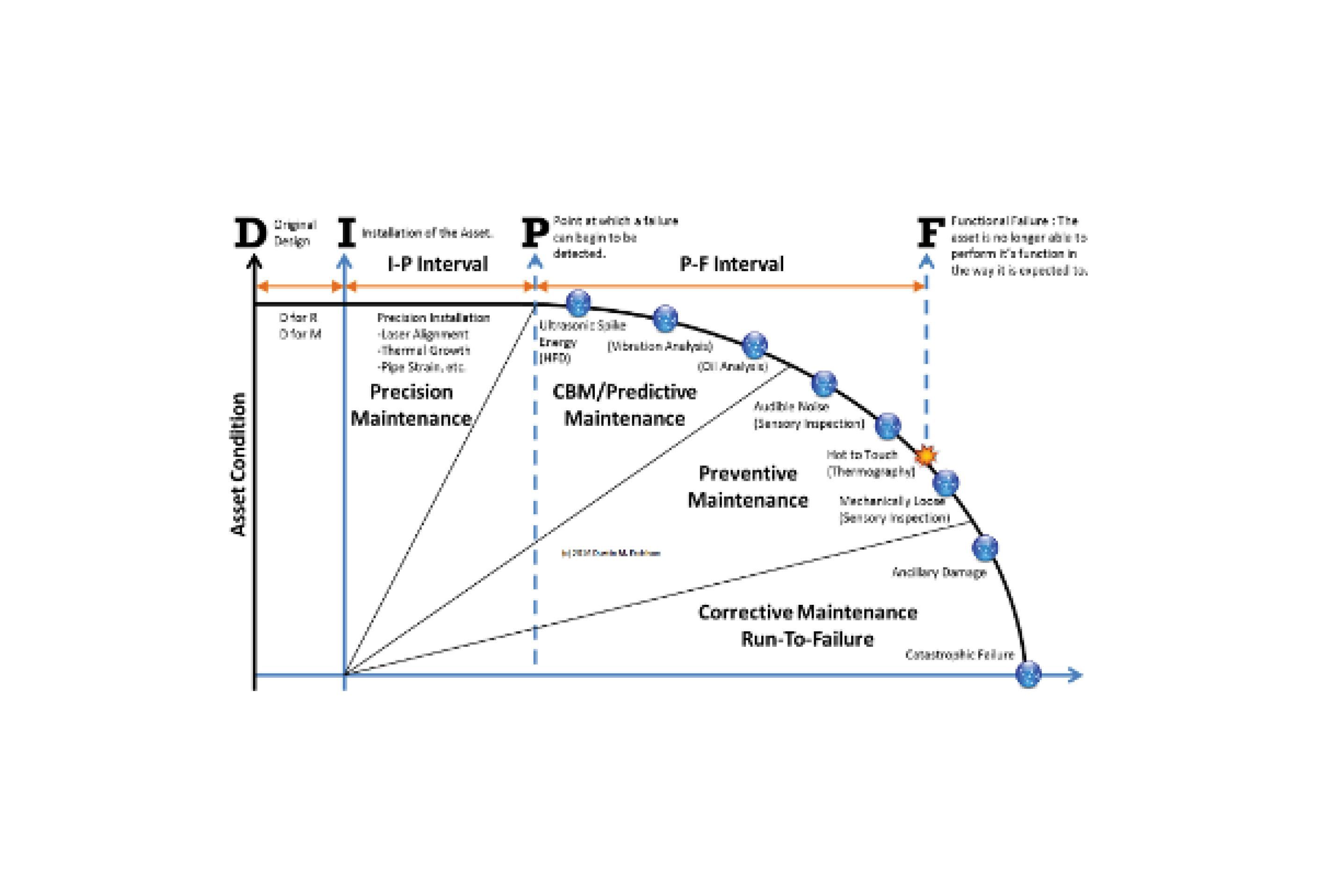
Figure 1: Maintenance strategies that can be applied based on criticality (Source: The Impact of Equipment Reliability on Human Safety, Production Technologies)
ACA is applicable for all industry assets (e.g., static, rotating, electrical and instrument) in order to optimize maintenance programs for plant assets to:
- Reduce Maintenance Costs: ACA can reduce maintenance costs by shifting maintenance activities to the right asset rather than spending money for all assets regardless of their contributions to the business goals.
- Enhance Reliability, Availability and Maintainability: ACA defines critical assets to identify ordinary and noncritical assets and properly apply a suitable maintenance strategy according to their criticality, mostly only PdM, PM, or run to failure strategies.
- Control Manpower Effort: ACA focuses on the critical assets that would minimize labor efforts and lead to more important work.
- Optimize Spare Parts Management: ACA can widely help optimize spare parts purchase orders and control quantity of spare parts.
Forming an Asset Criticality Assessment Team
For conducting any ACA, a team should be formed consisting of members from operations, maintenance, engineering and others based on the type of assets. For instance, the following proposed team is an example for the oil and gas industry, which covers most of the assets:
- Reliability Engineer (Facilitator: Provides support and coaching for ACA);
- Maintenance Engineers, Inspector, Maintenance Planner and Senior Technicians (Member: Provides maintenance knowledge data);
- Process Engineers and Senior Operator (Member: Provides health, safety and environment (HSE), process and operations knowledge and data);
- Technical Support Engineers and Subject Matter Experts (SMEs) as required (Member: Provides knowledge and data specific to the asset).
Process Methodology
According to the Uptime® Elements, the main criteria to govern the criticality assessment, which focuses on failure consequences, are safety and environment, production losses, system asset configuration, reliability, utilization, and maintenance costs.
The following steps are summarized at a high level to assist in understanding the ACA methodology:
- Identify the selected asset or system as defined by process flow diagrams (PFDs);
- Identify the plant’s business objectives (to achieve the business’s operating plan);
- Classify the different levels of critical boundaries/limitations for each criteria (e.g., failure consequences on safety and environment, production losses, system asset configuration, reliability, utilization and maintenance costs);
- Calculate the asset criticality index, a scoring system used to specify the grade of asset criticality based on criteria, as described in Equation 1:
Criticality Index = Criteria #1 × Criteria #2 ×…Criteria #X
Equation 1
- Classify the asset into different levels based on its calculated index (based on the outcome of the scoring process, categorize asset criticality into three categories, with A indicating asset essential to operation, B as asset critical to operation and C as asset nonessential to operation).
Each industry can assign the limitation for this index. Table 1 is an example that can be used as a guideline.
Table 1: Criticality Index
Results
The previously proposed oil and gas industry team applied the ACA methodology to optimize asset criticality based on the suggested criteria. Based on the outcomes from this exercise, the team was able to justify moving 10 percent of assets from asset class A (essential to operation) to a lower criticality with a cost avoidance around 15 percent. High quality data and qualified team members will help the plant’s workers identify the proper maintenance strategy, optimize maintenance costs and align the future budget.
References
Gulati, Ramesh and Mears, Christopher. Maintenance and Reliability Best Practices, 2nd Edition. Fort Myers: Reliabilityweb.com, 2012.
Erickson, E. “Equipment Reliability.” Solutions. Atlanta: SMRP, 2017.
Gulati, Ramesh. Uptime® Elements Dictionary for Reliability Leaders & Asset Managers. Fort Myers: Reliabilityweb.com, 2013.
Srivastava, Sushil Kumar. Maintenance Engineering Principles, Practices & Management. New Delhi: S. Chand Publishing, December 1, 2010.
Al-Jabr, Khalid A.; Ahmed, Qadeer; and Al-Anazi, Dahham. “Why Data Is the Foundation for Reliability.” Reliable Plant. Tulsa: Noria Corporation, 2017. https://www.reliableplant.com/Read/31717/data-foundation-reliability
Calixto, Eduardo. Gas and Oil Reliability Engineering, Modeling and Analysis, First Edition. Oxford: Gulf Professional Publishing, October 10, 2012.