Also at IMC, another significant milestone was being celebrated by those who recently updated the "Reliability Centered Maintenance Project Manager's Guide,"published by Reliabilityweb.com. This valuable guide was originated by Jack Nicholas, Jr., 10 years ago with the assistance of participants at the Reliability Centered Maintenance Managers' Forum in Clearwater Beach, Florida, the very first conference ever devoted strictly to reliability centered maintenance (RCM). This author commented at the IMC RCM presentation that one would be wise to pay the same attention to the project manager's guide that was being paid to the ISO55000 tracks. While the presentation was well attended, the gathering should have overflowed to the hallways.
Here is why.
We now have an international standard,which if adopted by any organization, requires that activities associated with the management of assets be risk based and that these risks be thoroughly evaluated and documented in the context of the significance of the asset and how it relates in realizing (or not) the higher level strategic business requirements of the organization. In other words, there must be a transparent line of sight (another term introduced at the conference) from all asset management activities right up to the decisions, policies and objectives made in the boardroom. This article suggests that RCM is a vehicle to provide that line of sight.
In a white paper entitled, "RCM Method and Means," presented at the 2010 RCM conference in Fort Lauderdale, Florida, this author and Eric Stevens wrote that, "RCM is a technical accounting system that details the functions and functional failures of a system and methodically leads an analyst through a series of decisions to prescribe maintenance tasks to prevent or mitigate the occurrence of functional failure. When implemented,one can trace back just why a maintenance task exists and the intended benefit." We went onto say, "If we fully expect that all expenditures of a company be thoroughly documented by sound accounting standards for future audit, then why would we expect less for documenting the purpose of a company's assets and the strategy in preserving their need?" And so, in RCM training sessions conducted by this author, the questions typically posed to the audience are,"Why does this asset exist?""Why was it purchased and why is it maintained? The answers are not always clear.
Figure 1 provides the line of sight from components to critical system functions for the Central Arizona Project. Noted RCM author Anthony "Mac" Smith, who devised this matrix, refers to this relationship as the connecting tissue between component and system. The value of assets lies not in the asset itself, but in the interrelationship the assets have within a family of assets - a system - to create value. Preserving the owner's needs of the system through effective asset activities is the most efficient policy.

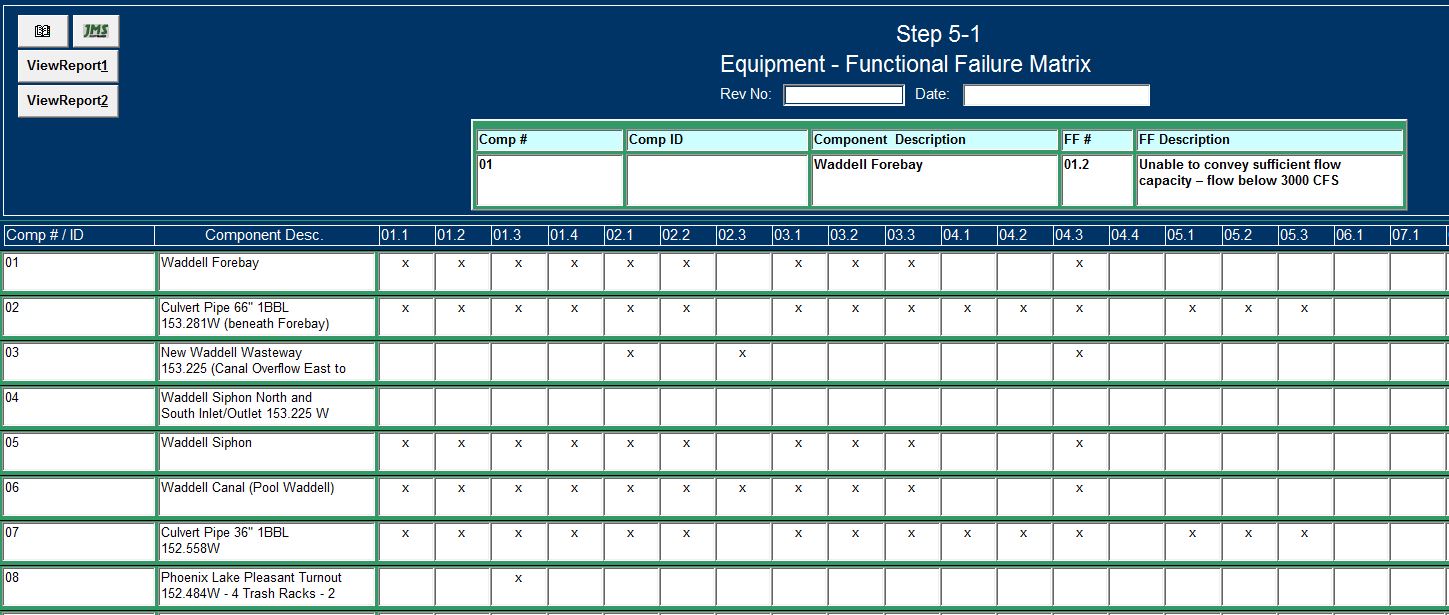
Figure 1: Functional failure matrix for RCM equipment for the Central Arizona Project diversion canal
Many have reacted through the years that wide scale RCM efforts are impractical. However,the benefits of a comprehensive RCM program have long been proven. Stevens and his colleagues at the Metropolitan Sewer District of Greater Cincinnati recognized this benefit, stayed the course and demonstrated with evidence how they managed to control critical systems through the RCM process. They are now proud recipients of two prestigious Uptime Awards.
ISO55001 requires an organization to determine “actions to address risks and opportunities associated with managing assets – taking into account how these risks and opportunities can change with time by establishing processes for:
- identification of risks and opportunities;
- assessment of risks and opportunities;
- determining the significance of assets in
- achieving asset management objectives; and
- implementation of the appropriate treatment
- and monitoring of risks and opportunities."
This article proposes that for these “risks” to be identified in any practical manner, they should come in the form of probable and possible asset failure modes and assessed in the context of a failure mode and effects analysis (FMEA), thereby enabling determination of those most consequential. Of course, to be relevant in the eyes of the ISO standard, these asset failure modes must be identified to specific system or asset functional failures that compromise the purpose of the system, as well as to strategic objectives of the organization. In other words, there is no better method and decision-making criteria for meeting procedural step 4.2 of the ISO requirementsthan the RCM process itself. The RCM logic tree to evaluate the applicability and effectiveness of a maintenance requirement was invented over 50 years ago by United Airlines.
To fully comply with the standard, one would need to take the RCM process a few steps further than traditional RCM and link asset or system functions to organizational business objectives, with such objectives documented in a strategic asset management plan. Take it one step further and envision RCM system functional statements transforming to include corporate priorities, such as energy efficiency, stakeholder values and other strategic objectives vital to the success of the company.
ISO55000 clearly states that the organization should establish a method with decision-making criteria to determine the risks and opportunities that must be addressed with asset activities to prevent or reduce undesired effects, and that these activities and resources be prioritized. It further says, “Asset management translates theorganization’s objectives into asset-related decisions, plans and activities using a risk based approach.” Therefore, asset criticality ranking systems without detailed documentation as to why such rankings have been assigned would not meet such criteria. The standard clearly looks for assessment, determinations and documentation of such to connect the dots. Preventive maintenance (PM) optimization does not do this. Original equipment manufacturer (OEM) maintenance recommendations do not do this and neither does PM templating. It is RCM that maintains the line of sight right from the applicability and effectiveness of PM tasks to maintaining the organizational need for the asset or system.
ISO55000 is silent to the words reliability centered maintenance and its acronym, RCM. However, if RCM didn’t already exist, wouldn’t we now have to invent it to comply with the standard?
The Reliability Centered Maintenance Project Manager's Guide is available at no cost www.reliabilityweb.com