Critical Factors to Achieve World-Class Manufacturing Reliability
The benefits of maintaining a facility with world-class reliability are enormous and should not be underestimated. Major advantages associated with excellent reliability are higher utilization of the asset, lower maintenance costs, fewer overall people required to run the facility, better safety performance and better energy efficiency.
What World-Class Means
Many perceive world-class reliability performance as a panacea, as plant operations always seem to be in flux with other priorities getting in the way or integrated asset upgrade plans suffer significant delays at manufacturing facilities.
Becoming top quartile, U.S. best, or world-class is not just about a robust capital investment program. It requires a relentless commitment to maintenance and asset care excellence. First and foremost, a fully engaged plant requires matrix participation from engineering, design, operations, maintenance and the reliability leadership team. This allows for complete utilization of the asset by maintaining close to maximum capacity. It also keeps maintenance costs consistent, sustainable and, generally, better than the average.

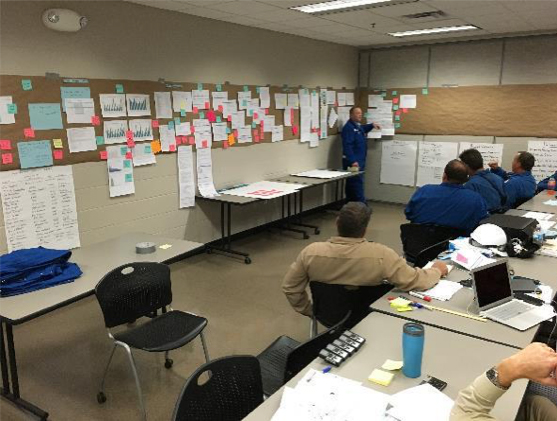
Figure 1: Problem-solving meeting with a reliability action team using a visual tracking board
Critical Factors
Maintenance organizations in world-class facilities are always focused on preventive and predictive activities instead of high priority break-in type work.
Maintenance organizations within reliable facilities are very good at planning and scheduling activities because they are not continually fighting equipment failures. Programs around precision maintenance and equipment specific care plans tend to have excellent results. A crucial and direct side effect of world-class reliability is a consistent safety track record. Additionally, when a facility is reliable, it requires much less energy to operate because it is always in a stable state, avoiding continuous shutdowns and rate cut situations that impact the uninterrupted functioning of the asset.
A number of requirements must be met before a facility can become world-class.
The four critical ones are:
1. A results-driven, high-energy and consistent management team
Employees need results-driven, consistent leadership to make lasting operational changes. When the management team is changing frequently, it is a sign that the facility is not a candidate for exceptional reliability. A facility needs a management team that is high-energy, focused and, most of all, visible to the workforce – these are by far the most effective. The management team should be committed to daily performance discussions with frontline teams. The more visual the communication, the better. For example, the leader standard work routine, which uses a visual board to formalize weekly maintenance walks, has proved successful in creating discussions about better pump care and overall root cause analysis.
2. A reliability culture in place from the top of the organization to the bottom
A reliability culture starts with facilitating the right forums. These forums discuss key topics, such as reliability imperatives, training and engaging in daily problem-solving. Each member of the reliability leadership team has to take an active role in following this script, spreading the reliability message and clearly assigning the reliability-centric roles, responsibilities and expectations. Until this reliability culture is in place, not even the most advanced and expensive reliability tools will be helpful. A reliability culture is where reliability is everyone’s responsibility and all decisions are made with reliability as a key consideration. For example, consider how a true safety culture works within a manufacturing facility. Safety becomes everyone’s responsibility, where all decisions involve a safety review. From the top of the organization to the bottom, everyone is focused on safety. The same holds true with reliability. Everyone in the organization must become personally responsible for reliability and all decisions should include a reliability review. Reliability culture is the most elusive, yet most important pillar for achieving world-class reliability. This pillar is why most manufacturing facilities fall short.
3. A playbook for reliability and maintenance programs
Only after a strong management team and a reliability culture are in place can established and efficient reliability and maintenance programs be put into place. A playbook to deploy the reliability program is a must. This playbook is not a thick book full of step-by-step procedures, but rather an easy to follow, visual manual that allows every member of the reliability team to understand both the short- and long-term plays. This helps drive preventive maintenance, predictive maintenance, root cause failure analysis and key performance indicators, tracks action items and provides leadership for continuous improvement.
Figure 2: Daily maintenance department accountability meeting using visual metrics board
4. Utilization of digitization and Internet of Things (IoT) tools
Top quartile teams are starting to integrate digitization and IoT tools, such as sensors, radio-frequency identification (RFID), enhanced reality, geolocation and operator mobility tools, to improve reliability programs. While many organizations are in the initial piloting phase, several large operators have started company-wide programs to utilize digitization tools that go from equipment monitoring to proximity analysis for scheduling efficiency. For example, by using enhanced reality with mobility platforms, technicians and maintenance crews are able to execute more accurate and comprehensive repairs and overhauls of pumps, turbines and valves as part of their daily reliability routines.
For a reliability program to advance into a next generation phase, realistically, one must have all these components in place. Never underestimate the importance of having good tools and systems to manage and drive better performance. More importantly, never underestimate the need to have a reliability culture in place to make sure the tools are used to their highest potential.