Thousands of articles can be found about the subject of improving rotating equipment reliability and even more subject matter experts are available to industries worldwide. However, sustaining a predictive maintenance (PdM) program over a long period of time is elusive for many. Generally speaking, purchasing the hardware and software, and then obtaining the necessary training can be the easy part. What is really difficult is trying to maintain the program through a severe economic downturn, employment attrition within the plant, plant and union management changes, etc. In fact, what makes the story of Romulus Engine so interesting is how the plant has been able to not only sustain the program, but also expand it when so many others within the industry have cut back or even eliminated their EMD program.
This particular part of the story starts around 2006 with the implementation of a computerized maintenance management software system called Maximo. In 2007, a formal PdM team was formed and the initial focus was inspections using infrared thermography. During this time, the process and procedures for implementing the inspection process had to be developed from scratch.
The goal from the beginning was to develop a world-class program. In order to do that, a selection process had to take place to find the right people who were self-starting individuals who could work within the parameters of a team concept. Also, a salaried electrical engineer was tasked at the beginning to act as a technical and administrative resource. This person also acted as a "cheerleader" to get this new group of people to function like a team. In order to get to that point, they had to adopt a new way of thinking.
This new way included establishing a communication process within the plant to inform all departments and personnel of the various technologies to be used. A weekly meeting consisting of both salaried and hourly team members was implemented. In the beginning, the plant focused on setting up the program, which, as you can imagine, was a daunting task. The team had to "hash out" everything from what to test and what technologies to focus on, to what the report should look like? From this process came the work procedures and processes that drive the program today.
The initial hourly team consisted of Mike Anaple and Ken Breece from the first shift. In 2008, the PdM program was expanded to include EMD based on United Auto Workers/World Wide Facilities Group quality network planned maintenance (UAW/WFG QNPM). Establishing the EMD program also involved field trips to motor vendors, other facilities doing motor testing, seminars and networking with subject matter experts. Later in 2008, a second shift team was added, consisting of Sam Richardson and Mike Nault. Key support from the salary side came from Electrical Engineer Cheryl Murphy, plus strong support from plant management.
As the program exists today, it consists of infrared, ultrasound, EMD and vibration. Of these four technologies, infrared and EMD are the most widely used. Ultrasound was expanded in 2010 and they expect to expand the vibration program this year.
Specific to EMD, this includes route-based testing of critical production equipment, request-based work (which can include both production and facilities equipment), testing of motors before and after repair, testing of new motors and shaft rotation of motor spares. Tracking of motors sent in for repair require that a process be established with the commodity manager so the information is available within their computer system.
EMD as practiced by Romulus Engine includes both on-line and off-line testing of motors. On-line testing using electrical signature analysis (ESA) is performed mostly on AC induction motors with off-line testing using motor circuit analysis (MCA) for AC induction and DC motors.
Some of the benefits of the EMD program include reductions in troubleshooting time, motor repair shop "no problem found" reports and severity of rotating machinery failures. Overall predictive maintenance cost avoidance for 2011 was over $3 million and EMD accounted for ~22 percent of this amount. Infrared inspection leads the savings at ~45 percent. Vibration and ultrasound, along with high-speed video camera analysis, make up the balance.
The team is required as a department to report program results on a quarterly basis as part of the QNPM guidelines. Reporting out includes sharing any new information on emerging technologies, cost avoidance and any significant finds. Sharing this information plant-wide brings greater awareness about the program and builds a level of trust in the PdM teams' equipment and knowledge. It is a constant learning process for everyone in the plant.
Another aspect that has proven to be important to sustaining the program is sharing information within the team. As an example, if one of them has an issue not seen before in a particular motor, they have each other's cell phone numbers so they can communicate even when off shift. In the beginning, all of this was brand new, so everyone had a steep learning curve and sharing of information proved to be very important to creating a successful program.
With respect to the PdM program, route-based testing follows this basic structure:
- Routes are generated using Maximo software.
- Monthly route sheets are used to perform PdM testing for infrared, EMD, vibration and ultrasound.
- As a route is completed, information is entered into Maximo.
- If follow-up work is generated, then a Maximo work order is created along with appropriate information to fix the problem.
- Area trades complete required work.
- The work order is returned to the PdM department so they can perform a follow-up test (retest).
- If the test comes back good, then this information is discussed with the appropriate tradesperson (creates program awareness and continuous improvement).
- If retest fails, then a corrective work order is issued to the area.



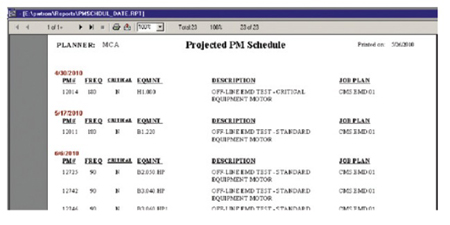
Figure 1: Maximo software PM schedule report

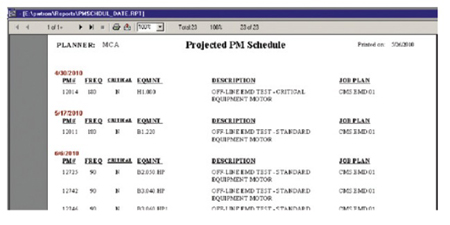
Request-based testing follows this basic structure:
- PdM team member is dispatched to investigate possible machine or process issue.
- Maximo work order is generated.
- PdM department determines if issue can be solved using appropriate equipment (infrared, EMD, vibration, ultrasound, etc.).
- If a problem is detected using PdM equipment, then a follow-up corrective work order is generated to complete any issue found.
- If no issue is found, then work order is closed out.
Maximo is used to track and report cost avoidance using a conservative calculation process. As previously mentioned, this information is shared plant wide.
Figure 2: Maximo is used to track cost avoidance
For those new to EMD, here are a few examples that illustrate program savings.
EMD off-line testing incoming inspection find: Ash house 60 HP motor located on a roof failed and a replacement was brought in. As part of the EMD testing program, the motor was tested prior to starting the installation process. Results from the motor circuit analysis (MCA) test showed the motor was in poor condition. A second motor was brought in and tested. This one tested okay, so installation was completed. Since this motor was located on the roof, installation required the use of a lift truck, elevator, block and tackle, and between six to eight hours of labor. The cost avoidance by not installing a new motor with a defect is ~$20,000. Incoming motor testing has increased rotating equipment reliability and the test itself only takes a few minutes.
EMD on-line testing find: This is a 60 HP pump system motor that is tested every six months. Routine testing detected a rotor fault and the motor was replaced during an off shift (normal production shutdown). The report from the motor shop showed cracked rotor bars and a blow hole in the end ring. Cost avoidance by replacing the motor before it failed during a production cycle was $142,500 for the supply pump. Figure 3 is a snapshot of the ESA software analysis screen.
Figure 3: On-line testing ESA software analysis screen
Motor troubleshooting: EMD, along with other testing technologies, are used for troubleshooting a motor system that is running poorly or has failed. Figure 4 is the structure that Romulus Engine developed.
Figure 4: PdM team troubleshooting process
Creative testing using MCA: This plant has many AC motors that include a coil activated brake. Diagnosing problems with the brake in the past was a problem. Since these brakes are a three-phase device made up of coils, Romulus Engine Operations uses the MCA test instrument to determine the electrical condition of the brake. No more guessing whether the problem is electrical or mechanical in nature.
Romulus Engine Operations has a successful and sustainable EMD program that has thrived when others in the industry have either reduced the scope of their EMD program or eliminated it entirely. The EMD testing program has generated significant cost avoidance savings over the years and is considered to be a pillar in their PdM reliability testing process. After interviewing team members, it is apparent that it is the people involved at all levels in the plant that has made the difference. As one team member stated: "To have a world-class PdM program is what we strive for."
About Romulus Engine Operations
Romulus Engine is located in Romulus, Michigan, and employs nearly 800 people. Hourly employees are represented by UAW Local 163. The plant produces a variety of V6 and V8 engines that power GM full-size SUVs and pickups, including the Chevrolet Express, Silverado, Tahoe, Avalanche, Suburban and Colorado, GMC Savanna, Sierra, Yukon, Envoy and Canyon, and Cadillac Escalade. Romulus-built engines are also used for marine and industrial applications. Over 477,000 engines were produced in the 2011 calendar year. Historically, the plant has a long-standing reputation for quality, productivity and performance.
Instruments used in their PdM program:
Infrared: FLIR P640, P60 and T400; Ultrasound: UE Systems Inc. 10000 Ultraprobe; Vibration: CSI 2130; EMD: off-line ALL-TEST PRO ATIV and on-line ALL-TEST PRO ATPOL II.
Romulus PdM team members are left to right: Mike Nault, Mike Anaple, Cheryl Murphy, Sam Richardson and Ken Breece.
Mike Nault has been a journeyman Electrician at GM since 1995 and doing Predictive Maintenance since 2008. He has completed Level I and Level II Infrared Thermography. He also has Level I Electric Motor Diagnostics and Ultrasound training.
Mike Anaple has been involved in Predictive Maintenance since 2007, focusing on Infrared (Level III), EMD, Ultrasound and Program Management. He has almost 25 years of Industrial Electrical Maintenance experience in various capacities.
Cheryl Murphy is a Level II thermographer with practical knowledge in the fields of EMD, Ultrasound and Vibration Analysis. She has BSEE and MSES degrees and over 30 years with GM.
Ken Breece has 34 years with GM (16 as an Electrician). He has been involved with Thermography since 2007 (Level II) and has been performing EMD since 2008, as well as using Ultrasound and High Speed video instruments.
Sam Richardson has been an Electrician at GM since 1989 and performing Predictive Maintenance since 2008. Sam completed Level I and Level II Infrared Thermography training. He also has completed Level I Electric Motor Diagnostics and Ultrasound training.
Richard Scott, General Manager, ALL-TEST Pro, LLC, Old Saybrook, Connecticut. He joined ATP in 2004 as a Regional Sales Manager, but first became involved with the ALL-TEST PRO line of motor testing instruments in 2001. www.alltestpro.com