
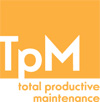
"It should be noted that although human factors such as leadership, motivation and culture are largely outside the scope of this Publicly Available Specification, they are critical to the successful achievement of asset management and require due consideration. This is applicable to the organisations' managers, employees, contractors and suppliers."
References to the "the human Factors" - Section 0.1 what is asset management? Para 8:-
1.2
For a company to be successful in Asset Management; - "It requires processes that are driven effectively by top management and supported by empowered and competent employees......
A key characteristic of successful asset management is consistently making sound decisions and good compromises, and carrying out the appropriate tasks at the right time and at the optimum level of expenditure. Above all it requires the commitment of top management, and it is unlikely that an organisation will successfully integrate and optimise their asset management without such commitment. It also requires a motivated workforce supported by an effective asset management system, adequate and appropriate information and only thereafter, the usage of various asset management tools.
For some organisations this may require a change in culture and it might challenge existing ways of thinking and working."
PAS 55 Part 2 References to "culture", "commitment" and "leadership" Section 0.1 General
The benefits of using Total Productive Maintenance techniques is well understood and is often seen as one of the tools capable of delivering an empowered and motivated workforce. These simple but effective techniques get the involvement of those very important people, who operate the key human interface with the asset. A TPM 1-point lesson is just one of the many tools that can be used to improve knowledge and understanding of the condition and performance of an asset on a day-to-day basis. The approach engages the front-line operations and technicians and encourages them to get involved in the continuous improvement of the asset. By simply passing on good ideas, maintenance interventions can be optimised to ensure there maximum impact on either the performance or condition of the assets.
2. What is a TPM 1-point lesson?
2.1 A 1-point lesson:
• Communicates knowledge and skill about the asset amongst members of the team.
• Raises the knowledge and skills of the team in a very short period of time.
• Is used for eliminating problems and for making improvements to the way of working.
• Makes sure that everyone knows about a better way of doing something.
• Makes sure that next time a problem is encountered everyone knows the way to solve it.
2.2 How is it generated?
• One member of the team prepares a sheet, which describes the problem and solution in simple language. It is often illustrated with pictures if possible.
• The team discuss the 1-point lesson, formally or informally, and incorporate any ideas.
• The 1-point lesson is approved by the line management to ensure it is appropriate and safe.
• The 1-point lesson is then published and read by all members of all shift teams.
• Individuals are then asked to sign to acknowledge that they have read the 1-point lesson.
Remember there is always an emphasis on "SAFETY"
2.3 Keys to a successful 1-point lesson
• Treat only one piece of knowledge at a time. The TPM approach is about small incremental steps to continuous improvement.
• Use simple clear language.
• Illustrate the idea with pictures or drawings.
• Make the 1-point lesson available to everyone.
• Recognise and reward those who share their knowledge.
2.4 Here are some simple examples
• Match marks painted on bolts and fittings.
• Improved procedures for size change.
• Procedures for efficient recovery from a machine stoppage.
• Instructions for the repair of a breakdown.
• Point out the optimum settings for a machine or process.
3. What should the TPM 1-point lesson contain?
The following sections: -
1. Before and after sections (the use of photographs or diagrams is encouraged)
2. Plant description
3. Plant location
4. A description of the situation or the solution
5. Who prepared the document?
6. Who approved the document?
7. Date of introduction
8. That the 1-point lesson is easily understood.
9. A suitable system embedded within it to ensure compliance and acceptance.
Keith Rimmer, a senior consultant at TWPL has a wealth of experience in reliability, maintenance and asset management gained within Royal Mail, rail and brewing industries. With a strong engineering/technical background, he has more recently specialized in the management of change, mentoring programmes and workforce culture development. Within Royal Mail he was a leading member of the Total Quality Management team, which introduced the concepts of TQM and TPM across the company, including winning the European Business Excellence award. He also helped to develop an on-line training programme for Interbrew's 65 maintenance engineering and management sites worldwide. He also led projects to launch the first ever public BTEC qualifications (levels 3 and 4) for technicians/operators and managers called ‘Asset Care & Renewal'. More recently Keith has been working with Enbridge Gas Distribution in Toronto, Canada and CLP Power, Hong Kong, where he is responsible for implementing interactive assessment programmes and implementing strategic improvement roadmaps.
Download a TPM One Point Lesson Template (PDF) Below