Overall equipment effectiveness (OEE) is an often touted tool for managing a manufacturing operation. In its basic form, it is intended to identify production losses, primarily so they can be managed, for example, planned and unplanned downtime, rate, and quality losses, and perhaps other losses. It is simple in concept, but much more difficult in practice. For example, do you measure availability during no demand times? Where do you measure – on all machines or processes, or just one? How do you measure? What specifically do you measure? How do you determine the rate? How do you measure quality? For example, what if quality measurement is difficult, say, when lesser quality product is still sold, but for a lower price? Do you measure all losses or only those associated with scheduled production? What about short stops and transition losses, which are often difficult to determine? Who does the measurements? How do you use the measurement results? The list is long. This article provides some guidance, but it is not intended to be all inclusive, but rather to provide a few principles that will help in the decision-making process and in making the use of OEE more productive.
About OEE
OEE was first developed by Seiichi Nakajima in his effort to help Japanese manufacturing companies reduce their production losses and become more productive and competitive.
Fundamentally, it takes the form: OEE = A x R x Q, where A is availability percentage, R is production rate percentage and Q is quality percentage.
Figure 1 provides one model for OEE. It contains the usual categories for an OEE measure – availability, rate and quality. However, it also adds transition and changeover losses, something that might be omitted in a conventional measure, along with an additional loss related to no demand and market losses. Some businesses may want to include other loss categories specific to their business, such as raw material supply, utility disruptions, operator no-shows, etc.
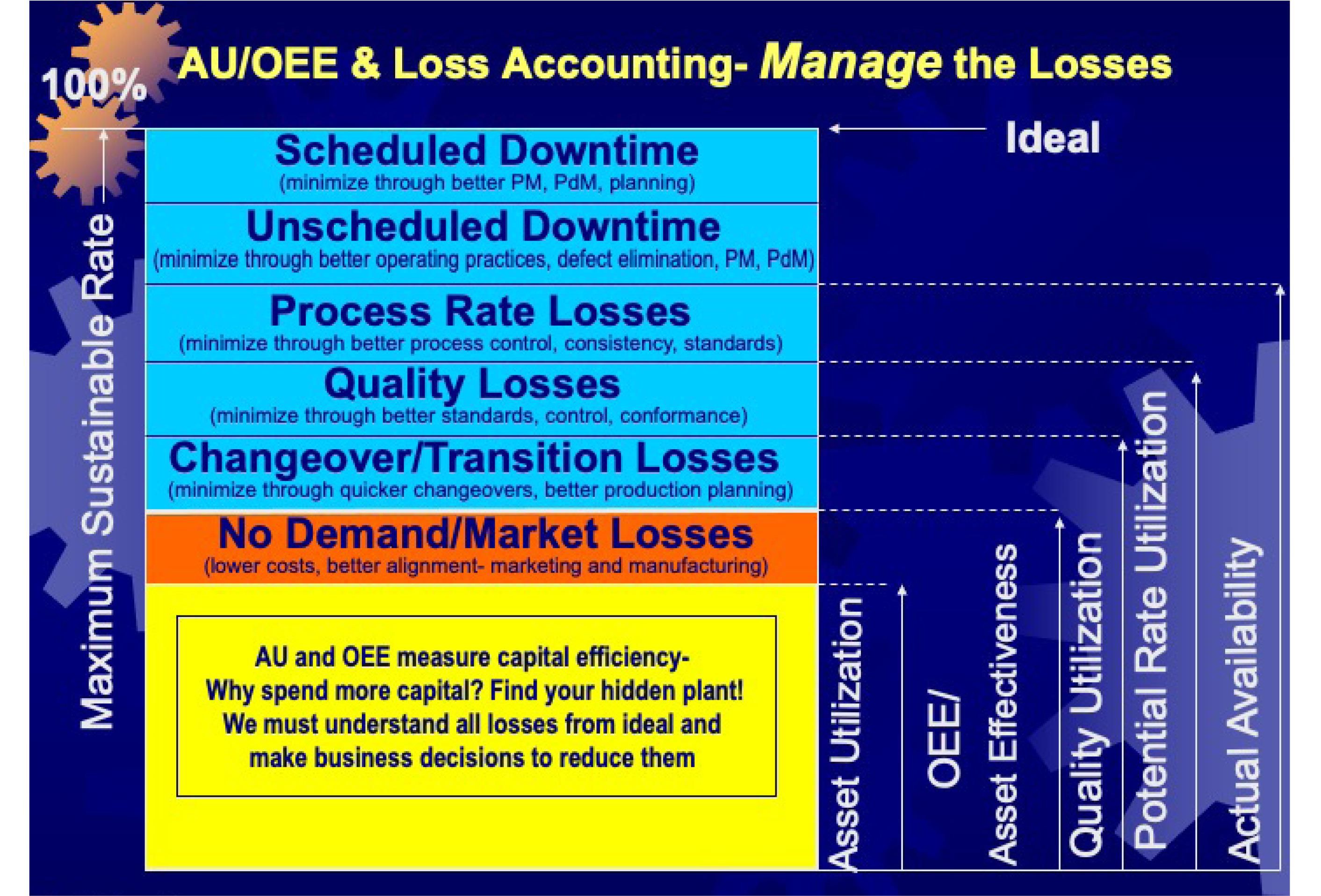
Figure 1: A model for OEE measurement
The losses shown in blue in Figure 1 are more typical in an OEE measure, the losses shown in orange are not. The distinction made is that measuring all losses from ideal provides a measure of the business’s asset utilization (AU) and includes no demand. The plant is responsible for the losses in blue, the business is responsible for all losses, including no demand. In this light, AU is a measure of the capital efficiency of the business, not just the production efficiency of the plant. It provides an indication of the additional capacity available to the business that does not require additional capital investment. In this light, it is essential that you measure ALL losses for a given production operation – 8,760 hours in a typical year.
This runs contrary to Nakajima’s recommendation to measure losses only during planned production time, which is an acceptable approach, but doesn’t provide a total business perspective. An important point here is that you will never achieve the ideal state or zero losses, but the key is to manage the losses to make business decisions about whether the losses are acceptable or not.
Fundamentally, if you apply the model in Figure 1, you would answer several questions – if you could run your plant 8,760 hours per year at 100% of your maximum, demonstrated, sustainable rate, at 100% first pass, first quality yield, with no losses for changeovers or transitions, and no demand losses:
- How much could you make? (the ideal, but unachievable state);
- How much are you making? (the reality);
- Where are your losses from the ideal state? (by category);
- Are these losses acceptable to the business? (highly unlikely).
The most important question here is clearly number four – Are these losses acceptable to the business? You will always have losses from ideal, but you must sort through the data and manage the losses. Some will be acceptable, like time for highly efficient product changeovers or planned maintenance, some will not. Some will require more investment than is required for an acceptable return, some will be long term, like market demand and so on. Things that are easier to do and have a high return will get done first; things that are hard to do, but have a high return will be longer term, with everything else in between. Of course, things that are hard to do and have a low return will be acceptable for now. As time passes and you learn more about managing the losses, or as new technology becomes available, you may revisit those.
Determining the Rate
With all this in mind, let’s get back to some of the questions or issues, starting with your maximum, demonstrated, sustainable rate. What do you use for that? Some thoughts are you might use the 95th percentile achieved to date for a given production line or process (more on locations later); your best three days ever; or your best three shifts ever. In a batch operation, you might use your best ever cycle time and yield for a given product. The point is, whatever measure you choose, you want it to be challenging, not easy, and you’ve demonstrated that you can do it, if everything goes well. Then, you work hard to eliminate those things that are preventing production from going well. Again, it must be challenging, but achievable and sustainable.
Here’s an example:
In working with a chemical operation, they used the best three days ever for their initial rate. It was challenging and had been demonstrated as achievable. As it turned out, though, this rate actually fouled the process more frequently, requiring more frequent maintenance downtime for cleaning and replacing equipment, thus a net loss in production. After considerable review and discussion, it was determined that the best seven days ever would be a more sustainable rate to use for the calculation.
It’s a judgment call, but the rate you select should be challenging, demonstrated and sustainable. Moreover, as you improve your processes and/or debottleneck and the maximum demonstrated sustainable rate improves, you must change the rate used for the calculation. Initially, you may be disappointed that your OEE declines because of this, but this should not be a concern. The broader point is that you’re managing the losses and productivity is improving.
Measurement Location(s)
So, where do you measure OEE? In a complex plant, this can be a difficult question to answer, but fundamentally, it should be at the design bottleneck or constraint in the system. While this may vary from time to time as you debottleneck, and may vary operationally on a given day depending on which step in the process is not working well, it is likely the best location for the measurement. To determine this in a complex process, you will likely need to map your processes, identifying the constraint for each flow path of a given production run. A few simple examples are shown in Figure 2, provided courtesy of Robert Hansen, author of the book, Overall Equipment Effectiveness.
For any given product, you may have different constraints. For a batch process in which you have a multitude of products, it initially may be too complex. In this case, you may want to use a product that is characteristic of the group and then refine it as you learn. As previously noted, you should measure all losses from ideal, including as applicable, setup/cleanup, time between batches/runs, lack of supply from upstream, inability to send downstream, batch yield that is less than ideal, utility supply, like steam, air, or other utilities that are not available as needed. In other words, measure and manage anything that causes you to lose ideal production. No demand time is a market opportunity to sell more product with the existing assets. As you eliminate the more common losses, you will create more capacity, and likely more no demand time, an opportunity to achieve greater market share at a lower cost with minimal additional capital investment.
Returning to the where to measure question, Figure 2 provides four different block diagrams for various plant configurations. Line 1 might be a chemical operation where a basic product is transformed using various processes for many different products. Note that the bottleneck for each production process is identified in red. Line 2 might be an automotive plant where various components come together to create a finished product. Likewise, the bottleneck for each production process is in red. Line 3 might be a steel plant where the final product is what comes out of the process stream or may require further action, such as slitting, coating, or some other operation. Lastly, Line 4 is a very simple process. The broader point is that each of the more complex processes can be simplified to that shown in Line 4, with each having a different bottleneck. You must map your processes and then measure OEE at each of the bottlenecks. As you might expect, this will be quite difficult if you don’t automate at least some of the processes to collect and analyze the data, something strongly recommended.Figure 2: Four plant configurations
Management and Systems Issues
As previously noted, measure all losses 24/7/52. The plant manager, in concert with the production and maintenance manager, is responsible for managing the plant losses, working with senior management as needed to address specific resources and/or systems that may be required to support the plant. Senior management is responsible for no demand and market losses, in collaboration with the plant. The goals of the business are to improve productivity, and therefore capital efficiency, and therefore market share and profits.
In achieving this, accuracy and sustainability of the systems in place are key. As such, it is important that operators input the data for OEE, with supervisors providing coaching and mentoring about who, what, when, where and how, and to ensure accuracy and continuing refinement in the measurement. The reason for having operators enter the data into the system is to create a sense of ownership for the data and for problem resolution related to the data. Properly done, including a feedback loop, will give them a sense of purpose, pride, control and ownership for helping manage the losses. This, of course, means that the systems in place must be easy to use and training and coaching must be excellent. Finally, definitions for the losses must be aligned from the shop floor to the site management team so that communication and management of the losses are based on a common set of definitions. You may even want to include a cascade of the losses, breaking down each major category into subsets that are specific enough to easily target and eliminate.
Other Considerations
OEE is primarily targeted at manufacturing operations and is not suited for all industrial operations. For example, it is not particularly useful in electric power stations, which consist of base load, cycling and peaking units. What may be more useful is equivalent forced outage rate and, for fossil units, thermal efficiency. That said, the fundamental question is similar to the driving philosophy behind OEE – what’s the ideal state? What’s the reality? Where are my losses? How do I manage those losses? For example, if the ideal forced outage rate is zero and you’re at five percent, that’s worth millions of dollars. So, what’s driving those losses from ideal and how can you manage them more effectively? Similarly, if the ideal thermal efficiency is 42 and you’re at 37 percent, you would ask the same series of questions.
Similar questions could be developed for other utilities and their ideal state, for smelting operations and even for infrastructure operations, like subways and trains – what’s ideal, where are your losses from ideal and how can you effectively manage them? It’s a Socratic approach to managing any given system.
Conclusion
The purpose of OEE is to measure and manage your losses from ideal, a concept that can be applied to almost any system, production, or process. OEE is both tactical and strategic. Tactically, it provides information about day-to-day performance and areas to focus on to minimize losses. It’s an opportunity to engage the entire workforce in minimizing losses. Strategically, it provides information about potential capacity that does not require incremental capital, but could be available for new products and/or additional market share, or may represent an opportunity for rationalization of assets. For example, you may have five lines or 10 plants, but as you improve your OEE, it turns out you only need four lines or eight plants. It may be that you now have options about retiring the least productive or most expensive line/plant, the oldest technology, or some other business reason. The staff on those lines/plants would then become available for even more improvements.
The key is to use OEE for your future success.
* The author is grateful to Bob Hansen, author of Overall Equipment Effectiveness, and David Brown, CEO of MxStrategies, for their input on this article.
- Reliabilityweb Is Stock Turns the OEE of Spares Management? ›
- Reliabilityweb Why TEEP (Total Effective Equipment Performance)? ›
- Reliabilityweb The final 10% OEE - Achieving Operational ... ›
- Definition: Overall Equipment Effectiveness (OEE) - Reliabilityweb: A ... ›
- Reliabilityweb Overall equipment effectiveness (OEE) ›
- Reliabilityweb Determining an OEE Goal Based Upon Customer ... ›
- Reliabilityweb Do Not Be Misled by O.E.E. ›