1) Introduction to Inventory Management
For Facilities Maintenance Organizations, the quickest and most substantial "hard dollar" returns are achieved through the Inventory and Purchasing modules. Even in Equipment-centric Organizations, where the emphasis is on uptime and asset efficiency, the savings from improved materials management can be sufficiently large to cover the cost of purchasing and implementing a CMMS project.
In the early 1990s, the primary materials focus of CMMS was the issuance and cost tracking of Inventory transactions to Work Orders. Today, the objective of maximizing the “Return on Investment” is strongly enhanced by the deployment of sound Inventory Management principles. Thus, the primary objectives have now become:
- To accurately expense the cost of purchased materials to the correct Work Order / Expense Account, and
- Through the use of efficient Part Storeroom Management procedures, to reduce the required level of on-hand Inventory stock while simultaneously reducing the number of costly “stock-out” events and their associated procurement expenses.
Due to inefficiencies and the high cost of maintaining a “less than optimal” storeroom, a growing number of Organizations have now outsourced their Inventory departments to third-party contractors. This need not be the case. This document will cover how to implement strategies such as Just-in-Time Inventory and normalization of stock keeping units (SKUs) to keep the ownership of Inventory and Purchasing activities where they belong – “in-house”.
The functionality expansion within the various CMMS packages has provided the necessary tools for Organizations to improve the process of Materials Management and to maximize their Return on Investment. Certain components are necessary to define the CMMS package as effective. Check your own system for the functions below:
• Tracks balances for all items, including issues, reserves, and returns
• Has the ability to reserve items for specific jobs
• Has the ability to automatically reorder parts when needed and to track the order through the receipt process
• Has the ability to produce KPI’s such as stock turnover, service levels, and fill ratios
• Cross references of spares to substitutes
• Maintains a Bill of Materials for specific equipment
The annual cost of maintaining an inventory storeroom is considerable. Through recent industry studies, it has been found that the percentage cost of maintaining an inventory storeroom will annually run 20-30% of the total inventory dollar value. Thus, a reduction of $1 million of Parts held on hand delivers an annual savings of $200,000 - $300,000. The primary components of this storage cost are the cost of money (capital) associated with holding inventory, insurance and taxes, facility space and maintenance cost, the cost of physical counts and reconciliation, and the cost of theft, obsolescence and spoilage. The high carrying cost certifies the need to reduce the volume of stocked inventory, but the reduction must be accomplished without increasing the number of out-of-stock ccurrences. Without the benefit of other inventory business process improvements, an “across the board” stock reduction might even prove counter-productive - as the increased cost of labor, transit time, and related purchasing expenses resulting from increased stock-outs events could outweigh the savings from reduced carrying cost.
2) Evaluate your Issues and Stores Management Business Processes
CMMS systems are effective in helping to meet these twin objectives (balance reduction and the reduction of stock-out events) through the implementation of a Just-in-Time Inventory methodology. This concept is not new and has been used with production inventory for many years. The success of this venture does require the cooperation of the Maintenance personnel. Storerooms need to be able to purchase Parts in anticipation of upcoming work requirements, rather than basing the Part reorder process on just visual inspections, historical usage trends or immediately after issue. Upcoming Parts requirements should be attached to repetitive Preventive Maintenance activities and other Planned Work Orders with sufficient lead times. Check the CMMS Job Plan and PM records for your Organization to see whether Part estimates have been included for PM work. A reactive Maintenance Department cannot be effectively sourced by the Storeroom.
On a weekly or monthly interval, PM Work Orders will be generated creating the Work Orders for the upcoming time interval. Each time a Work Order is generated from a PM record, the CMMS accesses the Job Plan and adds the appropriate Parts estimate information to the generated Work Order. As PM Work Orders are generated, the “available” bin balance for that Part will be reduced by the amount of the estimate - which may result in a stock reorder to replenish the minimal level. For the calculation of Inventory Reorders, a Part reserve acts the same as an issue. Thus, whenever the reorder process is executed, it will automatically place an order for Parts required (by the newly generated PM Work Orders) and have them received and available before the commencement of the work events.
Adding estimates for planned work is the only way that the Reorder process can properly anticipate (and stage) part requirements for upcoming work. As mentioned, visual inventory checks and issue history are only partially effective for determining reorders - and are highly dependent on the Stores manager’s observation capabilities and sense of historical usage rates. Failure to identify Parts that fall below the acceptable minimum balance can result in a substantial procurement cost - generated by spotbuys. After totaling the Purchase Order related costs, expedited purchase pricing and lost time for the maintenance department, the procurement cost of a spot buy might even exceed the cost of the part being ordered. Additionally, a reorder process developed solely on the basis of historical usage statistics has limitations, as some Parts are purchased for specific and non-recurring task assignments, and should not be reordered until another similar Work Order becomes reality. Finally, another ineffective, but widely deployed reordering strategy is the “Replacement Buy” or “Use one – Buy one” methodology. Replacement Buy creates numerous small (and high cost) Purchase Orders, as well as replenishing stock levels well ahead of the required usage time.
3) Reorder Point and Economic Order Quantities
In order to optimize the inventory stock balance and ordering function, let’s consider the employment of two proven Storeroom Management concepts: the Reorder Point and the Economic Order Quantity. The Reorder Point is defined as that point at which the stock balance should trigger the system to automatically generate a reorder document (usually a Purchase Requisition) to replenish the stock balance. Whenever parts fall to or below this Reorder Point, the CMMS should automatically generate new Purchase Requisitions for part replenishment - grouping them by primary vendor.
Initially, the Stores Manager will want to manually populate the Reorder Point field and Economic Order Quantity field values for each Inventory record. However, some of the CMMS products have reports that will assist the Stores Manager in setting the proper values. Factors which drive this calculation include the cost of a stock-out event (e.g., very high for a production critical spare) along with the usage rate and delivery time.
Most CMMS products also provide a standard Inventory Report to assist in the calculation of the Economic Order Quantity. The objective of the Economic Order Quantity calculation is to determine the optimal quantity (number of items) to reorder, whenever reorder is required. This calculation must balance the cost of procurement (Purchase Order cost) against the holding, or carrying cost of Inventory. As mentioned earlier, the Inventory carrying cost has been estimated to equal 20-30% of the outstanding balance. The end-to-end cost of a Purchase Orders in large Organizations is currently estimated to exceed $100 per PO. Thus, if on average, four parts are ordered on a PO and your estimated cost to process a PO is $100, the purchasing cost per part would equal $25. While a $25 order cost (per Part) would represent an insignificant cost addition for Part purchases exceeding $1,000, it would not be economical to execute small Purchase Orders with aggregate costs of less than $50. By balancing the Cost of Capital (inventory carrying cost) against the Part Procurement Cost, the Economic Order Quantity calculation can determine the most cost-efficient quantity of Parts to be ordered.
4) Work Order Reserves and the Available Balance
To minimize the number of stock-out events, the CMMS generally creates a reserve against Part balances for all associated Planned Materials on Work Orders, at the time that the Work Order first reaches a status of APPR (Approved) or higher. Calculation of this reserve against stock balances (a “Just-in-Time” inventory concept) allows the system to evaluate in its reorder calculation all stated Part requirements needed to fill upcoming Preventive Maintenance or other planned Work Orders. The Available balance process will help eliminate those situations where maintenance personnel go to the Storeroom to gather the required Parts for the Work Order tasks, only to find that the Storeroom balance is not sufficient to fully meet the part requirements.
Whenever a reserve is created, the CMMS reduces the (calculated) available balance to the level of the current balance on hand minus the reserved quantity. The Reorder Parts process compares the Reorder Point to the Available Balance, rather than the Current Balance and will reorder Parts, even though the balance on hand appears to be adequate. For example, if the reorder point is 10 and we have 15 Parts on hand in the Storeroom, a reorder would not normally be necessary. But, if PM Work Orders are generated that require the usage of 20 such Parts, we need to reorder these Parts prior to the Work Order commencement date, or the Storeroom will have insufficient stock balance at time of issue. The CMMS will place a “reserve” for 20 units on the Storeroom, making the available balance minus 5 (15 on-hand less 20 required for approved Work Orders). Thus, when the Reorder Parts function is activated, a reorder will occur to replenish the stock balances, even though the physical view of the balance would give the appearance that stock levels are adequate.
5) ABC Analysis
Most CMMS systems also support the concept of Cycle Count and ABC Analysis - to assist with the Inventory physical count process. The Organization can group its parts into categories and determine the proper interval by which an item should be physically counted and reconciled to the system balance.
Those Parts with the highest cost and turnover are valued in the report as “A” items, while the lower extended cost Parts are listed as “Bs” and “Cs”. After determining the count interval (number of days between counts) for each Part, a Cycle Count report can be used to provide a list of all Items that need to be physically counted for the week, month or other desired interval basis. This report evaluates the last physical count date and after adding the default interval as set by the ABC settings, prints an output list of all Items that need to be counted. If the number of days since the last physical count exceeds the interval from the ABC Analysis, then that Part would appear on the Report to be physically counted.
6) Conduct Item ID Normalization (common Part numbering) across all Sites
If your Organization has multiple sites, significant value can be achieved through the standardization of Part Identities across the various sites. First, define what source will provide the Part identification number (e.g. National Stock number (NSN), Universal Standard Products and Services Classification (UNSPSC) etc.). Although some Organizations have centralized on the vendor’s Catalog Number, this is generally not a good choice as your vendor may change, and even the catalog number for that Part may be changed by the vendor to discourage “knock-off” replacements. Once the parts have been normalized, significant cost savings can be achieved, as described below. The decision to “centralize” is made when the comparative transportation costs can be offset by the aforementioned cost savings.
a) Parts can be shared between Sites – Each Site becomes a potential vendor for a site that runs out of stock on a given Item. An objective might be to reduce the overall stock balances at your Organization. Each site can identify and post excess stock items for the benefit of other sites on a common inventory website or distributed spreadsheet. Then, the other sites will order from the site with surplus balance rather than purchasing additional stock from external vendors. This will reduce the internal cost of carrying those Items and will also reduce the spoilage factor, since Items will turn more quickly, effectively reducing average shelf life.
b) Bulk Buying discounts – After the normalization project is complete, it is easy to calculate the total usage rate of that Item across the Organization, which will result in better bargaining power when negotiating price discounts from vendors. Even if shipments must be shipped directly to the purchasing site, there may still be cost efficiencies to consider with the concept of centralized buying. New RFID technology also supports the case for Organizations to eliminate multiple purchasing departments, driving down the cost of Purchase Orders (by including more line items per PO) and centralizing the accounting and reconciliation process.
c) Costly emergency and expedited buys can be reduced. Items that are used on an infrequent basis can be purchased and stored at a Central storeroom and transferred to the requesting sites as needed, rather than having to maintain a stock balance at each site and incur the associated carrying cost.
7) Centralized and Controlled Storerooms
There are several advantages to using a controlled rather than an open storeroom environment. The presence of a dedicated Stores Manager will reduce shrinkage and spoilage, provide a consistent and experienced source for issue and return entry transactions, be available to monitor part balances, stage parts for Work Orders and refine Reorder Points and Economic Order Quantities.
INVENTORY KEY PERFORMANCE INDICATORS
Benefit expectations from using EAM/CMMS products vary from Organization to Organization. These objectives might include reducing the carrying cost of holding Inventory, spending less time looking for parts, establishing more efficient reorder methodology, eliminating duplication of Parts in the database, reducing the number of vendors, leveraging better management data to achieve bulk price discounts and others. Some key performance or benchmarking ratios are included below to assist in the development and tracking of these objectives.
Stock Out Percentage Ratio
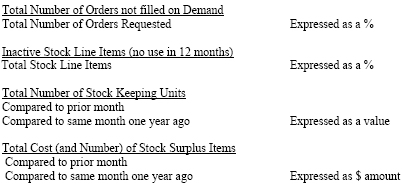
Inventory Turnover Ratio