Failure Modes: A Closer Look at Ductile and Brittle Overload Fractures
Metals are frequently thought of as ductile or brittle. However, they sometimes behave differently when they fail from an overload. A ductile metal may act as if it were brittle. A brittle metal may behave in a ductile manner.
Ductile materials frequently undergo brittle fracture. Inherently, brittle materials rarely crack in a ductile mode.
The factors that cause these different behaviors include: strength, temperature, rate of loading, stress concentrations, size and various combinations.
Strength
Strength is the most obvious determinant of a metal's behavior when it is overloaded. In general, soft tough metals will be ductile. Harder, stronger metals tend to be more brittle. The relationship between strength and hardness is a good way to predict behavior. Mild steel (AISI 1020) is soft and ductile; bearing steel, on the other hand, is strong but very brittle. The relationship between strength and hardness of steel is shown in Figure 1.

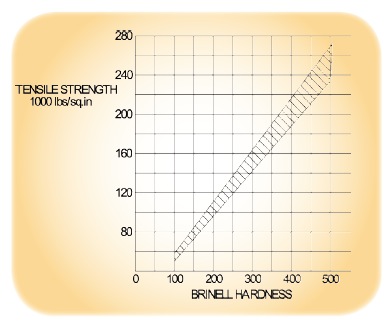
Figure 1: Steel Hardness vs. Strength
The elongation (stretch per unit of length) percentage, usually given as % in 2-inch length, is also a means of judging ductility. More ductile metals have greater elongation. For example, the elongation of harder and stronger 4340 quenched and tempered steel is about 16%, while elongation of more ductile hot rolled 1018 steel is about 36%.
There are exceptions to this relationship. The most common exception is grey cast iron, which is quite brittle even though it is fairly soft. Its composition of sharp-edged graphite flakes creates stress concentrations that override the ductility of the iron.
Temperature
Temperature has a significant affect on the ductility of metals. Low temperature decreases ductility, while high temperature increases it. When a part is overloaded at low temperatures, a brittle fracture is more likely to occur. At high temperatures, a more ductile fracture is likely to occur.
Lower strength steel (less carbon and alloys) maintains ductility (toughness) as temperature decreases. When steel strength increases (more carbon and alloys), ductility drops more quickly as temperature decreases.
The dominant factor causing brittle metals to become more ductile is high temperature.
The steels in the Charpy impact test chart (Figure 2) show this change.

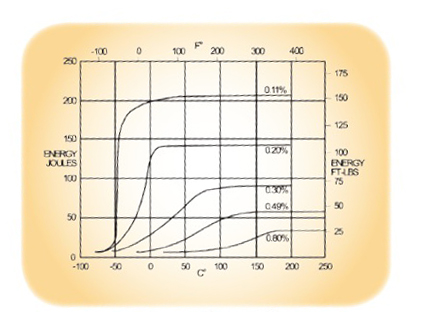
Figure 2: Charpy Impact Test Chart
Higher strength steels with carbon above 0.30% begin to lose ductility (toughness) below room temperature. Low carbon steels (0.20% carbon or less) do not begin to lose ductility until temperatures reach freezing (32°F).
There are exceptions to this relationship. Stainless steels maintain their toughness at low temperatures. However, stainless steels may become work hardened and also lose ductility.
Rate of Loading
When an overload happens slowly, there is enough time for microscopic movements in the metal to occur. The metal deforms plastically before finally breaking. Sudden impact frequently causes a ductile material to behave in a brittle manner. There is not enough time for microscopic movements to take place. Brittle behavior is often seen in a catastrophic failure when the overload is very sudden.
Stress Concentrations
Changes in geometry, such as keyways, diameter changes, notches, grooves, holes and corrosion, result in localized areas where the stress is much higher than in the adjacent region of a part.
In regions where there is no stress concentration, it is easier for microscopic movements to occur. In this case, the metal behaves in a ductile manner. A stress concentration does not allow microscopic movements, so brittle fracture is more likely.
Size
Thin parts are more likely to fail in a ductile manner when overloaded. Large or thicker parts will behave more like a brittle metal when overloaded because the geometry does not allow stress to be evenly distributed. Figure 3 shows the effect of size.
Figure 3: Ductile metals behaving more like a brittle metal
Thin parts will usually have a shear lip or fracture at an angle; this is characteristic of a ductile fracture. The shear lip becomes smaller as thickness increases and the fracture becomes more brittle.
Interactions
Figure 4 summarizes the factors that may be present in an overload failure.
Figure 4: Summary of factors affecting overload fractures
These frequently occur in many combinations and are subject to many complications in specific applications. If they are recognized as trends, they will help guide the analysis.
For example: If a ductile part has severe stress concentrations from corrosion or improper machining and receives an impact, the resulting fracture will have features of a brittle fracture.
The following examples illustrate the importance and interplay of these factors.
Brittle fracture of a ductile material
The roll journal in Figure 5 is made from annealed 4140 steel.
Figure 5: A brittle fracture of a journal. A piece was cut out for metallurgical analysis.
Its hardness was about 190 BHN and elongation 26%, characteristic of a more ductile metal. The journal fractured as a fully loaded roll was set into stands using a crane. The brittle fracture happened because three factors were present:
Stress concentrations - severe
- The journal had been repaired; the diameter was decreased and a radius cut at the location of the failure.
- A fatigue crack started in the radius, further increasing the stress concentration.
Rate of loading - high
- When the journal failed, the roll was being lowered into stands.
Size - large
- The diameter of the journal was 4 inches.
Remedy
- Reduce the stress concentrations by correctly machining and repairing the journal.
Failure of high strength plate at low temperature
High strength plate was substituted for mild steel in a conveyor transfer point. This was done because the mild steel plate was bent by repeated impact of large material pieces hitting it. As winter approached and the temperature dropped, the high strength plate began to fracture. It had to be replaced in the middle of winter.
Strength - high
- High strength steel was substituted for the ductile low strength mild steel.
Temperature - low
- The ability of the high strength steel to absorb energy (ductile to brittle transition) decreased very rapidly as the temperature fell.
Remedy
- Use thicker mild steel that maintains ductility at low temperature.
Sudden overload
The hoist chain in Figure 6 failed in two places. The fracture on the top of Figure 6 is a fatigue fracture caused by repeated loading.
Figure 6: Broken link from a hoist chain
The brittle fracture at the bottom of the link in Figure 6 occurred immediately after the fatigue fracture occurred.
The link deformed, indicating it was moderately ductile (344 BHN). The suddenly increased load on the remaining side resulted in the brittle fracture. The chevron marks of the brittle fracture are visible in Figure 7.
Figure 7: Brittle fracture face
Strength - high
- The chain was case hardened with a softer core. Tensile strength was approximately 160,000 psi.
Rate of loading - high
- When the first fracture occurred, the entire load was instantaneously transferred to the remaining side.
Remedy
- Periodically inspect chain for damage caused by improper use or maintenance
Take all the factors into consideration that may influence an overload fracture. An incorrect diagnosis can be hazardous and expensive for all concerned. When looking at a ductile or brittle overload fracture, remember there is frequently more than meets the eye.