El objetivo encomendado era aplicar un programa automatizado de lubricación, y el fracaso no era una opción. Recién ingresaba a la Industria del Papel después de dejar el Ejército de los EEUU con un gran deseo de conseguir el éxito en mi nueva carrera. Como la mayoría de los nuevos ingenieros, me embarqué a cambiar el mundo cambiado nuestro programa actual de lubricación de la Edad de piedra directamente a la era espacial.
En el Ejército, teníamos un dicho en forma de pregunta. ¿La pregunta era, "Confiaría su vida en el estado en que se encuentra su equipo en este momento"? La respuesta a esta pregunta era muy reveladora. Lo qué esta pregunta hizo fue marcar que el soldado pensara detalladamente acerca de si él había cuidado de todas las verificaciones relativas al mantenimiento preventivo para su vehículo, arma, y equipo adicional, así como el seguimiento al mantenimiento, para conocer el estado exacto de su equipo.
Cada lunes era nuestro día de mantenimiento de orden. Fue en uno de estos lunes que aprendí una lección importante en el inicio de mi carrera militar. Cada soldado (incluyendo los oficiales), sin importar su trabajo individual, se encontraban en la unidad mecánica realizando mantenimiento de orden (PM) en sus vehículos por ese día. Presencié a personas de primer nivel "azotar el lápiz" ("pencil whipping" expresión estadounidense utilizada en el medio para expresar que solamente se llenan los datos para acabar rápido con el formulismo. Nota del Traductor) sobre la hoja de PM para que pudieran salir de la unidad mecánica y reincorporarse a sus actividades de rutina. El "azotar el lápiz" termino abruptamente un lunes cuando a final del día, mi Comandante publicó una orden para que todos los vehículos salieran de la unidad mecánica y completaran una marcha sobre el camino de veinte kilómetros. El tenía en sus manos todas las hojas de PM completadas para cada vehículo ese día. Cuándo los vehículos no pudieron siquiera salir de la puerta y no había nada anotado en las hojas de PM que resaltara cualquier asunto sobre problemas de mantenimiento, puede imaginarse la conversación que siguió. El mantenimiento preventivo puede ser la diferencia entre la vida y la muerte en el campo de batalla.
Al hacer la transición del ejército a la industria privada, empecé primero evaluando las prácticas de trabajo de los petroleros que estaría dirigiendo (no solo supervisando) en nuestra nueva misión. Me sorprendió lo que encontré. Digamos solamente que encontré el verdadero significado de la frase "Destreza de malas prácticas". Por ejemplo, los engrasadores distribuían el aceite en contenedores metálicos abiertos antes de salir y atender una pieza de equipo de rotación. Si el aceite restante en el contendedor era de una viscosidad más ligera y necesitaban de un aceite de diferente grado, simplemente llenaban con un aceite de viscosidad diferente. Ni una vez vi que limpiaran el contenedor o miraran para ver si estaba sucio. Esto fue impactante, así que decidí encontrar por lo menos alguna documentación sobre los lubricantes utilizados en nuestro complejo. Lo que encontré fue aun más impactante, una carpeta de anillos con una inspección de lubricantes que había sido realizada 17 años atrás. Por supuesto, desde aquel entonces han habido numerosas nuevas instalaciones de equipo y varios aparatos se retiraron del servicio. Fue claro que nadie tenía ninguna idea de lo que se debía de hacer en una rutina diaria relativa a la lubricación.
La próxima fase de nuestra tarea fue la de contactar a nuestro proveedor y a nuestro ingeniero regional de lubricación. Puse en contacto a nuestro proveedor de lubricación con nuestro departamento de compras, haciéndoles saber que si su desempeño y apoyo al cliente no mejoraba, iniciaríamos el proceso para cambiar de proveedor. Gastábamos en el orden de más de las 6 cifras anualmente en lubricantes, y no obteníamos mayor apoyo que el camión de reparto que hacia una entrega a granel, y que la empresa invitaba a un par de personas a comer y les regalaban sombreros y plumas. Mientras tanto, nuestro equipo fallaba debido al uso de lubricantes incorrectos.
Así que la pregunta era, ¿Como me como el pastel? Sí, ya sé, una mordida a la vez, pero por dónde se supone que debíamos comenzar? Comenzamos analizando nuestro tiempo de inactividad debido a fracasos de lubricación utilizando una gráfica de Pareto (Figura 1) y comenzamos con nuestra peor área primero. Quería que nuestra compañía de lubricación realizara una inspección de lubricante bajo mi dirección. La primera cosa que ellos quisieron hacer era la de enviarnos un batallón de ingenieros de lubricación para vendernos lo mas que pudieran. Entendiendo que este iba a ser un viaje largo, renuncie a esta idea. Decidí que uniríamos nuestros esfuerzos y sólo nos centraríamos en un área a la vez. Asigné a un ingeniero de lubricación para manejar la grasa y otro a manejar el aceite. Identificamos todo el equipo en el área específica que utiliza aceite o grasa. Identificamos lo Siguiente:
- Nombre del Equipo
- Numero del Equipo
- Tipo de Lubricante (Recomendado por el fabricante del equipo)
- Cantidad correcta
- Frecuencia para re-lubricar
- Candidato para Análisis de Aceite

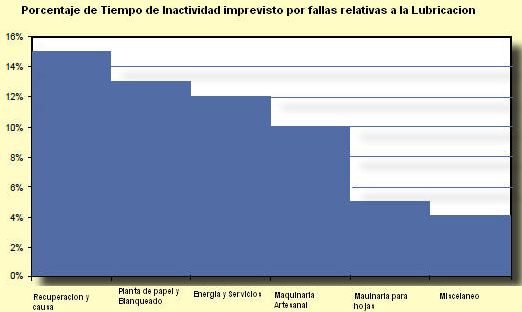
Lo que encontramos fue que la información en nuestro CMMS estaba incompleta. Al Verificar los datos en el campo, pudimos hacer dos cosas. La primera fue identificar y corregir las deficiencias dentro de nuestro CMMS y la segunda fue identificar el equipo crítico que estaba ausente de nuestra base de datos de vibración. Simplemente no podía creer que teníamos equipo crítico que no estuviera monitoreado. Esto no puede ser suficientemente acentuado - Usted debe tomarse el tiempo para verificar que su información de los equipos es correcta. Si no lo hace, entonces se estará encaminando hacia la falla antes siquiera de empezar.
El próximo era establecer las prioridades del trabajo. ¿En qué consisten las visitas diarias del trabajo? Uno de las grandes diferencias entre el servicio militar y la industria es la mentalidad de que algo se le debe al trabajador por hacer bien su trabajo. En el ejército, antes que usted piense siquiera en comer, la higiene personal, o aun en dormir, su equipo es primero. No importa en donde se encuentren ubicadas las manecillas del reloj. Por lo tanto, mientras en el ejército la pregunta es, "¿le confiaría su vida al estado de su equipo"?, en la industria la pregunta debe ser, "¿le confiaría su cheque de pago al estado de su equipo que USTED es responsable de mantener"?
Desafortunadamente para muchos de los engrasadores en el momento en que yo me incorpore a la empresa, la respuesta a todo era un ¡NO! Rotundo. Antes de implementar cualquier cambio, conseguíamos aproximadamente 20-30% de productividad de cada empleado. La responsabilidad estaba ausente, y se mostraba en objetivos no alcanzados, en números bajos de producción, y en costos altos de mantenimiento. Nuestra visita diaria de trabajo tenía que cambiar drásticamente. Después de cambiar nuestras prioridades de trabajo, y de reeducar a los engrasadores a través de un programa de capacitación, nuestra productividad inicial aumento 50%. Les mostraré luego cómo pudimos lograr esto. Lo que fue sorprendente es que todos nuestros fracasos relacionados con lubricación comenzaron a reducir dramáticamente.
Iniciamos nuestro primer proyecto piloto con un técnico de lubricación que recorría una ruta con un PDA. Instruí al técnico que realizara su ruta de la misma manera como lo hacía antes de que cambiáramos. Los resultados tambaleaban. Lo que encontramos fue, que cuando el nuevo técnico de lubricación recorrió su vieja ruta de engrasado, él sólo miraba aproximadamente 23% del equipo en alguna área dada. Ahora que hemos elaborado una ruta completa de lubricante y estaba en el PDA, la inspección tenía que ser apuntada por el aparato en el campo. El equipo ahora se estaba inspeccionado apropiadamente y el trabajo correcto comenzaba a suceder. Otro punto de contienda con la Administración fue que cuando comenzamos estas nuevas rutas, nuestros costos de mantenimiento comenzaron a aumentar por los años de descuido en el equipo. Cuando continuamos con este esfuerzo a través de toda la planta, nos encontramos con lo mismo en casi todas las áreas.
Tomó aproximadamente un año aplicar este programa a través de la Planta. La principal razón a que el proceso fuera tan largo, es porque deseé que todo el equipo fuera identificado y dejar un área totalmente funcional antes de iniciar la siguiente. Seguimos la información en nuestra gráfica de Pareto y continuamos la implementación. Cuando terminamos, nuestros técnicos de lubricación cambiaron de hacer rutas de lubricación, a realizar un "programa esencial de cuidado al equipo" que consistió en inspecciones visuales del equipo, verificación de la lubricación, y lecturas de la temperatura. En los dieciocho meses que siguieron después de nuestra implementación, nuestros costos de mantenimiento fueron constantemente en descenso, y el tiempo productivo de la maquinaria y la disponibilidad de la planta había aumentado dramáticamente.
Resumen
Después de aplicar este programa aumentamos nuestro muestreo de análisis de aceite por más del 400%. Nuestra ruta paso de un 23% a un promedio de 92%. Nuestra falla de maquinaria se redujo por más de un 70% en un período de 18 meses. Estos números son indicativos del nuevo programa, pero recuerden que al aplicar un programa automatizado de lubricación, se requiere mucho más que conectar los nuevos instrumentos y el software y sentarse a esperar los resultados. Usted debe hacer el trabajo "pesado" en el campo para asegurarse que haya reunido toda la información correcta para construir su programa en una base sólida. Usted debe desarrollar un programa de capacitación completo para asegurar que todos los técnicos comprenden no sólo lo que se espera de ellos, sino por qué ellos hacen el trabajo. Si todos comprenden por qué el hacer las cosas de forma distinta funcionara mejor, entonces es más probable que a ellos les agrade más realizar su nueva función. Por último, debe inspeccionar lo que espera. Usted puede enseñar fácilmente a un perro viejo nuevos trucos. El verdadero truco es encontrar la motivacion apropiada.
Paul Dufresne es Gerente Consultor de Confiabilidad en Trico Corp. Antes de trabajar para Trico, Paul trabajo para Georgia- Pacific Corp como Supervisor de Confiabilidad en su División de Pula y Papel. Paul sirvio 10 annos en el Ejercito de los EEUU como Oficla de Armada para una Compania de Tanques Abrams M1A1 y es un Militar graduado distinguido de la Universidad Central de Florida.