Additional material problems that impact labor productivity include late deliveries from vendors, wrong parts delivered, and parts that are damaged and cannot be used when they arrive.
The conflict between maintenance and the MRO organizations arises when neither sees the big picture. If they can focus on their shared impact on equipment capacity, they can be successful. The MRO organization supplies the spare parts; the maintenance organization then uses the spare parts to ensure that the company’s assets perform properly. Without focusing on a partnership to accomplish this, there will always be conflicts between the two organizations.
Stores Locations and Organization
A concern in most organizations is configuring the maintenance and MRO inventory and purchasing organizations. When considering MRO stores locations and organizations, one of the primary factors is how the maintenance department is organized.
If the maintenance organization is centralized, then it is usually best to have the stores locations centralized as well.

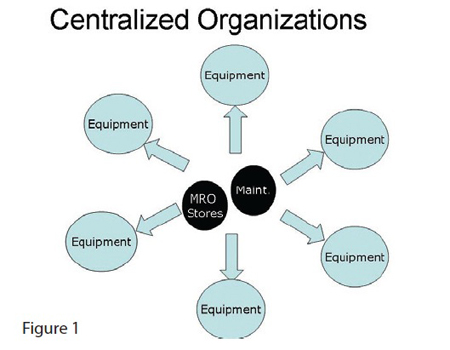
Figure 1 shows the advantage of this configuration. This diagram shows that when maintenance and stores are together in the center of a plant or facility, it is easy to travel to the equipment. The distance that maintenance has to travel to obtain spare parts and then travel to the equipment is minimized. This arrangement maximizes labor productivity for the maintenance department.
It also allows for more rapid response when equipment experiences problems. Therefore, for geographically compact plants or facilities, this is an ideal configuration.
The problem that is typically experienced when designing this type of an organization is trying to find the centralized space for both maintenance and the MRO storeroom. Most companies are reluctant to give up prime space for these two departments.
However, once the total cost picture is clearly understood, it is a good business decision to centrally locate maintenance and MRO stores for smaller geographically compact plants.

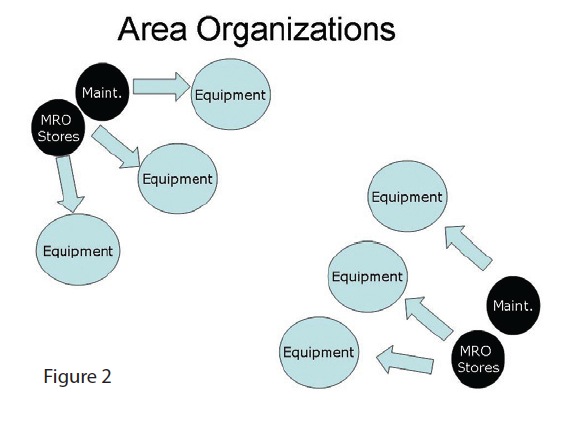
If the maintenance organization has an area configuration, then it is usually best to have the stores locations in an area configuration as well. Figure 2 highlights this configuration. In this figure, there is a larger geographical footprint for the plant or facility. It may actually be several miles from one side of the diagram to the other.
Given this condition, it makes sense to have MRO stores and maintenance co-located on opposite sides of the plant. This minimizes the travel time for maintenance to get to the equipment. Increased maintenance labor productivity is the result, whether it is in a proactive or a reactive environment.
The common complaint with using this type of a structure is the increased stocking levels for the MRO storeroom. In this configuration, it is true that there will be an increase in the stocking levels. This must be balanced against the increased maintenance labor productivity and the reduced downtime (and increased equipment capacity) that will be achieved by using this configuration.
If the maintenance organization is in a combination configuration, then it is usually best to have the stores locations in a combination configuration. Figure 3 highlights a combination configuration. A combination organization is typically used on large plants. Although maintenance and MRO stores maintain an area presence, certain parts of the organization and types of spares are brought to a centralized location.
In a maintenance department utilizing a combination organization, the central trades group will be comprised of technicians that would not be fully utilized in a single area. The combination organization allows the sharing of central trade technicians among several areas to increase their overall utilization. The same reasoning applies to the MRO stores. There are certain common spare parts that can be kept centrally, while parts specific to a certain area should be kept in the area. This configuration works well for large organizations and optimizes both maintenance resources and MRO spare parts, and also increases equipment availability.
The reason for matching the configuration is the impact that travel time to and from the storeroom can have on maintenance labor productivity. If there is a mis-match between the stores and the maintenance organizations, then the travel time to and from the stores to procure spare parts can be considerable. Figure 4 highlights this issue.
As can be seen from this figure, the distance (and time to travel) can be considerable if maintenance needs to travel to the equipment. If the maintenance technicians need to go to the storeroom before going to the equipment, they would face even more travel time. If the equipment is down, waiting on maintenance, then the losses increase to include not just lost maintenance productivity, but also lost production. In geographically compact plants, this may not be an issue; however, in large plants, the losses incurred with dysfunctional organizations can have a dramatic impact on profitability.
This example of lost maintenance productivity and lost production is particularly true in the early stages of developing a maintenance organization because a reactive organization needs spare parts on short notice. As the maintenance organization matures and becomes better at planning and scheduling, material demands can be specified weeks in advance. With this level of forecasting, kitting and delivery systems can be implemented and the location of the storeroom becomes less of an issue.
The decision on the location of the storeroom and possibly the number of locations needs to be carefully balanced. The balance is between lost maintenance productivity and the cost of inflating the inventory to support multiple locations. Some organizations, in an attempt to increase maintenance productivity, will carry excessive numbers of spare parts to compensate for organizational mismatches. Delayed spare parts procurement does not impact only maintenance productivity; it also impacts equipment availability. When making the decision about spare parts locations and organizational structures, it is important to consider all of the factors, and then come up with a financially balanced decision.Terry Wireman is a maintenance reliability expert who is a popular Keynote presenter at many industry events. He has authored dozens of books including the new Maintenance Strategy series published by Industrial Press (www.industrialpress.com). The second volume in that series, MRO Inventory and Purchasing, is available at the MRO-Zone.com bookstore at http://books.mro-zone.com
Terry Wireman is a maintenance reliability expert who is a popular Keynote presenter at many industry events. He has authored dozens of books including the new Maintenance Strategy series published by Industrial Press (www.industrialpress.com). The second volume in that series, MRO Inventory and Purchasing, is available at the MRO-Zone.com bookstore at http://books.mro-zone.com