These are all questions that should be addressed by the PM procedure, along with instructions on how to perform the task(s). The more information omitted, the more likely it is that mistakes will be made, such as using the wrong lubricant, missing lube points, over/under lubrication, etc. Well documented lubrication PMs allow for precision and consistency in execution, which are key elements in a precision lubrication program.
The first step in creating an effective lubrication PM program is to assess the current program. If the current program is found to be inaccurate or lacking greatly in detail, the best path forward may be to start over. Begin with an accurate equipment list and then break the equipment down into a hierarchy that works with the type of equipment you have. You may want to assign PMs at the machine level, the component level, or the lube point level, depending on the complexity of the equipment. With the lube points identified, the next step is to identify the required lubrication tasks and determine the optimum frequency for each. Each type of lubrication task has required variables, such as lube type, amount, required operation state, etc. Create a simple spreadsheet or database to house this information for inclusion in the documented PM procedures. There is really no one size fits all solution for this item, but using a systematic approach will make this project surprisingly simple.
EQUIPMENT HIERARCHY
A well thought out equipment hierarchy is a crucial foundational element for the program design work. The hierarchy should have enough layers to accommodate the necessary data collection at the beginning and later to sort tasks in lube routes. In some cases, such as with mobile equipment, it is more practical to create PMs for an entire machine and assign tasks based on coinciding frequencies. With mobile equipment, it is common to assign multiple tasks to multiple lube points in a composite PM that combines all the tasks that should be executed at a particular time. For stationary equipment, it is usually more efficient to create PMs that assign a particular task to the component or lube point level. Later, these tasks can be sorted into convenient lube routes by application type, lubricant type, frequency, etc. Regardless of the level to which PMs are assigned, the individual tasks and their variables should be associated at the lube point level. A common hierarchy structure for lubrication program engineering would be: plant, unit or area, process, machine, component, then lube point. In many cases, the component will only have one lube point, but the structure should still be consistent.
TASK ASSIGNMENT AND TASK VARIABLES
With the detailed equipment list and hierarchy in hand, the lubrication tasks can be identified using a variety of sources, such as equipment maintenance manuals. For the most part, lube points of a particular type will generally have the same tasks. For example, a wet sump lube point, like a gearbox, will have a routine inspection and an oil drain and fill at a minimum, and possibly other tasks, such as oil sampling, off-line filtration and others. Once the tasks are assigned, the necessary data fields or variables for a particular lube point can be identified based on the type of component and the associated tasks. Remember, more information is better, so when creating data fields, try to consider any information that could be useful. In addition to the primary data, such as component type, make, model and size, include other information, such as operating temperature, vibration, contamination and other environmental factors that might lead to deviations from standard practices or task frequencies.

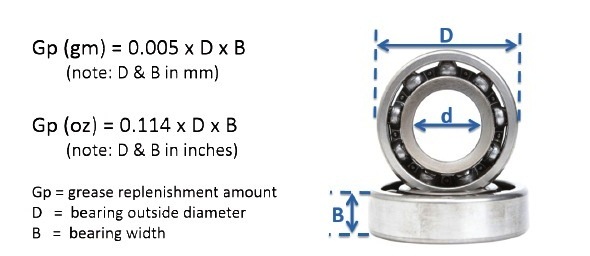
Figure 1: Calculated values, such as grease volumes, should be determined using valid engineering methods. In addition to documenting the values, the methods also should be documented for future validation.
CALCULATIONS
Many data field values, such as lube specs and sump volumes, can be looked up in original equipment manufacturer (OEM) literature, but others must be calculated or determined using standard lubrication engineering techniques. Grease volume and application frequency are two such values that typically require some calculation or research to obtain the optimum value. If there is insufficient expertise on staff to determine these values, it is a good idea to bring in outside help, or at least consult with a subject matter expert. Methods for determining these values are available in lubrication engineering texts and bearing manufacturer manuals, but recently, some manufacturers, have created software applications that do much of the work for you. If one of these applications is to be used, it is still a good idea to become familiar with the underlying principles to help rationalize the computed values. Additionally, lubricant specifications are not always available, or they may lack sufficient detail. If an OEM manual just lists particular lubricants, then that product type should be converted to a generic specification so it can be cross-referenced to a product already in use.
PUTTING IT ALL TOGETHER
A good lubrication PM should serve more than one purpose. It should serve as a training tool for new technicians or those unfamiliar with the job, and as a checklist and feedback tool for experienced technicians. To make this practical, two versions of each PM procedure should be created in both a long and an abridged format.
The full or long version procedure should follow a standard procedure template that includes task name and asset identification, purpose, scope, summary, detailed instructions and safety considerations. The task procedure instructions should contain sufficient detail to allow technicians to complete the task even if they are unfamiliar with the equipment. If the machine or component contains multiple lube points, an annotated picture or detailed rendering should be included to identify each lube point. Be sure to use consistent nomenclature when naming components or lube points. It is not uncommon for different individuals in a plant to refer to the same component by different names. Again, the pictures or drawings should avoid confusion.
The abridged version of the procedure is intended to serve as a checklist for an experienced technician. Step-by-step instructions on how to drain oil or apply grease are not necessary, but certain items should still be included. The most basic details, such as the lubricant type and the amount to be applied, should be on any lubrication PM. In addition to the basic information, checklist items also should be included, especially for inspection items. Even the most experienced mechanic can miss something from time to time if there is no prompt on the PM worksheet. The final item on the abridged procedure should be a section for feedback. A lack of a proper reporting mechanism may result in observed problems slipping through the cracks until it is too late to correct them.
When creating new procedures, it is a good practice to include technicians in the design process. Because of their familiarity with the equipment, their input will likely streamline the project, identifying problems before the new procedures are deployed.
EXECUTION
Once the new program is complete, everyone in the program should be trained on the proper execution of common tasks. This will help ensure that tasks are completed to the desired standard and performed in a consistent manner. With some tasks, such as taking an oil sample, consistency is almost as important as quality.
LONG-TERM BENEFITS
Properly documenting procedures for lubrication tasks not only increases the quality of the program today, it helps ensure success in the future. In the absence of good documentation, the program really resides in the minds of individuals who can retire, change jobs, or leave the plant at any time. If this happens, their experience, education and training will leave with them. With an aging workforce, this is an ever present risk, so protect your program and your hard work by documenting everything, including the decision-making processes. By documenting the methods used to make lubrication decisions, such as lube specs and grease volume, those who come behind you will be able to carry on the program and avoid starting over.