Modelo Integral para Optimizar la Confiabilidad en instalaciones Petroleras
En términos generales, el modelo planteado propone integrar una serie de técnicas modernas de Confiabilidad tales como: análisis de modos y efectos de falla, análisis causa raíz, modelaje de Confiabilidad, evaluación costo riesgo beneficio y análisis del costo de ciclo de vida, las cuales, al ser aplicadas de forma estructurada permitirán: definir los eventos de fallas, modelar el comportamiento histórico de fallas, estimar la Confiabilidad y cuantificar los costos totales a lo largo del ciclo de vida de los sistemas de subsuelo utilizados en el proceso de extracción de petróleo. En términos generales, el trabajo propuesto, sirve de guía para orientar a las organizaciones en el proceso de selección e implantación de las diversas técnicas de optimización de Confiabilidad, permitiendo finalmente, que se incremente la efectividad de la Gestión del Mantenimiento y se mejoren los niveles de rentabilidad del sistema de producción
1. Introducción
Con la finalidad de mejorar la rentabilidad de los procesos productivos, las denominadas organizaciones de categoría Clase Mundial (Mackenzie, 1997), dedican enormes esfuerzos para visualizar, analizar, implantar y ejecutar estrategias para la solución de problemas, que involucren decisiones en áreas de alto impacto: seguridad, ambiente, metas de producción, calidad de productos, costos de operación y mantenimiento. La mayor parte de estos esfuerzos, no sólo buscan garantizar la máxima eficiencia en sus procesos productivos, sino que adicionalmente, buscan satisfacer las necesidades de sus clientes y del personal que labora en estas organizaciones (Labib, 1998).
Según Woodhouse (1996), para poder conseguir lo antes expuesto, las empresas Clase Mundial, deben focalizar sus esfuerzos en cuatro aspectos básicos:
- Excelencia en sus procesos medulares.
- Máxima disponibilidad, Producción requerida y Máxima seguridad.
- Calidad y rentabilidad de los productos.
- Motivación y satisfacción del personal.
Las empresas que han logrado alcanzar la categoría de Clase Mundial, tienen como factor común la aplicación de las siguientes prácticas de trabajo (Woodhouse, 2001):
- Trabajo en equipo
- Contratistas orientados a la productividad
- Integración con proveedores de materiales y servicios
- Apoyo y visión de la gerencia
- Planificación y programación proactiva
- Mejoramiento continúo
- Gestión disciplinada de procura de materiales
- Integración de sistemas
- Gerencia de paradas de plantas
- Producción basada en la optimización de la Confiabilidad Operacional
Dentro del entorno de la función mantenimiento, las organizaciones de categoría Clase Mundial (Labib, 1999), proponen mejorar sus procesos a partir de la práctica 10 denominada: Producción basada en la optimización de la Confiabilidad Operacional. Esta práctica la define Woodhouse (1996) como: “la capacidad de una instalación o sistema (integrados por procesos, tecnología y gente), para cumplir su función dentro de sus límites de diseño y bajo un contexto operacional específico”. Es importante puntualizar que en un programa de optimización de Confiabilidad Operacional, es necesario el análisis de cuatro factores habilitadores: Confiabilidad humana, Confiabilidad de los procesos, mantenibilidad de los equipos y la Confiabilidad de los equipos. La variación en conjunto o individual de cualquiera de los cuatro parámetros presentados en la Figura 1, afectará el comportamiento global de la Confiabilidad Operacional de un determinado sistema.
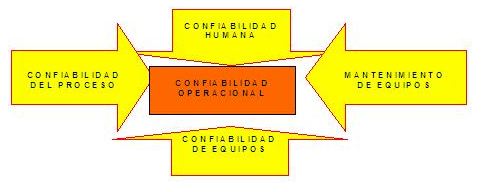
En función de lo expresado anteriormente, las compañías líderes del sector petrolero, han promovido dentro de los procesos de extracción y producción de petróleo, el uso de las mejores prácticas propuestas por las organizaciones de Categoría Clase Mundial, haciendo especial énfasis en la Práctica de Producción basada en la optimización de la Confiabilidad Operacional, la cual, en años anteriores ha sido utilizada con muy buenos resultados en las instalaciones de Superficie. Es importante mencionar, que el proceso de mejoramiento de la Confiabilidad propuesto en el área de Extracción, debe estar enmarcado dentro de un programa integral de Gerencia de Activos y su objetivo principal consiste en maximizar la rentabilidad del negocio petrolero. Con el fin de maximizar dicha rentabilidad, se desarrollo un Modelo integral de optimización de Confiabilidad, que se ajuste a las necesidades de las instalaciones petroleras de subsuelo y que garantice su continuidad operacional. A continuación se presenta el modelo desarrollado:
Para ampliar la imagen haga clic sobre ella, regrese utilizando su navegador.
2. Desarrollo del Modelo Integral de Análisis de Optimización de COnfiabilidad para Activos Petroleros de Subsuelo
El modelo desarrollado (ver Figura 2) sirve de guía para orientar a las organizaciones petroleras, en como aplicar de manera integral diversas técnicas de optimización de Confiabilidad, y de esta forma: predecir el comportamiento de los eventos de fallas y determinar cuales son las estrategias más efectivas para eliminar y/o minimizar el impacto de estos eventos de fallas dentro del contexto operacional en el cual se desempeñan los activos de instalaciones petroleras de subsuelo. Las etapas a seguir que propone el Modelo son:
- Jerarquización, selección y definición del contexto operacional de los activos a evaluar.
- Análisis de Modos y Efectos de Fallas (AMEF).
- Jerarquización de los Modos de Fallas.
- Modelaje de índices de Confiabilidad
- Análisis costo riesgo beneficio para determinar actividades de mantenimiento e inspección
- Análisis del Costo de Ciclo de Vida
Es importante mencionar que para la ejecución de las distintas etapas propuestas por el Modelo de Confiabilidad, la organización debe conformar equipos naturales de trabajo, conformados por personal de las distintas áreas de la organización (operación, mantenimiento, proceso, seguridad, etc.), con el fin de garantizar un proceso de análisis integral de la Confiabilidad en los activos a ser evaluados.
A continuación se explica de forma simplificada cada una de las etapas más importantes involucradas en el Modelo Integral de optimización de Confiabilidad propuesto.
2.1. Jerarquización, Selección y Definición del Contexto Operacional
En esta fase el equipo natural de trabajo se encarga de seleccionar los activos a ser evaluados en función del impacto que generan los eventos de fallas sobre las: operaciones, mantenimiento, producción, ambiente, seguridad, etc. Existen una serie de características particulares de los activos que pueden ayudar a definir de forma rápida, cual de ellos genera mayor impacto dentro del contexto operacional:
- Sistemas que afectan la producción.
- Sistemas de alto riesgo con respecto a aspectos de seguridad y ambiente.
- Sistemas con un alto contenido de tareas de Mantenimiento Preventivo (MP) y/o costos.
- Sistemas con un alto número de acciones de Mantenimiento Correctivo y altos costos de corrección y penalización.
- Equipos genéricos con un alto costo global de operación y mantenimiento.
- Sistemas donde no hay confianza en la operación y el mantenimiento existente.
2.1.1. Matríz de Criticidad
Para jerarquizar los activos de subsuelo (pozo), se propone utilizar un método de jerarquización basado en la evaluación cualitativa del Riesgo (Woodhouse, 2001):
Riesgo = Frecuencia de fallas x Consecuencias (1)
Frecuencia = Número de fallas en un tiempo determinado (2)
Consecuencia = ((Impacto Operacional x Flexibilidad) + Costos Mtto. + Impacto SAH) (3)
El análisis se realiza vía tormenta de ideas en una reunión de trabajo con un grupo multidisciplinario entre los que se encuentran la línea de supervisores, trabajadores de operaciones y mant., ingeniería de procesos o infraestructura, analistas de mant. (preventivo/predictivo), con la finalidad de unificar criterios y validar la información.
Áreas de Criticidad (ver Figura 3): Área de sistemas No Críticos (NC) Área de sistemas de Media Criticidad (MC) Área de sistemas Críticos (C)
2.2. Análisis de los Modos y Efectos de Fallas (AMEF)
Una vez jerarquizado y seleccionado el activo de subsuelo, se procede a realizar la metodología de AMEF (Parra, 2000). Esta metodología permite identificar los modos y efectos de fallas de los activos seleccionados. En resumen el AMEF propone responder las siguientes preguntas:
- ¿Cuáles son las funciones y los estándares de ejecución asociados con el activo (equipo a mantener) en su actual contexto operacional?
- ¿En que forma se produce la falla del activo, con respecto a la función que cumple en el contexto operacional?
- ¿Qué causa cada falla funcional?
- ¿Qué ocurre cuando sucede una falla?
- ¿Cómo impacta cada falla?
El flujograma de aplicación del AMEF mostrado en la Figura 4 se explica a continuación:
- Función: propósito o misión de un activo en un contexto operacional específico (cada activo puede tener más de una función en el contexto operacional).
- Falla funcional: es definido como una ocurrencia no previsible, trayendo como consecuencia que el activo no pueda cumplir con su función o la cumpla de forma ineficiente
- Modo de falla: es el evento que provoca la falla funcional.
- Causas de las fallas: se define como las causas físicas/operacionales/humanas que originan la aparición de los modos de fallas.
- Consecuencias de las fallas: representan los posibles efectos que generan los modos de fallas sobre la seguridad, ambiente y operaciones.
La información generada en el AMEF se registra en un formato modelo, diseñado para activos de Subsuelo. Este formato se presenta a continuación:
El éxito del proceso de implantación del AMEF, dependerá básicamente del trabajo de un equipo multidisciplinario (ver Figura 6), el cual se encargará de responder las cinco preguntas básicas.
2.3. Proceso de Jerarquización de los Modos de Fallas
Una vez definidos los eventos de fallas se procede a jerarquizar de forma cualitativa el Riesgo de cada uno de los modos de fallas en función del impacto que generan los mismos dentro del contexto operacional. El método propuesto esta basado en la evaluación cualitativa del riesgo (Woodhouse, 2001):
Evaluación cualitativa del riesgo (Frecuencia de fallas x Consecuencias):
· Factor de frecuencia de fallas / Escala 1-5
- Sumamente improbable: menos de 1 evento en 5 años
- Improbable: 1 evento en 5 años
- Posible: 1 evento en 3 años
- Probable: entre 1 y 3 eventos al año
- Frecuente: más de 3 eventos por año
· Factor de Consecuencias /Escala 1-5
- Impacto en SHA
5. Explosión / Muerte
4. Incendio / Lesión incapacitante/ área sensible al ambiente
3. Incendio localizado
2. Accidente ambiental reportable /Lesión menor
1. Incidente
- Impacto en el negocio
5. Daños irreversibles al sistema
4. Pérdida de Producción 75%
3. Pérdida de producción 50%
2. Pérdida de producción 25%
1. Pérdida menor de productividad
Se selecciona el valor más alto de: SHA/Negocio, como determinante de la consecuencia.
Los resultados del análisis se presentan en una matriz de criticidad 5 x 5 como la que se muestra en la Figura 7. El eje vertical expresa cinco categorías de consecuencia de los fallas, mientras que el eje horizontal indica cinco categorías de frecuencia de las fallas. La matriz está dividida en cuatro zonas para indicar la criticidad de los modos de fallas:
B = Baja Criticidad
M = Media Criticidad
A = Alta Criticidad
MA = Muy alta Criticidad
2.4. Índices de Confiabilidad, Disponibilidad y Mantenibilidad
El cálculo e interpretación de los índices básicos de Confiabilidad, Disponibilidad y Mantenibilidad permite visualizar el comportamiento de un activo, considerando los siguientes aspectos: frecuencia de fallas, tiempo de reparación y tiempo de operación.
A continuación se presenta una descripción general de los índices a ser evaluados:
- Tiempo Operativo (TO): indica el tiempo en el cual el activo operó, Figura 8.
- Tiempo Fuera de Servicio(TFS): indica el tiempo en el cual el activo se encuentra indisponible. Este índice esta formado por el tiempo para reparar (TPR) y el tiempo fuera de control (TFC), Figura 8.
- Tiempo Entre Fallas (TEF): indica el tiempo en el cual se presentan dos fallas consecutivas sobre el activo, Figura 8.
- Confiabilidad R(t): se define como la probabilidad de que un equipo cumpla una misión específica (no falle) bajo condiciones de operación determinadas en un período determinado”. La Confiabilidad se relaciona básicamente con la tasa de fallas (cantidad de fallas) y con el tiempo medio operativo (TPO -tiempo promedio operativo). Mientras el número de fallas de un determinado equipo vaya en aumento o mientras el TPO de un equipo disminuya, la Confiabilidad del mismo será menor.
R(t) = Probabilidad de que el sistema no falle en un intervalo de tiempo.
ƒ(t) = función de densidad, representa la variación de la probabilidad de fallas por unidad de tiempo, esta función de densidad variará según las distribuciones de probabilidad (Weibull, Log normal, Exponencial, Gamma, etc.). El cálculo de este parámetro dependerá de los tiempos operativos.
t = es el intervalo de tiempo en el cual se desea conocer la Confiabilidad del equipo, partiendo de un período de tiempo = 0
- Disponibilidad (A): es una característica que resume cuantitativamente el perfil de operabilidad de un elemento. Representa el porcentaje del tiempo disponible (de uso) del activo en un período determinado). Es una medida importante para estimar el factor de utilización de un activo. La disponibilidad relaciona básicamente los tiempos promedios fuera de servicio (TPFS) y los tiempos promedios operativos (TPO).
A = TPO / (TPO + TPFS) (5)
- Mantenibilidad M(t): es la característica inherente de un activo, asociada a su capacidad de ser recuperado para el servicio (programada/ no programada) a partir de la ejecución de tareas de mantenimiento. En la práctica, se puede expresar en términos de factores de: frecuencia de mantenimiento, tiempo empleado en mantenimiento y costos de mantenimiento. El parámetro fundamental para calcular la mantenibilidad lo constituye el tiempo promedio de reparación (TPPR) de las fallas.
M(t) = Probabilidad de que el sistema sea recuperado de forma éxitosa en un intervalo de tiempo
ƒ(t) = función de densidad, representa la variación de la probabilidad de reparaciones por unidad de tiempo, esta función de densidad variará según las distribuciones de probabilidad (Weibull, Log normal, Exponencial, Gamma, etc.). El cálculo de este parámetro dependerá de los tiempos de reparación.
t = es el intervalo de tiempo en el cual se desea conocer la mantenibilidad del equipo, partiendo de un período de tiempo = 0
En el caso particular del modelaje de los índices de Confiabilidad, disponibilidad y mantenibilidad de los activos de subsuelo, se propone seguir los pasos citados a continuación (Álvarez y Parra, 2001):
- Recopilación y validación de los datos (modos de fallas, tiempos operativos y tiempos fuera de servicio).
- Análisis de la tendencia de los datos a través del test de Laplace (tendencia creciente, decreciente, constante).
- Ajuste estadístico:
a. Método de Poisson: Proceso Homogéneo, Proceso No Homogéneo.
b. Pruebas de ajuste (Best Fit): Distribuciones de Weibull, Exponencial, Log normal, Normal y Gamma.
2.5. Análisis Costo Riesgo Beneficio de actividades de Mantenimiento e Inspección
En esta fase, se toman los resultados del AMEF y el modelaje de Confiabilidad y se optimizan las distintas las frecuencias de ejecución de las actividades de mantenimiento e inspección relacionadas con el activo de subsuelo. Tradicionalmente, el criterio que se ha utilizado para seleccionar la frecuencia de aplicación de las distintas actividades de mantenimiento ha sido básicamente la data histórica de fallas: tiempo promedio hasta la falla (TPF) -ver Figura 9.
Según Woodhouse (2001), en el contexto actual, el rol del mantenimiento se puede describir de la siguiente forma: “Preservar la función de los equipos aplicando estrategias efectivas de mantenimiento “costo/riesgo/beneficio”, que ayuden a minimizar los riesgos asociados a las consecuencias que generan los distintos modos de fallas dentro del contexto operacional”.
- Relación Costo-Riesgo. El mayor problema consiste en relacionar CUANTO se obtiene de lo que se gasta en un departamento y los beneficios que se reflejan en otro sector. Esto significa que debemos, CUANTIFICAR las variables involucradas y ser capaces de RELACIONAR cuanto se logra con un gasto adicional o reducido. De hecho, es difícil definir el objetivo básico de esa “compensación”; nadie esta profesionalmente preparado para expresar juicios en nombre de todos los sectores a la vez.
- Impacto total. Una vez evaluados el potencial impacto de los modos de fallas sobre el contexto operacional, deben definirse: cuales son las estrategias más efectivas para minimizar el riesgo y cual es el momento óptimo de aplicación de estas actividades. Esta frecuencia óptima, debe generar el impacto total más bajo de los costos asociados a las tareas de mantenimiento propuestas y a las potenciales penalizaciones de los modos de fallas (ver Figura 10).
2.6. Análisis del Costo del Ciclo de Vida
En la última etapa del modelo de optimización de Confiabilidad de los activos de Subsuelo, se contempla el proceso de evaluación del Costo del Ciclo de Vida. En este proceso, es esencial que se evalúen de forma simultánea los factores operativos y de Confiabilidad que afectan el desempeño de los activos y que se asuman las responsabilidades del impacto que traen consigo estos aspectos sobre el costo total de vida. Este análisis implica un método secuencial que permite evaluar de forma integral aspectos económicos y de Confiabilidad con el fin de alcanzar un diseño adecuado desde el punto de vista de costo-efectividad (Riddell y Jennings, 2001). Las categorías principales de costos son:
- Costo de investigación y desarrollo.
- Costo de producción y construcción.
- Costo de operación y apoyo.
- Costo de retirada y eliminación.
Desde el punto de vista financiero, los costos generados a lo largo del ciclo de vida del activo son clasificados en dos tipos (ver Figura 11):
CAPEX: Costos de capital (diseño, desarrollo, adquisición, instalación, entrenamiento staff, manuales, documentación, herramientas y facilidades para mantenimiento, repuestos de aseguramiento, desincorporación).
OPEX: Costos operacionales: (labor, operaciones, mantenimiento, almacenamiento, contrataciones, penalizaciones).
2.6.1. Métodos de Análisis de Costo del Ciclo de Vida
Para la evaluación de los costos de ciclo de vida de los activos de subsuelo, se propone el método del de Análisis de Costo de Ciclo de Vida – Valor Presente (ACCV(P)), el cual representa una forma matemática de relacionar las acciones de diseño con los resultados operativos. Esta metodología permite calcular los costos totales esperados a lo largo del Ciclo de Vida Útil de un activo y viene expresada por:
Para el período de vida útil en años (n) y una tasa de descuento (i)
Dónde:
CI = Costo inicial de adquisición e instalación, normalmente dado en valor Presente.
CO = Costos operacionales, normalmente dado como valor Anualizado**.
CMP = Costos de Mantenimiento Preventivo, normalmente dado como valor Anualizado**.
CTPF = Costos Totales por Confiabilidad, normalmente dado como valor Anualizado. En este caso se asume tasa de fallas constante, por lo cual el impacto en costos es igual en todos los años **.
CMM = Costos de Mantenimiento Mayor –Especiales, normalmente dado como valor Futuro**.
CD = Costos de Desmantelamiento, normalmente dado como valor Futuro**.
VR = Valor de reposición, normalmente dado como valor Futuro**.
** Todas las categorías de costos se convertirán a valor presente (P).
En resumen, es importante definir el impacto de las decisiones relacionadas con el proceso de mejoramiento de la Confiabilidad (calidad del diseño, operaciones, tecnología, complejidad técnica, frecuencia de fallas, costos de mantenimiento preventivo/ correctivo, niveles de mantenibilidad y accesibilidad), ya que estas decisiones, tienen una gran influencia sobre el desempeño de los activos a lo largo del ciclo de vida.
3. Recomendaciones
A continuación se presentan algunos puntos de interés que deben ser tomados en cuenta por las organizaciones petroleras, a la hora de implantar el Modelo de Confiabilidad propuesto:
- Promover el uso de las diferentes metodologías de optimización dentro de un proceso global de mejora de la Confiabilidad Operacional de toda la organización, y no como una iniciativa aislada del área de mantenimiento. No se debe limitar o disminuir el campo de acción, de las técnicas de optimización de Confiabilidad, a herramientas únicas asociadas en muchas oportunidades a simples moda.
- El éxito de la implantación de las metodologías de optimización de la Confiabilidad, dependerá fundamental-mente del recurso humano involucrado, motivo por el cual, hay que tener un especial cuidado en el proceso de inducción y en la formación del personal que participará en este proceso. El proceso de inducción y formación, deberá ser capaz de motivar al personal y de generar en este, el compromiso necesario, para implantar las metodologías de Confiabilidad de forma eficiente.
- Evitar al principio de un proceso de optimización, el sobrecargarse y aplicar muchas iniciativas de forma simultánea - para esto es necesario conocer el objetivo de cada metodología y justificar su aplicación. La falta de conocimiento de las técnicas de Confiabilidad puede llevar a la organización a abstenerse de aprovechar herramientas útiles y a generar expectativas poco fundadas. Tanto la abstención como las expectativas poco fundadas terminan lesionando el liderazgo gerencial.
Finalmente, el Modelo propuesto, propone un esquema lógico y flexible, que permite el uso combinado de diferentes metodologías, con el fin de mejorar los niveles de Confiabilidad de los sistemas de subsuelo, y de esta forma, poder maximizar la rentabilidad del negocio petrolero.
4. Referencias
- Álvarez, A., Parra, C. 2002. “Métodos Estadísticos de estimación de la Confiabilidad y la Mantenibilidad”, Curso de Postgrado Universidad Simón Bolívar, Venezuela, p. 16-23.
- Jones, R. 1996. “Risk-Based Management: A Reliability-Centered Approach”, Gulf Publishing Company, First Edition, Houston, Texas.
- Labib, A.W. 1998. "World-class maintenance using a computerised maintenance management system", Journal of Quality in Maintenance, London, Vol. 4, Iss. 1, p. 66-69.
- Labib, A.W. 1999. "A framework for benchmarking appropriate productive maintenance", Management Decision Journal, London, Vol. 37, Iss. 10, p. 792-794.
- Mackenzie, J.1997. "Turn your company's strategy into reality", Manufacturing Management Journal, January, p. 6-8.
- Moubray, J. 1994. “RCM II: Reliability Centered Maintenance”, Industrial Press Inc., New York, USA.
- Parra, C. 1996. “Modelo de Aplicación del Mantenimiento Centrado en Confiabilidad en el Centro Refinador Paraguaná”, Tesis de Maestría, PDVSA - Universidad de los Andes, Mérida, Venezuela.
- Parra, C. 2000. “Mantenimiento Centrado en Confiabilidad”, Manual de adiestramiento, PDVSA - CIED, Venezuela.
- Riddell, H. & Jennings, A. 2001. “Asset Investment & Life Cycle Costing”, Curso de Adiestramiento CIED - PDVSA, Venezuela.
- Robin, M., Raymond M., y Michale, B. 1996.“ The Basics of FMEA”, Quality Resources, New York.
- Smith, A. 1992. “Reliability Centered Maintenance”, McGraw Hill Inc., New York.
- Woodhouse, J. 2001. “Introduction to the Operational Reliability”. Manual de Adiestramiento, PDVSA – CIED, Venezuela.
- Woodhouse, J. 1996. “ Managing Industrial Risk”, Chapman Hill Inc, London.
Resumen curricular autor: Carlos Alberto Parra Márquez
Gerente IngeCon (Asesoría Integral en Ingeniería de Confiabilidad), www.confiabilidadoperacional.com
Estudios:
- Ingeniero Naval, Instituto Universitario Politécnico de las Fuerzas Armadas Nacionales, 1986-1991, Caracas, Venezuela.
- Magíster en Ingeniería de Mantenimiento, Universidad de los Andes, Escuela de Ingeniería, Programa de Maestría en Ingeniería de Mantenimiento, 1994-1996, Mérida, Venezuela.
- Especialista en Reliability Engineering, Convenio ASME y Tennesse University, 2001-2002, Estados Unidos.
- Optando por el título de Doctorado en Ingeniería Industrial, Universidad de Sevilla, Departamento de Ingeniería de Organización Industrial, 2004 - 2008, Sevilla, España.
Actividades laborales en las áreas de Ingeniería de Confiabilidad y Mantenimiento:
- Coordinador del proyecto de desarrollo de la Metodología de Análisis de Ciclo de Vida para los activos de la industria petrolera Venezolana.
- Coordinador del proyecto de mejoramiento de optimización de la Confiabilidad Operacional en las áreas de Refinación y Compresión de Gas de Petróleos de Venezuela.
- Asesor del proceso de implantación de las técnicas modernas de mantenimiento: Reliability Centered Maintenance (RCM), Total Productive Maintenance, Risk Based Inspection (RBI) y Total Quality Management, en las áreas de gas, petroquímica, refinación y producción de Petróleos de Venezuela.
- Evaluador y diseñador de herramientas de análisis Costo/Riesgo/Beneficio, que ayuden a optimar la Confiabilidad Operacional en los proyectos de ingeniería de Petróleos de Venezuela.
- Coordinador del proyecto de implantación de la técnica de “Asset Managment” en las áreas de Gas, Petroquímica, Refinación y Producción de Petróleos de Venezuela.
Publicaciones:
- Primer Congreso Mundial de Ingeniería de Mantenimiento, Bahía/Brasil, Septiembre 2002. Ponencia/Publicación: “Optimización del proceso de Gestión del Mantenimiento en la Industria Petrolera Venezolana a partir de la Metodología del Mantenimiento Centrado en Confiabilidad”.
- Cuarta Jornada de Ingeniería de Mantenimiento, Universidad de Sevilla, España, Enero 2004. Ponencia/Publicación: “Modelo integral para optimizar la Confiabilidad en instalaciones petroleras”.
- Sexto Congreso Panamericano de Ingeniería de Mantenimiento, Distrito Federal, México, Septiembre 2004. Ponencia/Publicación: “Modelo integral para optimizar la Confiabilidad en instalaciones petroleras”.
- Segundo Congreso Mundial de Ingeniería de Mantenimiento, Curitiba, Brasil, Septiembre 2004. Ponencia/Publicación: “Modelo integral para optimizar la Confiabilidad en instalaciones petroleras”.
- ESREL 06 (European Safety and Reliability Congress), Estoril, Portugal, Septiembre 2006. Ponencia/Publicación: 'On the consideration of reliability in the Life Cycle Cost Analysis (LCCA). A review of basic models'.
Experiencia Universitaria (docente):
Estudiantes de Postgrado:
- Universidad de los Andes, Postgrado en Ingeniería de Mantenimiento, Mérida, Venezuela, área: Nuevas tendencias en Mantenimiento, Análisis Probabilístico de Fallas.
- Universidad Simón Bolívar, Postgrado en Ingeniería de Confiabilidad, Caracas, Venezuela, áreas: Introducción a la Ingeniería de Confiabilidad, Análisis estadístico de la Confiabilidad y la Mantenibilidad, Análisis Costo Riesgo Beneficio en Mantenimiento, Evaluación de Costo de Ciclo de Vida de Activos Industriales.
- Instituto Universitario Tecnológico de la Victoria, Postgrado en Gerencia de Mantenimiento, La Victoria, Venezuela, cursos: Tendencias modernas de Gestión del Mantenimiento y Análisis Probabilístico de fallas.
- Universidad Industrial de Santander, Postgrado en Gerencia de Mantenimiento, Bucaramanga, Colombia, área: Nuevas Tendencias del Mantenimiento.
- Universidad del Norte, Postgrado en Ingeniería Industrial, Barranquilla, Colombia, área: Modelos avanazados de simulación en el área de Ingeniería de Confiabilidad.
- Tecnológico de Costa Rica, Especialización en Ingeniería de Mantenimiento, San José de Costa Rica, área: Mantenimiento Centrado en Confiabilidad.
- Universidad de Sevilla, Postgrado en Ingeniería de Mantenimiento, Sevilla, España, área: Tendencias modernas de Gestión del Mantenimiento y Análisis Probabilístico de fallas.