Sample Calculation of Batch Plant OEE
Continuous plants tend to be relatively straightforward for setting up an uptime measurement. With some minor modification to the model of Figure 1-5, losses can generally be routinely accounted. Measuring OEE in batch and discrete plants, however, is often more difficult, partly because they generally have more discrete manufacturing steps, some of which feed multiple finished products, partly because they generally produce a larger number of products, partly because the logistics of doing the calculations is just more complex. Using the technique previously described will help to focus the measurement effort, but to illustrate the method, let's take an example from Beta's Hemp Hill plant, a batch operation, which had been measuring the following performance indicators at one of its plants for one of its key production lines:
1. Availability. Although the term being used was uptime, or any time the line was up and running, availability is a more accurate characterization using our model, because it did not include the effects of rate, quality, or other losses. And, because downtime was accounted separately, this number also excludes scheduled downtime.
2. Downtime. This is the time when the equipment is down unexpectedly, and is synonymous with unscheduled downtime losses in the model.
3. Changeover time. This is the time for product changeovers. In the model this was part of the changeover and transition losses.
4. Clear/clean/material changes. This is the time for clearing, cleaning, and setups. This also could be part of the changeover and transition losses.
5. No-demand time. This is the time during which the equipment is not in use for production and can be used to help determine asset utilization rate. It also apparently included scheduled downtime for the following:
(a) Scheduled PM and repairs. This time would normally be characterized as scheduled downtime in the model, and subtracts from no-demand time.
(b) Special and planned projects. This time is not considered by the model shown, but could easily be made a part of the model as a separate category.
6. Quality losses. This was broken into several categories, one of which was product quality losses due to equipment failures.
7. Process rate losses. This was available, but there was some confusion about the industrial engineering standards being applied, as compared to ideal rates that required additional analysis.
8. Other. There were also other losses that did not directly fit into these categories, but needed an accounting, e.g., break times, utility failures, startup losses, etc. These losses may be acceptable under the current business structure, but should be identified separately.
Note: Convincing everyone to account for every hour the line was not operating at peak rate, and the related causes, for loss accounting, was a difficult process. Excuses were numerous, thwarting the effort to assure that there's "no place to hide" poor performance. Ultimately, the value in the measurement was seen, and a measurement system put in place to make sure production lines were being used effectively; and that additional information was available to make tactical and strategic decisions for process improvement.
The calculation in Table 1-1 was applied to a line that essentially operated on a 5-day, 1-shift basis, with the following information being "normalized" to a 24-hour day. The basis for the calculation included:
1. No-demand time was reported at 63%, but this also included scheduled downtime for PM, repairs, and projects. This was reported to average 1 hour/day, although the work was actually performed in much larger blocks of time.
2. Quality losses were reported at 1%.
3. Process rate losses were estimated at about 10%. The peak demonstrated sustainable rate was reported at 200 units per minute, but the line was reported as typically running at 150 units per minute, or a 25% "loss" from ideal. However, this required further review with industrial engineering. A nominal loss of 10% loss was used.
4. Changeover, cleaning, setup, etc., losses were reported at an average of 31%.
5. Breaks were reported at 40 minutes per run. Note: No one is suggesting that people shouldn't be allowed to take breaks. The model accounts for all time related to all production activity. Once the losses are accounted, then business decisions are made as to their acceptability.
Using these data, an average day was broken into two parts-63% of 24 hours for "no-demand" and 37% for production activities, including maintenance, or 15.1 hours for no-demand, and 8.9 hours for production. However, because an average of 1 hour/day was reported for PM/repair/project activities, we subtracted 1 hour from no-demand and added it to production activities, making the average production time (including maintenance) 9.9 hours, and no-demand 14.1 hours.

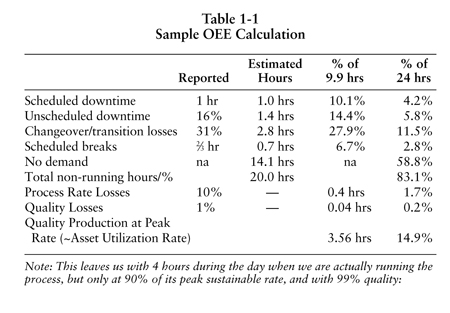
Nakajima, who developed total productive maintenance (TPM) principles that include the measurement of OEE, might disagree with this approach, because he apparently allows for an indeterminate time period for scheduled maintenance. In this example, we're following a more restrictive application of OEE principles, which accounts for every hour of every day, and improving all business activities associated with the entire production function, including maintenance. Every production function must make these kinds of decisions, and then use the measurement tool for improving its processes, and not necessarily as an end in itself. This approach gives the calculations shown in Table 1-1, and depicted graphically in Figure 1-6.
Using different scenarios for OEE and asset utilization calculations gives:
Further, at Beta's Fleming plant, also a batch operation, which supplies material for the line previously described, some additional difficulty was being experienced in developing an OEE measurement, primarily because the plant used a fermentation process as part of the production process. How do you measure peak sustainable rate on a fermentation process? Rather than do this per se, after reviewing historical production data, Beta found that for the key process, which had already been mapped, a cycle time of some 100 hours (e.g., the average of the three best runs) was an ideal run for the fermentation process. We also found from the data that a peak yield of 92% was achievable. With this information the OEE measurement was remodeled:
In this example, the production process ran at 55% of the ideal. If 85% is considered a "world-class level of performance," then the estimated loss is 30%. This could in turn be assigned a $ value for the production process and product, and a value estimated for the losses from the ideal. Some observations on this method:
1. It requires that maintenance and production work as a team to define more clearly the losses from ideal. For example, the 80 hours could be because of poor practices for setup, cleanup, PM, production, etc.; likewise for yield performance. The key here is to identify the losses from ideal, and to work hard to eliminate them. We might also find that in a given circumstance 55% is actually reasonably good.
2. This process could be used to calculate a weighted average for all production using this process stream, and could be combined with other production processes to calculate an aggregate weighted average of manufacturing performance.
3. A quality rate of 100% was assumed in this example, or alternatively that quality was included in the yield determination. In this process the batch was either good, or not, and in the latter case the quality was 0%.
4. The calculation does not include the effects of low (or high) asset utilization. For example, if this process was only used during 50% of the month, then the effective asset utilization rate would be 50% of 55%, or 27.5%. Both measures are useful in that one gives a measure of the effectiveness of the production process itself; the other a measure of the business use of available production capacity. Both measure the prospective business opportunity associated with the product being made.
Discussion of Sample Measurement
The previous discussion suggests substantial opportunity for production process improvement, or market share improvement, or production line rationalization, or some combination. However, the decision making process is subject to additional discussion, because not all factors that lead to business decisions at Beta or in any given organization are included in this approach. For example, if Beta decided to rationalize production lines at Hemp Hill (mothballing, decommissioning, etc.), it would also have to consider whether or not the remaining lines were capable and/or qualified under current regulatory, corporate, and engineering requirements to run the products that would otherwise run on the decommissioned line. Qualifications of operators, anticipated products, etc. would also have to be considered.
In the short term Beta used the given information to make tactical decisions about improving production practices. If Beta could eliminate unscheduled downtime, and reduce scheduled downtime for PM and repair (without deleterious impact on the equipment) by half, and if changeover and transition times could be cut in half, then on average production times could be reduced by 33%. Additional improvements could also be made in assuring running the process at peak rate during a production run, and assuring minimal quality losses.
After considerable review, it was finally concluded that about the best OEE achievable under present circumstances for the Hemp Hill plant was 50-55%. At the present time, nine people are operating this line per shift. Theoretically then, the same quantity of product could be produced with 6 people. At a nominal cost of $50K per year per person, this reduces costs per year by $150K. It is understood that theory rarely equals reality, and making linear assumptions is not always valid, because systems tend to be non-linear, but at least Beta now has a basis for making decisions about production planning and rationalization of existing capacity.
Strategically, Beta will use this information to rationalize production capacity. As certain plants improve performance, production requirements will be transferred there, assuring maximum performance. If markets materialize as expected, production capacity will be brought to bear using existing capital assets. If markets do not materialize, then certain production facilities will be decommissioned, at least until they are needed again.
A Special Case-Beta's Dwale Plant
At Beta's Dwale plant, a continuous process plant, they had developed an understanding from a benchmarking effort that 95% uptime was a world-class level of performance for their type of plant. They determined their peak demonstrated sustainable production rate based on their output during their best-ever 3-day continuous performance. However, on further review, they found that there were nonlinear variables for fixed and variable costs that would influence their decision about what the optimal targeted uptime should be. They found that variable costs in the form of energy and certain feed material increased sharply above about 87%, leveling off thereafter, but then increasing again above 95% (see Figure 1-7). They also found that maintenance costs increased sharply between about 90% and 95% of peak demonstrated rate, primarily due to fouling and choking of the process. This fouling also affected their ability to keep the process on line, reducing their uptime due to additional maintenance. After some analysis, they concluded that their best sustainable performance would be running the plant between 90 and 95% of peak demonstrated rate. Operating the plant at this rate, they felt they could achieve an uptime of 90%, which was considered to be their best achievable and sustainable production rate. It was just not realistic, nor cost effective, to try to run the plant at 100% of its demonstrated rate and still expect to achieve an uptime in the range of 95% without significant additional engineering and capital investment.
Some sites, particularly large, integrated process sites with multiple plants may have structural constraints imposed upon any given plant. For example, environmental discharge constraints may limit one or more plants' ability to operate at peak rate. Business constraints and/or feed stock supplies from upstream plants may force a downstream plant to operate in a less than optimal mode. For example, at one of Beta's downstream plants, some chemical reactor vessels were operated to take feed stock of one kind, while the other vessels were operated to take feed stock of another kind, a kind of buffer for fluctuations in site operation. However, no one ever reduced the peak demonstrated rate to account for this, or counted this as a loss attributed to the site operation. Structural constraints imposed by business or operating conditions must also be accounted in the measurement of uptime or OEE.
Hiding Behind Excess Capacity
(The Hidden Plant)
Many managers take the position that they couldn't sell all that they could make. Whether this is true or not is problematic. For example, if they could reduce their unit costs and improve delivery performance, they might be able to immediately gain market share, and sell all they could make. In a strategic sense, however, those underutilized assets represent opportunities such as increased business volume, and return on net assets, but it may be in the rationalization of assets. Hence the previous model.
Many managers use excess capacity as an excuse for poor or sloppy practice. For example, if a plant is operating at 60% asset utilization rate, when world class is 90%, the plant may have another 30% of sales opportunity, at a lower unit cost of production; or could potentially make the product for substantially lower costs, improving profits, and without incremental capital investment. Some managers have been known to use this 30% "reserve" to make sure they can meet delivery schedule, incurring additional costs associated with work-in-process buffer stocks, higher levels of staffing, overtime, scrap product, higher operating and maintenance costs, etc.
Using excess capacity as a "reserve" is the wrong way to do business. It almost always assures no better than mediocre performance, and sometimes worse. Costs incurred are excessive, often extraordinary. Excess capacity often masks poor practices, which increases unit costs, reduces profits and market share, and can result in capital expansion for needed capacity, rather than optimal use of existing assets. These things make companies less competitive, and can ultimately lead to their demise. For example, suppose a company is operating a 5-day, 3-shift operation. With this in mind, our asset utilization rate can be no better than 15 ÷ 21 = 71%. Further suppose that when we measure our uptime or OEE during the 15-shift period, we find that we're operating at 57%, a fairly typical rate when all losses from ideal are accounted. If we could get this rate to 85% or better, this would represent a 50% improvement. We would find that we could produce the same product during a 5-day, 2-shift operation. In the short term we save a great deal of money. In the long term, we have incremental capacity without incremental capital investment.
When excess capacity does exist, it should be viewed as opportunity waiting, and used strategically to increase market share, and over the long haul to maximize return on assets and profits. It should not be used as an excuse for sloppy practice. At Beta's Salyersville plant, a large, continuous process plant, the following conversation occurred with the maintenance manager:
Benchmarking Consultant: "How much does downtime cost you?"
Maintenance Manager: "Nothing, we have 8 lines, we only need 5 to meet current market demand, so when one line shuts down, we start up one of the spares, and keep on producing. So it doesn't cost us anything."
Benchmarking Consultant: "So you're carrying sufficient staff to operate and maintain 8 lines, or at least more than 5?"
Maintenance Manager: Pausing, "Well, probably more than 5."
Benchmarking Consultant: "How about spare parts, are they sufficient for more than 5 lines?"
Maintenance Manager: "Well, probably more than 5."
Benchmarking Consultant: "How about overtime, do you spend considerable overtime to make repairs, or switch over the lines? These failures don't usually occur at a convenient time do they?"
Maintenance Manager: "Well, no they don't, and we probably spend more overtime than we should."
Benchmarking Consultant: "How about collateral damage, do you ever have any because of running a machine to failure, rather than catching it long before it gets so bad it becomes a crisis?"
Maintenance Manager: "Well, probably . . . well, yes we have, on line 3 last week we had a heck of a mess because of a catastrophic failure."
Benchmarking Consultant: "How about scrapped product, or reduced quality, does that occur when you have to switch lines and lose product in process?"
Maintenance Manager: "Well . . ., almost always."
Benchmarking Consultant: "How about inter-process flows, does the downtime on the failed line result in delays or disruptions in upstream or downstream processes, requiring considerable effort to realign the plant?"
Maintenance Manager: "Well . . ., usually." (At this point, the wind was clearly out of his sails. He was even a bit agitated.)
Benchmarking Consultant: "How about management attention? Don't events that require a switch-over result in distracting management attention away from other issues that could add more value to the corporation?"
Maintenance Manager: "Probably."
Benchmarking Consultant: "Look, I'm not trying to be hard on you, or anyone for that matter. I try to help people see things from a different perspective, to help them identify opportunities for improvement, so they can make more money."
Maintenance Manager: "I think we have several opportunities here, don't we?"
Benchmarking Consultant: "It sure seems that way, but we've just taken the first step in capitalizing on those opportunities. Let's look at how improved processes and practices can help eliminate some of these costs." (We went on to review a strategy to help change the plant's culture from being repair focused to being reliability focused.)
If we have 8 lines, but only need 5, why not operate the plant as if we have only 5, using staff, spares, overtime, etc. at world-class levels of performance to maximize profitability for those 5 lines? Alternatively, why not operate a production line at a world-class level using a 5- day, 2-shift operation, vs. a 5-day, 3-shift operation? What about the "excess capacity"? Strategically, those represent increased market share and improved profits (not excess capacity per se; or, it represents the opportunity to rationalize assets). Once we get the plant to operating reliably at superior levels of performance for 5 lines-striving to be the low-cost producer in the market-then we can position our products to increase market share, while still making a healthy profit, expanding our marketing and distribution efforts, and bringing those additional lines on as we need the product for our newly gained customers. In doing so, we maximize return on assets, profits, and share price.
Differences Between Batch and Continuous Manufacturers
Many have noted that there are substantial differences between the way in which batch and continuous manufacturing plants are operated, most observing that you really cannot expect a batch or discrete plant to be operated like a continuous plant. Agreed. However, these differences should not be used as an excuse for sloppy practice. One of the fundamental questions still remains-What is ideal performance, and how far is my plant from ideal? This is regardless of the type of plant.
Data collected from some 300 manufacturing plants-batch/discrete, continuous, and combination-show that the differences in performance, as viewed by the people who operate the plants, are striking. As described in the next chapter on benchmarking, people who work in continuous manufacturing plants report that their practices, when compared to a best practices standard (one that results in higher uptimes, lower unit costs, and better safety) are almost always better than the practices in a typical batch or discrete plant. The reasons or this are uncertain, but it is theorized that the batch manufacturers always believe they can make up for lost production with the next batch, not recognizing that time lost is lost forever. Whereas the continuous manufacturer's mistakes are almost always highly visible, principally because of the very nature of the plant-there are fewer places to hide when a continuous plant suffers lost production. When a batch plant does, this appears not to be the case. More detail on this issue, as well as key success factors, and the differences between batch and discrete plants is provided in Chapter 2 and Appendix A.
Lean Manufacturing, Six Sigma, and Focused Factories
In recent years, Lean Manufacturing, Focused and Agile Factories, and Six Sigma Methods have come to the forefront as models for manufacturing excellence. Below is a discussion of these principles or methods.
Lean Manufacturing
Womac, Jones and Roos' book, The Machine That Changed the World (8), was an interesting discussion of the history of what came to be known as Lean Manufacturing, but it was scant on the details of the methods for achieving it. More recently, in Running Today's Factory9, Charles Standard and Dale Davis have provided a clear methodology which integrates lean manufacturing concepts and factory physics principles together in a very practical way, and whose points of emphasis are: a) reducing process variability, b) reducing system cycle times, c) minimizing delay times between process, and above all, d) eliminating waste in the manufacturing process and supply chain, from receipt of order to delivery of product and payment. Indeed, measuring system cycle time, from receipt of order to delivery, and minimizing delay times between processes, is essential for discrete manufacturers to assure their competitive position, and as they point out, much more important than the "efficiency" of any given machine.
One of the major issues which needs to be addressed is the understanding (or lack thereof) that Lean Manufacturing is not about head count reduction. Lower head count per unit of output is a consequence of applying lean principles. And yet it seems that many managers even at very high levels still believe that reducing head count will result in a lean company. There is a huge body of evidence which indicates that head count reduction will not provide sustained improvement. An analogy which may help is to recognize that "lean" and "fit" are two very different concepts. Olympic athletes are "fit", which would typically give them a "lean" appearance. Anorexic people are "lean", but hardly "fit", and we certainly don't want an anorexic company. So, Lean Manufacturing is more about the concept of being lean though being fit, not the other way around. Moreover, if you reduce the resources available to your system without changing its basic design, then system performance will likely decline.
Lean Manufacturing is more a philosophy or condition than it is a process. For example, when you're lean, you:
• Have minimal inventory, WIP, and raw material
• Have high on time delivery performance
• Are typically operating in a "pull" mode-you only make enough to fill near-term demand
• Make more smaller batches and have less longer runs (a bit counter-intuitive)
And you use techniques such as:
• One piece flow, quick changeover, takt time10, and mistake proofing
• Measuring system cycle times and delay times, and managing them more effectively
• Minimizing the variability of your processes
• Having very reliable equipment through proactive maintenance
If you don't have reliable processes and equipment, it will be very
difficult to be lean.
You need that extra "stuff"-buffer stocks, spare parts, spare equipment, etc., to manage your un-reliability and still meet your customer's demands. It's hard to be lean when you're broken. So, get the basics of good reliability practices in place to assure good lean manufacturing performance.
Further, as we've seen reliability is not just about maintenance. Superb reliability requires excellence in design, procurement, operations and maintenance. MCP Consulting, in its work with the Department of Trade and Industry in the United Kingdom, observed that some 40-50% of equipment breakdowns were related to poor operating practices; 30-40% were related to poor equipment designor condition, and 10-30% were related to poor maintenance practices.As shown in Figure 1-8, several Fortune 500 manufacturers, including several of Beta's plants, have reported that some two thirds of all production losses as measured against ideal are not related to equipment downtime, but rather due to rate and quality losses, changeover losses, no demand losses, lack of raw material, poor utility supply, etc.; and that of the remaining one third that is due to equipment downtime, some two-thirds of that are a result of poor operating or design practices, not poor maintenance. This leaves maintenance in control of only about 10% of the production losses from ideal. Clearly, if you want high performance, the first order of business is to assure excellence in operating practices.
Six Sigma
In their book The Six Sigma Way11, Pande et al. provide the following model for applying Six Sigma principles. Six Sigma is a statistical term which characterizes your quality having less than 3.4 defects per million for a given product or process specification. However, Six Sigma has become a methodology for reducing the variability of processes such that the result is greater quality and consistency. It stresses simultaneously achieving seeming contrary objectives:
• Being Stable, and Innovative
• Seeing the Big Picture, and the Details
• Being Creative, and Rational
Similar to Deming's "plan, do, check, act", it applies the DMAIC model-define, measure, analyze, improve, control-to core processes and key customers.
Principal themes include:
• Focus on customer satisfaction/success
• Data/fact driven management
• Process management and improvement
• Proactive management
• Boundaryless collaboration
• Drive for perfection, but tolerance for failure
Principal tools/methods include:
• Continuous improvement
• Process management
• Process design/re-design
• Customer feedback
• Creative thinking
• Analysis of variance
• Balanced scorecards
• Design of experiments
• Statistical process control
• Improvement projects
One of the cautions regarding the use of Six Sigma is-don't start with a "nerdy" monologue on SPC or statistical analysis-this damages its credibility, particularly with the shop floor. According to David Burns of SIRF Round Tables in Australia, the first step in applying Six Sigma principles is to address the obvious and make sure good basic practices are in place, the second step is to standardize your processes, and finally, the third step is to perfect your processes. This is depicted graphically in Figure 1-9. Of course applying the tools described above in doing this is a good approach. The point of emphasis here, however, is that achieving step one-getting good basic practices in place first, including excellence in maintenance and reliability, is essential for success.
Focused Factories
The concept of Focused Factories has also been offered as a strategy for assuring manufacturing excellence.12 While the concept of focused factories has been well received and has shown considerable improvement at some of Beta's plants, it should be emphasized that this has typically been at their batch and discrete plants, with the concepts being more difficult to apply at their continuous plants. Further, even at their batch and discrete plants, what has often resulted within the maintenance function is that "the firefighters have only moved closer to the fires, and little is done to eliminate the cause of the fires." Improved equipment reliability and performance rarely results from this approach, nor is it expected to adequately support related strategies such as agile and lean manufacturing, which require high reliability and performance. Again, It's hard to be agile or lean when you're broken. Further, improving production flows and minimizing floor space can lead to substantial production improvement, but has also led to inadequate pull space, lay-down area, etc., for maintaining equipment, at times resulting in increased costs and longer downtime.
Certainly plant layout and production flow are critical, but they must fully consider reliability, maintenance, and operating requirements. The view by some focused factory advocates that having backup machinery and equipment is a solution to capacity and production problems does not appear to be well founded. Additional equipment is not normally the solution to poor maintenance practice, as it increases the need for additional capital, as well as operating and maintenance expense, etc. Getting to the root cause of equipment failures and improving maintenance practices is a much better approach. Beta has found that properly applied, maintenance management systems are not a burden, but a key tool for equipment reliability, and that work orders are an essential element for planning, managing, and generally minimizing maintenance work requirements. They have also found that most often a hybrid organization of some decentralized (focused resources), and centralized resources works best at most of their operations.
Summary
As best practices are implemented at Beta International, fewer people will be required to achieve the same production goals. However, Beta decided to show loyalty to its employees and to work hard to avoid downsizing, and has pledged that it will use the following techniques to minimize that possibility:
1. Not replacing workers lost through attrition: resignations, retirement, etc.
2. Reduced contract labor, using employees even when retraining is required.
3. Reduced overtime. A smaller paycheck is better than no job.
4. Voluntary reductions in staffing.
5. Termination of poor performers.
6. Reallocation of employees for new, or different jobs, including any retraining.
7. Finally, and by no means least, reallocation of resources to handle expanded business volume.
World-class business performance requires excellence in and the integration of marketing, manufacturing, and R&D, and that we know what excellence is by measuring it; it requires that we know what it means to be the low-cost producer of our products, and how to achieve and sustain that position; it requires that we understand how our manufacturing performance relates to our return on net assets and general corporate performance; it requires that we understand our losses from ideal and manage them; it requires that we put in place a reliability process for manufacturing that assures that we design, buy, store, install, operate, and maintain our manufacturing assets in a superb way. Finally, it requires that we integrate our marketing and manufacturing strategy in a comprehensive way, focused on world-class performance.
Each of us sees light (and information) according to where he stands relative to the prism. Beta, like most major manufacturing companies, tends to operate each business function as if each one were the only "color" in the rainbow, and works hard to optimize each function, missing the continuous, interrelated nature of all the issues. Because of this, they only "see" things from one distorted perspective. Although they have tried to optimize their processes, they have always optimized at the sub-optimal level. If Beta is ever to find the proverbial gold at the end of the business rainbow, they must recognize that this continuum of issues must be fully integrated and each recognized for its contribution, and interrelationship. Bob Neurath must instill a common sense of purpose for world-class performance among all within Beta International-world-class performance and the gold at the end of the business rainbow. This involves focusing on reliability and capacity improvement for the existing assets, understanding and integrating manufacturing with markets and their sensitivities, measurement of uptime and losses from ideal, and understanding and applying best practices in an integrated way in the design, buy, store, install, operate, and maintain continuum for manufacturing excellence.
References
1. Skinner, W. "Manufacturing-The Missing Link in Corporate Strategy," Harvard Business Review, May/June, 1969.
2. Hayes, R. H. and Wheelwright, S. C. Restoring Our Competitive Edge:Competing Through Manufacturing, The Free Press, New York, 1984.
3. Hayes, R. H. and Pisano, G. P. "Beyond World Class: The New Manufacturing Strategy," Harvard Business Review, January/February, 1994.
4. Hill, T. Manufacturing Strategy-Strategic Management of the Manufacturing Function, Macmillan Press Ltd., New York, 1993.
5. Turner, S. An Investigation of the Explicit and Implicit Manufacturing Strategies of a South African Chemical Company, Master's thesis, The Graduate School of Business, University of Cape Town, S.A. December, 1994.
6. Flynn, V. J. "The Evolution of Maintenance Excellence in DuPont," a presentation sponsored by E.I. duPont de Nemours & Co., Inc., by arrangement with the Strategic Industry Research Foundation, Melbourne, Australia, August, 1996.
7. Fraser, A. Reliable Manufacturing Associates, Warrington, Cheshire, England, 1997.
8. Womack, J.P., Jones, D.T., and Roos, D. The Machine That Changed the World, The Story of Lean Production, HarperCollins Publishers, New York, 1991.
9. Standard, C. and Davis, D. Running Today's Factory, A Proven Strategy for Lean Manufacturing, Hanser Gardner Publications, 1999.
10. Takt time is a constant pace at which to operate the plant to exactly meet market demand.
11. Pande, P.S., Neuman, R.P., and Cavanaugh, R.R. The Six Sigma Way, McGraw-Hill, New York, 2000.
12. Harmon, R. L. Reinventing the Factory II, The Free Press, New York, 1992.