Just what is the right oil type and why? What is the best way to properly store oil, and the preferred distribution methods to get it from storage to the equipment? Are all filters and breathers created equal? What are the advantages and disadvantages of different styles and types of filters and breathers? How about the importance of correct oil levels, both high and low, and just what is the proper level in all these different types of sight glasses? Why do we do oil analysis, what should we test for, what can be gained from the tests and how can you get the most from the information of your tests. Finally, how do you do Condition Based Maintenance based on your oil analysis?
With the ever increasing costs of lubrication products, why not get the most out of them? Do you really need to change that oil every six months? Just because it’s been done that way for years, or the OEM manual that hasn’t been updated in twenty years says to do it that way, does it really need to be done? Hopefully, the next few pages will provide you with some information about how to get the most bang for your buck, while helping to preserve a valuable resource and reduce disposal and waste. Why not start something that will help reduce your operating costs, while increasing the reliability of your equipment? In a perfect world, this would be an easy task to accomplish. In the real world, there are constant bumps in the road, curve balls, and hiccups to contend with.
Lubricant Types
Well, unfortunately, a lot of people would be content to say that oil is oil. (Hopefully, not anyone who reads this magazine though.) Actually, there are a host of variables to consider when choosing a lubricant. Let’s start off by briefly discussing some of the different types of base stocks used for lubricants.
GROUP I – These are your solvent refined mineral based lubricants. People figured out pretty quickly that crude oil from the ground left a lot to be desired if it were to be used as a lubricant for equipment and engines. The solvent refining method removed some of the impurities from the crude which made it better.
GROUP II – This process utilizes hydro-cracking of the molecular structure on mineral oils to remove impurities and other undesirables from the crude oil. Group II base stock has become the main stay for lubricants in today’s market.
GROUP III – These are still a mineral oil, but are considered a synthetic due to the severe hydro-cracking and processing the crude oil undergoes. These were deemed a synthetic through a law suit between Mobil and Castrol, in which the courts decided that since the mineral oil was so severely processed, the original molecular structure was no longer anything like its original structure. Therefore, it could be called a synthetic. While these are better than group II oils in most respects, they still lack some qualities of a true synthetic lubricant.
GROUP IV OR SYNTHETIC – Polyalphaolephins (PAO), Organic Esters, Phosphate Esters (Fire Resistant), Polyglycols and Polyolesters are the common types of synthetic oils. PAO’s are the most commonly used base stock, while each of the others have very specific applications in which they work best.
Oil is not just oil. In Figure 1, we can clearly see that not all oils are created equal. They have different specific gravities, additive packages, base stocks, and thus, different purposes and uses. The other old adage, “something is better than nothing” is not always true either. Using the wrong oil or mixing incompatible oils can cause as many, if not more, problems than running an incorrect oil level. This difference in oil types clearly demonstrates why there is no ‘one size fits all’ scenario, and, thus, the importance of specifying the correct oil for a particular piece of equipment.

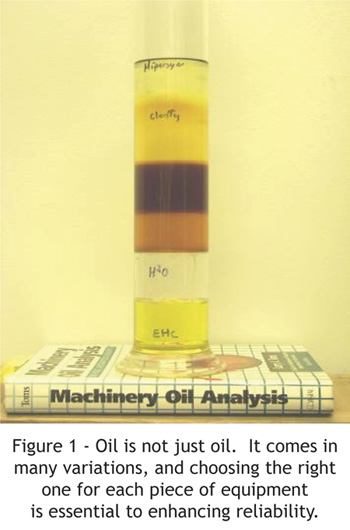
Finished lubricants consist mainly of a base stock, with some additives to extend the life of the base stock and enhance it for specific applications. Turbine oils generally have the least additives (about one percent); while automotive oils usually contain the highest amounts of additives (around thirty percent). Typical additives consist of: antioxidants, corrosion and rust inhibitors, detergents and dispersants, anti-wear and extreme pressure agents, viscosity index improvers, pour point depressants, defoamers, demulsifiers, and friction modifiers. Each of these additives has a specific purpose in the finished product. They enhance the base stock for a specific application of that lubricant in a piece of equipment. Almost all oils have a rust and oxidation inhibitor at a minimum, to help preserve the base stock.
Now that we know oil is not just oil, and that there are many different types of oils with specific properties for specific applications, let’s discuss some of the preferred storage and distribution methods.
Storage and Handling
Oil comes in many different sized containers, from quarts, drums, totes, and bulk tankers. When manufactured, most oil is clean. However during handling, shipping, and storage is where we develop most of our problems. All oil should be tested for acceptance before placing it into your system for use. This is especially true with bulk shipments, as you can’t always be assured what was in the tanker before your load of oil. Drums and smaller containers are not as critical to be tested before use, but random testing should be performed to have a baseline for comparison with your in-use products. Lubricant formulators will change additive packages in products without notice, which can leave you wondering about a possible problem seen in your oil analysis that might only be a formulation change in the product.
Bulk storage tanks need to have breathers and secured hatches to reduce ingress of moisture and debris. If it is a large volume of oil located outside, a dry air head space or nitrogen blanket might be helpful to keep the water levels down in your new oil. Totes should be stored out of the weather if possible, or at least under a roof with all openings closed and a desiccant type breather installed rather than a loose plug or fitting to allow air to come in as the product is drawn out.
With drums, they should be stored inside if possible, even though this usually isn’t done. The preferred method of storing a drum is on its side (horizontal) with the bungs located at the three and nine o-clock position. Figure 2 illustrates this method of storage. This method reduces the amount of ingress through the bungs as the drum breaths due to temperature changes. If a drum is left standing, this allows not only air but any water that might be on top of the drum to be pulled into the drum, through the bungs, as it cools. Occasionally, a bung might leak slightly when stored on its side, so you pull the seal and tighten it to stop the leak. Even if a drum is stored inside, the preferred method is still on its side if it will be stored for any length of time. This reduces the amount of air exchange that will accelerate the oxidation of the lubricant. If you can’t store drums on their side, then preferably they should have rain caps on them or be tilted so bungs are not located to the bottom of the tilt. This will allow any water to run off the drum top without the chance of it being sucked through the bung into the drum as temperature changes. Also, since we never know when it might rain, when the drums are sent out for use, rain caps are a good idea.
For small volumes of oil, there are several products to get the oil from the storage area to the equipment. (See Figure 3 for some examples.) Safety cans have been around for a long time and provide a positive closing lid or cap, but usually require a funnel to get the product into the equipment. The newer versions have larger openings, positive closures, pump versions, long and short spouts, flexible spouts, and labeling systems. One draw back is they are only available up to two gallons in size. Of this newer style, Oil Safe products were first on the market, with others following such as the I-can and Lube Rite.
Funnels are great tools and a necessity to get a product to the specified place. Unless they were properly stored in a plastic bag, steel or plastic funnels usually sit around waiting to be used, doing what they do best, collecting dust and dirt. There are disposable paper and cardboard funnels available from various manufacturers that eliminate the storage and cleaning issue of hard funnels.
Since most stored and handled lubricants are not up to equipment target ISO code specifications, we need to filter them before installing them. There are many different types of filter carts and filter systems to accomplish this task. Figure 4 shows a lube oil room setup with air pumps and filters in line with the metering heads.
The oil can be transferred from the drum into smaller containers for top ups and smaller quantity needs. For larger volume needs, filter carts or drum filter carts can be used to pump the product from the drum or tote into the equipment. It is much easier and less expensive to clean the new oil as it is installed, rather than try to clean it once it is in the equipment.
Filtration and Breathers
The main function of a filter is to remove ingressed or generated debris from a lubrication system. Very careful consideration should go into the original selection of a filter for a piece of equipment; based on micron size, BETA rating, flow rate, and operating pressure, just to list a few. A lot of newer equipment is coming equipped with side stream or kidney loop filtration rather than full flow filters. They provide valuable benefits with smaller micron sizes and, thus, better filtration, without the worry of flow restrictions. There are many aftermarket filters available on the market today. Always consult a reputable source if changing from an OEM filter or filtration system to assure you are getting an equivalent filter. Don’t leave it to the purchasing department to go with the cheapest element available, as this could cause serious detrimental effects to the equipment.
Filter carts can provide excellent filtration without disrupting the operating system. These too, must be properly chosen for the fluid viscosity, flow rate, and micron rating. Otherwise the filter will just be running in bypass, and not really accomplishing much. Most filter carts are designed for lower viscosity fluids (i.e. hydraulic oils). There are a few on the market that are designed to handle high viscosity fluids (i.e. gear lubes). These generally have a lower flow rate and larger or more filters to increase the surface area to reduce flow restriction. So, when choosing a filter cart, be sure to explain what you will be filtering so you can get the proper unit for your needs.
Breathers play an essential part in helping to reduce ingress into reservoirs. Older systems merely had snorkel pipes or screen mesh caps that worked fine to keep large particles and bugs out of the fluid. Modern breathers are rated for two to three micron particulates and usually have some form of moisture removal. There are still several OEM fill caps and breathers that only utilize a fiber mesh to catch the larger stuff. (Although, sometimes this is because of the air exchange rate required for the reservoir.)
As with filters, if you choose to upgrade to a better breather type, do your homework first to establish the air exchange rate in the reservoir or damage and system malfunctions can occur. On an average, a disposable desiccant type breather can handle about 15 CFM. By using a manifold, these breathers can be grouped together to handle higher air flows. There are also either larger metal-type breathers that have replaceable desiccant, or breathers with regenerative moisture removal crystals that can handle much higher air flows (up to 45 CFM), that can be used.
Sight Glasses and Correct Oil Levels
There are many types of sight glasses. Figure 5 shows three, from the round bulls-eye (left), tube type (middle) and bolt on tank type (right). The main purpose of these is to allow a quick easy check on fluid level in a reservoir. They can also provide a window into the condition of the fluid by observing the color of the fluid in the glass.
In a bulls-eye type glass, the half to three quarters level is considered the correct level. In most oiled electric motors, the slinger ring, which carries the oil from the reservoir to the top of the shaft for bearing lubrication, is usually less than one inch below the bottom of the sight glass; so, this doesn’t leave much room for error for a low level. A high oil level can allow the shaft to churn the oil causing aeration which can reduce the correct oil film between the shaft and bearing. A high oil level can also create leaks which can get into the motor windings and cause extensive problems.
On a stick or tube type sight glass, the middle third is considered the correct level. These are sometimes used on gear reducers to replace an oil level plug for ease of checking the level. When this is done, the sight glass must be installed below the level plug so the correct oil level is represented in the sight glass. If the sight glass is placed in the oil level plug hole, this will cause the gear reducer to be overfilled causing loss of efficiency, aeration, leaks, and excessive heat generation.
The bolt on tank type of sight glass is generally used for reservoirs. These usually have a generic high and low mark on them which might be incorrect for the proper level. In one case of an aeration problem, it was found that when the oil level was in the middle of the sight glass, the fluid was less than a half inch above the suction strainer, thus the cause of aeration. The correct level was marked on the tank beside the sight glass and problem solved.
There are several constant level lubricators, of which the Trico Optimatic (Figure 6) and Watchdog oilers are probably the most common types. The Optimatic does not have a sight glass as such, but as long as it has oil in the bulb there should be oil in the equipment. One of the more critical parts of the Optimatic is the adjustment assembly, which supports the oil bulb. Care must be taken to set this adjustment assembly properly as this establishes the oil level in the equipment. If this adjustment assembly is left out or incorrectly set, this will cause an incorrect level to the bearing, which can cause failure.
The Watchdog oiler installs in the bulls-eye type sight glass location. These require no adjustment since they work off an angle tube, which establishes the oil level in the center of the sight glass. These need to be correctly sized and not used with a reducer bushing which can cause a false level indication.
Oil Analysis Sampling
Oil analysis not only monitors the health or condition of the oil, it also monitors machine wear and contamination levels. The sampling process is probably one of the most important parts of a good oil analysis program. If you don’t get a true representative sample of the lubricant from an in-service piece of equipment, you are limiting your available data. One of the best samples is a live sample from a supply line upstream of the filter, located in a turbulent area of the piping (Figure 7). This can be accomplished with the use of a sample fitting, a number of which are available from several companies such as; Donaldson, Trico, Minimess, and Checkfluid to mention a few. These can be used in static as well as pressurized locations. Once again, do your home work to be sure you get a properly suited fitting for the viscosity and pressure of the system. A lot of new equipment is coming equipped with sample fittings, or if you have any input into specifying new equipment, request a sample fitting in the spec.
Where a pressurized sample is not available, sample fittings are still a preferred method for a consistent sample point. These can be obtained with a drop tube, through a reservoir wall or level check plugs (Figure 8). An additional item you will need for static sampling is a vacuum pump to withdraw or suck the oil into the sample bottle. Never get a sample from a drain line (unless you want a bottom sample to see what type of sediment you have), as these are not truly representative of the fluid in circulation. Sample fittings are also a significant time saver in the sampling process, reducing route time by half or more on average. They can also be labeled with the equipment ID or sample information to avoid confusion during the collection process.
Sensory and In-House Oil Analysis
Now that we have a good representative sample what do we do with it? Some larger facilities have the luxury of having an on-site oil lab to do the analysis. There are some self contained mini labs that test for specific things in the oil such as; viscosity, dielectric strength, and particle counts. These can provide a good idea of lubricant and machine condition. And, of course, there are off-site professional oil analysis laboratories that can perform many specific tests for lubricants.
The first line of defense is sensory analysis; color, look, and smell, go a long way during the collection process. This is where training and a well trained, dedicated person are invaluable. Many problems with the oil or the equipment can be spotted before the sample is ever formally analyzed. Even with sensory analysis the samples should be sent to the lab for formal analysis for data and trending purposes. A good example of sensory analysis that wouldn’t be caught by the lab would be air entrainment. This would be obvious in the sample when it was collected. However, the air would release before the lab ever got the sample. The lab may report an increase in oxidation, but this would be minimal compared to the visible air in the sample at time of collection. If you don’t have the option of an on-site lab, there are a few tests that are inexpensive, easy to do, and provide invaluable immediate information that can save a costly repair.
Water can be very damaging to most equipment. A well trained technician can usually spot water with sensory analysis; however the crackle test (Figure 9) is an inexpensive way to provide a definite answer. The test utilizes a hot plate heated to 300°F, and generally provides positive results for water above 1,000 ppm. Put a few drops of oil on the hot plate, and if it splatters and bubbles, you most likely are above 1,000 ppm water. If it looks like a volcano erupting you have some serious problems. This can also be done with a spoon or piece of tin foil and a lighter; anything to boil the water out of the oil. There are also several commercial test instruments available for use in the field that can provide exact data or just a positive for water results.
A patch test kit (Figure 10) allows you to pull a sample of oil through a selection of membrane filter patches, which have different ratings from 0.5 microns to 5 microns for general use. While these can be used for quantitative particle counts, I find them more useful for debris analysis. There are many charts that provide information on what different particles of metal, dirt, silica, etc look like when magnified for you to compare to; as well as comparative patches for ISO code reference. When doing debris analysis it is very helpful to know what type of metals the equipment is made of, and what type of airborne particles might be ingressed.
Since viscosity is considered the most important property of a lubricant, an instrument to measure viscosity is a must have. There are many of these available from sophisticated to the simplistic visgage (Figure 11).
There is one last simple in house test that will make you wonder about its use. It involves a blender and a stop watch. Now don’t laugh, it’s a good test. With the simple version of this test you are doing a comparison between new oil and the in-service oil in question. The blender can be used for air release and demulsibility testing for quick results.
As with any in house test, repeatability is your safeguard to good results and a sample should still be sent to the lab for formal testing.
Oil Analysis Laboratory Tests
There are many different tests available for formal oil analysis. Several of these should be performed for all samples such as viscosity, spectral, water, FTIR (Fourier Transform Infrared Spectroscopy), and particle count. Other tests, such as acid number (AN) and base number (BN), are performed depending on the equipment. Tests that are usually completed on an as needed basis are analytical ferrography, demulsability, air release, RVPOT (rotating vessel pressure oxidation test) and some newly designed tests for varnish potential such as the Ruler and the MPC (still under development by the ASTM D02.C committee). Below we will discuss briefly the above listed tests.
Viscosity: A measure of oils resistance to flow
Spectrographic Analysis: A comprehensive lube oil analysis which measures elemental concentrations in the sample such as, wear metals, additives, and contaminants. Common methods are; Atomic Emission, Atomic Absorption, X-ray Fluorescence.
Water Content: Determines the percent of water content.
FTIR: Determines by infrared light absorption the amount of soot, sulfates, oxidation, nitro-oxidation, glycol, fuel, and water present in the sample.
Particle Count: The number of particles per milliliter of fluid normally stated in ppm and reported in a ISO code of >4 µm, >6 µm, and >14 µm
Acid Number (AN): Determines the level of acidity.
Base Numbers (BN): Determines the oil’s acid resistance.
Analytical Ferrography: A microscopic inspection of the size, shape, and origin of the wear metal and contaminant particles for oil and grease.
Demulsability: The ability of oil to separate from water.
Air Release: The ability for entrained air to release from oil.
RPVOT: Determines the useful life of the anti-oxidant in the lubricant. New oil minutes versus used oil minutes.
RULER: Plots aromatic amines and hindered phenol antioxidants against a new oil or base line reference sample to determine a relative concentration. Used to determine useful life left in a lubricant.
MPC: Measures the amount of soft contaminants in a lubricant. This is performed by a color comparison of membrane patches. (This test is still under development by the ASTM D02.C committee) A method for determining varnish potential in a lubricant.
There are numerous other tests available to identify specific problems you may be experiencing. These tests can either be looked up by ASTM method listing, or discuss them with your lab to decide which is the right one to use.
Condition Based Maintenance
The goal of CBM (condition based maintenance) is to fully utilize the information from your oil analysis and other predictive maintenance technologies. When properly performed, it can be viewed as both proactive and reactive. It is proactive when the routine data is used to defer normally scheduled PM’s for equipment maintenance or a lubrication change, based on the fact that everything is OK and doesn’t need any work at that time. It becomes reactive when the routine data indicates an upcoming problem, but this data allows you to schedule the maintenance for a time of least economic impact or avoid a catastrophic failure.
There are many advantages to the use of CBM such as, cost savings, deferring normally scheduled or frequency based service, reducing the human intervention factor on good running equipment, a reduction on our natural resources, and disposal problems and their associated costs. There are very few things today that can save the kind of money that a properly utilized CBM program can. Just on deferred oil changes alone for the equipment monitored at our plant we save over $150,000 per year. This figure is based on seven times the cost of new oil per gallon to include the associated costs of receiving, handling, changing and disposal. If you could easily track the other costs not incurred by doing almost nothing, that figure would be significantly more.
Conclusion
Hopefully through this rapid overview of the many topics discussed, you have learned some of the many opportunities available from a properly managed lubrication program. Over the past few years the importance of lubrication has taken the main stage instead of the minor role it once played as ‘just a disposable commodity’. There are many resources available to help guide you along your journey to not only a successful lubrication program, but the financial rewards, and increased equipment reliability that can come from it.
So what are you waiting for, start your reliability journey through lubrication today.
References
Machinery Oil Analysis - second edition, Larry A. Toms
Handbook of Lubrication and Tribology – second edition, edited by, George E. Totten
Sponsored by the Society of Tribologists and Lubrication Engineers
Brian Thorp has been involved with mechanics and maintenance for over 30 years. His range of knowledge includes automobiles, trucks, heavy equipment, and power plants. In his earlier years, he received extensive training in engines, transmissions, gear trains, hydraulics and pneumatics. His current position is as a Predictive Maintenance Technician with Seminole Electric Cooperative Inc, where he is responsible for the lubrication and analysis for a combined total 1300 MW coal fired power generation plant. His current certifications include, CLS, MLT II, Level I Infrared Thermographer, Level I Vibration Analyst, Level I Certified Airborne Ultrasound Inspector and he previously attained STLE, OMA I. He has also attended numerous seminars on root cause failure analysis, failure analysis and laser alignment. He has made several presentations, and authored several articles, related to lubrication, predictive maintenance, and reliability
issues.