Being tasked to gather data about machine condition is an important responsibility, but it is only one component of the condition-based maintenance (CBM) routine. Having a computer full of facts and figures is not much good to anyone if the data cannot be mined and shared in an efficient way. There is a certain power and consequence responsibility in the knowledge gained from CBM data collecting. Finding meaningful ways to share that knowledge empowers the entire team and is the final piece of the CBM puzzle.
In Part 1 of this series, we identified what condition-based maintenance is and some of the reasons for implementing it. We asserted that CBM represents a change of thinking where work orders are driven by data rather than lapsed time. The importance of carefully planning condition-monitoring tasks was highlighted, while we stressed the necessity to think beyond rotating assets when compiling asset lists to survey. Aligning the expectations of upper and middle management, as well as frontline staff, is another key ingredient for success. Part 1 reputed the simplicity and versatility of ultrasound testing as a CBM pillar. Ultrasound answers the one question that every planner asks: "Is it okay?"
Part 2 took us beyond the "what is it?" and "why we need it?" message to tackle a much more formidable question: "How do we do it?" We revealed the secrets to avoiding early frustration and not overwhelming your initiative by taking too big a bite. We also showed how to keep at bay naysayers whose negativity remains a constant threat to your success. The central message of Part 2 teaches us to categorize the types of problems we will encounter. Sort which defects are binary (good/bad), which defects are trendable and which defects are best identified with dynamic signal analysis. Only then can we begin to build a useful database.
We began Part 3 of this series by stating that "knowledge is power." We also asserted that sharing knowledge empowers us all. So it should come as no surprise that the final piece of the CBM puzzle is COMMUNICATION. Remember, condition-monitoring data is really just gathered intelligence that suggests something is about to go really wrong. To maintain alignment between the expectations of upper management, middle management, production and frontline workers, how can CBM data best be conveyed so it means something to everybody? Let's start by looking at the objective of good reporting.
Reporting
The objective of good reporting is to inform the people who need to be aware. They need to know what work they must do to bring an asset back to best condition. They need to know when that work should be done and the consequences of not acting on the work in a timely fashion. The job of the report generator can be compared to that of a translator. This job normally falls on the person responsible for collecting condition-monitoring data. CM data is the machine, the valve, the pump, the motor, the "whatever it may be" talking to you in an ultrasonic language. You are trained to understand that language. It is your job to translate what the asset is telling you into meaningful information that the planner, the repair crew, production and management can understand. That is what a good report should be; a product of considered engineering opinion based upon the facts you have gathered.
A report should NOT be data spewing. Time signals and spectra are merely hieroglyphics to most and while they may look pretty to techies, they will not impress upper management. Should they be included? Absolutely, but only as supporting illustrations to your clear explanation of the problem. What message should you be conveying then? Your report should start by stating the problem:
"There is an issue with this machine, or this valve, or this bushing, or this transformer. Additional follow-up with vibration analysis and an oil lab report is recommended to confirm the problem."
Identify the asset and identify the issue. Then clearly state what needs to be done to bring it back to best condition. A good report should also include a message about the consequence of doing nothing:
"You can fix it now and the cost for the repair, including spares, labor and scheduled downtime, will be $500. Or, you can leave it alone, hoever, besides continuing to impact production and product quality, the cost to fix it on an emergency basis will be $50,000."
What is wrong with writing a strong messaged opinion such as this in your report? Is it politically incorrect to make that assertion and state the blindingly obvious? Or is there lingering fear of making a bad call. The latter is a confidence issue that relates either to distrust in the technology used for CM or the person charged with collecting the data. Both can be addressed through expert training.
Specific Reports
Compressed Air Surveys
What should be included in a compressed air report? First off, the report should identify the location of the leak and if it is tagged, the serial number of the tag. Why was the leak tagged in the first place? State the reason why it couldn't be fixed there and then. Maybe the part was not available. Perhaps the leak could not be fixed without interrupting production. If you are going to write a report about an air leak, and part of fixing it means turning the air off, then make sure you write enough description for them to find the leak. We've lost count of the number of plants we visited where air leak tags are hanging from this year's survey and right behind them is the previous year's survey tag. You have to wonder why energy is being spent to find leaks that are not being fixed. And if you are curious, then write that in the report, too. It may be the only way to communicate to upper management that your efforts are being wasted.
Steam Trap Surveys
The first few times doing a steam trap survey, you will generate a huge list with lots to fix, especially if a survey has not been done there. Can steam trap problems correlate to production problems? Do you have complaints like, "I can't maintain temperature in the autoclave," "I can't maintain temperature in the oven," or "energy costs from the boiler are 25% higher than a year ago?" Can any one issue be tracked back to a specific steam trap? If yes, this is quite useful in terms of your "what happens if I do nothing" calculation for your report:
"If we do nothing about steam traps we can't carry on with production, or product quality."
Valve Inspections
Not all valves operate all the time, so scheduling needs to play into data collection, not just repairs. Valves are a very typical binary defect. They either work or they don't. However, the use of dynamic signal analysis is useful in determining if a valve is closed or partially leaking, as you can see from the time signals in Figures 1 and 2. Both dynamic time signals were taken on the same valve body of a 60cm recycle valve. The first signal was captured with the valve closed and the second when the valve was cracked open ten percent. The signals sounded very similar to the ear, yet the dBμV measured value was 41 when closed and 67 when opened. The difference of 26dBμV means the signal is 18 times louder when opened.
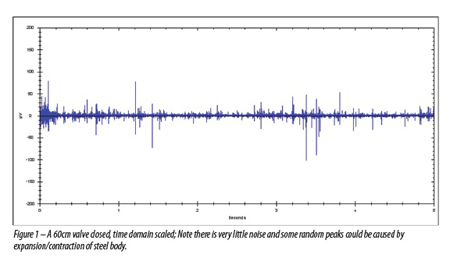
Figure 1 - a 60cm valve closed, time domain scaled; Note there is very little noise and some random peaks could be caused by expansion/contaction of steel body.
Figure 2 - A 60cm valve 10% open, time domain scaled; Note carpet value noise is significantly higher when compared to scaled dynamic signal in Figure 1.
The problem is the cost of overhauling the valve is $50,000, regardless of condition. Producing a report that clearly identifies this passing valve must convince all concerned that the overhaul is necessary. By providing the measured dBμV delta of 26, you give quantitative data. By providing the scaled time domain graphic, you provide a visual illustration of a closed valve versus a suspected leaking valve.
Electrical Surveys
Combining ultrasound with your infrared (IR) scans makes for a more complete inspection. Both technologies will find things the other may miss. Combining a time signal alongside the thermal image in your report adds a visual impact that may otherwise be missed. Take for example the time signal in Figure 3 showing a three-phase transformer connection with corona activity. The images illustrate the problem as found and the positive effect simple maintenance played in improving the situation. These types of images serve as an excellent visual addition to your reporting.
Figure 3 - Corona discharge prior to and after cleaning on a three-phase bushing
Listen to a Sound File of Figure 3a
Listen to a Sound File of Figure 3b
Lubrication Surveys
So you've been out checking a number of bearings for your pump survey and found a list of those that need greasing. Provide a trend graph (Figure 4) that shows static ultrasound readings increasing over time to the point where relubrications are required. Reinforce the decision to lubricate by attaching a time domain graph showing before and after affects of properly applied lubrication. And finally, by attaching the actual wave file to the report, everyone in the office can listen to what you heard in the field.
Figure 4 - A dynamic recording of a bearing as it receives the required shot(s) of lubricant
Listen to a sound file of Figure 4
Final Thoughts
If proper thought and planning are not given to reporting, all our best efforts to implement condition monitoring come crashing to the ground. The primary purpose of good reporting is to translate what the machine is telling us about its health, what condition it is in today and how long we have to fix it properly with minimal consequence to production and profitability. We must produce reports that are clear about what the issue is, where the machine is located and what must be done to bring the asset back to best possible condition. Finally, a report must tell all who read it what will happen if no action is taken. If data and historical trends suggest that failure is three weeks or less, what will be the consequence and cost of delaying action to a shut down scheduled four weeks out? Be clear, be concise and know the interpretive capabilities of everyone who will read your report.