by Krishna Kumar
Maintenance engineers in today’s environment are finding it difficult to decide and act on three main issues:
- Job priority by consensus with operations on a daily basis by knowing consequences and risk.
- Operations clearance to execute PM jobs for failure-finding tasks and standby equipment.
- Operations in process plants postponing the equipment release to annual turnaround, thus increasing the shutdown scope.
How do you reach a better understanding between operations and maintenance regarding equipment criticality, work priority and system condition so the missing links and gaps are identified, thus making the maintenance processes more effective?

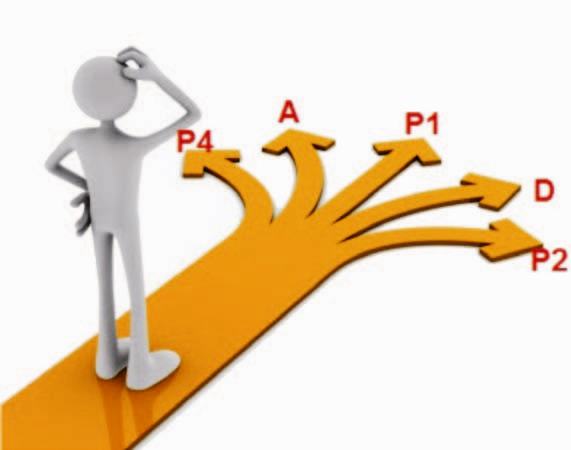
In the day-to-day work order management of process plants, the operating team mainly dictates priority from the view of production loss only. Sometimes, it may not be the actual case and we need to look into other impacts, like health, safety and environment (HSE) consequences due to problems in the asset. Mostly, operations dominates and insists that the maintenance crew accepts the priority and breaks the schedules, which affects the planning and scheduling process.
Equipment changeover from running to standby is another nightmare for operating supervisors due to fear of plant trip or product off spec. Most of the times, either it gets declined or postponed, or may even be refused for changeover. Also, a shift supervisor may decline a permit to carry out a PM task on standby equipment, reasoning that the job may upset or trip the system, or suggesting to plan and execute the job during shutdown. These are all common problems and issues in many process plant operating companies.
The biggest challenge for a maintenance organization is to give the confidence to operations and get the clearance to execute PM jobs for failure-finding tasks or on standby equipment and allow them to accept the equipment changeover. An even more challenging task is preventing all the jobs from accumulating, which makes an uncontrollable shutdown scope at the end. This may lead to extended shutdown duration, which is a huge loss compared to the fear of a plant trip while executing a PM or changeover.
This can be resolved and a consensus reached if we have a better understanding of the following:
- Equipment criticality;
- Consequences of loss of function;
- Job priority for execution;
- System or plant condition to execute the job.
In defining criticality and priority, understanding is very crucial for work order management, otherwise we will work on what is urgent to a supervisor rather than what is important to preserve the function of the asset.
It is well known that an equipment criticality assessment is the starting point for a maintenance work order management system and in developing maintenance strategies that assure the sustained reliable performance of equipment over the lifecycle of the asset. It begins with the identification and ranking of risk of systems and equipment within systems.
Equipment Criticality Assessment helps in:
- Applying maintenance strategies and frequencies appropriate to equipment depending on the level of criticality.
- Defining maintenance strategy development.
- Prioritizing and scheduling preventive, predictive and corrective maintenance work during discussions with operating team.
- Defining priorities for shutdowns and turnarounds.
- Identifying training needs of critical equipment for operating and maintenance crews.
- Performing bad actor analysis and defect elimination.
- Spares identification and procurement based on criticality of the equipment.
The equipment criticality process is how we look at the equipment in our processes and determine how critical it is to the overall process functionality and risk. There are many factors to be considered when ranking a piece of equipment with a criticality assessment. Many questions need to be answered and factors analyzed before assigning a level of criticality to a piece of equipment.
Identifying functionally HSE critical equipment and assigning an exclusive criticality ranking will help in complying with increased HSE regulatory requirements. Moreover, we can have a clearer control on the operation and maintenance issues of assets functioning for HSE. Balance equipment can be classified based on business function, such as business high critical, medium critical and low critical.
A typical example of criticality ranking is shown in Table 1.
The priority is nothing more than how quickly we need the equipment back in operation when there is an outage and notification is raised (see Table 2). If we do not have a better understanding, then the priority gets distorted and people work only from their gut feeling than with a logical mind. What they see is only what they work with and what is behind or beneath is ignored. The concern with this is when a problem gets more urgent, it also gets more important and at the end will be more confusing. How can we ignore one problem that will “bite me” this week and work on another that won't affect me until next month when we have a whole month to fix the second problem? In the real world, there is often not enough time to do both. What makes a non-urgent job more important than an urgent job? The answer is the level of likely final consequences of doing it totally at a wrong time.
Many combinations of criticality and priority may come in real situations, but it is not necessary for all “A” critical equipment to always undergo P1 priority. Figure 1 explains the combination of an “A” critical equipment with all priorities.
System condition is an often ignored factor when creating a PM order, or specifically, a corrective maintenance order. Planners receive notification in the CMMS and convert it to a maintenance work order without considering the system condition in which operations is ready to release the work. This will lead to confusion at shop level. A well-defined system condition in the CMMS and regular use of this system status will help teams understand the jobs to plan and execute for various system conditions.
Table 3 illustrates well-defined system conditions captured at each work order level, which makes the categorization easier.
A typical matrix of criticality, priority and system condition, shown in Figure 2, will help in gaining a better understanding for the work order management process.
YES = Work order must be or to be executed at that priority level; NO = No work order should be assigned with the conditions, example A Critical P2, P, Plant shutdown. YES = Work order must be or to be executed at that priority level; NO = No work order should be assigned with the conditions, example A Critical P2, P, Plant shutdown.
As in Figure 2, similar logics can be arrived for B, C and D critical equipment. In many companies, the operations supervisor insists on designating the job as priority, irrespective of the criticality level. However, one factor alone should not dictate the real priority of the work order. To form a logical conclusion, the consequence, probability and risk of each work order must be assessed keeping the above factors in mind.
While this article is a typical example of a company that has criticality, priority and system conditions defined, different companies may be following different methods for assigning criticality, priority and system conditions. In this instance, the information conveyed here can be used as a guide and adopted to get better clarity and understanding of these three factors for a better work order management process.