
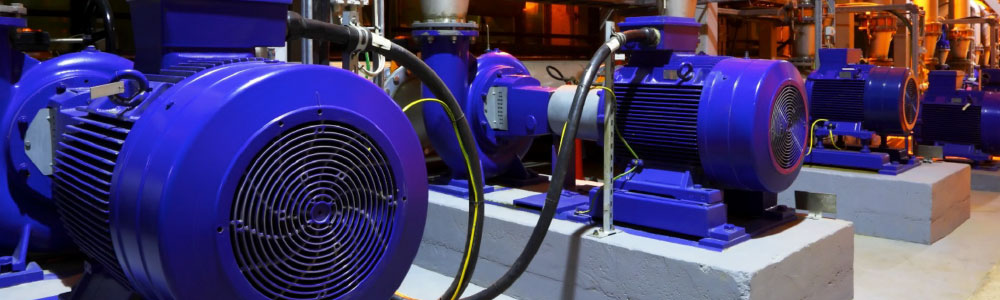
by George Frey
With the many types of maintenance techniques available to the industrial professional, there are many tools to provide a great deal of information on the quality and workings of electric motors and their processes. However, if maintenance basics are ignored, all the techniques are like three drops of rain in a drought - ineffective and futile. If the three basic rules for proper motor operation and upkeep are not followed, why bother investing in advanced technologies to confirm known problems? These three rules are keeping a motor clean, keeping it dry and keeping it tight. Without these rules, fancy equipment simply doesn't matter! This is perhaps the oldest maintenance story of them all.
Keep It Clean
There are many examples of how keeping equipment clean can provide great reliability benefits. Electrical circuits are designed with specific insulation thickness across coils, phase conductors, inside relays, circuit boards, etc. One element that is important for these applications is the concept of electrical leakage and/or tracking. Electricity, analogous to water, always seeks the path of least resistance in any circuit. When there is an insulation system keeping the electrical current flowing where it should be, there is always a certain electrical stress. The electrical stress is across insulated conductors and through cracks, flaws, thin points in insulation, or circuit areas where inadequate clearance exists. This stress forces the current to flow across, over surfaces, or through the electrical insulation. A circuit board in electronic equipment may become extremely heavily packed with dust, hair, or foreign particles and these items deposit on electrified surfaces. The result is a protective system breakdown and failure. Coils and cooling passages in a motor may be plugged with debris. A major culprit is the operation of cooling fans. When filters are inadequate or not present, they can pull large amounts of material right into the interior spaces. Result = In Service Failure.
Keeping these areas clean can be accomplished in several ways. In the realm of electric motors/generators and insulators, cleaning is usually performed when the motor is switched off, locked out and after a visual inspection. It also may be performed based upon hours of operation or years of service. Visual inspection can reveal the presence of surface contamination that may be possible to remedy by one or more of the following steps:
- Vacuuming out the material, which usually prevents you from driving it further into the apparatus.
- Removal with a special cleaning apparatus, such as those on the market that use CO2 pellets or dry ice. This can protect surfaces and interior spaces by removing surface contamination without leaving abrasive residues or leftovers inside the cabinet/enclosure.
- Removal by solvents or wiping away the material with cleaning towels and/or manual removal. Because of their sticky nature, oil and other types of lubricants and grease may have to be dealt with by this method. Large motors or generators may have access panels that can be removed to allow access.
- Removal with compressed air can be used, but special consideration should be taken. You can easily drive foreign substances further into the electrified spaces and aggravate the problem versus mitigating it.
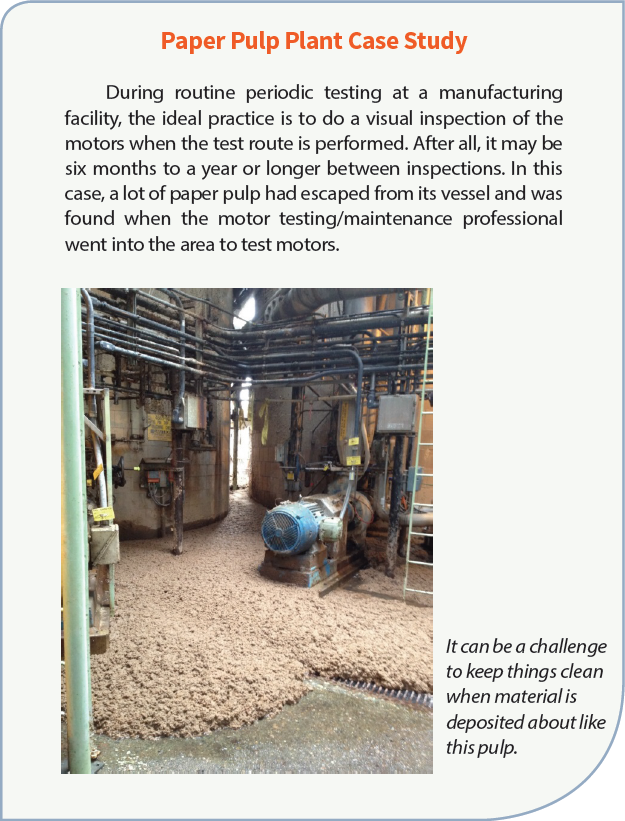

Keep It Dry
The old expression, "water and electricity don't mix," is the main subject for this section. Motors can be, and are, designed to operate properly underwater or in other liquids. When designed to operate underwater, they
will perform flawlessly for many years. The kicker is that not all motors are designed to be operated underwater.
When water penetrates the inside of an electric machine, what happens? Aren't these motors sealed very well with a vacuum pressure impregnation process and other measures, like waterproof seals? The fact is NO! Not all motors are designed to be impervious to water. Extra types of sealing measures drive up the cost of a motor's design and often drive down the manufacturer's profit margins.
A much less expensive type of enclosure is standard. These come in many shapes, sizes and applications. Even totally enclosed fan cooled (TEFC) motors can be penetrated by foreign substances. One of the most common, undesirable substances is water. Water can be absorbed by electric machines in several ways. One way is by condensation. The thermal mass of the motor causes it to lag behind ambient temperature. A motor is always trying to achieve equilibrium with the ambient temperature, but because it has quite a bit of mass, it may not totally catch up. When the motor is cooler than the dew point, water droplets condense out of the air and deposit on the motor, including the interior spaces. Why? Because the interior space's temperature lags behind the furthest, leading to the greatest delta in temperature. Once inside, it is difficult to get out.
Wind-driven water or torrential rain by tropical conditions can be forced through seals. Processes, such as pulp and paper production, generate a lot of wet pulp and other by-products. These can penetrate connection boxes and conduits, be sprayed about by shaft mounted fans, or achieve ingress via weakened or worn seals. The net result is water gets inside and stays inside, especially when drain plugs are clogged by debris.
When a motor is properly designed and perfectly sealed with vacuum pressure impregnation, a barrier to water penetration is established. A defect in the sealing requires at least two flaws in the insulation system to exist for an electrical tracking problem to occur. One flaw would have to be on the insulation on the surface of an electric coil. The second flaw would have to be in the insulation on a second strand or phase, or in the insulation between the electric coil and stator steel, where electric potential exists during operation.
Keeping water out in the first place is usually the most effective strategy. It's better to keep the inside of the apparatus warm and dry versus trying to force out water after the fact. Space heaters or winding heaters are designed in either from the start or retrofitted after real-world conditions affect motor and machine reliability. It is important to check for the presence of current flow through the space heaters periodically. The breaker may be energized, but if the fuses have blown, the heater has burned open, or other problems exist, the heater could be nonfunctional.
Keep It Tight
Items in an electric motor that are susceptible to tightness related problems are the ring lugs under the taped connections at the motor's leads. Periodically taking off-line measurements can help determine if they are operating effectively. In motor testing circles, this is known as the resistance test.
A high quality milli-ohm or micro-ohm meter is used to perform this resistance test. Use an instrument that offers at least 3.5 digits or greater resolution. Less capability means less effective results. These devices are also known variously as ductor, Kelvin bridge, digital low resistance ohmmeter (DLRO), or 4-wire resistance meters. The general idea is that measurements are taken when the motor is turned off, locked out and tagged out. The most time-effective practice is to test from the motor starter through the feed cables to the motor. In this way, the entire circuit can be evaluated relatively quickly. Results can be viewed and interpreted easily by trained maintenance professionals.
Just how much resistive imbalance is too much? Table 1 shows some of the guidelines, developed through experience of many years, for a threephase induction motor. These targets give a good baseline or starting point on how to proceed and urgency actions based on trending results.
Table 1 can be easily interpreted as: The smaller the imbalance, the better!
Summary
The three basics of motor operation and upkeep are vitally important. Without them, the investment in advanced maintenance technologies is moot. By keeping your motors and machines clean, dry and tight, they will always perform better. By investing in technologies that help perform the basics well, a plant's operation will be more effective and outages less catastrophic. After all, the old saying, "keep it simple," remains in full effect.
www.edeinst.com