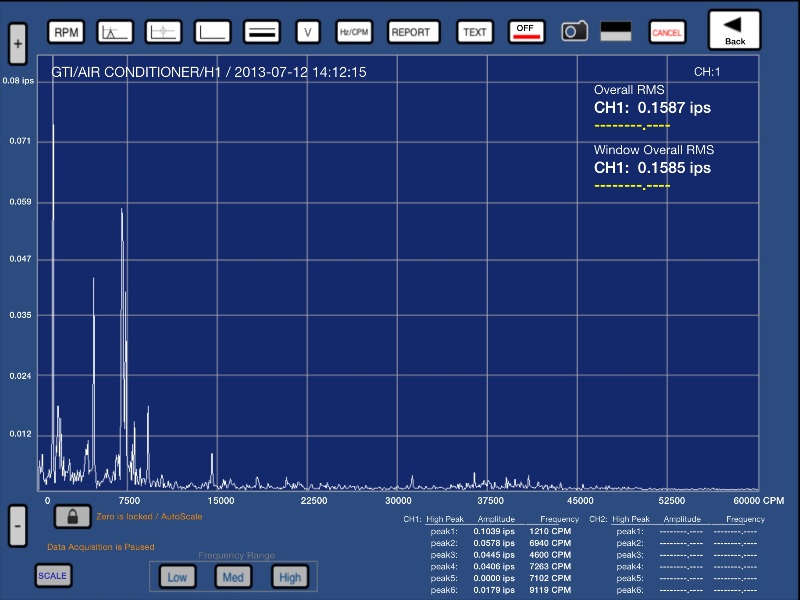
Figure 1: Vibration analysis
Predictive maintenance (PdM) is a strategy where maintenance is performed when one or more indicators show that equipment will fail or performance is deteriorating. Time-based maintenance tasks for machines shown to be running well are avoided, eliminating the possibility of introducing a defect into the system.
Predictive maintenance is the core of reliability maintenance. Technologies, such as vibration analysis, motor current signature, ultrasound and oil analysis, are used to help assess machinery health and predict future failures. Prediction of failures allows maintenance to be planned on the user’s schedule, not the machine’s.
Advantages of a Predictive Maintenance Program
PdM has been a goal of many maintenance reliability programs. The advantages of a PdM program are:
- Improved system reliability;
- Increased production;
- Decreased maintenance costs;
- Less human intervention, less human error influence.
While PdM is recognized as the best way to monitor a plant’s assets, there have been many hurdles preventing implementation, among them:
- Initial investment costs;
- Lack of trained technical resources for analysis;
- Dealing with an abundance of data;
- Change management.
But all this is changing. Just as in many other high-tech markets, new advances in computer hardware and software are bringing the cost of PdM technology down. Who would have thought 10 years ago that tablet computers would be available for under $500 or that most people would be carrying an Internet-capable computer in their pocket?
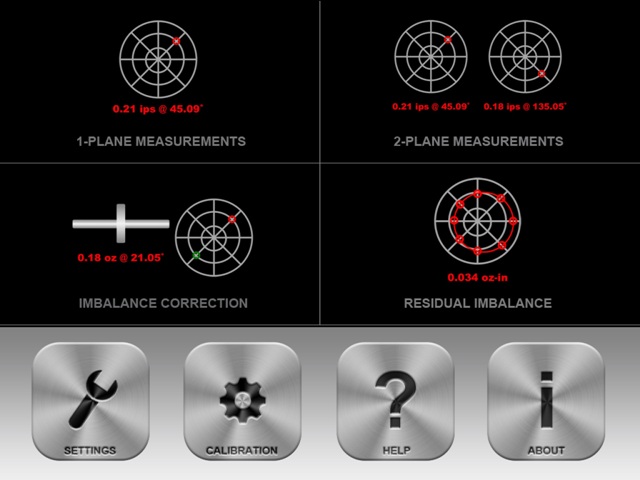
Figure 2: Balancing
When you visit an online app store for tablets, you can now find solutions for vibration analysis and data collection, rotor balancing, laser shaft alignment and infrared thermography. With tablet technology, the one or more indicators mentioned earlier in this article eventually will be all in one device.
Even as the cost is going down, advanced features are being added. Today’s PdM software allows problems to be readily identified and prioritized from machine’s that do not currently have problems. Trends can be built with route-based programs. Modern networks allow the owner to outsource data analysis in real-time and “expert” software programs have improved greatly over the years.
Another technology that has experienced huge technical advantages along with decreasing cost is wireless communication. Greater amounts of data can be sent at greater speeds over greater distances with much improved reliability. A wireless infrastructure saves the cost of installation, eliminating the need to install conduit and pull cables. Tablet-based PdM systems of the future will feature wireless communication almost exclusively.
Tablet Applications and What They Mean to Reliability Centered Maintenance
So, what do tablet-based solutions offer? First, as mentioned earlier, is cost. Their $500 average price is coming down, but another cost savings factor is that their processing power is typically greater than that of the average single purpose data collector. Another huge cost reduction factor is the apps being developed for each technology. Once a company owns an app, it owns it forever. That means the app software is free to the user after the purchase of the first unit. Upgrades are free through the app store and they come automatically with alerts on the tablet when they are available.
Figure 3: Alignment
Second, all of the different technologies, such as vibration, infrared, balancing, ultrasound, motor testing and laser alignment, can be developed as apps on a single platform. Need a new technology? Contact the vendor for any hardware and download the app. The tablet is a one-time purchase.
Thirdly, tablets are not purpose-built. A tablet can function as whatever tool you want it to be that day. Because all the functionality is developed in software, it is simple to upgrade (most upgrades are free through the app store) and add new functions and capabilities as customers ask for them. There is no need for a list of upgrades that will be included in the next version of hardware that has to be purchased to get the upgrade.
If a tablet is dropped or damaged, there are no worries. Simply go to the local computer store and get a new one, then download all your apps and reload your data from the cloud. It is less expensive and certainly takes less time than sending a computer display unit back for repair and waiting two to three weeks to get it back.
Other tasks that can be done with a tablet include:
- Preventative maintenance checklists;
- Photo documentation;
- Video documentation;
- Inspection checklists;
- Integrated reports with multiple technologies on the same report;
- Training videos;
- Complete user manuals;
- Maintenance procedures;
- Work orders with parts lists and specifications;
- Whatever you can think of.
In a nutshell: One tablet, multiple technologies, add new technologies when you want or need to.
Why Cloud Technology
Another tablet advantage is cloud data storage. Reliability data stored in the cloud is always available, anywhere, anytime. Data and other information stored in the cloud can be easily shared immediately with others in the organization or with experts across the world for collaboration.
Figure 4: Cloud computing
To get started, it’s important to understand what a cloud-based network is. The cloud brings together a large number of computers (data centers) to operate a single application. Imagine running a social networking site like LinkedIn, Facebook, or YouTube and having to host the entire database on your home computer. You would need a data center in your house! And then to access remotely, you would have to take the data center with you. With cloud-based networking, databases for programs reside in the cloud.
The cloud consists of layers, primarily the back end and the front end. The front end layers are the ones you use and interact with. The back end consists of hardware and software architecture that support the interface you see. Since computers are set up to work together, the applications take advantage of all that processing power and operate as if they were all running on the same computer.
Cloud computing offers:
- Reduced costs;
- Easy maintenance;
- Greater flexibility;
- Real-time access to data;
- Unlimited (almost) data storage;
- IT acceptance;
- Greater profits.
Now let’s apply cloud computing to a predictive maintenance solution. The cloud allows access to data anywhere in the world, including by third-party analysts, without having to add additional, expensive infrastructure. This also makes it easier to monitor remote installations – pipelines, offshore drilling rigs, small facilities with limited resources – via existing Internet connections and cellular technology.
According to Michael Jackson, co-founder of Adaptive Computing, “Cloud computing is becoming a priority for almost every IT organization in business today. According to a Pew Research Center survey, a decisive number of technology professionals predict that by 2020 most people will access software applications online and work through remotely accessed networks.”
Virtually every technology company is incorporating the word cloud somewhere in its description. The rapid developments in cloud technologies and services can only work to benefit the maintenance reliability community. All these factors will work together to bring affordable, accessible and powerful predictive maintenance products and services to every reliability program.
What’s Next?
Wireless sensors to eliminate cables, motor current apps, ultrasound apps – the sky’s the limit because there’s an app for that.
Tablets are the future for portable predictive technology. Get involved and let manufacturers know what functionality you want. Start looking around at what’s available; there’s no telling what you’ll find or what you can afford!
About the Author
Paul Berberian is a Predictive Maintenance Specialist for GTI Predictive Technology. Paul has over 15 years of experience in the maintenance reliability industry. http://www.gtipredictive.com