Take a look at this picture. They look like identical machines on the truck don't they?
Well they are identical machines. They actually have consecutive serial numbers. They were installed at the same time, right next to each other, and perform the same duty (hot air supply to the dryer section of a web process).

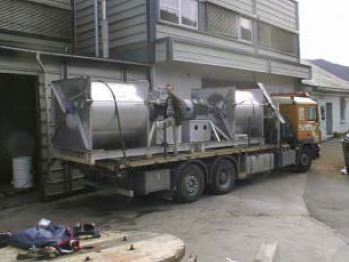
These fans heat up in operation, so calculations were made to determine the running position (since the fan housing and supports would grow as the units went on-line). What was found is that the two identical fans did not grow identically? There was almost a 20-mil difference in their on-line position. Why the drastic difference? The foundations were identical as were all the connections, ducting, etc. What this points to is the need to measure the actual position of machinery. Calculations of anticipated growth are a good starting point, but should not be the sole effort made.
This paper will cover some fundamentals of precision alignment, as well as the methodology for calculating thermal growth. Then discuss and demonstrate the importance of field measurements of actual on-line positions.
Some Basics
What is shaft alignment? Shaft alignment is the positioning of the rotational centers of 2 or more shafts such that they are co-linear when the machines are under normal operating conditions. Proper shaft alignment is not dictated by the TIR of the coupling hubs or the shafts, but rather by the proper centers of rotation of the shaft supporting members (the machine bearings).
Before discussing alignment tolerances, we should mention that there are actually two components of misalignment, Angular and Offset. Let's consider each of these separately.
Offset Misalignment, (sometimes referred to as Parallel Misalignment) is the distance between the shaft centers of rotation measured at the plane of power transmission from the driving unit to the driven unit. This is typically measured at the coupling center. The units for this measurement are Mils (where 1 Mil = 0.001").
Angular Misalignment, (sometimes referred to as "gap" or "face"), is actually the difference in the slope of one shaft, usually the moveable machine, as compared to slope of the shaft of the other machine, usually the stationary machine. The units for this measurement are comparable to the measurement of the slope of a roof, Rise/Run. In this case the rise is measured in Mils (1 Mil = 0.001"), and the run (distance along the shaft) is measured in inches, therefore the units for Angular Misalignment are Mils/1".

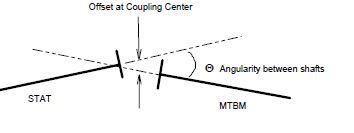
Figure 1
As stated above, there are two separate alignment conditions that require correction. There are also two planes of potential misalignment, the Horizontal Plane (the side to side) and the Vertical Plane (the up and down). Each alignment plane has offset and angular components, so there are actually 4 alignment parameters to be measured and corrected. They are Horizontal Angularity (HA), Horizontal Offset (HO), Vertical Angularity (VA) and Vertical Offset (VO).
Shaft Alignment Tolerances
Historically, shaft alignment tolerances have been governed by the coupling manufacturers' design specifications. The original function of a flexible coupling was to accommodate for the small amounts of shaft misalignment remaining after the completion of a shaft alignment using a straight edge or feeler gauges. Some coupling manufacturers have designed their couplings to withstand the forces resulting from as much as 3 degrees of angular misalignment and 0.075" (75 mils) of offset misalignment, depending on the manufacturer and style of the coupling. Another common tolerance from coupling manufactures is the Gap tolerance. Typically this value is given as an
absolute value of Coupling Face TIR (example Face TIR not to exceed 0.005"). This number can be very deceiving depending on the swing diameter of the Face Dial Indicator or the diameter of the coupling being measured. In fairness, it should be noted that the tolerances offered by coupling manufacturers are to ensure the life of the coupling; with the expectation that the flexible element will fail rather than a critical machine component.
If this angular tolerance was applied to a 5" diameter coupling, the angular alignment result would be 1 Mil/1" of coupling diameter or 1 Mil of rise per 1 inch of distance axially along the shaft centerline. If the coupling was 10" in diameter the result of the alignment would be twice as precise (0.5 mils/1"). This would lead one to conclude that an angular alignment tolerance based on Mils/1" would be something that could be applied to all shafts regardless of the coupling diameter.
While it is probably true that the coupling will not fail when exposed to the large stresses as a result of this gross misalignment, the bearings and seals on the machines that are misaligned will most certainly fail under these conditions. Typically, machine bearings and seals have very small internal clearances and are the recipient of these harmonic forces, not unlike constant hammering.
Excessive shaft misalignment, say greater than 2 mils for a 3600 rpm machine, under normal operating conditions can generate large forces that are applied directly to the machine bearings and cause excessive fatigue and wear of the shaft seals. In extreme cases of shaft misalignment, the bending stresses applied to the shaft will cause the shaft to fracture and break. By far the most prevalent bearings used in machinery, ball & roller bearings, all have a calculated life expectancy. This is sometimes called the bearing's L-10 life; a measurement/rating of fatigue life for a specific bearing. Statistical analysis of bearing life relative to forces applied to the bearings have netted the following equation describing how a bearings life is affected by increased forces due to misalignment.
This formulation is credited to the work done by Lundberg and Palmgren in the 1940's and 1950's through empirical research for benchmarking probable fatigue life between bearing sizes and designs. For Ball Bearings:
L10= (C/P)3x 106;for Roller Bearings: L10= (C/P)10/3x 106
Where:
L10 represents the rating fatigue life with a reliability of 90%
C is the basic dynamic load rating - the load which will give a life of 1million revolutions - which can be found in bearing catalogues
P is the dynamic equivalent load applied to the bearing.
In summary, as the force applied to a given bearing increases, the life expectancy decreases by the cube of that change. For instance, if the amount of force as a result of misalignment increases by a factor of 3, the life expectancy of the machine's bearings decreases by a factor of 27.
Quite a bit of research in shaft alignment has been conducted over the last 20 years. The results have led to a much different method of evaluating the quality of a shaft alignment and increasingly accurate methods of correcting misaligned conditions. Based on the research and actual industrial machine evaluations, shaft alignment tolerances are now more commonly based on shaft RPM rather than shaft diameter or coupling manufacturer's specifications. There are presently no specific tolerance standards published by ISO or ANSI, but typical tolerances for alignment are as follows:
Another common method of determining shaft alignment tolerances is to ensure the machine feet are within a specified distance from what is considered "zero". This method can also be misleading. If a machine is considered to be aligned when the foot corrections are less than 2 mils at both the front feet and back feet, serious misalignment can sometimes be present. As a general rule, the smaller the machine foot print (distance from front feet to back feet), the worse the alignment condition based on the above criteria for alignment tolerance. Consider the following graph. The motor foot distance front to back is 10 inches. The distance from the front feet to the center of the coupling is 8 inches. If the front foot of the motor is left 2 mils high and the back feet are left 2 mils low, the shaft alignment results will be as follows:
Vertical Angularity of 0.4 mils/1", open at the top of the coupling, and a Vertical Offset of 5.2 mils high at the plane of power transmission. If this machine operates at 1800 RPM, it would be outside the acceptable shaft alignment tolerances. Again, this reinforces that a set of shaft alignment tolerances based on shaft RPM would apply to all machines regardless of their footprint.
Thermal Growth
Keep in mind the definition for shaft alignment from above while we discuss Thermal Growth. Machine conditions change from the time they are off line to when they are running under normal operating conditions. Some of these changes are due to process forces (e.g., fluid pressures, airflow, etc.). The most notable of these changes is the change in the temperature of the machine bearings and supports. This is called the machine's Thermal Growth.
Thermal Growth is the change in the length of a particular metal as a result of the change in temperature of that metal. Typically, when a metal bar is heated, it will get longer. These changes can be very small (0.0005") or they can be very large, depending on the length of the piece of metal and it's coefficient of linear expansion. The formula used for this calculation is often referred to as the T x L x C formula. T represents the change in the material's temperature in degrees Fahrenheit, L represents the length in inches of the material and C represents the material's coefficient of linear expansion. Different materials have a different C value. Using the above formula, we can anticipate the change in a machine's shaft alignment based on the expected changes in machine temperature. This is a chart of the most common machine materials and their C values:
Consider the following example:
A motor with a starting temperature of 70 °F is perfectly aligned to the pump shaft it will be driving. For the sake of this example, the temperature of the pump will not change, however the temperature of the motor will increase to 120 °F under normal operating conditions. The motor end bells material is cast iron with a C value of 0.0000059. The distance from the bottom of the motor feet to the center of the shaft is 15 inches. We can now calculate the change in position of the motor from Off Line to Running by multiplying the T, L and C values.
T x L x C = growth
(120 °F - 70 °F) x 15" x 0.0000059 = 0.0044"
Based on the above information, the motor will "grow" 0.0044 inches or 4.4 mils. If the growth of the motor is the same for both ends, the result will be a change in the Offset Alignment of 4.4 mils but the Angular Alignment will not change. This motor shaft should be aligned 4.4 mils lower than the pump shaft which will allow the machine to grow into an aligned condition.
This was a fairly simple example and does not accurately reflect what will happen to an actual machine. In reality, the temperatures of all the machine supports will change, however they will almost never change equally.
Using the above machine example, let's consider the change in the shaft alignment if the Outboard End (OE) bearing temperature changed by 20ºF and the Drive End (DE) bearing temperature changed by 50ºF. The drive end bearing would grow by 4.4 mils, however the Outboard bearing would only grow by 1.8 mils. The result will be a change in BOTH the Offset and Angular Alignment. If the motor feet are 20 inches apart, the change in the Angular Alignment will be 0.13 mils/inch [((4.4 - 1.8)/20) = 0.13] open at the top of the coupling. So as you can see, changes in the temperature of machines from Off Line to Running can have a significant impact on the shaft alignment.
These changes in the shaft alignment can be accounted for a few different ways. One way is to align the machines to "zero" and then remove or add the amount of shim under the machine feet as determined by the temperature data. Another way is to gather the alignment data, graph the results and pre-determine the actual shim corrections based on the graph.
With today's modern laser alignment technology, accounting for thermal changes at the
machine feet is actually a very simple evolution. Most alignment systems on the market today have within them a function that allows the user to program in the "Foot Targets" of the machine they are aligning. For the above example, the Front Foot Target would be -4.4 mils and the Back Foot Target would be -1.8 mils. After programming the determined foot target values at the machine feet, the user simply aligns the machines to "zero" on the display unit. The shaft alignment system will automatically calculate the required foot corrections to leave the feet at the prescribed positions. As the machine heats up, the shaft centerlines will "grow" into a properly aligned condition.
Thermal changes in gearboxes can be especially difficult to calculate. Often the input shaft temperatures will be different than the output shaft temperatures. This also causes the gearbox shaft alignments to change in the horizontal plane as well as the vertical plane.
Force lubricated systems with an oil cooler can also have an effect on the final alignment condition of a machine. Higher oil temperatures out of the cooler will result in a hotter operating condition of the machine, therefore a more drastic change in the Running Alignment condition. A 10ºF change in the operating temperature of a turbine from 105ºF to 115ºF can change the foot positions by as much as 2 to 4 mils. The alignment condition of turbines and compressors that operate at very high speeds can be adversely affected by these relatively small temperature changes.
Pipe Strain
Another condition that changes is the increase or decrease in temperatures of the suction and discharge piping attached to pumps and compressors. Some compressors may actually form ice on the suction end while the discharge piping is too hot to touch. Conditions like this can force major changes in the operational alignment condition of machines. While OEM's might be able to anticipate the nominal changes in operating temperatures of a piece of equipment, they cannot accurately anticipate the effects of the piping configurations of the final machine installation or the changes in the temperature of the piping runs. Piping runs are typically very long and can have a tremendous impact on the change in the shaft alignment from off line to running condition. In addition, piping connections act as fixed (or restraining) points with respect to the tendency of machines to move/grow when on-line. The effect of these fixed points on the final position of the machines is almost impossible to calculate or predict.
Depending on the piping configuration, these changes may be in the Vertical Plane or in the Horizontal Plane and are extremely difficult or impossible to accurately calculate based on the TLC formula above. Let's consider two identical Boiler Feed Pumps.
BFP #1 and BFP #2. BFP #1 feeds #1 Boiler which is 20 feet away and BFP #2 feeds #2 Boiler which is 60 feet away. The length of the discharge piping on BFP #2 will be approximately 3 times longer that BFP #1. This will result in the two "identical" machines showing drastically different alignment changes from Off Line to Running. A great deal of care must be taken when calculating the changes in the alignment condition of these machines. Just because two machines appear identical and serve the same function does not ensure they will exhibit the same operational characteristics.
Determining Alignment Changes
In the past, there have been several methods used to attempt to measure the changes in the shaft alignment of two or more machines. One of these methods involves measuring the changes in the machine temperatures at each machine support and perform the target alignment based on mathematical calculations.
Another method relies on tooling balls mounted on machine bearings. Typically an optical transit (scope) is used to measure the off-line positions of the tooling balls. Once the machine is at operating conditions, another set of measurements is made; the positional changes are compared to the "stationary" tooling balls. These changes are triangulated to calculate the change in the position of the shafts.
There is a variant to the above method, called the Acculign® method, which involves installing tooling balls in the foundation as well as at the bearings. The distance between the fixed tooling balls (mounted in the foundation) and the bearing-mounted tooling balls is measured off-line and then on-line. Precise measurements of the distances and angles are required to make the calculations of the growth.
Yet another method to gather this data is to perform a "Hot Alignment Check" of the affected piece of equipment. The procedure for this is relatively simple. The machine is aligned off-line and the results of the alignment are documented. (HA, HO, VA, and VO). The machine is then placed on-line and allowed to reach normal operating conditions. At this point the machine is shutdown and allowed to stop rotating. The alignment system is re-mounted on the machine and the shaft alignment is re-measured and documented. At this point the machine may be aligned hot by re-shimming and re-positioning the moveable machine as quickly as possible. One drawback of this method
is that the machine will begin to cool as soon as it is shutdown, adversely affecting the accuracy of the hot alignment check.
If the two sets of alignment readings were documented, a set of "Cold Alignment Targets" can be calculated. Alignment Results (hot) - Alignment Results (cold) represents the change in the alignment condition of the machine from Cold to Hot. The alignment targets for this machine will be the opposite of the changes in the alignment parameters.
While this is currently a widely used method of hot aligning machines, it will only measure the changes in the shaft alignment due solely to the changes in the machines' temperature. Discharge pressure, shaft torque, multiple machines operating in parallel, electrical loading of a generator, etc. can also play a very large role in the change in the alignment condition from Off Line to Running. These changes will most often be seen in the Horizontal Plane, but could affect the Vertical Alignment as well.
Yet another factor to consider is where the machine in question is located. If a machine is located indoors in a controlled environment the operating characteristics should be relatively constant throughout the year. A machine that operates outdoors and is exposed to large changes in temperature could also exhibit extreme changes in its shaft alignment as the temperature changes (as in the change of seasons).
On-Line positional change measurements
One method used to measure the change in the alignment of two pieces of machinery is to document their bearing cap positions in both the horizontal and vertical planes relative to some fixed points in space while the unit is Off Line. After the data has been documented, the machine can be started and placed on line. When the machine has reached its normal operating temperature, the positions of the bearing caps is again measured and compared to the points that are stationary. The movement of the machines and the changes in the shaft alignment can then be either calculated or graphed. In the past, there have been problems obtaining on-line readings using this method. A nominal amount of vibration can make an optical scale very hard to read through a transit or theodolite. Care must be taken that the scale is placed back in the exact location for each measurement at each point. Bearing caps are not typically precision machined on the outside surfaces. A very small deviation in the position of the detector can lead to a very large error if the surface that is being measured is not flat and smooth.
Modern laser based measurement systems designed to measure flatness and surface parallel can also be used in this manner. One benefit of the laser based positional measurement systems is that the data can be averaged, eliminating the potential large errors when measuring machines that are running. When the laser beam strikes a vibrating detector surface the data will appear to "bounce" slightly. A simple function in the display unit will sample the data for the desired amount of time, locate the maximum and minimum value on the detector and average the data accordingly. Since vibration, by definition, is cyclic and repeatable very good results can be obtained.
Laser Measurement Systems
In the 1980's a laser-based system became available that could be mounted to the DE bearings of a machine and would monitor the changes in the machine's alignment from Cold to Hot or from Hot to Cold. Two laser transmitter/detectors are mounted on the Stationary Machine Drive End Bearing. One of these transmitter/detectors must be positioned in the 12:00 position (to monitor vertical changes) and the other must be
positioned in the 3:00 position (to monitor horizontal changes). The transmitter/detector's are positioned coaxially with the stationary shaft centerline and level. Corresponding prisms are mounted on the moveable machine DE bearing. The prisms are positioned to reflect the laser beam back to the detectors mounted on the stationary machine. The transmitter/detectors are hooked up to a computer running the measurement software. The user can now program the alignment monitoring equations into the software. The user can program the system to monitor all 4 alignment parameters simultaneously. The values are "auto-zeroed" and the data collection begins.
When the machine is started and the alignment changes, it is recorded in the system software. When the machines reach normal operation the data collection can be stopped and the alignment changes calculated. The results are displayed as a graphical trend.
The cold alignment targets will be opposite of the measured change in the machine alignment if the data collection was started when the machine is cold. If the cool down was monitored, the targets are equal to the values displayed in the software. While this system can be very effective for diagnosing alignment problems, it can also be very time consuming and frustrating to setup and monitor. Any change in the bracket position
during the data collection will introduce errors into the results. This system also requires the user to purchase a PC to use for the data collection.
Thermal Growth Case Histories
What are the Real Alignment Targets?
A real life example is a recent project at a wastewater treatment plant in Cleveland needing the development of realistic cold alignment targets for a 3600 rpm compressor. This machine had a long history of coupling and bearing failures. Over a two-year period several attempts were made to calculate the thermal growth on the motor and compressor supports. The OEM's technical manual gave a vertical thermal offset value of +0.040".
There were no recommendations for a target Vertical Angularity. Horizontal alignment changes were not mentioned.
There was some confusion with the OEM targets as provided. The maintenance personnel did not know if this value represented what the Rim Dial Indicator should read when the cold alignment was completed (with a dial indicator mounted on the stationary shaft and indicating the motor coupling). Dial indicators will indicate the Total Indicated Runout (TIR) each time the shaft is rotated 180 degrees. Half of the TIR represents the actual centerline offset, therefore the target should actually be +20 mils vertical offset.
The technician averaged temperature changes measured from the bottom of the support to the split line of the machine. This data was also compared with hot alignment readings taken with a modern laser shaft alignment system. The result of all the data was a calculated Vertical Offset target of +19 mils and a Target Vertical Angularity of +.65 mils/1". No targets were calculated to compensate for horizontal alignment changes.
A laser-based monitoring system was installed on the machine and the shaft alignment was monitored as the machine was placed on line and allowed to operate until it reached normal operating conditions. There were some very interesting changes in the machine's operating characteristics. A set of machine vibration data was collected at thirty-minute intervals during the machine's warm-up period.
Below are the graphs collected from the laser-based monitoring system.
Change in Vertical Angularity when vibration was at its lowest recorded value. -18.61 mils
Change in Vertical Angularity when vibration was at its lowest recorded value. -.55 mils/1"
Change in Horizontal Offset when vibration was at its lowest recorded value. +4.658 mils/1"
Change in Horizontal Angularity when vibration was at its lowest recorded value. +0.252 mils/1"
The shaft alignment was set with a Vertical Offset value of +19 mils and a Vertical Angularity value of -.65 mils/1". The vibration data collected on the machine bearings continued to improve reaching a low of 0.130 in/sec (peak overall) until the change in the alignment reached the calculated targets. Unfortunately the alignment continued to change past the calculated values and as the alignment moved farther away from "zero" the vibration data trended back up to fairly high levels, 0.3 in/sec (peak overall). Spectral data indicated misalignment. The farther the alignment moved away from tolerance, the more clearly the signs of shaft misalignment became.
The laser-based monitoring systems data indicated changes in the horizontal alignment that would take the alignment out of tolerance in the horizontal plane as well. The total change in the shaft alignment was as follows:
Vertical Offset: -22.2 mils
Vertical Angularity: -0.88 mils/1"
Horizontal Offset: +4.42 mils
Horizontal Angularity: +0.55 mils/1"
Based on the changes in the alignment as measured by the laser-based monitoring systems the cold alignment targets for this machine are as follows:
Vertical Offset: +22.2 mils
Vertical Angularity: +0.88 mils/1"
Horizontal Offset: -4.42 mils
Horizontal Angularity: -0.55 mils/1"
Note: data was obtained from a start-up, therefore targets are opposite of the recorded change
So, what was learned from this example of thermal growth documentation? The first lesson learned is that no matter how many statistical calculations go into a thermal growth estimate, the best way to get thermal growth information is to measure it directly.
Another lesson to be learned is that OEM recommended cold alignment targets, while sometimes close, can't accurately predict the actual operating conditions of a machine in it's final installed state.
A third lesson can be learned from the changes in the horizontal alignment data. The dynamics of machines during operation force changes in the shaft alignment that can't be measured during a "Hot Alignment" check. The machine examined in the above example had a Horizontal Offset of +4.4 mils during operation. When the machine was shutdown the Horizontal Offset immediately changed by -3 mils leaving a net horizontal change of +1.4 mils. The +1.4 mils is most likely due to temperature changes in the piping, however 3 mils of the total change were most likely due to rotor torque and discharge pressure of the compressor.
Knowing the initial alignment condition of the machine and the measured changes in the alignment allows us to estimate the current operating misalignment of this machine. They are as follows:
Vertical Offset: -3.2 mils
Vertical Angularity: -0.23 mils/1"
Horizontal Offset: +4.42 mils
Horizontal Angularity: +0.55 mils/1"
For a 3600 RPM machine, the offset values would be considered outside the acceptable tolerance and the angularity values are also higher than would normally be considered acceptable. This also goes directly to the subject of shaft alignment tolerances based on shaft RPM rather than on maximum coupling alignment values as discussed above. Many coupling manufacturers would consider the alignment data acceptable, however, from the vibration data we can see that considerable force can be applied to the machine bearings due to small amounts of shaft misalignment.
Identical Machines Not Identical Alignment Targets
Another recent project involved performing Off Line to Running examinations on 2 identical machines at a Co-Generation facility in Virginia.
The machines are Gas Turbine Generator units that have been experiencing high vibration issues at particular times along their operating cycle. Both of these units were considered "identical" in terms of manufacturer, size, containment structure, load rating, installation, RPM, etc. A laser-based monitoring system was set up on both units and the set-up dimensions were programmed into the computers. Data collection was started and the machines were placed into their start-up modes at approximately the same time. While the trended changes in the alignment had the same basic shape to the graph, one of the units showed a dramatically different change in the Vertical Offset alignment. Both of these machines are supposed to operate at the same temperature and both machines were set to the OEM recommended cold alignment targets. Below are the graphical results of the Vertical Offset changes on these supposedly "identical" machines.
Unit #5 Maximum change in Vertical Offset
Unit #6 Maximum Change in Vertical Offset
Units #5 showed approximately a +20 mil maximum change in the Vertical Offset and settled around +10 mils at normal operating conditions.
Unit #6 showed approximately a +30 mil maximum change in the Vertical Offset and settled around +20 mils at normal operating.
The OEM technical documentation states that the generator will "grow" 20 mils evenly front to back and the clutch will grow 22 mils evenly front to back. That works out to a +2 mil change in the alignment from Off Line to Running at Normal Operating Conditions. As noted above, this value is not accurate and does not reflect the actual operating conditions of either machine.
Going back to the tolerances for a 3600 RPM machine, +/- 2 mils recommended vertical offset misalignment, Unit #5 is operating with a Vertical Offset of +8 mils and Unit #6 is operating with a Vertical Offset of +18 mils.
These particular machines have been operating under these conditions since their installation over a year ago and have a history since their first day of operation of high vibration readings and premature clutch failures. The test on both of these units required less that one day to complete.
Conclusion:
The cost of an alignment is typically very small when compared to the cost of the loss of production should a critical piece of equipment fail. Even with the introduction of portable vibration monitoring equipment and easy to use laser alignment systems, alignment still ranks as one of the leading contributors to premature rotating machinery failure and lost production. One of the reasons for this is the neglect (or miscalculation) of machinery dynamic movements. We have shown that besides cold alignments, the actual dynamic movements of machinery need to be considered when aligning.
This problem, of ignoring the dynamic changes in the shaft alignment of two machines from an Off Line to Running condition, needs more attention. There is mounting evidence that long-standing assumptions are leading to machine reliability problems. Assumptions such as believing "identical" machines have identical dynamic movements, relying solely on the OEM recommendations, ignoring the possibility of horizontal movement, assuming growth will be symmetrical and only accounting for the thermal effects. These assumptions need to be challenged, and behaviors changed.
Granted, the options available on the market today are not very enticing. Optical methods, mechanical methods, and even the laser-based monitoring systems all require some special skills and expertise in order to obtain good results. As an equipment owner/operator, it may be prudent to contract these services for critical equipment rather than attempting to grow the skills in-house (the learning curves can be pretty steep!).
Regardless of the approach taken to measure true dynamic movement, coupled machines need to be set to cold alignment targets that will reflect the actual changes in the shaft alignment. This will lead to lower vibration levels, increased Mean Time Between Failures, decreased maintenance expenditures and increases in production. Much like the philosophical change from aligning shafts with dial indicators to aligning shafts with laser based systems, these types of measurements will take some time to be generally accepted and routinely practiced. While the current technology may be relatively expensive, a simple cost/benefit analysis will help you make the right decision, which can yield a significant increase in machine availability and profit.
© 2002 VibrAlign, Inc