Napoleon Engineering Services Announces Aerospace Bearing Offerings
Reverse bearing engineering services for PMA-FAA Certification
One of the more comprehensive inspection programs offered by NES is the reverse engineering of Typed Certified aircraft ball and roller bearings for FAA Certification. Bearing suppliers which were not integrated into an aircraft at the point of original design must obtain an independent PMA from the FAA. PMA-FAA bearing reverse engineering is a method for ensuring that commercial aircraft replacement bearings can meet or exceed the same rigorous quality, design and performance standards as those originally specified. To support these requirements, a team of highly experienced NES engineers and technicians perform a thorough physical evaluation of aircraft bearings, using highly specialized equipment and data analysis tools. The end product is an accurate and detailed analysis which provides aircraft bearing suppliers with all of the necessary PMA-FAA certification inspection data, as well as added assurances that its aircraft bearing manufacturing meets or exceeds supplier standards for form, fit and function.

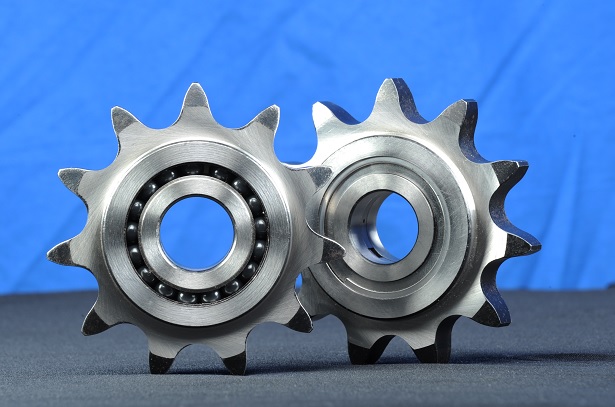
Aerospace bearing manufacturing typically requires the use of superior quality raw materials; the incorporation of extensive design and project review processes; and support for any required material or process traceability. To meet these needs, NES offers complete design, development and manufacturing of custom high-precision aerospace ball and roller bearings, as well as custom bearing modification. The manufacturing process includes close collaboration with an aerospace OEM’s own in-house engineering team, with full project management support from initial concept thru final delivery. Typical requirements range from all stainless steel full complement bearings; to M50 long life angular contact ball bearings; to superelastic Ni-Ti alloy designs which incorporate wear-resistant, high-life materials and coatings. Supported applications include satellite and UAV arm actuation, antennas, fuel pumps, ram air turbines, rocket engine valves, turbine engines, and rotorcraft transmissions. Expedited lead times are available upon request.
First article inspection (FAI) per AS9102
NES offers FAI as an integral part of its aerospace bearing inspection offerings. FAI is used by aerospace manufacturers to verify that a delivered bearing conforms to all engineering requirements. A physical and functional inspection further verifies that prescribed production methods have produced a part or item that is acceptable with respect to engineering drawings and specifications, purchase orders, planning documents, or other relevant design documents. Using FAI, customers gain added confidence in the total conformance of first-run bearings to required end-use material, engineering, and quality standards. For companies requiring an FAI per AS9102, NES can provide a complete, independent, and documented FAI, with or without material specification and special process accountability.
Aerospace bearing inspection and bearing testing services
In addition to the aforementioned capabilities, the Olean, New York-based NES is also home to North America’s largest independent aerospace bearing inspection and bearing testing facility. This includes over 40 active bearing test rigs. In-laboratory capabilities include bearing failure analysis and metallurgical testing; bearing stress analysis, including source qualification inspection (SQI); environmental testing; RCF and dynamic life cycle testing; and impact and static load testing. In addition, NES can design and manufacture a custom aerospace bearing test rig to suit virtually any in-house requirement.