One way of determining the quantity of grease comes from the bearing suppliers. Knowing the bearing number or dimensions generalizations can be made and a rough quantity of grease can be determined. The formula is as follows: Re-lubrication Amount of Grease (g) = 0.005 * Bearing Outside Diameter (mm) * Total Bearing Width (mm). If the speed and load are known for the bearing; only then can a frequency be determined, otherwise it is trial-and-error. Unfortunately an error in lubrication means a machine is down.
The next few paragraphs will discuss a couple grease lubrication devices and then the benefits of using them in combination.
Sonic and ultrasonic lubrication devices have been quite popular at a number of plants that I have had the opportunity to work for. Generally this device is used by the Plant Lubrication Technicians on their grease routes to allow them to determine when the bearing has enough grease and avoid over-greasing potentially destroying bearings. Sonic lubrication devices have a transducer mounted on the end of the grease gun and passes a signal to an electronic processor that filters out some sounds and amplify others. Ultrasonic units pass the signal through an electronic processor which converts the ultrasonic vibrations to an audible sound range. Both types have had great success in condition based lubrication and with experience the user can determine what greasing frequency works best with a particular bearing.

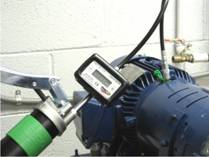
Grease gun meters are fairly common and useful units. The equipment OEMs generally recommend specific amounts of grease in grams or ounces; in other to dispense the recommended amounts, nothing is better than a metering device. The problem with using a meter alone is that there is no feed back on if the quantity is too little or too great.
When using a sonic/ultrasonic lubrication device and a grease meter on a grease gun, you gain a tool more powerful than any of the components on their own. Your grease gun will now ‘tell' you when the bearing has enough lubricant and the amount. After completing the grease routes a few times and recording the amounts of grease used, you will be able to determine the optimal frequency and quantity. If you listen to what your machines tell you, your equipment will dictate the interval and amount themselves.

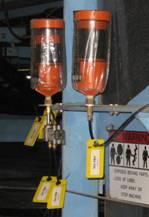
Another advantage with this system comes across when using autolubers in your equipment greasing strategy. Both electrochemical and microprocessor controlled autolubers have different ways they control the flow of grease; however, they are both based on a volume over a period of time. Once the optimal frequency and quantity has been determined through sonic/ultrasonic metering all that is required is a quick calculation and you can find the best dispensing rate for the autoluber. Below is an example:
Ultrasonic metering determines 4g/month of grease is optimal
4g/week= 17g/month
Streamliner M Dispenser: 125cc pouch= 113g of grease
Settings: 113g per ½, 1, 2, 4, 6 & 12 months
A setting of 113g per 6 months would give us 19g of grease each month
As with any maintenance program, a greasing program has to be monitored and updated regularly. Conditions in which machines operate change and with these changes, so do the lubrication requirements. Feed back from bearing and ambient temperature readings and vibration readings are valuable since they can tell you how well your lubrication program is working. Feed back from Production and Operations can also provide insight as to if any process changes have occurred which can lead to a lubrication revaluation.
Written by: Kristopher Sonne, Senior Field Service Technician
Article provided by Tricocorp