
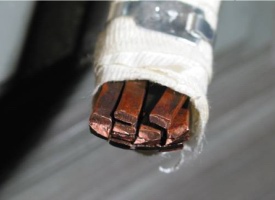
Figure 1: Multiple Wires Making Up One Conductor
The Stator Connection Testing
The highest quality connections involve brazing the conductors together in order to make a solid, low resistance connection. However, mistakes in brazing will cause broken wires or a loose connection. During the rewind process, the connections are first made, then insulated and tied down. Figure 2 shows a completed winding set up for power testing. Normally, during this test, power is supplied to the winding and a ball bearing or dummy rotor is used to ensure that there is proper rotation. If a coil or connection is reversed, then the bearing or rotor will stop or reverse.

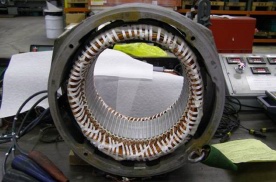
Figure 2: Motor Set Up for Power Test
The second part of the power test is to increase voltage until the current matches the nameplate current. This is applied until the winding and stator core begins to heat and the operator checks for hot or cold spots on the winding or core.
Infrared Analysis of Test
Another method of evaluating the condition of the winding can be performed. In this test, prior to insulating the connections, they are left exposed and the power applied to nameplate value. At that point, infrared images are taken and the connections evaluated, they should be the same, or lower, temperature than the winding end-turns.
An additional test can be performed, using this method, after the winding is completed and before it is varnish insulated. With the stator set up as shown in Figure 2, power is applied up to the nameplate current rating. The winding is then evaluated and any hot spots are evaluated further, as shown in Figures 3 to 7. This data was taken at Dreisilker Electric Motors, Inc. (http://www.dreisilker.com) as part of a study on motor repair.
Figure 3: Stator Winding and Connection as it Begins to Heat
Figure 4: Stator Winding Heating (1)
Figure 5: Stator Winding Heating (2)
Figure 6: Stator Winding Heating (3)
Figure 7: Stator Winding Heating (4)
In Figures 3 through 7, taken with a Fluke Ti30 Thermal Imager (http://www.fluke.com), the connection points were good. Additionally, the winding had passed when the connections were exposed.
Conclusion
Loose winding connections will generate heat based upon I2R losses. As part of a final test, infrared can be performed before the connections are insulated, then after. Hot spots in the windings or connections can be investigated and repaired prior to varnishing, reducing potential warranty issues. The time to perform the test is negligible as the power testing is normally performed as part of a rewind quality control step.
Bio:
Howard W Penrose, Ph.D., CMRP, is the President of SUCCESS by DESIGN, a reliability and maintenance services consultant and publisher, and the Founding Executive Director of the Institute of Electrical Motor Diagnostics, Inc. He has over 20 years in the energy, reliability and maintenance industries with experience from the shop floor to academia and manufacturing to military. Dr. Penrose's personal clients include the UAW/GM Worldwide Facilities Group for all GM facilities energy and maintenance best practices, US Steel motor system maintenance and management programs, Amtrak electrical reliability and Reliability Center, Inc. as their electrical scene investigator and trainer. In the past, Dr. Penrose worked as an electric motor repair journeyman, field service manager, Adjunct Professor of Industrial Engineering at the University of Illinois at Chicago, Senior Research Engineer at the UIC Energy Resources Center, General Manager of an electrical motor diagnostics instrument vendor, Vice President of a US Military R&M consulting firm and President of an industrial R&M consulting firm. He has repaired, troubleshot, designed, installed or researched a great many technologies that have been, or will be, introduced into industry, including being involved in the reliability investigation of Left Ventricle Heart Device motors and design improvements in association with the University of Virginia. He has coordinated US Department of Energy and Utility projects including the industry-funded modifications of the US DOE's MotorMaster Plus software and the development of the Pacific Gas & Electric Motor System Performance Analysis Tool project. Dr. Penrose's UAW/GM WFG team won the 2006 Quality Network Planned Maintenance ‘People Make Quality Happen' award for their work in improving the steam systems within General Motors facilities by adopting the US Department of Energy tools and best practices. Dr. Penrose is a past Chair of the Chicago Section of the Institute of Electrical and Electronics Engineers (IEEE), and presently leads several IEEE Standards Authority efforts and is a USA representative to ISO for industrial reliability standards. He is a member of the Vibration Institute, Electrical Manufacturing and Coil Winding Association, International Maintenance Institute, Society of Maintenance and Reliability Professionals, NETA and a Life Member of MENSA. He has numerous articles, books and professional papers published in a number of industrial topics and is a US Department of Energy MotorMaster Certified Professional as well as a trained vibration analyst, infrared analyst and motor diagnostics professional.
Questions concerning this article can be emailed to Dr. Penrose via howard@motordoc.net or view the SUCCESS by DESIGN website at http://www.motordoc.net