By way of generalization, it has been said that all manufacturers operate with business models that emphasize either quality, low price, or innovation. Rare indeed is the entity that simultaneously and consistently achieves all three, or even only two of the three. Plain logic should convince us that if a manufacturer truly reached pinnacle status in all three, it would soon become the only surviving provider of the asset in question.
That does not imply there aren’t any capable, experienced vendors, but we have to find them and invite them to bid. Three principal characteristics1 identify such capable, experienced vendors.
- They are in a position to provide extensive experience listings for the equipment or components offered and will submit this information without much hesitation. (That is to say, beware of vendors hiding behind the smoke screen of “that’s proprietary” whenever we ask questions).
- Their machines or devices enjoy a reputation for sound design and infrequent maintenance requirements. Potential buyers must ascertain that a previously good reputation still holds true today after the provider has perhaps struggled through periods of mergers, downsizing and rightsizing.
- Their marketing personnel are thoroughly supported by engineering departments. Also, the marketing and engineering departments are willing to provide technical data or details beyond those customarily submitted with routine vendor proposals.
Vendor competence and willingness to cooperate are shown in a number of ways, but data submittal is one of the most discernible tests. When offering fluid machinery or components in compliance with the standards of the American Petroleum Institute (i.e., the latest editions of API-610, 617, 618, 682 or any other standard), a capable vendor will make diligent efforts to fill in all the data requirements listed on the API data sheets. However, the real depth of technical know-how will show in the way a vendor-manufacturer explains exceptions taken to either an existing API clause or a user's supplementary specifications. Most users are willing to waive some specification requirements if the vendor is able to offer sound engineering reasons or meets the design intent, but only the best qualified vendors can state their reasons convincingly. Buying from best qualified vendors should not, however, be misinterpreted as an encouragement to single-source or standardize just for standardization’s sake. And, of course, there are the occasional (but rare) exceptions when common sense directs us to consider deviating from the rule.
WHY THERE’S RISK IN SELECTING ONLY A SINGLE-SOURCE OF SUPPLY
Not all equipment purchases entail the same risk; occasionally single-sourcing may be appropriate. Still, single-source vendor alliances require carefully worded contractual agreements between user and supplier. Moreover, any such agreement must be fair to both sides. The agreement also must be enforceable and must later be actively enforced by the main parties. We will start out by using mechanical seal partnerships (or “seal alliances”) as our first example.
CAVEATS IN SEAL PARTNERSHIPS
Many mechanical seal alliances or partnership agreements are made by an owner’s purchasing department. Unless a competent reliability engineer is involved, contracts usually end up being awarded to the lowest initial cost bidder. In those instances, seals get cheap and everything else gets costly. Safety and reliability are among the first victims.
Therefore, leading user companies choose to involve their most knowledgeable seal specialist and, ultimately, a perceptive legal adviser. The user’s team recognizes its primary options and then moves in one of two possible, but different, directions:
Option (a): The parties enter into a performance- based contract. Seal life extensions (fewer failures) are rewarded and both sides hope to benefit.
Option (b): The owner-purchaser buys only about 80 percent of its seals from reputable Vendor “A” and 20 percent from reputable Vendor “B,” or Vendors “B” and “C.”
In the single-source situation described as Option (a), some alternative flush plans historically have not received wide acceptance. There may be a need for elaborate cooling auxiliaries in old-style seals. In these, flush circulating devices or elementary pumping rings are still applied by the average single-source provider. Therefore, not all seal manufacturers are able or willing to provide the best solution from the seal user’s vantage point.
However, modern, computer controlled manufacturing methods have helped implement superior sealing technology and it’s in the user’s interest to capitalize on that. Purchasing from two or three vendors, as described in Option (b), makes the agreement with principal provider “A” self-enforcing. Each manufacturer knows that the purchaser’s reliability engineers have other choices. This gives manufacturers “A,” “B” and “C” an incentive to put their best talent to work. Competing manufacturers or vendors tend to provide better service and product quality, accordingly, the user benefits. Competing vendors are more receptive to implement well-engineered and highly innovative solutions.
As an example, review the high performance pumping rings in dual seals in Figure 1. Suppose an owner-purchaser deals exclusively with Vendor “A” and assume that Vendor “A” does not offer this type of pumping device. Unless the owner-purchaser uses the approach described as Option (b), superior products may not easily find their way into the facility.

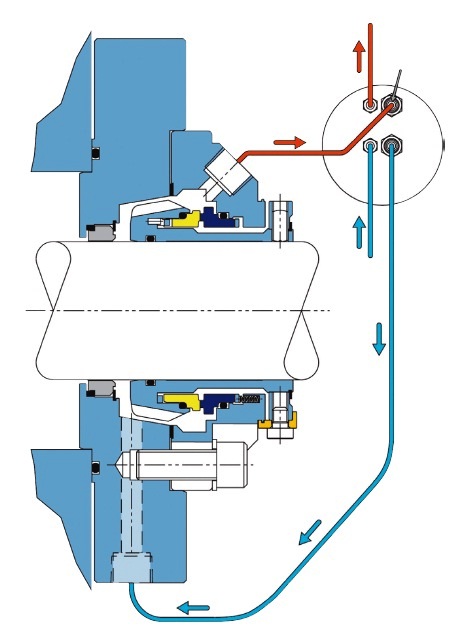
Figure 1: Plan 23 cross-section of a seal cavity with a bidirectional (tapered) pumping device. The flush fluid is product that passed through the throat bushing on the left. After being cooled in a small heat exchanger (upper right), this product re-enters the seal. A bi-directional tapered pumping device promotes relatively high flow rates and thus cooler face temperatures. (Source: AESSEAL Inc., Rotherham, UK and Rockford, TN)
This is why a number of best-in-class users prefer Option (b), the 80/20 approach. Option (b) keeps these users and their reliability engineers informed about technology advances and lifecycle costs. The two or three providers of sealing components, bearings, or gaskets participating in Option (b) become the user’s technology resources and networking partners. If one of the providers does not perform well, the others will step in to fill the gap. The user and competent partner companies benefit from this open networking arrangement.
While often used, single-source, performance-based contracts described in Option (a) are not always easy to interpret or enforce. In the eyes of the provider’s management, the user-partner is in it for the long term. Accordingly, the provider may give priority to cultivating other potential customers and the long-term user-partner will suffer in the process. The seal provider often sets up a resident seal specialist at the user’s site. But perhaps the supplier-partner’s resident representative does not meet all of the user’s expectations and the resident specialist’s influence at the seal manufacturer’s factory or the provider’s principal engineering offices is often rather limited.
As an example, after finding many new seals that leaked from the day they were commissioned in 2011, a very large U.S. refinery began testing every mechanical seal before installation. Fortunately, there was a performance clause that allowed flawed products to be rejected. The seal manufacturer’s quality subsequently improved. Single-source contracts without performance clauses and routine procurement from a single-source vendor can burden the purchaser with even more serious quality control issues.
Another example involves electric motor lube issues and purchaser’s indifference plays a role here. At a 2013 reliability conference, a user related a situation where several, large grease lubricated 13.2 kV electric motors required bearing replacements after a single year of operation. While much more detail would be needed to zero in on the root causes of this unacceptably high failure frequency, the feedback illustrates what happens when lowest bid price is of paramount importance. At certain speeds, grease lubrication may impede reaching a user’s projected reliability goals. And at all speeds, excessive pressure on greases and non-optimized grease paths will take their toll.
Users with true reliability engineering expertise understand all and will specify most of the items listed on motor nameplates. The motor winding life effects of buying a 100 hp motor with a service factor of 1.15 versus a 115 hp motor with a service factor of 1.0 are understood by good reliability engineers. Also, whenever bearing data on motor nameplates are incomplete, competent reliability experts seek clarification. To manage an effective lubrication program, one needs to know grease entry and exit locations, whether or not there are shields and where these shields are located relative to the grease reservoir. The issue at hand is illustrated in Figures 2 and 3, although many more configurations are available.2
Figure 2: Grease injection at Point 1 without first removing the plug in exit Point 2 is almost certain to (a) push spent grease into the bearing and (b) force the shield into troublesome contact with the rolling elements.
Serious failure risk exists if, in Figure 2, grease is injected at Point 1 without first removing the plug from exit Point 2. High-pressure “new” grease is almost certain to push some spent grease into the bearing and force the shield into contact with the rolling elements. This vulnerability did not escape ARCO Alaska who, over 30 years ago, opted to remove the drain plug and replaced it with a length of pipe, as see in Figure 3. The drain pipe terminates in an elbow and a short nipple. The threads on the open side of the pipe nipple must be mangled so as not to allow capping. In Figure 3, a plug of spent grease is always located in the drain pipe and over-pressuring the grease reservoir is no longer a threat.3 The “old plug” gets expelled at the time of regreasing (grease replenishing).
Figure 3: An inexpensive and very effective way to prevent over-pressuring the grease reservoir.4
Understanding the design intent of shielded bearings is of paramount importance. Shielded bearings are to be used in housings where grease resides in the adjacent reservoir. The oil contained in the grease is supposed to “bleed” from its soap matrix past the small annular gap into the bearing. Greases have different bleed points for different applications and, for long life, superior motor greases should not be exposed to pressure for more than just a few minutes. Although homogenous at the point of original manufacture, most greases under pressure will separate into their soap and oil constituents.
Different bearing housing types or directions of grease flow are shown in Figure 4. On single shielded bearings, the shield should face the grease reservoir. Installing the shield away from the grease reservoir causes 100 percent of the bearing to be filled with grease. Bearing manufacturers are unanimous in recommending bearings to be filled only 30 to 35 percent to prevent churning and overheating of the grease.
Figure 4: Different types and directions of grease flow. Understanding the design intent of shields is of paramount importance: Grease resides in the adjacent reservoir and oil is expected to “bleed” from its soap matrix past the small annular gap into the bearing. Greases are compounded with different bleed points for different applications; superior motor greases should not be pressurized.
Chances are that single-sourcing electric motors from the lowest bidder will deprive diligent users of a comparison basis. Having electric motors from more than one source also provides an excellent learning opportunity for grooming newly-hired personnel to become the diligent reliability engineers of the future. Diligent engineers know how things work; they never confuse facts with mere opinions. That said, understanding why some reputable motor manufacturers went through the trouble of adding a separate shield in front of shielded bearings (see Figure 5) is of interest. The Reliance Electric Machine Company called it a “metering plate” and hoped that no attempt was made to squeeze grease through the gap between shields and bearing inner rings. Oil was to bleed through that gap and no grease -- an oil-soap mixture -- was to be introduced by brute force. Having this understanding then reemphasizes the three important points of (1) not making the lowest bidder your only source, (2) incorporating lubrication details in the motor purchase specification, and (3) learning and teaching facts instead of opinions.
Figure 5: In this 1970s vintage bearing housing, the electric motor manufacturer placed a metering plate in front of a double-shielded bearing. The motor manufacturer thus reduced the risk of applying excessive pressure to the bearing shield adjacent to the grease reservoir.
The message is this: Why lock yourself into the wrong bearing style? Pursuing Option (b) will likely prove highly informative. The key is to work with only the most competent manufacturers. Understand who they are and do not get wedded to the one who claims to be both best and cheapest.
Another aspect of our topic, why single-source supply contracts can disappoint, is the subject of a follow-up article in the next Uptime issue.
References
- Bloch, Heinz P. Improving Machinery Reliability, 3rd Edition. Houston: Gulf Publishing Company, 1998.
- Bloch, Heinz P. and Budris, Allan R. Pump User’s Handbook: Life Extension, 3rd Edition. Lilburn: Fairmont Publishing Company, 2010.
- Bloch, Heinz P. Practical Lubrication for Industrial Facilities, 2nd Edition. Lilburn: Fairmont Publishing Company, 2009.
- Bloch, Heinz P. Pump Wisdom: Problem Solving for Operators and Specialists. John Wiley & Sons, Hoboken, NJ, 2011.