
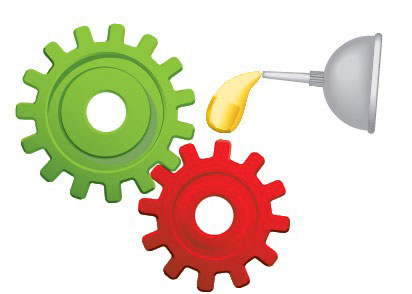
When executing a precision lubrication program, these "rights" should be the primary objectives, and ensuring the objectives are met is largely a matter of optimizing lubrication PM activities. Once all lube points have been identified, placed in a proper equipment hierarchy and assigned a proper lubricant specification, the next step is to identify the appropriate lubrication tasks and the optimum frequency for each. The key term here is optimum. Simply doing more lubrication tasks, such as more grease applications or more frequent oil changes, doesn't necessarily equate to better lubrication or better anything. On the contrary, it can actually be harmful in many cases. Over greasing bearings is a common cause of premature failure and performing unnecessary oil changes proportionally increases the chance for errors, such as leaks, improper fill levels, or cross contamination of lubricants.
The term "PM" can be somewhat ambiguous in that it means different things to different people, including preventive, predictive, proactive and even plant maintenance, but for this discussion, it means planned maintenance, which includes all of the above. Most lubrication PMs can be conveniently categorized into four categories: oil applications, grease applications, oil sampling/ analysis, and routine lubrication inspection PMs. Determining the optimum frequency for some of these activities is relatively easy, for others somewhat rigorous, and a few are practically impossible because they require the application of experience and intuition. On the bright side, making most of these decisions is like throwing horseshoes or hand grenades, just getting close is usually good enough.
Oil Changes
There are many factors that affect oil life in lubricated machinery. The lubricant type, quality, relative sump volume, cleanliness, application type and operating temperature all play major roles in determining the useful service life of lubricating oil. These factors are what allow oil to last for many years in some applications, but only a few days in others. This becomes clearer when you consider that oil in a passenger car typically lasts about 50 to 100 operating hours, while oil in a large turbine might last five years or more. The difference is that the internal combustion engines present an extremely harsh operating environment for the oil in terms of temperature and contamination levels,combined with a very small oil sump relative to the circulation rate. The turbine system, on the other hand, has a large sump and provides relatively mild operating conditions.
Oil changes for systems with large volume reservoirs should be almost always performed based on condition as indicated by oil analysis; so in this case, the sampling frequency is the primary concern. For those machines where oil analysis is not available, the optimum frequency must be estimated based on the available information starting with the recommendation of the OEM. When it doubt, the OEM recommendations will normally suffice, but this may not be optimum. Because equipment manufacturers don't normally know the type of service or quality of lubrication provided for a component, they must err on the side of caution and assume poor conditions. Therefore, they will typically recommend a very conservative oil change frequency. A typical OEM recommendation for oil changes on a bath lubricated gearbox is six months, but with good contamination control and oil quality, the actual oil life is usually more like 12 to 24 months. For programs that practice good contamination control and use high quality lubricants, these frequencies should be determined experimentally. A good way to do this for assets not normally included in the oil analysis program is to test a representative sample of similar components to determine the actual useful service life of the oil and make that the standard PM frequency. To be safe, it is a good idea to back off of the experimentally determined value by an appropriate engineering factor. When trying to maximize oil change frequencies, it is important to remember that the penalty for overextending oil drains can be fill) high. Overextended or oil drains don't normally lead to catastrophic failure, but the byproducts of oil degradation can lead to ongoing problems with sludge, deposits and curtailed life for subsequent oil changes due to additive depletion caused by the "bad" oil that remains behind. The point is to get most of the life from the oil, not necessarily all of it.
Grease Application
Grease application frequency is an item that many people get wrong. In most cases, they tend to over grease or not grease at all. Just as with oil, useful grease service life can vary tremendously. A bushing on a wheel loader may need to be greased several times a day, while an electric motor bearing in a cool environment may run for many years without needing new grease. Unlike oil life, grease life usually can be predicted fairly accurately using common methods, making this part of the PM optimization process relatively easy. This is fortunate because it is usually difficult to find OEM grease recommendations for most equipment other than electric motors. Because electric motors are particularly sensitive to over greasing, one should almost always follow OEM recommendations, which tend to be more conservative than other bearing re-grease frequency calculators. For all others, calculators like the one published by SKF1 work well for most applications. Using this method, one needs to know the size, type and speed of the bearings to determine the correct grease replenishment frequency. It is, however, recommended to make adjustments to these values based on the temperature, orientation, vibration levels and the likelihood of particle and moisture contamination. In extreme cases and in slow speed applications, these actually become the predominant factors. For more information on this complex topic, refer to the referenced article by Dr. Mark Barnes2.
Figure 1: Re-grease interval calculations (Reference SKF Group/Des-Case Corporation Practical Machinery Lubrication Training Course Manual)
In most cases, this exercise will lead to fewer grease application activities, freeing up time for other PMs that may have previously been neglected.
Oil Sampling and Analysis
All too often, maintenance programs focus on sampling more equipment rather than sampling at the optimum frequency. When optimizing sampling frequencies, the best way to start is to decide which machines should be sampled. It's better to do good oil analysis on the most critical assets than to perform ineffective oil analysis on all of them. There is no universal formula for determining oil sampling frequency, but most experts consider monthly sampling to be optimum for critical machinery.
When making these decisions, it is important to consider the objectives of the oil analysis program. If the only objective is to perform condition-based oil changes, the sampling frequency should be determined relative to the lubricant's expected service life, which goes back to OEM recommended oil change frequencies. In most situations, this is not the only objective, or even the most important one. The real value of oil analysis is its ability to serve as a proactive condition-monitoring tool, allowing for the detection and quantification of particle contamination, moisture, other lubricants or fluids and lubricant condition. In addition to the criticality of the asset, one must consider how the machine would be affected by an unacceptable amount of contamination and the likelihood of a contamination or other abnormal condition. If oil analysis is used as a predictive condition-monitoring tool, the biggest consideration is the likely time period between detection and failure. Obviously, the sampling frequency must be shorter than this period to be successful.
The best approach to this problem may be to employ a formulaic method similar to failure modes and effects analysis (FMEA). This process will allow each of these issues to be pseudo-quantified and gives each asset a numeric score that reflects the importance of sampling more frequently.
Sampling Criticality Factor (SCF)
- Identify all assets to be sampled and assign a criticality factor from 1 to 10, with 10 being the most critical.
- Identify all potential failure mechanisms for the lubricant that can be detected with oil analysis, such as wrong lubricant, particle contamination, moisture contamination, etc.
- Assign a severity rating (1 to 10) for each failure mechanism.
- Assign an occurrence rating for each failure mechanism.
- Multiply all three factors to obtain the SCF for the asset (1 to 1,000).
Table 1: Sampling Criticality Factor
Although the ratings are subjective, this process will at least offer a structured approach to deciding how critical it is to sample an asset at a short interval. The average SCF could be a problem in some cases as it may downgrade a potentially severe failure mechanism. Therefore, it may be preferable to simply use the highest individual SCF for a given asset rather than the average. For various reasons, many plants have a limit on the number of oil samples they are willing to perform each year. When this is the case, methods like this will help to guide the allocation process.
Routine Lubrication Inspection PMs
In a well-designed program, the most common lubrication activity by far should be routine inspections. The very nature of condition-based maintenance is to inspect for conditions that require corrective action. Routine lubrication inspections typically only require a few minutes to perform and include items such as checking the lubricant level and its visible condition, as well as inspecting for other related items, like filters, breathers, seals, etc. Because oil level is so critical for many applications, it is important to perform these tasks at a relatively high frequency. Ideally, these checks would be performed every day, if not every shift. This is an excellent place for operators to be involved in the lubrication process, as their availability is usually much greater than the mechanical staff. With well-documented inspection procedures and a modest amount of training, most individuals can be qualified to perform these tasks. Unfortunately, this is not an option in every situation and if all inspections must be performed by lubrication technicians or mechanics, there may very well be a shortage of resources to perform these checks at the optimum frequency. When this is the case, a FMEA-type process may again be the best solution to allocating resources in the most efficient manner. Just as with the SCF, we can skip machine and lubricant failure modes and go directly to lubrication failure mechanisms that can be detected through typical visual inspections.
Table 2: Inspection Criticality Factor
Again, it may be desirable to replace the ICF average with the highest individual factor. A process like this will often show that while a machine may be very critical, the routine PMs are not. Likewise, lubrication inspections for a machine of low criticality may be very critical due to the sensitivity of the machine to an item, such as oil level. Combining a rating system like this with experience and intuition will likely be the optimum approach to optimizing your PM inspection program.
With resources stretched thin in most plants these days, it makes sense to take a critical look at the type and frequency of PMs in the current program. While most plants fall well short of performing all scheduled PMs, studies show that anywhere from 35% to 50% of PM activities essentially have no value. If you haven't done so recently, it may be time to take a big step back and redesign your lubrication program from the ground up to make sure you are using the right lubricants, in the right amount, of the right quality, in the right place and at the right time.
References:
1. SKF USA Inc. Bearing Installation Guide . USA: SKF Publications,
2. Barnes, Mark. "Precision Regreasing of Element Bearings." Uptime Magazine Feb/March 2012: 28-30.