Design Phase Spare Parts Optimization: How to Reduce Spare Parts Inventory Costs
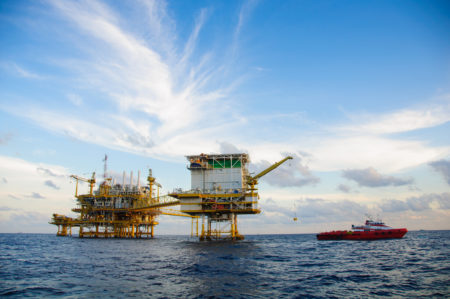
Ideally, inventory requirements need to be defined during project detailed design phase so they can be ordered and stocked prior to project start-up. For this, two items must be developed: a listing of parts for each equipment in the project and the number of each unique part that should be kept in stock for this equipment.
Typically, vendors make recommendations for spare parts needed for their equipment, however, their recommendations do not consider risk (i.e. probability and consequence of failure) for the operating equipment. Instead, the recommendations only consider the need to repair the failed equipment. Thus, if the vendor recommendations for spare parts are accepted without being reviewed, the result will be excessive stock (i.e. too much cost). If too few parts are stocked, repair times for equipment will increase, potentially resulting in production losses, which usually far exceed the cost of the corrective work order—including labor and materials.