Table 1: Impact of Maintenance on Availability, Quality and Yield
Compared to lower quartile performers, companies that exhibited upper quartile maintenance practices showed an average improvement in availability of seven percent (81.8% vs. 88.8%) and an increase in yield of five percent (79.2% vs. 84.2%). Put simply, companies that better maintain their assets are able to run their assets more reliably, resulting in greater throughput and more first pass quality products.
But what’s really interesting is the maintenance costs as a function of sales among lower, average and upper quartile companies. Conventional wisdom would hold that to better maintain our asset base, we would need to spend more, not less, on maintenance. But in the Aberdeen study, the opposite appears to be true. Assuming sales are fixed, the average performer showed an 11.5 percent reduction in maintenance costs (20.8% vs. 23.5% as a % of sales) compared to the lower quartile performer, while an upper quartile performer spent a whopping 26.8 percent less (17.2% vs. 23.5%) on maintenance, again assuming fixed sales. It’s clear then that good maintenance costs less!
So how much of this is due to lubrication? Since a large percentage of assets in a plant are rotating or reciprocating, I would argue a lot! But don’t take my word for it. SKF has published a number of articles on the effect of lubrication on bearing life (Figure 1) that seek to answer this very question. Based on SKF’s data, we can conclude that, in a general sense, poor lubrication as defined by the impact of particle contamination, water contamination (corrosion) and inadequate lubrication equates to as much as 63 percent of all bearings failures.
So let’s summarize what we’ve learned here: Companies that perform maintenance at an upper quartile level have 26.8 percent lower overall maintenance costs than lower quartile performers. Of that percentage, 63 percent is due to avoidable lubrication issues. In other words, if your current lubrication practices are in the lower quartile, 18 percent (28.6% x 63%) of your maintenance costs are being consumed servicing the impact of poor lubrication!
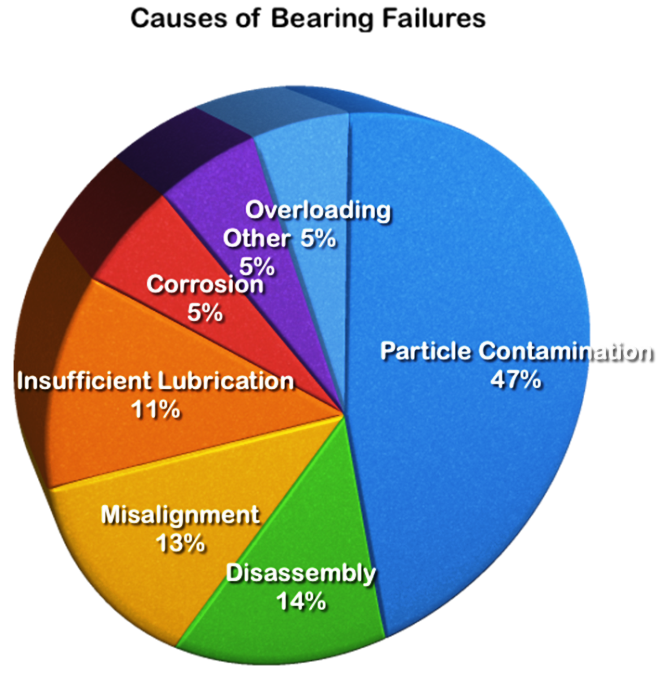

Figure 1: Factors that affect premature bearing failure
This number is pretty consistent with what I’ve seen over the past 15 to 20 years. In my experience, most companies that have yet to focus on lubrication experience losses that amount to anywhere from five to twenty percent of their annual maintenance budget, depending on the level of maturity of their current practices and the industry they serve.
But wait, you say, how can that be so? We spend less than two percent of our maintenance budget purchasing lubricants. Surely this number is too high? The key is to understand the difference between the words “lubricant” and “lubrication.” The lubricant is the product – the oil or grease – we use to lubricate our machines. Lubrication, on the other hand, refers to the way in which we store, handle, dispense, apply and otherwise maintain the lubricant throughout its lifecycle in the plants. It’s our inability to nurture lubricant health and cleanliness, coupled with less than precise application, that causes all the costs in the plant, not the price per gallon or number of gallons of oil we buy each year.
Now let’s look and compare lower quartile lubrication performers with upper quartile performers. Figure 2 shows the typical benchmark for companies in each category. Lower quartile performers are typically characterized by a blasé attitude to lubrication. Lubricants are generally stored either outside or in the main production areas. Few, if any, machines are labeled with the correct lubricant and only a handful of people know which lubricant is used in each machine. For grease lubricated assets, the right quantity and frequency of re-greasing is left to the “experience” of the lubricators, with most bearings over lubricated versus under lubricated. While oil analysis is done to some extent, few in the plant understand how to use the data effectively and samples are poorly taken using less than ideal methods.
Compare this to the upper quartile performer. In this case, the plant has been through a process to optimize the number of lubricants in use and has set aside an area of the plant where lubricants can be stored in an organized, clean work area. Each lubricant is color-coded and all equipment, as well as transfer and top-off equipment, has been properly tagged. The frequency of all lubrication tasks has been optimized and procedures developed that are included in lube routes. Each preventive maintenance (PM) lube contains specific guidelines for precise application, including volumes and lubricant to use, and training is provided specific to each task. Oil analysis is used to make critical decisions on oil changes and other condition-based maintenance tasks, while all critical assets are set up to control contaminants from entering the machine and for removal through filtration.
Of course, all of us would rather be in the upper quartile group rather than the lower quartile group, but how do we get there, and perhaps more importantly, what’s the cost to get there? Using the example shown in Figure 2, the plant workers realized that lower quartile lubrication performance was costing close to $1.62 million per year, an amount equivalent to approximately nine percent of its annual maintenance costs. But to correct these issues, the plant would need to spend almost $350,000 to become an upper quartile performer. In addition, due to the very nature of the plant, which was plagued by a naturally dirty working environment, the plant workers were not at all confident they could eliminate any more than one out of every four lubrication issues. In other words, out of the $1.62 million in lubrication losses each year, they thought they could address $567,000. So what’s the benefit?
Figure 2a: Lubrication benchmark scores, Before
Figure 2b: Lubrication benchmark scores, After
Applying a simple business case analysis (Figure 3), the potential benefits were compelling. Over the next five years, a strong focus on lubrication should help to eliminate close to $1.36 million in lubrication losses, with the up-front investment yielding a stellar 145 percent return on investment. Having accepted the challenge and obtained buy-in from management, the results in Figure 2b, which represent the same plant 18 months later, speak for themselves. While far from perfect, the plant is now well on its way to upper quartile performance and is starting to see many of the financial benefits the business case analysis predicted.