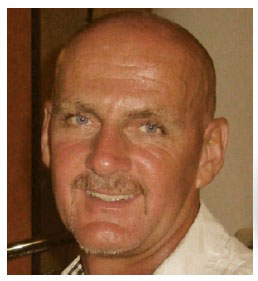
Q Leo, you recently attended CBM 2012 as a guest speaker and created quite a ripple among attendees. Your presentation, "My Journey with Ultrasound," was inspiring and thought provoking. Can you talk about the products your company produces?
A Mississauga mill produces linerboard paper from 100% recycled fibers. We produce several grades and they vary from 127 grams to 337 grams per square meter. We also produce a grease-resistant paper that is used for pizza boxes, etc., as well as a product for food and deli containers. There is also a paper produced here for the gypsum board industry. Colors of our products include different shades of brown, as well as white. In my opinion, this is a very universal mill because we can run a product per request to weight according to customer demand.
QThere is a lot of emphasis out there for establishing a world-class condition-based maintenance program. What was the driving force for Norampac to get this program off the ground?
A With the emphasis on establishing a worldclass condition-based maintenance program, several factors inspired Norampac to take on this endeavor. One, in particular, that affects Norampac-Mississauga is the opening of a new green pack paper mill in the near future, which will be in direct competition with our product lines.
In addition, the struggling paper industry impacted by new products and high energy costs and raw materials were other factors. Prices escalating have set the stage for an efficient maintenance process. The traditional maintenance programs that replaced equipment on timelines proved to be expensive and often ineffective. In many cases, equipment being changed out were still in excellent condition and did not require replacement. Knowing, understanding and monitoring our equipment has created a maintenance environment that is cost effective and reduces maintenance labor requirements, parts, cost, etc.
Q For many people, a journey like yours never moves forward. Can you help our readers take the first step to success by sharing what your first priorities were?
A My first priority for this journey to be successful was for me to take ownership, be responsible and consider any room for failure not acceptable. The following step was for me to obtain training and knowledge in all fields of predictive maintenance tools that were at my disposal. The next step, and maybe the most important one, I think, was to get myself introduced to each and every piece of equipment and the process perimeters in which it operates.This also would be a definite asset since, coming from a mechanical and electrical trade background, it gave me an advantage for achieving my goals.
Q How important was the support of upper management and, ultimately, corporate level sponsorship of your initiatives?
AThe support and understanding from management at the corporate local level cannot be underestimated because without it, the process will fail. Management must clearly set the stage for the initiative and be an active member in the process. In all successful industries, strong leadership creates an environment for evolving and progressive workplaces, allowing these programs to flourish.
Q What would you say is the most important thing you did to ensure continued management and corporate support of your efforts?
A Provide real-time results, proven reliability, lower maintenance costs, decreases in stores inventory, better defined planning and scheduling, and increases in production availability. Quick return on investment from the overall cost of the predictive tools assured continued support.
QTell us about some of the biggest wins uncovered by your CBM program?
A Some of the biggest wins uncovered by our CBM program would be:
- Our steam consumption cost reduction;
- Better reliability on over greasing;
- Overall reduced maintenance costs;
- Witnessed a decreased breakdown or urgent work orders.
So to sum it up, the biggest success in my opinion would be that predictive maintenance provided us with the ability to conduct repairs in an organized environment, resulting in equipment life utilized to its maximum potential. As a result, maintenance costs, such as contract labor, parts, etc., were drastically reduced.
QWhat condition monitoring technologies do you use at Norampac? Are some more useful than others?
A This is where when you venture into predictive maintenance, to have the ability to make decisions as to how you will measure equipment, you appreciate all the technology at your fingertips. This is where we have the overall advantage. We use all the CMTs: ultrasound, infrared, vibration, motor current analysis and oil analysis.
For which ones are used more fully than others, well we are now two years after conducting surveys and implementing best practices for which tool will give us the best return on value. With regards to knowledge, we now grasp that using these technologies has given us a greater understanding that over-monitoring can easily be applied also, so be cautious. For the best practice, I have found from using these technologies that one might say that a degree of common sense has to be the provider. Let me explain. Early prediction as possible has to be the key to great success in keeping equipment from failing. Ultrasound, in my opinion, would be the first defense in predictive maintenance, and all other tools would be complementary. This strategy has been my greatest ally, while keeping in mind that one cannot or should no exist without the other. I am not being bias, but if the only predictive tool you are using, whether being one or the other, it can and has been proven to be a definite asset to any predictive department.
I have learned from years and years of firefighting on the floor; I know what it is like on a hot summer day at four in the afternoon on a Friday when you have a major breakdown and you have to do a changeout, whether it was a motor, bearing, fan, or any other piece of machinery. Then on Monday morning, you're told that this could have been avoided if you were conducting predictive measures and yes, only if we had the tools and the knowledge to do so. This is where I consider myself fortunate that I was introduced to predictive maintenance best practices and given the opportunity to excel.
Norampac-Mississauga's 10 million dollar press is monitored by ultrasound analysis, vibration, infrared and oil analysis.
QIt seems like you have gotten a ton of mileage out of ultrasound technology. Talk to us about that.
A Yes, to me, making this statement has to be one of the best learning curves that I encountered. I was introduced to SDT ultrasound, educated by one of the most distinguished, in my opinion, ultrasound and vibration educators, knowing now what I have learned over the last couple of years, I am fortunate to speak about the miles I walked. This educator is Tom Murphy from SDT Ultrasound Solutions, and he first told me that an ultrasound inspector has to create his database, create his routes and survey his equipment. Well, I did just that. I went through the entire mill here and looked at every piece of equipment. Surveyed steam traps, did air loss surveys, monitored bearing and motor deficiencies, and also used the ultrasound to scan electrical rooms before I conducted any infrared scans. I spent two years coming and going, getting data, predicting failures, troubleshooting, and pushing the technology and its database to its limits. Then there is the one thing that Tom told me that I am only now starting to apply. He said, "When you understand the technology and you adapt to its capabilities, share it!"
To date, we have introduced the technology to all 18 mechanical technicians, to all the electrical personnel and instrumentation users. The ultrasound technology is currently being widely used throughout the mill. Not only one unit, but several units
The results of the first steam trap survey showed that of the 164 steam traps surveyed, 24.2% were either failed closed/failed open or by-passing. The lost revenue was $275,000.
Safety as a justifier. Electrician using the SDT270 Ultrasound Detector before starting the annual infrared electrical scan.
QHow important has training and certification been to your success?
A To me, it has been a positive return. But this can be controversial to some since it's one's self achievements that only can be measured from training and certification. I have exceeded in this journey from education, training and learning from the knowledge of others. There is an old saying and where it came from I'm not sure, but it asks, "How can you ask someone to perform a task if first you don't understand how to do it yourself?" Education has always been a positive endeavor for me.
QYou told us about vendor certification training, but you also mentioned implementation training from the same vendor. Which would you say provided the biggest value and impact for your team?
A The biggest value and impact for us was to have a vendor like SDT Ultrasound Solutions to not only sell us a piece of equipment, but to have their continued support as an industry leader. Their knowledge and expertise in this field gave us confidence to venture on in our journey because we knew we were not alone. We were fish out of water and their profound training and support was what contributed to our success. This has to be, as far as I'm concerned, at the front of the table when trying to decide which vendor will be introduced to any facility. Long-term engagement definitely has to be the utmost concern. When things go wrong, and they will I'm sure, having a vendor that will build a relationship not only for sales, but for technology growth, has to be the front-runner for any predictive maintenance success. Vendor implementation will provide a shorter timeframe for achieving your goals. They are subjected to all industries and have the knowledge and feedback that people are searching for.
QNothing ever goes 100% as planned. Share with us some of the trials and mistakes made along the way.
A One would think that when we have everything in place, when we balance predictive and preventive maintenance, we would never have another failure. Wrong! There were times when we detected bearing faults, motor deficiencies, etc., and scheduled a planned shutdown to correct these measures, but then we had a premature failure. This is where we learn from our root cause analysis; there are so many variables in the mechanical and electrical components associated with industry that one could only expect to predict early enough to act accordingly to address it before failure. I think one of the greatest assets that would be beneficial to everyone would be to evaluate the effects of improper installation or maintenance. Applying the strongest proactive measures can decrease the amount of time needed for applying predictive measures.
Before revising the grease schedules for the roller bearings, the temperature was 123 deg C. After ultrasound inspection, it was 39 deg C.
All new bearing installations will have a baseline created under the UAS software as a first defense detection against early stage warning defects.
QIt would seem you have everything in place at your Norampac mill for continued success. Where will you go from here?
A We will look at how to balance CBM and our PM inspections in order for us to have a more effective maintenance strategy. We are going to introduce more employee training on the PDM tools, and embrace to our advantage the benefits from this education and training. Education is an equal opportunity for everyone. Learning from each other and evaluating our wins and losses builds for a better team.