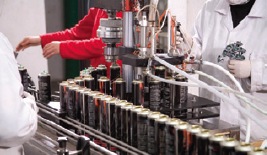
At the same time, there is also a widening knowledge gap. Many of those in the electric industry power quality groups, who have until now been responsible for understanding the sources of problems and providing solutions, have either retired or been reassigned to other tasks. Thus, there is an increased need for plant electricians, electrical contractors, facility managers and others who may not have an electrical engineering background to prevent and/or solve PQ-related problems.
Solutions for doing so abound, but first it is perhaps instructive to see how some of these power quality issues manifest themselves in the real world. To that end, the following mini case studies illustrate how power quality issues can impact plant operations, and how everyday solutions can be applied to fix them.
Over-current Trip Shuts Down Manufacturing Process
Located in an industrial park, a medium-sized manufacturing facility experienced the sudden shutdown of several adjustable speed drives (ASDs), an unanticipated event that wreaked havoc on key process equipment. At approximately 6:00 each morning, the utility-owned power factor capacitor kicked on to compensate for the inductive loads prevalent in many of the park's manufacturing facilities. The ASDs were conditioned to anticipate this scheduled power quality event and typically rode through the problem. So when one of the ASDs closed down and interrupted the continuous-stream manufacturing process, the facility manager needed to instantly find out why, correct the problem and prevent it from happening again.
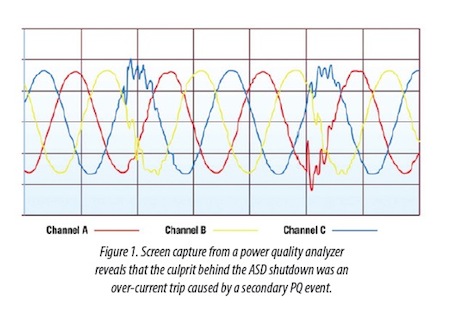
As Figure 1 shows, a second, unanticipated capacitor-switching event occurred shortly after the first. This event was categorized by the facility's permanently installed power quality monitoring instrumentation which enabled the facility manager to pinpoint the exact source of the problem. Further analysis revealed that the ASD shutdown was the result of an over-current trip that was quickly remedied, thus preventing several hours of downtime, calculated at approximately $10,000 per hour.
Harmonics Generated by the Utility Transformer
Despite their differences, continuous or batch-process industries all share at least two characteristics in common: (1) continuous operations by definition represent substantial start-up costs and time and (2) they can be interrupted or disrupted by seemingly minor fluctuations in power quality. Any disruptions to the product stream mean lost productivity, lost product, scrapped material and a substantial financial drain.
As one well-known manufacturer of sausage, salami, bologna and other meat products demonstrated, power quality problems are not always created inside the facility itself. In this particular plant, most of the process load consisted of HVAC and refrigeration for approximately 6000 sq. ft. of cold room storage. Additional loads included grinders, slicers, presses and other machinery. The facility was powered by a 120/240V service fed through a utility-owned 500 kVA high-leg delta transformer that was also shared by another factory.
Plagued by frequent interruptions when the main 1200 amp circuit breaker tripped, sometimes several times a day, previous measurements had not shown the cause of the events. The highest current measurement was only 760 amps, which was below the threshold that would cause the breaker to trip. From the power quality recordings, the following was noted:
• At times the peak current exceeded the breaker's 1200 amp rating without causing it to trip. An interruption that was tied to such a peak current was detected only once during the measurement period. Further investigation from the captured waveforms revealed that the voltages were distorted during such times, which resulted in the nuisance tripping of the other breakers and caused the capacitor banks to fry.
• A long-term measurement conducted with a power quality analyzer showed that the capacity of the breaker could be reached when a combination of tasks occurred at the same time.
• Since most of the load at this site is linear, no harmonics were generated from within the facility. When the investigation turned to looking outside the factory, the cause of the distortion was traced to a faulty power transformer.
The problem was solved after the utility replaced the transformer, which enabled the factory to increase its capacity and production.
Inrush-induced Sag Prevents Motor Start
An industrial customer operating a pair of 1250 hp motors on a 4kV circuit was stymied when the motors refused to start. To determine the problem, a power monitor was installed at the motor input. The power monitoring instrument quickly identified the motor itself as the source of the problem. In fact, the motor start caused a deep sag to occur, which impacted the motor control circuitry and prevented the motor from starting. In effect, the motor was "shooting itself in the foot," creating a cycle of non-performance.
The customer was presented with several mitigation options, including adding more capacity to the circuit, installing a constant voltage transformer, or installing an uninterruptible power system (UPS). The customer selected the UPS option, which was installed to protect the motor control circuitry during motor start-up and verified by the power quality analyzer (Figure 2).
Inrush currents like those associated with motor starts can cause interaction problems with other loads. When motors are started, they typically draw 6-10 times their full load, which often results in voltage sags that can dim the lights, cause contactors to drop out, disrupt sensitive equipment and, as in this example, affect the successful start of a motor. Power quality monitors that can capture waveforms during long-duration start-ups are quite effective for characterizing and optimizing motor starts.
Conclusion
What is important to remember is that the characteristics of the power required by the load is compatible with that of the power being supplied, whether by the utility or some type of mitigation equipment. Everything must play together harmoniously or problems will surface. And when they do, chances are the call will come for you, the facility engineering professional, to ride in and save the day.
The good news is that there are many excellent solutions out there to help you do just that. Dranetz and others, for example, not only offer a breadth and depth of power quality monitoring and analysis solutions, but expert applications engineering assistance is only a phone call away, so that you will never feel like you're out on a limb, winging it alone.
About the Author
Ross Ignall is Director of Product Management at the Edison, NJ-based Dranetz, the leading provider of intelligent handheld and permanently installed monitoring solutions for electrical demand, energy and power quality analysis. He may be contacted at: (800) 372-6832 or rignall@dranetz.com.