You Are What You Think You Are Going to Eat!
Applying the adage, "you are what you eat" to MRO material stock, we get "you are what you think you are going to eat!" So what does MRO material stock tell us about the implied reliability, durability, and maintainability of physical assets? Based on the following cross-industry MRO material stats, it's a miracle we can produce anything!
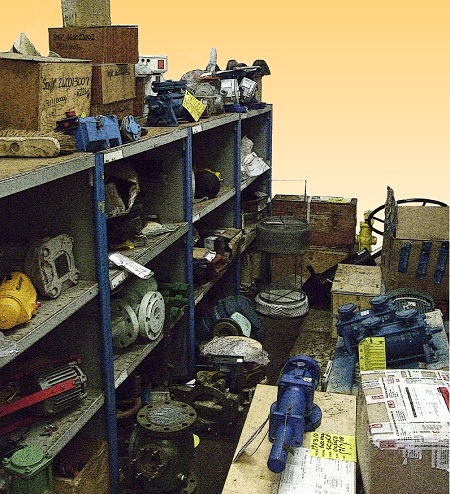
Non-moving MRO inventory typically grows at an annual rate of 6.7%.
Nearly 68% of all SKUs purchased on an annual basis will never be used.
On average, 58% of MRO inventory investment does not move in any three-year period.
Only 6% of parts account for 90% of the MRO inventory expenditures on an annualized basis.
On average, only 17% of new MRO items added to inventory will be used within the first month, with the second use nearly 8 months later.
For initial MRO inventory orders > 2, on average 69% are not issued within the first 3 years.
Stop the Expert Insanity!
If the truth be told, I have spent most of my professional career operating in the weeds and not seeing the entire landscape. I thought my purpose was to solve problems, but I was unwittingly perpetuating them. I was a roofer, wearing spiked shoes. Why? Because I didn't understand the ultimate "future perfect" objectives of production and asset management systems. Nor did I truly grasp how asset management systems operate. And I certainly did not understand how to construct and model system capabilities (flow charts and value stream maps just aren't sufficient). So experts, listen up: this advice is worth its weight ingold, which is valued currently at $1,531.29 per ounce!
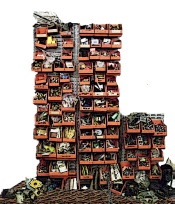
Imagine Perfection, Then Pursue It!
Future perfect objectives are used to ensure directional correctness. A perfect asset is one that never fails and has zero total ownership cost over its useful life. Impossible you say? Certainly, but all asset investment decisions should be measured twice and cut once against this standard.
Ideally the perfect asset would be self-powering, self-scheduling, self-monitoring, self-diagnosing, self-prognosticating, self-adjusting, self-improving, self-repairing, and self-decaying to its essential elements at the end of its useful life. No such system exists, one might contend. I suggest studying the human body, or for that matter a gecko.
Think of your physical assets in this "future perfect" paradigm. Most things don't fail over their useful life, or else you would be afraid to drive your car, or sleep in your own home. Begin by defining the useful life of the asset-normally equal to the life of the product it produces or the service/operations it enables. Use sound methods to estimate first likelihood of failure and then criticality. A toilet is critical, but do you carry a spare?
Develop a complete profile of the nature and costs of asset demands over its useful life. If you don't like the resultant asset demand profile, then I suggest you change the way work is done or how the asset is designed, or look for alternative solutions. Understand that when an asset requires a maintenance technician to conduct weekly PMs, perform predictive maintenance analysis, or replace components on schedule or cycles, this is a real cost to the organization. For example, would you have purchased a refrigerator if it required that you to pay the reseller a weekly fee to inspect it and arbitrarily charge for parts and labor deemed necessary to keep it running? What does this service requirement imply about the refrigerator's reliability, durability, or maintainability?
To the bigger point, what if the reseller expands its services and sends a technician to your house every day for 8 hours, looking for everything that could possibly go wrong, changing your furnace filter, adding oil to your lawnmower, attending to those things that do go wrong, and replacing worn out parts before they fail. And as the home owner, it is your responsibility to stock all the possible parts and pieces that may be needed at your house, even though the reseller's stock of parts is nearby. Are you willing to pay them? Are you willing to invest in the parts, storage space, and an inventory/procurement system? After all, this investment is necessary for managing risk, maintaining the performance of your assets, eliminating unplanned failures, and preventing accelerated deterioration. You certainly don't want risk your house collapsing on your family.
Eliminate Failure, Don't Institutionalize It!
In the future perfect paradigm, the cost of the maintaining an asset is a cost associated with the inability of the asset to never fail over its useful life. When companies establish PdMs and PMs and implement
planned component replacement (lifecycle maintenance), they unwittingly institutionalize failure. They see all of these proactive activities and investment in labor, tools, and materials as a good business practice, albeit a necessary evil of owning assets, where over time the "evil" descriptor disappears. Most component OEMs rightfully profess that they are improving the reliability and durability of their products. After all, warranty has a real cost, not to mention the negative impact of failure on both brand reputation and future revenues, yet end-users still overinvest in parts and labor as if nothing has changed.
One can argue I am not living in the real world. I suggest that few experts accept the real-world reality that asset components wear out and fail on their schedule, not yours. The reason maintenance is predominantly in the fire-fighting mode is because businesses must attend to real and often unpredictable "asset" demands, just like an Emergency Department in a hospital. Organizations don't like the notion of fire-fighting, so they tend to force failure or heighten the urgency of deterioration to fit into defined activities that can be planned for, queued, resourced, scheduled, level-loaded, EOQ'd, and so on. The goal: a nice, neat, and predictable model that can be budgeted a full year in advance!
Where we lack real failure data to understand and predict demand, we create it in wonderful Monte Carlo simulations, well-intentioned Weibull analyses, and standardized MTBFs. In the end, what does the magic of statistical modeling tells us? Run for the hills?
Understand Reality, Accept Reality, Improve Reality!
I get that all of us might want to say "look Mom I did well; I kept everyone productive, and it was a good investment." But in the lean Six Sigma paradigm applied to asset management, in order to optimize supply (e.g., resources that respond to asset demands) and to meet budget objectives, "failure has to be more reliable than the asset!" We should simply recognize that in reality failure is not reliable, nor should it be, nor should we force it to be so! Stuff happens-it is just the way life is.
We need lean systems that improve our ability to predict actual bad "stuff" before it happens (they exist) and more efficient systems for queuing "stuff" based on its occurrence or the high probability thereof and its consequence, within the constraints organizational resources and the attendant supply chain. Lean thinking requires one to mentally reclassify "fire-fighting" to "short demand lead-time," and then to build lean supply chains that understand the time value of lettuce, not processed cheese.
Unfortunately, we pay huge sums of money for systems like ERP, EAM, and CMMS, yet they do little to help queue work based on real priorities. This leaves the maintenance supervisor to use a white board to list the day's work, or hand out a batch of work orders for that day/week, or produce an Excel spreadsheet that is updated daily if not more, based on events as they occur and resources as they become available.
Constraining Supply Does Not Eliminate Demand!
The only "real" way to make tangible improvements in asset management investments is to eliminate or lessen asset operating demands; then supply will follow. It is nonsensical to constrain supply thinking that it reduces "real" demand created by "real" assets. Constraining supply (i.e. how many parts we keep on the shelf, how many electricians we employ, or the number of PMs we conduct) may indeed reduce "artificial" supply demand created under the guise of being productive and economically efficient, but it does not eliminate "real" asset demand. The proof is found in the unaccounted-for back stock scattered throughout the plant, or the cannibalized equipment lying in bone yards.
So what is the success rate of the experts getting it right? 2007 estimates of U.S. industry purchases suggest that in excess of $136 billion in MRO material stock still sits in end-user operations. Are you getting this? That is $136 BILLION that could have been put to better use-"opportunity cost" for the financial experts trying to solve this conundrum. In my world, the experts have failed those they serve, and unfortunately I have the stats to prove it. I suspect you do, too.
Rich MacInnes is the Director of Professional Services for Net Results Group. Rich is the principle author of the book Strategic MRO, A Roadmap for Transforming Assets into Strategic Advantage. Rich also has authored The Lean Enterprise Memory Jogger for Production and The Lean Enterprise Memory Jogger for Service, foundational books used to advance lean methodologies and decision making within organizations. www.netresultsgroup.com