How Do Continuous Improvement Management Philosophies Relate to the Maintenance Function?
PDCA (Plan, Do, Check, Act cycle)
The Plan Do Check Act cycle is the basis of many management philosophies and was a model conceived by Walter Shewhart in the 1930s and then promoted by W. Edwards Deming in the 1950's. It was originally applied to business processes but can be used to implement continuous improvement in almost any process. In relation to maintenance engineering it can be applied to improving maintenance systems, equipment reliability, equipment design, work practices, employee capability, safety and environmental issues related to maintenance practices. The six sigmaspc Website (2006) refers to this cycle as "work smarter not harder".
The Stages of PDCA
Plan.
To plan is to develop a method or process. In a manufacturing environment the planning process may be to decide on what problem needs resolving or process needs improving. The main criteria for deciding what this model should be applied too, is that there should be a significant improvement gained from implementing the plan. The plan should define activities and expected improvement outcomes.
Do.
To do is to execute or complete. The ideas and methods or processes in the plan must now be put into place. This may include changes to production processes, maintenance strategies, implementing training or changing work practices.
Check.
To check is to examine the accuracy of. If a plan does not deliver a significant outcome, the effort is wasted. Data such as production output, machine availability and safety statistics must be measured against the projected outcomes detailed in the plan.
Act.
After reviewing the data in the "Check" process. A decision must be made to Act by either:
1.Dropping the activity, as there are no gains to be made.
2.Modify the plan to improve the outcome. (Go back to the "Plan" stage.)
3.Look to improve the outcomes further.
This leads us back into the planning stage. We should ask the question. What's next?
TPS. The Toyota Production system.
In 2004 Toyota was the third largest Automobile manufacturer in the world and by far the most profitable (Liker. J.K., 2004). Toyota is extremely successful due to their company philosophy, which is now known as the Toyota Production System. The TPS became the basis for the LEAN and Six Sigma manufacturing philosophies that have been prevalent in industry since the early 90's. The TPS includes 14 management principles that can be correlated into four principal Categories of Philosophy, Process, People and Partners and Problem solving (Fig 1). The TPS philosophy on Assets is "Use only reliable, thoroughly tested technology that serves your people and processes"(Liker. J.K. 2004). Toyota builds reliability into its equipment as the "one piece flow" arrangements depend on this reliability and the application of rigorous standards being applied to all areas of maintenance management. The overall effect of the TPS on maintenance is that it drives the pursuit of "best practice".
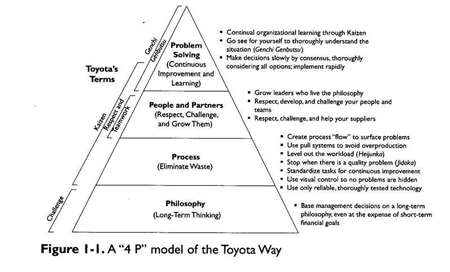
LEAN Manufacturing.
Lean is a philosophy that is based around the reduction of waste in all aspects of a business, including customer relationships, product design, supplier networks, production flow, maintenance, engineering, quality assurance and factory management. The term "Lean" came as a result of a research group led by James.P Womack that had set about analysing and defining the Toyota Production system in the 80's (Smith & Hawkins 2004). Although the major theme of Lean is the reduction of waste, it includes a package of manufacturing philosophies and tools as depicted in Fig 2. The key to success of a Lean implementation is to provide an infrastructure for Kaizen or "Continuous improvement".
Fig 2.Lean Tools.
Lean and the Maintenance function.
Five of the key guiding principles of Lean are:
•Challenge. Don't accept waste, encourage innovative ideas, remove the "if it's not broken don't fix it" mentality, reduce the fear of asking dumb questions.
•Go and See. (Genchi Genbutsu) If there is an issue YOU go and look at it, don't just talk about it. Assess what you see against Lean principles. Go with the team to review areas of concern.
•Continuous improvement. (Kaisen) Encourage simple cheap improvements, reward individuals who develop continuous improvement ideas.
•Respect the operator. Each individual has a role to play, respect it. Remove the emotion by using the facts. Use a situational leadership approach.
•Teamwork. Understand individual's strengths and weaknesses, train your team, work together on projects, and create Pride in the team.
The Lean Manufacturing seven categories of waste (WORMPIT)
Bruce Hawkins (2005) highlights how the seven categories of waste can be associated with the maintenance function, and that "Lean Maintenance" can be achieved by addressing the following:
•Waiting. This can be waiting for a job to be handed out, waiting for production to stop the machine, waiting at the store for parts. Waiting generally occurs because of poor planning.
•Over Production in maintenance refers to doing unnecessary work, and is related to incorrect maintenance strategies or poor work management.
•Repair/ Rework/ Rejects generally occurs because of poor workmanship, lack of training or incorrect procedures.
•Motion losses can be generated by poor workshop or stores setup. This can lead to significantly more movements being required to complete a task.
•Processing waste can occur when maintenance systems and processors are inefficient by having unrequired steps or duplication inbuilt.
•Inventory waste occurs with the development of "Squirrel" stores, incorrect master data in the materials management system and the inability to identify obsolete parts, which continue to be stored.
•Transportation waste is related to the time it takes to travel to a job.
Generally there will be many areas in all workplaces where waste is evident. Within the maintenance function the following actions are recommended:
•Remove non-value adding inspections from the PM system and improve the detail in value adding tasks.
•Move to on-line condition based maintenance wherever possible.
•Have a clearly documented and understood Work Flow System.
•Clean up workshops and ensure tools and equipment have nominated storage areas.
Generally, Lean processes will have a positive effect on the maintenance function, but initially the introduction of the 7-day, 5-why problem solving process (Kaizen) may put maintenance into a very reactive mode. To counteract this workflow procedures must be documented and continue to be followed during the Lean implementation.
KAIZEN.
Kaizen is a philosophy that promotes continuous gradual improvements and translated from Japanese means "change to become good." Kaizen is a philosophy on its own but is included as an important factor within the Lean production system. The 5 foundation elements of Kaizen are:
1.Teamwork
2.Personal discipline
3.Improved morale
4.Quality Circles
5.Suggestions for improvement.(Value Based Management.net 2008. pg 1 of 1)
Much of Kaizen is related to changing the culture of an organisation by encouraging employees to be willingly involved in improvement processes.
If Kaizen was effectively applied to the Maintenance strategy review process, you would see all team members voluntarily feeding improvements back into maintenance task lists at regular intervals, E.g. The quality of job instructions and estimated hours to complete tasks.
80/20 rule (Pareto Principle).
The 80/20 rule, sometimes known as the Pareto principle is a philosophy that highlights that some things are more important than others (Latino and Latino, 2006). The rule can be considered both an operating philosophy as well as a prioritisation tool. In relation to maintenance, an example of the rule could state: "80% of plant downtime applies to 20% of the installed equipment". The significance of the 80/20 rule is that if the top 20% of losses can be identified and then eliminated improvements will be made in the shortest timeframe. Fig 3. is an example of how the 80/20 philosophy can be applied to maintenance delays. The top graph shows that Machine 9 is the one that suffers the most downtime. Assuming this is critical plant, this machine becomes the focus of the effort. At the next level down we will assume that the two biggest issues have to be handled by Operations so we focus on the 3.5% associated with Mechanical and Electrical issues. The third graph breaks down the downtime to actual problems, and in this instance the focus will be applied to Issue 1 and 2 as elimination of these issues will give the most significant improvement.
Applying the 80/20 philosophy to the maintenance function in this manner will lead you on the path of continuous improvement in reliability of your assets.
TQM. (Total Quality Management)
Total Quality Management is a management approach that encourages all employees to become involved in the continuous improvement of the production of goods and services, the aim being to have "No defects". The presumption is that a culture of continuous improvement will deliver a quality outcome that will satisfy the customer's needs.
TQM has eight key elements that are the building materials of the philosophy. The foundation of TQM is based on ethics, integrity and trust between all levels of the organisation. The Bricks laid on the foundations are training, teamwork and leadership that has an inspiring vision. Communication is the mortar that binds TQM together and the success of the philosophy is dependant on communication occurring effectively between all levels of the organisation. The roof of the structure is Recognition of all suggestions and achievements for teams and individuals. (Padhi, 2008., pg1of 1)
If TQM were applied to failure analysis processes employees at all levels would be interacting positively with a common goal of achieving the required understanding of chronic and sporadic losses, and then collectively coming to conclusions. Effective TQM would improve Teamwork, ownership and relationships between maintenance and other functions.
5 S.
The 5 S philosophy is aimed at organizing a workplace to create an environment that will achieve optimum output. Generally 5S is associated with housekeeping and shadow boards, but Smith and Mobley (2008) suggest that 5S can be applied to maintenance and reliability in the other ways.
•Sort. Sort all assets based on risk, so all effort can be focused in the correct area.
•Set in order. Have an excellent work management system that sets priorities based on criticality. Have appropriate asset strategies.
•Shine. Take pride in asset reliability. Be able to understand the health of an asset to repair it before it breaks.
•Standardize. Have as many standard tasks as practical.
•Sustain. Keep to standards and have a controlled change management process for these standards.
5-S is another integral part of the LEAN production system and applying this to maintenance will lead to more organised and hence productive maintenance workgroups.
TPM
Where TQM is based around zero defects, Total Productive Maintenance is based around having zero breakdowns and production losses, and is one of the foundation stones of the Lean production system as can be seen in Fig 2. TPM evolved from suppliers to Toyota in Japan so they could meet the demands of the TPS (Kennedy, 2006. Pg 5 of 15).
TPM is a philosophy that does not just focus on the "Maintenance Department" although maintenance does have a large part to play. TPM addresses all the reasons for equipment losses. Losses can be categorised into 6 categories:
1. Breakdowns. E.g. Circuit breaker trip.
2. Setup and adjustment. E.g. Re tooling for a different product.
3. Idling and minor stoppages. E.g. Problem with raw material.
4. Reduced speed losses. E.g. Speed reduced because of feed quality.
5. Quality defects and rework. E.g. Variation in output quality. Repairs not completed effectively.
6. Start-up losses. E.g. Cold starts, inefficient start-up procedures.
The aim of TPM is to eliminate or minimise the losses from all of these items. TPM as it was presented to the Onesteel Rod and Bar Mills as a base and pillar model as shown in Figure 4.
Consistent standards are the basis of the structure and the pillars that hold up TPM are:
1. Autonomous Maintenance. This means that everyone owns maintenance and that everyone has a role related to maintaining equipment.
2. Effective Training. The TPM training is to be focussed on plant operators so they can detect abnormalities in equipment before a breakdown occurs.
3. OEE. The Overall Equipment Effectiveness of a machine is equal to the %Runtime x %Yield x %Rate. OEE is the measurement of success of the TPM program.
4. The maintenance function must have a multi-functional workforce, effective and appropriate PM's, well-defined KPI's and an in built continuous improvement loop.
5. Early Equipment Management refers to ensuring equipment is fit for purpose before it is put in service. This includes making sound engineering decisions during the design process, ensuring the machine is operator friendly and understanding the preventitive maintenance requirements for the life of the equipment.
The TPM philosophy promotes training to understand potential breakdown causes, and the development of effective and efficient maintenance strategies that are continuously improved.
Fig 4 The Five Pillar model of TPM
In summary, virtually all continuous improvement philosophies and tools reviewed have some link back to the PLAN, DO, CHECK, ACT cycle, the Toyota Production system and hence LEAN manufacturing. Applying any of these philosophies to the maintenance function will have a positive effect if all stakeholders are involved in the deployment and effective Work Flow processes are maintained.
Article submitted by: Mark Brunner, CSAM
References.
Hawkins, B. 2005. "The many faces of Lean Maintenance".ProQuest database. Plant Engineering. Barrington:Sep 2005. Vol.59, Iss.9; pgs 63-65Kennedy, Ross. "Examining the Process of RCM and TPM. What do they ultimately achieve and are the two approaches compatible?" Jan 2006. http://www.plant-maintenance.com/articles/RCMVsTPM.pdf Viewed 8-3-2008.
Latino, R.J & Latino K.C. 2006, "Root Cause Analysis, Improving Performance for Bottom-Line Results" Third edition. CRC Press, Taylor and Frances Group, FL, USA.
Liker, J.K 2004, "The Toyota Way. 14 management principles from the worlds greatest manufacturer." McGraw-Hill publishing, New York.
Padhi, N, 2008 "The eight elements of TQM" http://isixsigma.com/library/content/c021230a.asp Viewed 13-5-2008.
Six Sigma SPC website. "PDCA- Plan Do Check Act". 2006.
http://www.sixsigmaspc.com/dictionary/PDCA-plan-do-check-act.html
Viewed 14-5-2008.
Smith, R & B Hawkins, B 2004, "Lean Maintenance, Reduce Costs, Improve Quality and Increase Market Share." Elsevier Butterworth-Heinemann, MA,USA.
Smith, R & Mobley, R .K 2008, " Rules of thumb for Maintenance and Reliability Engineers." Butterworth-Heinemann, MA, USA.
Value Based management.net, 2008 "Kaizen philosophy and Kaizen method" http://www.valuebasedmanagement.net/methods_kaizen.html Viewed 23-2-2008.