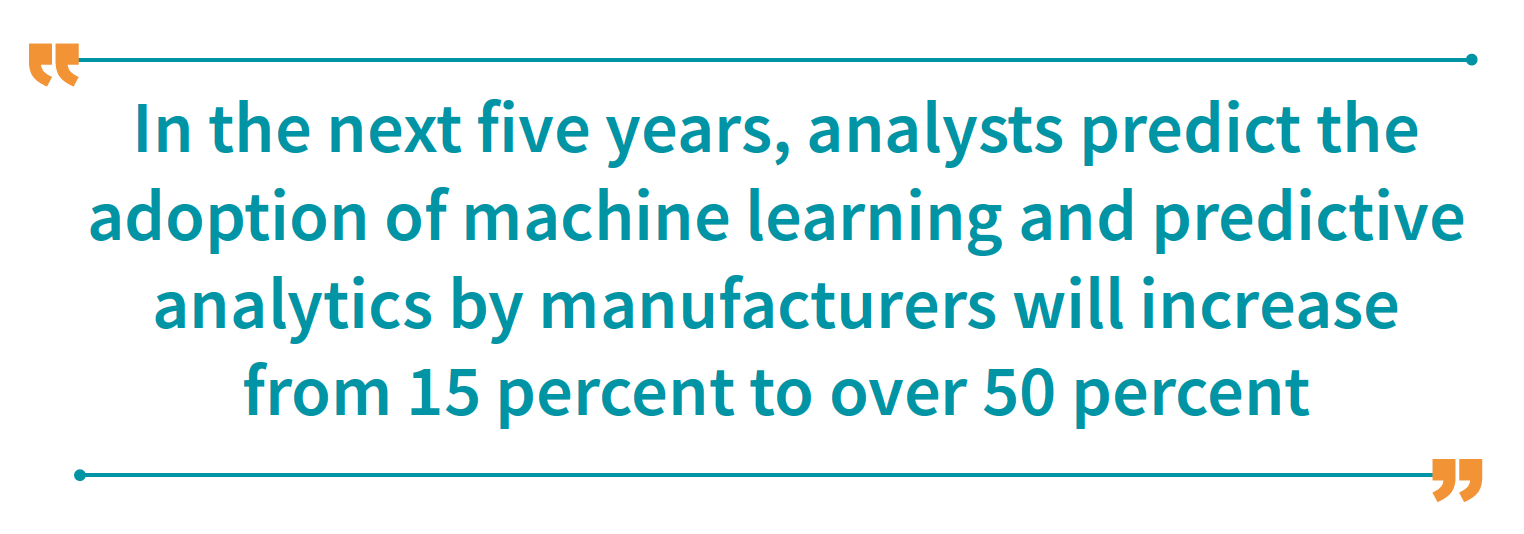

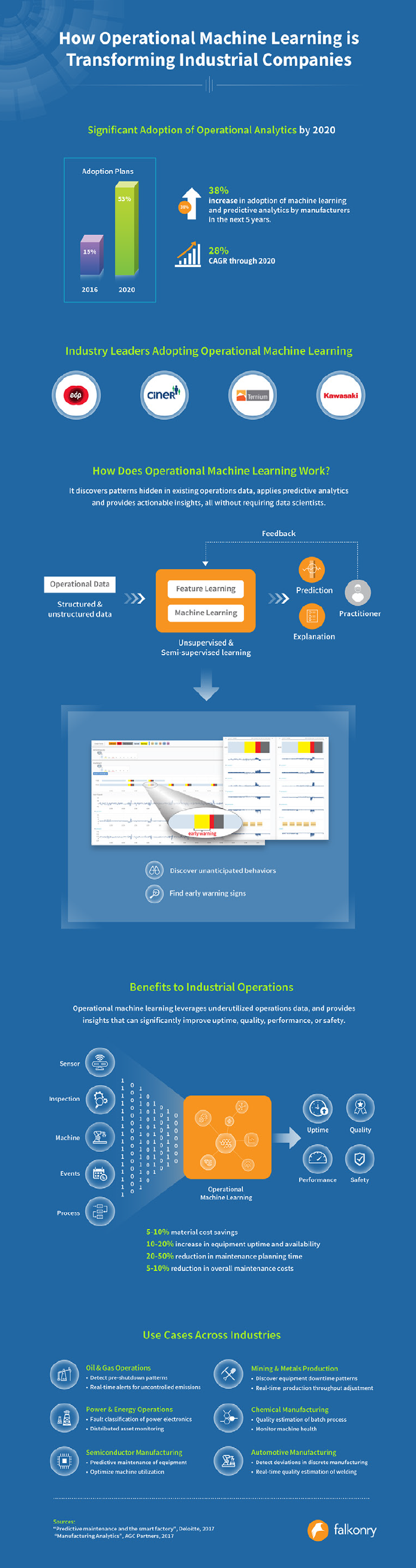

This technology enables operations teams to create significant business value by using machine learning and predictive analytics themselves, without the need for data scientists. The infographic in Figure 1 provides an overview of operational machine learning and how it is improving production throughput, uptime, quality and safety across multiple industries and applications.
In the next five years, analysts predict the adoption of machine learning and predictive analytics by manufacturers will increase from 15 percent to over 50 percent. The driving factor behind this is that the technology is no longer limited to data scientists. Companies have developed machine learning systems that are effectively a “data scientist-in-a-box,” which means the systems can be easily used and deployed directly by manufacturing engineers or process engineers, either in the cloud or on premises.
Using operational machine learning, companies can achieve initial results in less than three weeks and deliver five to 10 percent material costs savings, 10 to 20 percent increase in equipment uptime and availability, 20 to 50 percent reduction in maintenance planning time, and five to 10 percent reduction in overall maintenance costs. These gains represent significant savings in the order of millions of dollars annually for an organization.
Leverages Data Already Available
Another reason machine learning in industrial operations has become so popular is that it leverages time series data already generated by equipment and production systems in most discrete manufacturing and industrial process operations today. This data historically has been unutilized in operations, but machine learning can help industrial manufacturers discover hidden patterns in the data that cannot be observed by humans or traditional analytics. These patterns, in turn, provide insight on the operating state and identify conditions that precede undesired events to provide an early warning. Depending on the process being monitored, such early warnings may occur hours, days, or even weeks in advance, and can save several millions of dollars annually in operating costs. Figure 1: Operational machine learning overview
How It Works
Four key capabilities in a machine learning system make it easy for industry practitioners to begin reaping its benefits:
- Automated Feature Learning - The system discovers patterns in time series data. Once the patterns have been discovered in the data, machine learning can be applied.
- Prediction - You can select a pattern that appears consistently prior to the event and label that as a precursor. Based on the use case, the precursor can provide an early warning or prediction that ranges from several hours to several days ahead of the event occurring.
- Explanation - You can determine which of the provided data signals are actually required to make the prediction, as well as how much each signal contributed to that result.
- Flexible Deployment - In addition to running models on premises or in the Cloud, you can also deploy them at the edge. This can support low latency applications or disconnected environments that require being close to the data source.
Pattern discovery plays a critical role, particularly for assets, in identifying patterns prior to degradation occurring. This is crucial as it moves asset management from reactionary (i.e., degradation has occurred and you attempt to minimize its impact) to proactive (i.e., you prevent it from occurring).
By identifying patterns that are precursors to undesired events or operating conditions, these predictive systems can provide actionable insights on the current and future health of the production systems and the products they create. With this in place, an operational machine learning system can perform pattern discovery, condition monitoring and predictive analytics in real time on existing operational data.
Figure 2: Machine learning enables pattern discovery and early warning
Spanning Many Industries – Example Use Cases
Since operational machine learning discovers patterns in available time series data, it does not require developing mathematical models of a physical system or organizations having deep domain expertise in a particular industry. As a result, it is highly versatile and can be applied across industries, such as automotive, chemical, electronics and semiconductor, mining and metals, oil and gas, and power and energy. To illustrate the power of this technology, here are some sample use cases in both the semiconductor and automotive manufacturing industries.
- Semiconductor: A major semiconductor manufacturer operates complex, expensive equipment that executes many different types of step-based operations daily. Optimizing utilization through predictive maintenance is a high priority. The machines are instrumented to collect operational data every second in the form of sensor readings, control parameters and other settings. Use and benefits of this data proved ineffective in predicting faults to operators. The manufacturer decided to deploy a machine learning system, which was quickly integrated into its operational data store containing trace data, quality measures, and inspector and operator log information. A four-month history of data created a model identifying multiple, abnormal conditions known to create maintenance indicators, thus creating alerts in the system. The availability of advanced warnings provided by the assessment stream enabled early intervention by the maintenance team and resulted in an improvement in uptime and overall equipment effectiveness (OEE).
- Automotive: A leading automotive manufacturer needed to assess its welding quality in real time. The quality of its machine welds would vary over time, resulting in expensive manual rework of over $14,000 per machine, per day. Using a machine learning system, the company was able to discover patterns that precede quality variation in robotics welds and provide advanced alerts. This helped to significantly reduce downstream rework and material losses.
The Future
With the emergence of operational machine learning, the next industrial revolution is here. Whether you call it Industry 4.0, industrial Internet of Things (IIoT), or digital transformation, the increased access to machine and operational data, proliferation of two-way communications and speed of data flow, combined with the lower cost of computing, connectivity and storage, has created the perfect environment to transform industrial operations. The time series data generated by these operations, when harnessed effectively, can provide actionable insights to reduce downtime, as well as improve throughput, operator safety and product quality.
There is no better time for industrial operations teams to start harnessing the power of these systems now that specialized resources, such as data scientists, are no longer required to implement them.