Maintenance Supervisors should use this tool to train their maintenance techs, welders and contractors - 10-20 minutes - Post them in the Maintenance Shop after use:
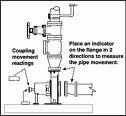
Pipe stress is caused by misalignment of the mating surfaces of two pipe flanges creating abnormal internal stress of pump bearings, seals, motor bearings, couplings, and can possibly change the displacement of a pump.
General Rules which must be followed by maintenance personnel and contractors: (if you want to stop self induced failures)
1. Pipe Flanges attached to pumps must be aligned where the gap does not exceed the thickness of two gaskets or tolerance established by your company's engineering standards.
2. Pipe flange bolts must drop in without assistance.
3. Cable pullers, come-a-longs, or long bars should not be used when aligning a flange which is connected to a pump.
4. Validate the elimination of pipe stress by following the procedure below.
Failure Modes experienced from Pipe Stress on Bearings:
- Wear caused by seals leaking
- Wear caused by static vibration
- Indentations caused by overloading while static
- Corrosion caused by inadequate lubrication caused by abnormal loading (seal leaking)
- Flaking caused by misalignment and excessive loading
WARNING: Ensure your contractors follow the same process to eliminate pipe stress. Pipe stress elimination should be validated during commissioning of new pump.
Follow this process if you want to inspect your pumps which may have pipe stress:
1. Align the two shafts between your pump and driver (typically an electric motor) to tolerance recommended by the equipment vendor or your company's engineering standards.
2. Validate misalignment to insure motor and pumps shafts are aligned to specification.
3. Disconnect the outlet flange on the pump.
4. Revalidate laser alignment of shafts.
5. If alignment has moved then you have pipe stress. Do the same for the inlet flange.
6. Make corrections as stated in the following procedures to eliminate pipe stress.
Elimination of Pipe Stress - The Ricky Smith Method as learned from Dan Turner (my maintenance and engineering manager at Exxon during the 1970s)
1. Bolt flanges to pump and insert blind flange gasket along with two regular flanges between pump and mating flanges. (cover the hole between welding area and inside the pump)
2. Attached welding ground to flange. (do not attach ground lead to pump; welding group must always be attached to flange) Warning: failure to accomplish this one task properly will cause bearing failure by "electric arcing" which is a failure mode of bearings.
3. Tack weld flange into place reverse welding each tack.
4. Allow to cool for 10 minutes.
5. Reverse stitch weld on opposite sides on the flange similarly used for cast iron welding.
6. After initial reverse stitch weld then weld normally using electrode recommended by the American Welding Society (typically E-6010 5P or GTAW.
7. After root pass; weld in any direction you wish.
8. Allow to cool and then disconnect flange, replace gaskets and;
- Validate bolts will drop into holes without pry bar
- Validate gap between flanges is no more than two gaskets thick.
If you have questions send me an email at rsmith@gpallied.com