Se contactaron con A.T. Kearney para comparar sus resultados contra el "mejor de lo mejor" en los EE.UU., Europa y Asia (Figura 1). DuPont descubrió que no tenían que preocuparse por la pérdida de la excelencia funcional porque no tenían una para empezar. La diferencia más dramática en el rendimiento fue con los japoneses que tenían costos mucho más bajos con una mayor confiabilidad y menor inventario.

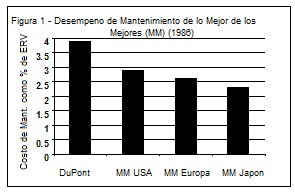
Figura 1
Hasta este punto, el enfoque de los puntos de referencia había sido en gran medida de la función de mantenimiento y coste de mantenimiento. El análisis estadístico de los datos de evaluación comparativa (benchmarking) parece indicar que sólo unas pocas variables en los puntos de referencia representaron casi la totalidad de la variación en el rendimiento, pero todas estas variables eran fundamentalmente las variables de costos. La implicación de este análisis fue: centrarse en la reducción de costos para lograr el rendimiento de "mejor de lo mejor". Sin embargo, el equipo de evaluación comparativa que habían participado en las visitas durante esta evaluación, sabía que los "mejores" no se centran en el tan solamente en el costo. Tenían la sospecha de que estos factores de mejora en los costos eran el resultado de un buen mantenimiento y no la causa, así que comenzaron a excavar más profundamente en la estructura de la confiabilidad.
DuPont decidió utilizar los Sistemas Dinámicos de Modelado para comprender mejor la estructura de la confiabilidad. Los Sistemas Dinámicos es una disciplina que salió del MIT (Instituto Tecnológico de Massachusetts) en la década de los sesentas y fue creada por Jay Forrester en 1961. Ha ganado popularidad en los últimos veinte años con la publicación de La quinta disciplina de Peter Senge (1990), y la introducción de herramientas mas fáciles de usar mediante programas en las computadoras personales. Los Sistemas Dinámicos de Modelado se enfocan en el descubrimiento y la articulación de la estructura subyacente de un sistema, y luego busca los puntos de influencia para cambiar el sistema. En lugar de simplemente mostrar una instantánea de lo que el rendimiento podría ser similar al final del viaje, como un punto de referencia lo hace, muestra el viaje en sí.
Lo qué DuPont descubrió a través de este esfuerzo fue que el mantenimiento y la confiabilidad podría describirse como un proceso de gestión de defectos. Una visión simplificada de este "modelo mental" se presenta en la Figura 2.

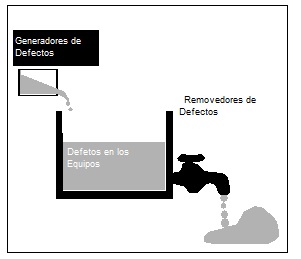
Figura 2
Definimos un defecto como "cualquier desviación de la perfección "para evitar largas discusiones acerca de si un rasguño de 1 o 2 pulgadas de de largo, es sólo un defecto. Con esta definición, todos los equipos tienen defectos; es solo cuestión de grados. Los defectos pueden provenir de varias fuentes, discutidas en detalle más adelante, y cuanto mayor sea el nivel de defectos, mas problemas de confiabilidad el sitio tendrá. Los defectos se remueven a través de trabajos de mantenimiento ya sean reactivos una vez que el equipo falla, o de manera proactiva a través de prevención o mantenimiento predictivo. A través de este esfuerzo se hizo evidente que el "mejor de lo mejor" en los EE.UU. y Europa logra sus resultados principalmente mediante la eliminación de defectos de forma más eficaz mediante una mejor planificación, programación, habilidad de sus técnicos, y de tecnologías predictivas. DuPont descubrió que era fundamental que estas cosas se tenían que hacer de manera coordinada y no sólo un programa a la vez. Lo interesante fue que el "mejor de lo mejor" en Japón no sólo tiene una versión mejorada de estas técnicas de mayor eficiencia. Tenían un enfoque fundamentalmente diferente, le quitaron el defecto temprano en su vida o evitaron poner defectos en el equipo en primer lugar, que eliminó el trabajo que viene con estos defectos.
Las Fuentes de los Defectos
Para eliminar los defectos es importante comprender de donde vienen. La Figura 3 le muestra las 5 principales causas de defectos.
1. Defectos de calidad de los materiales. DuPont descubrió que una de cada tres piezas de repuesto tenía un defecto de algún tipo. Estos defectos pueden ser defectos de fabricación pero también pueden ser defectos por la forma en que se almacenan, manejan y distribuyen. (Ejemplo: la corrosión de una parte debido a almacenamiento a la intemperie.)
2. Defectos de mano de obra. Estos defectos provienen de no hacer un trabajo de reparación adecuada. A veces estos defectos provienen de las carencias de cualificaciones en los mecánicos, pero igual de importante, que puede provenir de la no aplicación de las habilidades que se conocen. En una planta reactiva típica por lo general hay una serie de políticas, sistemas y culturas que mantienen a los mecánicos de hacer el mejor trabajo que saben hacer. Lo que cuenta en la mano de obra es la calidad del trabajo que en realidad se hace, no la calidad del trabajo que se sabe hacer. (Ejemplo: No alinear una bomba antes de ponerla de nuevo en línea.)
3. Defectos de los eventos de falla. Cuando un sistema de un equipo falla, generalmente energía extra se dirige a otra parte del sistema. Esta energía extra a menudo añade nuevos defectos que pueden ser fuente de futuras fallas. (Ejemplo:. un rodamiento detenido, provocando una ligera inclinación en el eje)
4. Defectos de diseño. Para cualquier grado el diseño del equipo no se ajusta a las necesidades actuales de la empresa, habrá defectos de diseño. Estos defectos pueden venir desde un diseño inicial pobre, pero por lo general son el resultado de los cambios en el negocio que no se reflejan en las operaciones. A medida que el cambio en los negocios y la operación con el tiempo, los requisitos de los equipos van a cambiar también. Si el diseño no es actualizado y si no se modifica el equipo o sistema para adaptarse a las nuevas condiciones, los defectos serán agregados al sistema. (Ejemplo: el flujo a través de cierta bomba se corta hacia atrás haciendo que se ejecute de nuevo en la curva y se desgaste a sí misma.)
5. Defectos de las operaciones. En nuestra definición de un defecto, cualquier equipo que se opera, acumulara algunos defectos del desgaste normal. Sin embargo, como cualquier lector con un conductor adolescente puede dar fe, la forma en que se opera algo, tiene un gran impacto en el nivel de defectos que se introducen. Muchos de los defectos que en última instancia conducen al fracaso o se introduce a través de operaciones o son detectables por las operaciones mucho antes de que causen una falla. (Ejemplo: una bomba de cavitación, haciendo caso omiso de vibración excesiva.)
Un mantenimiento tradicional enfocado técnicamente a la confiabilidad se centrará en las tres primeras fuentes a través de mantenimiento preventivo, tecnologías predictivas, las auditorías de los proveedores, inspección de piezas y la capacitación profesional, pero por lo general se ignoran las últimas dos fuentes. Cuando usted se centra en la limitación de todas las fuentes de defectos, así como la eliminación de los defectos actuales en su sistema, la mejora de rendimiento puede ser dramática. Recientemente, la Refinería de Lima nos ha enseñado que la mejor filosofía para incorporar la eliminación de fallas en la labor ordinaria de mantenimiento, operaciones, diseño y compras. Llamaron a esta filosofía "No sólo arréglelo, mejórelo", que es el nombre de nuestro libro sobre la eliminación de defectos.