Spindles are one of the most expensive and sophisticated rotating components on the planet. They rotate at super high speeds with fits and tolerances 10 to 20 times what is required on other rotating devices, such as pumps or motors. If there ever were machines that needed to communicate their health and activity it would be spindles.
What Is M2M?
{image:1}
M2M or machine to machine is one of the fastest growing segments in technology. M2M solutions can connect millions of devices, like machines, heart monitors, cars, appliances and buildings. Basically, nearly anything with sensors that can report device-specific information back to other devices or computers can be connected using an M2M network.
Based on collected data, M2M can start tasks and give important instructions without human intervention. According to a 2013 article in Forbes, M2M is currently a $24 billion market and predicted to be close to $100 billion by 2017.
How to Listen to What Machines and Spindles Are Telling Us
Combining today’s latest sensors and wireless and mobile devices, it is now possible to listen to machines using M2M. This is all done without causing any incomplete or lost data. A manufacturing plant can either permanently mount or manually collect vital sensor data wirelessly from the machine and spindle. Manufacturing companies can rely on International Organization for Standardization (ISO) standards for predictive decisions. However, vibration and ultrasound ISO standards are useless without data to apply to them. M2M connects the data to the science used to develop these standards.
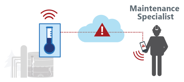

Several types of vibration and ultrasound sensors exist that can talk to a tablet or phone and transmit this vital data to the Cloud. Permanently mounted sensors can talk directly to the server without using mobile devices to transmit the data. Sophisticated software applications make it simple to collect, analyze and export this spindle health data.
The M2M network then pushes down an alert of an approaching failure to the people that need that information. Correcting the degradation prior to significant deterioration of the spindle or equipment saves production costs, crucial downtime and expensive run to failure spindle rebuilds. The M2M network also contains a sophisticated engine to diagnose what the problem is, extending valuable time to correct before the failure becomes catastrophic.
Not a New Technology
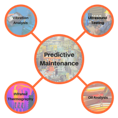

Predictive maintenance on spindles, pumps and motors is nothing new. Highly trained professionals have used vibration and ultrasound as a proven method to manually collect and analyze data for over 20 years. Most production facilities have this capability or contract it out to a predictive maintenance company. The typical audit cost was $30 to $60 for one machine recording and the analysis took seven to 10 days.
What Is New
The technology breakthrough is the M2M communication. It's all about delivering data to the right destination at the right time to make the right decision. Data can be collected and analyzed in seconds, rather than days.
How It Works
A production facility that adopts this technology simply uses a permanently mounted or portable sensor to collect and analyze data on a predetermined schedule, such as hourly, daily, or monthly, as conditions require. The manual samples are conducted with a magnet-based wireless sensor. Using a wireless sensor makes it possible for machines to run with safety doors closed and limits interference with production. The permanently mounted systems can sample several times a day, if necessary. The data then gets pushed to the secure server for analysis and storage. The server has its own software and programming. Server side alarm levels and the diagnostic engine communicate alarms and make suggestions of specific problems, such as imbalance, misalignment, looseness and early bearing failure. The server can be set to send e-mail or SMS messages when there is a problem.
Other Advantages
Now that the data is viewable from anywhere on any platform with an Internet connection, other specialists can view and analyze the data. This allows for one specialist to handle multiple facilities without having to travel or collect the data. It further allows many professionals from around the globe to collaborate on a specific problem. Several professionals can log in and view the same data at the same time.
The raw data also can be downloaded from the server for an analyst to manipulate and analyze in a custom, natively run Windows® application.
M2M is the best of both worlds. It gives you the data at the right time and in the right place to make the right decision. This is what the M2M solution is all about.