INTRODUCTION
Aiming to improve the profitability of productive processes, huge efforts are made daily that focus on visualizing, identifying, analyzing, implementing and executing activities to solve problems effectively, make successful decisions involving high impact areas like safety, environment, production goals, operation and maintenance costs, and guarantee a good corporate image and customer and staff satisfaction. Maintenance or asset care plans represent one of these efforts. Due to their high costs in design, elaboration and implementation, the establishment of asset care plans must adhere to the belief that through these you will get better levels of performance and profitability throughout the value chain.
The proper selection of methods and tools used during preparation significantly affect the processing time and cost of the plans.
CONCEPTUAL FRAMEWORK
Risk
In the decision-making process, risk is used as a tool for optimizing asset care plans, directing more resources and efforts to equipment that presents a high risk and less to low risk equipment, to allow a justified expenditure of resources directed to maintenance items1.
To evaluate the risk through the probability of occurrence and its respective consequences, risk relatively is estimated using a qualitative matrix1 as shown in Table 1.

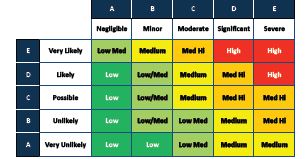
Table 1: Risk Ranking Matrix
Equipment Group
Hierarchical level characterization of all equipment supports functions or a group of functions for which they have been selected (Figure 1).

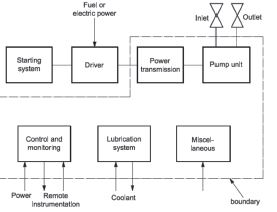
Figure 1: Equipment Group2
Criticality Analysis
This methodology establishes a facilities, systems, equipment and devices hierarchy or priorities according to a figure of merit called criticality. Proportional to risk, criticality creates a structure that facilitates decision-making and steers effort and resources in areas and situations that have the greatest impact on business.
Figure 2 is a typical arrangement of a semi-quantitative 4x4 risk matrix. It shows that the likelihood or frequency axis is divided into high, medium, low and remote classifications, and consequences are equally divided into ranges as grave, substantial, marginal, or negligible. These ranges should be associated with numerical values for quantitative studies and/or clear descriptions in case of semi-quantitative or qualitative studies.
Three risk regions can be identified in the matrix: unacceptable, acceptable and a region between the two that requires detailed assessment activities, risk management and monitoring.
Figure 2: Criticality matrix3.
Risk-Based Inspection (RBI)
An RBI study is based on the implementation of American Petroleum Institute (API) standards, API580 and API581, and establishes frequency and scope of inspections based on historical behavior, damage or deterioration modes, design features, operating conditions, maintenance, inspection and management policies, the quality and effectiveness of inspections, and the consequences associated with the occurrence of potential faults.
Graphically, this methodology allows for the identification or location of equipment under analysis risk level in a 5x5 matrix (Figure 3) that has four levels of risk classification: low (white or green), medium (yellow), medium high (orange) and high (red).
The result of this methodology is a hierarchical list of equipment based on risk calculated to determine the types of inspection and the appropriate frequencies.
Figure 3: Risk-based inspection risk matrix4.
Reliability Centered Maintenance (RCM)
It is an analytical and systematic process based on understanding the system's role (functional analysis) and functional and components failures that aims to identify company policies to handle the failure modes that can cause functional failure to any physical asset within an operational context.
The objective of an RCM analysis is to generate the appropriate maintenance tasks to minimize the recurrence of failure modes and/or mitigate the consequences of its occurrence.
Failure Modes and Effect Analysis (FMEA)
At the heart of the RCM process is FMEA, a systematic methodology that might occur in specific equipment, evaluated in its operational context. This analysis shows the possible causes and failure mechanisms and, therefore, can be inferred preventive, predictive, detective and/or corrective actions required to avoid failure and/or mitigate their consequences using a maintenance task selection diagram, as shown in Figure 4.
Figure 4: Reliability centered maintenance process using FMEA methodology5
Cost Risk Optimization
Cost risk optimization is a model to determine the optimal risk level and the appropriate amount of maintenance to get the most benefit or minimal impact on business. Figure 5 shows graphically the model; three curves are highlighted and may vary over time:
Figure 5: Maintenance frequency optimization2
• Risk level curve (risk = probability of failure x consequence).
• Risk mitigation action costs curve - simulates the costs of different frequenciesfor the proposed action.
• Total impact curve - results from the sum of the risk curve and the cost curve, point to point. The "minimum" of this curve represents the "minimal impact on the business" and is located on the value that can be translated as the period or optimal frequency for the implementation of the mitigation activity, a shift to the right of this point would mean "taking a high risk" and a shift to the left would mean "spending too much money." It is important to highlight that each of these curves represent probability distributions based on the fact that the level of uncertainty of the input variables has been considered.
INTEGRAL ASSET CARE METHODOLOGY
IAC was developed to meet the requirements of integral asset care, such as dynamic, electrical, fixed and instruments, both primary and secondary. Additionally, this methodology directly involves the operator as principal in the design and implementation of different asset care activities.
IAC is based on the combination of the criticality analysis methodologies, Level I of RBI, RCM, FMEA and cost risk optimization, in order to design integral plans for asset care (Figure 6).
The application of this methodology is developed in the following steps:
1. Establish system boundaries that will design the integral asset care plan.
2. Define care policies for all asset types.
3. Search and analysis of: databases of main and secondary equipment,
maintenance plans and policies of current support, maintenance indicators,
operational philosophy, process and instruments diagram (P&ID), Process
Flow Diagram (PFDs), current equipment conditions equipment and
technical features, technology used, etc.
4. Perform criticality analysis for each system's assets based on known methods,
such as integral criticality analysis; functional analysis; criticality based
on maintenance and reliability management indicators (e.g., mean time
between failures, mean time to repair, etc.) and risk-based inspection.
An integral asset criticality analysis application can be developed according to the flowchart in Figure 7.
The flowchart shows how the integral criticality assets analysis methodology is divided into two branches. The principal and secondary equipment hierarchy includes the instrumentation critical analysis that depends on the type of instruments and the resulting level of criticality of the principal equipment for which the instrument is providing its functions. The other branch is the critical analysis for specific instrumentation, where the level of risk is determined according to failure probabilities and their consequences. The type of methodology used depends on the time and resources available.
Figure 6: Integral asset care methodology5
Figure 7: Integral asset criticality analysis methodology5
An integral asset criticality analysis application can be developed according to the flowchart in Figure 7.
The flowchart shows how the integral criticality assets analysis methodology is divided into two branches. The principal and secondary equipment hierarchy includes the instrumentation critical analysis that depends on the type of instruments and the resulting level of criticality of the principal equipment for which the instrument is providing its functions. The other branch is the critical analysis for specific instrumentation, where the level of risk is determined according to failure probabilities and their consequences. The type of methodology used depends on the time and resources available.
Phases of Integral Asset Criticality Analysis Methodology
1. Determination of criticality level for principal equipment in an equipment group (dynamic and electric according to the risk matrix of the system under analysis) - Based on the probability and consequence level from health, safety, environment (HSE) and process analysis using the risk matrix defined for the specific business.
The analysis should be developed with personnel from maintenance and operations, or with any other personnel that has knowledge of risks associated to the safety of the unit or equipment under analysis. The highest level of criticality resulting from the hierarchy of the HSE and process analysis is selected.
2. Determination of criticality level of secondary equipment in an equipment group - Based on the level of criticality of the principal equipment and the established criteria, including whether the secondary equipment assists or supports the principal equipment's function performance.
Once the process impact and HSE level for the secondary equipment are determined, the highest level of criticality resulting from both criteria is selected to determine the real risk level of assets from the HSE and process perspective.
3. Conduct Phase I RBI to determine the level of criticality of fixed equipment in an equipment group using Level I of API580 and API581 standards - Level I corresponds to a qualitative analysis that determines the level of risk for assets of a working installation, ranking each unit based on both elements of risk: probability and consequence (Figure 8).
To apply this methodology, it is necessary to treat the technical, historical and operating conditions data that was used to obtain the first product of the analysis. In addition, a qualitative risk mapping of the units of installation to study is developed to rank the units to determine the level of analysis, classify the level of risk of the units in the installation and place them on the risk matrix, and identify areas inside the plant that require special attention and perhaps special inspection programs.
Figure 8: Criticality analysis methodology for fixed equipments4,5,6
4. Design a generic inspection plan - Applies to equipment with a low criticality level.
5. Create FMEA or generic templates - These are procedures taken for asset healthcare and generated for equipment that operates under similar technical characteristics and policies.
One of the most important steps in the development of a FMEA is the risk index number (RIN), determined by arranging the level of risk associated to each of the failure modes in a qualitative way (Table 2).
Table 2 - Components of the Risk Index Number
One of the final and very important requirements for completing the FMEA is the selection of mitigation strategies for each failure mode by applying the decision diagram and task selection of SAE International's JA1012, "A Guide to the Reliability Centered Maintenance Standard." This diagram allows the identification of hidden failures, the determination of consequences and has some criteria of technical feasibility that contributes to the assertiveness on the selection mitigation strategies.
6. Generate asset healthcare programs for the remaining equipment families - Includes dynamics, electrics and instrumentation according to their criticality levels and technical characteristics.
7. Store assets' healthcare programs in a dynamic database - This allows for the sharing of all information among administrative and managing systems.
CONCLUSION
The optimal combination of criticality analysis, risk-based inspections, reliability centered maintenance, FMEA and cost-risk benefit analysis methodologies allow for the development of asset healthcare integral policies. In comparison to traditional methods, the development and application of integral asset care reduces the time and resources used in the design of asset healthcare programs by more than 50 percent.
When applying this methodology, the operator plays an important, proactive role in the healthcare program activities and migration of such programs to the managing system guarantees the success of their implementation.
This methodology facilities the decision-making and resource allocation process by basing it on risk levels and aversion, which allows for a more profitable business.
REFERENCES
1. Yañez Medardo, Gómez de la Vega, Hernando, Valbuena Genebelin. Reliability Engineering and Probabilistic Risk Analysis. Venezuela, June 2003. ISBN 980-12-0116-9.
2. International Organization for Standardization (ISO). ISO/DIS 14224 Petroleum and Natural Gas Industries - Collection and Exchange of Reliability and Maintenance Data for Equipment. London: ISO, May 2005 (draft).
3. Norwegian Petroleum Industry. Norzok Standard Z-013, Risk and emergency preparedness analysis. Rev. 2, 2001-09-01. http://www.standard.no/pagefiles/955/z-013.pdf
4. American Petroleum Institute (API). Risk-Based Inspection, API Recommended Practice 580 First Edition. Washington, D.C.: API, May 2002.
5. Fuente R2M S.A Reliability and Risk Management.
6. SAE International. SAE-JA1011/SAE-JA1012: Guide for the Reliability Centered Maintenance Methodology (RCM). Warrendale: SAE, 2002.
7. Materan, E; Aranguren, J; Bravo, J; Medina, R. Generation of Optimal Inspection Plans for Fixed Equipment in the Oil and Gas Industry. Venezuela: Reliability and Risk Management, 2006. American Petroleum Institute (API). Risk-Based Inspection Base Resource Document, First Edition. Washington, D.C.: API Publication 581, May 2000.
8. Calixto Ivaneska, Bahoque Evila, Gutierrez Edwin. Develop of a Methodology for the Design of the Asset Health Care Policies. Venezuela. January 2006.
at Reliability & Risk Management S.A. Mr. Gutierrez
has over 16 years experience in the area of
reliability engineering, asset maintenance and
condition monitoring strategies. He has a degree in
Mechanical Engineering with a Masters in Reliability
Engineering. www.reliarisk.com