I worked directly with a large pharmaceutical company to identify the root cause of issues with critical rotating pumping equipment. We used data from the CMMS to run a top ten bad actors report and identified many issues with failed couplings and motors. We calculated that the issue stemmed from poor alignment practices, so we launched a new laser alignment program.
Our first step in the launch was to provide a training seminar on the benefits of precision laser alignment technology. The first telltale sign that we were going to have an issue with the culture was when only the younger, less seasoned mechanics attended the training, while the most senior mechanics used the excuse they were busy with emergency repairs, indicating we were getting resistance to change from the senior mechanics. The new laser alignment equipment was ordered and received a few weeks later. We provided hands-on training, but over the next few months, we noticed the laser equipment was being used infrequently and only by the younger mechanics.
We then approached the senior mechanics and asked why they were not using the laser equipment. They said they didn’t need the new laser equipment because they could perform the alignment better with the old rim and face method using dials. This rim and face method they were using was still producing failures on the critical rotating equipment after a short period of time after repairs. We decided to offer the three senior mechanics a challenge – if we can prove that using the laser alignment equipment would be quicker and provide additional precision, then the mechanics would need to use the laser equipment moving forward. If not, they could continue to use the rim and face method and we would have to buy them lunch.
With the stage set, we let the senior mechanics perform the rim and face method on a selected critical pump. Once they were complete with their alignment, they documented the as-left results. Next, one of the younger mechanics used the new laser alignment equipment to align the same pump. He proceeded to baseline the new as-found readings and then performed the alignment using the laser equipment.
The results showed the younger mechanic was able to perform the alignment faster and then print out the final report showing the as-found and as-left readings. The readings were then reviewed by all the mechanics and the senior mechanics said they were truly amazed with the results of the final precision alignment. From that point on, the entire team was sold on using the laser equipment. To celebrate the success, I did buy the entire team lunch to mark the launch of this new technology.
The overall takeaway was resistance to change, which is often seen among older people who are set in their ways and often fearful of replacement. Younger people, on the other hand, tend to roll with change with greater comfort and are very technology savvy. The key findings are to never underestimate the work culture, ensure they understand the benefits of the new process, and make certain that everyone is fully engaged with the new process.


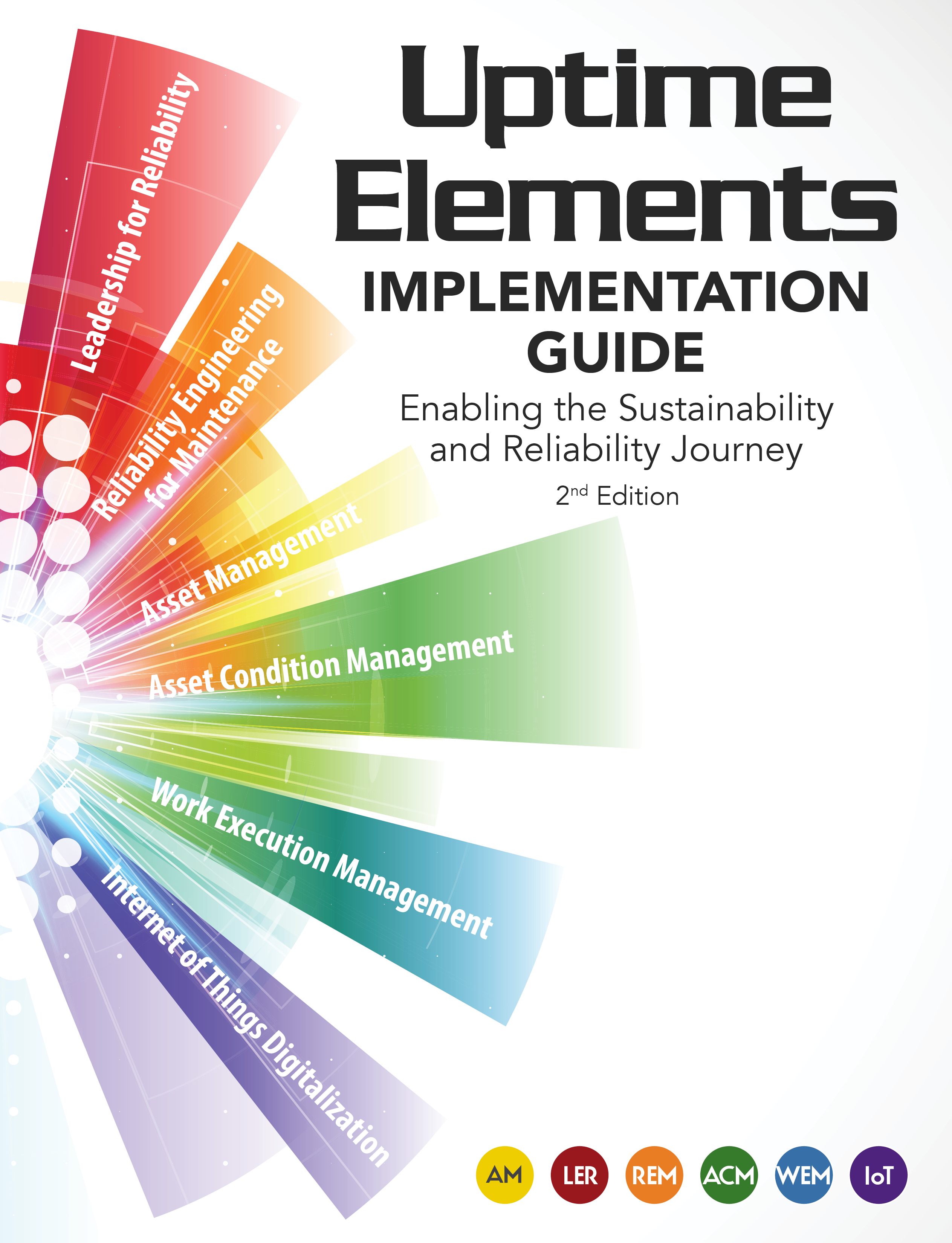
This Tales from the shop article, written by Eric Newhard, was originally published in our Uptime Element Implementation Guide