by Carlos Mario Perez Jaramillo
7 questions to ask when analyzing your assets:
- What are the functions and performance associated with the asset’s standards in its current operating context?
- In what ways does it not perform its functions?
- What is the cause stopping it from performing its function?
- What happens when each failure occurs?
- What is the impact of each failure?
- What can be done to predict or prevent every failure?
- What should be done if adequate work could not be performed before the failure?
Reliability centered maintenance (RCM) focuses on identifying what should be done to assure the functions of a system or asset in a safe, cost-effective and reliable way. RCM analysis is carried out by a group of experts, called the analysis team, for the equipment, asset, or object of the study. It is their responsibility to answer seven questions (above) about the asset being analyzed. In Part 1 of this series, myths 1-10 were discussed. Now we will examine the remaining 12 myths.
MYTH 11: RCM is a project, i.e., an initiative with defined termination or completion.
The application of reliability centered maintenance (RCM) is not temporary; it is a process that has a very clear objective. It is defined as “a process used to determine what should be done to ensure a physical element continues performing the desired functions in its current operational context.”
RCM is a dynamic and permanent process because analyses must be validated over time since operational context, functions, failure modes, effects and failure management strategies can be changed by different requirements of the assets, changes in the skills of operators and maintainers, and by environmental modifications.
MYTH 12: RCM must be applied to all assets of the company.
RCM is a process that can be applied to all assets of a company, but not necessarily at the same time in a massive and intensive effort. The most advisable is to implement it stepby- step, selectively to equipment, systems, or assets that facilitators, along with their analysis groups, have identified to reduce high levels of dissatisfaction. In doing so, the results motivate management and the company to continue investing in further asset analysis.
The approach of analyzing all equipment hastily with large amounts of resources and time, but without defined foundation is not recommended because few people share knowledge on a lot of assets and it is physically impossible to be in several analysis groups.
MYTH 13: RCM is only for companies with many assets.
All companies, from all sectors and conditions, want to be more reliable. In fact, the answers to these questions will validate the interest in reliability:
- Can the company sell everything it can produce (i.e., products or services)?
- Does the company want a tolerable and acceptable performance in terms of safety and environmental integrity?
- Does the company have a lot of preventive activity simply because it is a habit?
- Are operating costs high in relation to other, similar businesses?
- Has the company been collecting information for decades to be able to make the best decisions?
- Do user areas believe that shutdowns and breakdowns are only maintenance problems?
- Are priorities and criteria for operators and maintainers different?
- Are shutdowns long and costly?
- Were maintenance plans not made by people close to assets?
MYTH 14: RCM has a poor cost-benefit ratio.
Many maintenance managers do not understand what RCM is and believe they cannot handle costs to do it properly. This is dangerous, since in decision-making schemes, money and production stoppages are no longer the only elements present; now risk shows up too. Therefore, those who say they do not have time and money to implement responsible and defensible methods cannot afford not to do it because there are lives depending on them.
Applying RCM slightly, without a series of indicators that check the progress, makes achievements and the advance of the process useless. The rate of return of a RCM process is 17 to 1. That’s why RCM, in addition to its intangible achievements, is still used and enjoys such a good reputation.
If RCM is applied correctly by well-trained people working on projects clearly defined and properly managed, the analyses typically pay for themselves within weeks and months.
MYTH 15: RCM outcomes take time to be seen.
Outcomes from a RCM process are related to the level of dissatisfaction the user has with respect to the asset. So when choosing assets, some kind of indicator showing the opportunity for reliability improvement should be selected. In some cases, the assets have not been operated, maintained and managed in an appropriate manner, therefore, in the stage of analysis implementation, urgent findings are achieved and serve to show the benefits of the process without finishing it. In other cases, analyses must be implemented, as well as the proper application of the results, to achieve the expected improvements.
If there are no urgent findings, especially in assets that currently have “satisfactory levels” in their indicators but offer attractive opportunities for improvement, it is necessary to implement all the recommendations of the analysis to obtain the results.
MYTH 16: RCM is not considered one of the so-called best practices.
Best practices are understood as the consistent application of a certain technique, methodology, tool, process, activity, or action, as the most effective way to deliver a particular outcome. It includes experiences based on learning and continuous improvement; that’s how processes and activities are progressively checked and tested. The application of best practices is very useful. Standardization of practices across companies allows optimization of integration and management tools, so many organizations perform similar tasks using the same method.
RCM can be described as a process of high levels of commitment. Constructing new maintenance plans is a great improvement for two reasons: First, experts in operating and maintaining the equipment perform the RCM analysis and second, companies know that maintenance plans are technically justified.
MYTH 17: RCM is a maintenance initiative; therefore its success lies in the maintenance staff.
Although there is a wrong perception that RCM is an initiative that is only within the maintenance area of a company, it is necessary to emphasize that the success of RCM is associated with all units of the company. Only in this way will the company reach the required degree of reliability.
Conviction, support and monitoring of the directors of the company are key factors for achieving the purpose of a RCM process. This manifests itself in a good budget, reporting requirements, results and extension efforts in all areas of the company.
MYTH 18: RCM requires weekly meetings, schemes and work teams.
Companies have time to gather; they do it all the time because they are immersed performing failure analysis, problem analysis, corrective actions, planning and scheduling to handle failures, and using software to attack failures. Modifying their routine to analyze how to solve problems is something that can be linked to the proactive and modern vision of the management.
In addition, creativity to find appropriate times to meet is linked to intelligence, motivation and commitment. There are also alternative models for meeting, such as full weeks of total dedication, which increase efficiency and effectiveness of the process.
MYTH 19: RCM only can be carried out by the maintenance area, or even more, it can be hired.
RCM is not a household word of the “do-ityourself” style. There is the idea that RCM must be learned and practiced to achieve skill and gain the benefits that can be obtained. Maintenance staff cannot answer all the questions themselves. Many of the answers only can be provided by operators; this applies especially to the questions concerning the desired performance and effects and consequences of failures. For this reason, an analysis of maintenance requirements of any equipment must be performed with work teams that include operators and maintainers.
Seniority of team members is less important than having a broad knowledge of the equipment being considered. Each member of the team also must have been trained in RCM. The team must be multidisciplinary and be able to receive the knowledge from specialists in the subject when required. The use of these teams not only allows managers to gain access in a systematic way to the knowledge and experience of each team member, but it also distributes maintenance problems and their solutions in an extraordinary manner.
MYTH 20: Third parties who use templates to save time in the analysis may be hired.
Third parties are far less informed than maintenance personnel about the operational context of the asset, the desired performance patterns, failure modes, effects and their consequences, and the capabilities of users and maintenance staff. Often, these third parties don’t know anything about these issues. As a result, plans achieved with this support are almost always unsatisfactory.
Third parties commit resources from maintenance users, therefore, they have little interest in optimizing them. The mistake made in these cases is committed by the users, for making unreasonable requests to organizations that are not in the best position to meet them.
On the other hand, an analysis performed on a particular procedure or on systems that are technically identical under the “buying an analysis is cheaper” assumption, has to be carried out with the greatest care for several reasons:
- The operational context is different.
- Different competencies of individuals performing maintenance. In one case, they may prefer a proactive technology type, while another team working on another identical asset may be more comfortable using other technology.
- The analysis level may be inappropriate to establish the causes of failures for technically identical resources. This can deliver a result that is too superficial, possibly dangerous, or perhaps useless.
- Performance standards may differ.
All these reasons show that the best thing to do is to take advantage of the accumulated experience of those who operate and maintain assets to define the best strategies to handle failures.
MYTH 21: The RCM process does not require facilitators.
The RCM process requires enthusiasm champions, persevering individuals with the ability to overcome resistance to change and have management support.
The primary function of a RCM facilitator is to enable the application of the RCM methodology by asking questions to a group of people selected for their knowledge on the equipment or asset, ensuring agreement upon answers and registering them. He/she is responsible for:
- Technical quality of the analysis.
- Proper handling of the attitude of the participants.
- Handling of the analysis as a project.
- Time administration during the analysis.
- Application of an appropriate analysis pace.
- Application of RCM logic without tricks, shortcuts and mistakes.
- Conducting the meetings.
- Managing the implementation of RCM with a corporate approach as a whole.
- Proper implementations of all tasks, redesigning, training, coaching, inventory policies, and keeping alive and updated the RCM process in the company.
MYTH 22: All methods are equal; after all they are called RCM.
It is true that many systems call themselves RCM, but in most cases, these approaches have been shortened and carry the statement that they can produce the same results as legitimate RCM in one half or a third of the time.
Since the RCM model was implemented, a variety of processes have emerged and are called RCM by their proponents. But they often have little or no resemblance to the original process developed by F. Stanley Nowlan and Howard F. Heap, which is structured and fully tested. As a result, if an organization says it wants assistance to use or learn to use RCM, it may not be sure which process will be offered to it.
The word “abbreviated” suggests that something is being left out and leaving things out inevitably increases the risk. If the worst happens, directors and managers will have to give explanations as to why they chose a non-optimal decision-making process to establish their strategies, instead of using one that meets a standard set by an international organization specialized in establishing such schemes.
Throughout this two-part series, we have discussed myths about RCM methodology implementation that is widespread in organizations. This is intended to provide clarity about the true strengths and forms of RCM application.
READ PART 1: MYTHS 1-10
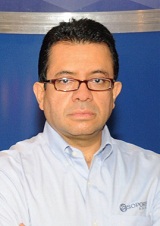