Q. Jim, we understand that your company, Technical Associates of Charlotte, has just certified its 10,000th vibration analysis student. That is quite an accomplishment and aligns well with Uptime Magazine's mission of promoting professionalism in the maintenance reliability community.
What is the secret to getting management to support this important employee development resource of Vibration Analyst Certification?
A. It is primarily plant and corporate management that has driven certification of vibration analysts. We initially encountered this in early 1989 when a multinational corporation needed to get a solid feel on how their Predictive Maintenance (PdM) programs AND their PdM analysts stacked up in comparison, not only with their own plants worldwide, but also how they compared with PdM programs in other corporations both here and abroad. Thus, we initially conducted PdM program audits (benchmarks) at various facilities of this one corporation, then expanded our audits to encompass programs implemented at a number of other corporations. After completing this comprehensive study, one big question remained in the mind of management - "How do we evaluate the knowledge and expertise of our own PdM analysts at each of our plants?" After much deliberation, Technical Associates was asked to develop a meaningful vibration examination that could be given at their plants worldwide to gauge the relative knowledge and skills of a large number of such analysts. When this initial exam was developed and given, the results proved to be very revealing. There were obviously some analysts who possessed a high skill set in vibration while others had much to learn.
A request was then made for an even higher level of vibration examination that again was given at a wide number of facilities, not only at this corporation, but also at outside companies who had PdM programs. This higher level exam revealed a great difference in what analysts knew and understood, and allowed management to obtain one of their initial objective assessments of what their analysts did and did not know. Near the end of 1989, we discovered that the biggest single factor revealed under scrutiny of the examinations was the amount of formal training such persons had or had not received. Some plants had analysts who had been doing vibration for many years but unfortunately had not received formal training (other than how to use an analyzer or PdM software; but not on how to detect problem conditions or faulty components from the data being captured). These analysts were doing the same thing for many years but were predominantly building large PdM databases requiring much storage; however, they were not benefiting from making diagnostic calls, evaluating problem severity, and recommending proper corrective actions on a wide variety of machinery types. On the other hand, it was found that those analysts who successfully passed this initial set of vibration examinations had for the most part received at least some training on how to interpret the data, find problems and make recommendations. Audits of programs at such plants showed much more effective PdM programs that were achieving substantially higher savings in maintenance costs and increased machine reliability and availability. Thus, "the roots" of vibration certification were born, and in 1990, our company began to give them to analysts from a wide array of industry types under the watchful eyes of both individual plant and corporate management.
Q. How have you been able to certify over 10,000 vibration analysts?
A. Technical Associates was the first organization to offer vibration certification beginning in 1990. Since then, we have worked with certification-test psychometricians on several occasions, not only to ensure our examinations met strict professional requirements, but also to assure our tests met requirements of published standards that stipulated what was to be taught in seminars and what was to be evaluated in accompanying examinations (see information on such standards below). When we initially offered such examinations in the early 1990s, only about 25% to 30% of students elected to take them. Later, as management began to realize what certification testing could do for them, more and more students took these tests. Today, approximately 85% to 90% of students take the exams following our public seminars, and most all clients desiring in-plant (on-site) classes elect to have their analysts tested. It is interesting to note that this percentage grows higher as our students take higher level certification exams, with the highest percentage being at ISO Category IV (the highest available certification level). Currently, only two organizations in the United States now offer ISO Category IV certification - Vibration Institute and Technical Associates. It is a prestigious certification level.
Some persons have asked "Why is vibration certification important?" Certification serves as documented evidence that an analyst has successfully comprehended the topics and techniques taught to him or her within formal seminars. Certain corporations have begun to require certification in order for analysts to remain within a PdM team (not only for vibration, but also for other PdM technologies). In addition, some companies require that all consultants, like Technical Associates, have a minimum certification level (or "category" in the case of ISO). Finally, beginning approximately 15 years ago, certain insurance companies began requiring a minimum certification level by at least one person on a plant site to even provide coverage; and some providers began to offer discounted premiums to facilities who had a certified vibration analyst of a minimum level on site (typically Technical Associates Level II or ISO Category III).
Q. Is Vibration Certification based on any published standards?
A. Probably the leading two published standards of today are ISO 18436 entitled "Condition Monitoring and Diagnostics of Machines - Requirements for Training and Certification of Personnel"; and the ASNT SNT-TC-1A document entitled "Recommended Practice No. SNT-TC-1A: Personnel Qualification and Certification in Nondestructive Testing" established by the American Society for Nondestructive Testing, Inc. The main purpose in adopting and complying with ISO 18436 and ASNT SNT-TC-1A is to have a worldwide recognized set of standards that stipulates what topics are to be taught in class and evaluated by certification exams.
Q. How has Vibration Certification changed since the ISO 18436 standard was published?
A. Probably the biggest change ISO 18436 brought about was the introduction of an additional certification level - ISO Category IV. Category IV was a notable step above Category III, requiring much more in-depth understanding and proficiency with more sophisticated techniques and analytical tools. Even though many of these more advanced techniques and topics were taught by various training organizations, many of them had not yet developed certification exams of these topics. ISO Category IV requirements forced such development of exam questions and answers (in our case, we had taught "Advanced Vibration Analysis" for nearly 15 years but had never developed a test to evaluate how well students comprehended the topics taught). The other change ISO 18436 required was greater emphasis in Category IV on some topics not formerly covered in-depth by certain training organizations. Such topics included rotor dynamics, experimental modal analysis, torsional vibration, etc. Finally, one other positive thing ISO 18436 brought about at all category levels was standardization of seminar topics to be taught and evaluated on certification exams worldwide.
Q. Is Vibration Certification only for technicians and engineers, or should managers consider earning certification?
A. At first thought, one would not normally think a manager would need to be certified at any level in a technology such as vibration analysis. However, our experience has proven to be different, particularly at lower certification levels. The problem that has plagued programs worldwide has commonly been that management initially supports PdM when a number of the more obvious problems are caught and corrected by the PdM team. However, after this initial success and visibility, many programs have fallen into oblivion if management is not continually kept informed of problems detected and cost savings achieved by the PdM Team. This is particularly the case with vibration analysis since it is not normally well understood by most all management (even degreed engineers) since universities do not typically teach rotating machinery vibration analysis. Thus, most managers do not understand what it is their vibration analysts are doing when they acquire their data with their "black boxes" and somehow find a number of problems that cannot necessarily be seen or heard.
In our case, surveys show that nearly 22% of our ISO Category I (Entry level) students hold management positions. In such cases, their plants or corporations have recognized the "knowledge gap" and have sent them to this entry level vibration class where they will have the opportunity of pushing buttons during hands-on exercises using several different analyzers, seeing what the PdM software does, and getting an introductory look at basic vibration fault detection analysis. In addition, they learn the terminology of basic vibration and how to understand the reports written by the PdM team documenting the problems found and recommending corrective actions as required (Most managers have told us that before taking this entry-level class, they truly did not understand what these reports were telling them, and did not have a good understanding of what vibration analysis could and could not do). Even though this is about all that is required of an ISO Category I class and exam, this experience gives the manager a feeling of confidence and some insight on what his PdM team analysts are doing and how they are making their diagnostic calls on likely problem sources and evaluating problem severity. Follow-up with clients who have had managers take the ISO Category I class has shown a much higher level of management support for an extended period of time, thereby allowing the PdM program to fully mature (various studies have found it requires approximately 3 years for a PdM vibration program to mature if the analysts obtain the training they must have). It should be noted that a much shorter time period is required for other PdM technologies such as ultrasound, infrared thermography, and similar tools due to a less steep and shorter learning curve than that of vibration.
Q. What methods do Technical Associates of Charlotte employ that sets it apart from other training organizations?
A. One thing separating Technical Associates from other training providers and consultants is that we maintain a whole staff of highly experienced vibration analysts and engineers here in our Charlotte office (called the Analytical Group). Each of our Analytical Group members (including both instructors and those who only go into the field) are experienced analysts having from 10 to 35 years vibration experience. Another thing setting us apart is that each of our instructors not only teach, but also go into the field and perform vibration analysis on a regular basis using a wide variety of analyzers and accompanying software. ("If you do not use it, you will lose it.") This is a decision we made when we began doing vibration training in 1988. Our instructors do vibration diagnostics, implement PdM programs, conduct acceptance tests, etc. We have been told by corporate management on several occasions that this is why they have chosen Technical Associates as their training provider (due to our continuing availability after a seminar is over and our remaining updated with the latest vibration analysis techniques and analyzers).
All of our instructors have been teaching vibration analysis seminars for at least 10 years for us and not only have considerable vibration experience, but also the ability to transfer their knowledge to our students. We also have the wonderful opportunity of working with hardware and software from many different major PdM suppliers and have even been allowed multiple opportunities to offer input into the development of such vibration products/tools. This gives our instructors broad expertise with many PdM systems, which benefits our seminar students who use vibration analyzers and software from a wide variety of suppliers. In addition, many years ago, Technical Associates made a commitment to hold virtually every public seminar we scheduled - and have been able to keep this commitment by holding approximately 98% of the classes over the past decade (teaching at least 100 classes per year for the last 6 consecutive years). Finally, when the class is over and the students have returned home, there is always someone here at our office from our Analytical Group to provide assistance and answer questions. This is an important point since students inevitably will have questions when they begin trying out the new techniques they have been taught using a wide variety of analyzers and supporting software (most of which we likely have).
Q. Have you seen the need for training grow or contract since the recent economic downturn?
A. In our particular case, the need for vibration training actually grew in 2010 despite the recession that most all the world has suffered. Probably the main reason is that during such times, unscheduled shutdowns of critical production or utility machinery cannot be afforded. Therefore, those plants and corporations who realized the power of vibration signature analysis made moves to ensure their PdM teams received the training they needed to detect faults and to prevent unscheduled failures or shutdowns. In our case, since we have the opportunity to teach so many persons holding management positions, and likewise are asked to speak at many corporate reliability conferences attended by key managers, engineers, etc., we had the distinct privilege of persuading noteworthy numbers of influential persons to persevere with (or even to enhance) their PdM programs during such difficult times. As evidence of this, during the period from October 1 through December 17, 2010 (normally a somewhat slow period), we held 31 seminars in a 10-week span (excluding Thanksgiving week), including both public and on-site classes. Our clients often told us during this time they needed such training to ensure they could maximize reliability and uptime of their machinery.
Q. What do you see over the next 10 years for Vibration Analysis and related training?
A. I had the privilege of acting as keynote speaker at the CMVA 2008 annual conference held October 28-31, 2008, during which I presented a comprehensive paper entitled "Greatest Events Within the Past 50 Years of Vibration Analysis" (CMVA is the Canadian Machinery Vibration Association). This paper has been updated since that time and not only takes a look at significant events in this fascinating vibration field, but also envisions some of the things that might occur in future years. Among the items we foresee are the following:
Improved Expert Diagnostic Rule-based Software Systems - Expert systems developed to date have generally not yet been potent enough to effectively detect a wide range of faults on a wide array of machinery types. Many of them generally require much time to input a noteworthy amount of configuration information about each machine, and some do not allow the analyst to either see or modify the rules used by the expert software to make certain diagnostic calls and offer recommendations. Much work still needs to be done to enhance expert rule-based software to make it the effective analytical tool it needs to be.
On-Board Display of Machine Photos - Showing measurement points and key machine information (i.e., RPM range, bearing manufacturer/model numbers, # of blades, # of gear teeth, etc.).
Wireless Sensors and Data Collectors - "Point and click" operation of analyzer to detect and identify specific permanently mounted wireless sensors and signal sensors to power up and acquire data from them (possibly using Bluetooth technology). Will increase data acquisition speed, and often improve safety.
"Smart" Sensors - Sensors that have built-in capabilities to actually acquire time waveforms and possibly convert these to FFT spectra. Some work is now being done to eventually outfit such sensors themselves with expert diagnostic capabilities.
Remote Diagnostic Analysis via the Internet - From mounted sensors for analysis in real time by highly skilled specialists. Might allow more timely and accurate analysis and decision support. This might even be performed at a corporate level with a team of specialists placed in a strategic "Situation Room" where data from literally thousands of machines from throughout the world can be evaluated. (At least one large corporation has begun this on a limited basis).
Linking of PdM and CMMS Systems - Work is now being accomplished to directly interface the output of PdM software with CMMS software systems, issuing work orders and tracking costs.
Artificial Neural Network (ANN) Possibly Combined with Vibration Expert Software Systems - To date, a number of rule-based vibration expert software systems have been developed with some success (typically requiring the user to input much configuration information about a specific machine train). I have had the opportunity to work with 5 or 6 vibration expert systems to date. An Artificial Neural Network (ANN) is an information processing system designed to mimic the way biological nervous systems, such as the brain, process information. The key capability of an ANN is that it theoretically can "learn" in a manner similar to a human being, and if combined with an expert software system, could theoretically be taught how to detect a number of machine faults by using pattern recognition of vibration spectra and waveforms in a manner similar to a human vibration analyst. A number of organizations have begun work on such systems (particularly those serving the military). Can such a system be successfully developed within the next 10 years (at least for a limited type of specific machine types that have specific failure patterns)? The answer is - possibly, as of this writing. However, in the opinion of the author, it will likely be quite a few years before such a system can be developed to operate without nearly continuous human guidance and interpretation at quite a high level.
Two things will likely have to occur with vibration training:
(a) Training must be developed and elevated to cover each of the above enhanced tools likely to be developed. Some of these topics will demand much field experience and research on the part of the training providers to adequately address these items.
(b) Many vibration analysts are "baby boomers" and will begin retiring during the next decade. Much will have to be done to ensure that those persons retiring pass on their knowledge to younger persons, including the very important task that already has major problems - learning how to properly establish meaningful measurement setups and alarm levels for a wide variety of machine types and operating speeds; and learning how to analyze acquired data, detect problems and correct problems. Once again, formal training at a minimum of ISO Categories I and II will be very needed to bridge the gap as the "new generation analysts" come up to speed.
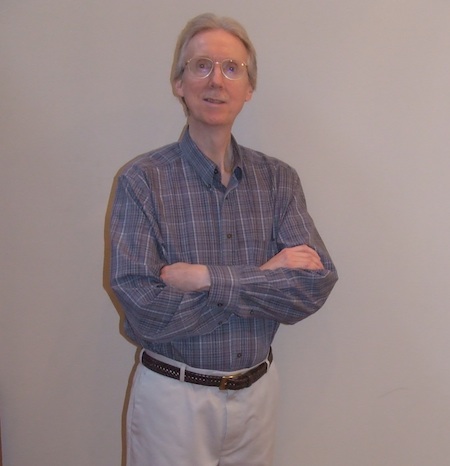
JAMES E. BERRY, P.E.
PRESIDENT
TECHNICAL ASSOCIATES OF CHARLOTTE, P.C.
Jim received his BS and Masters Degrees in Mechanical Engineering from N.C. State University. Jim has now authored 5 Seminar textbooks in vibration analysis, has 33 years vibration analysis experience and has evaluated numerous types of machines and structures. He has 22 years experience as a Vibration Analysis Instructor. Jim is also noted for development of the renowned "Illustrated Vibration Diagnostics Chart" that has been acquired by Vibration and Condition Monitoring engineers and technicians in 64 countries to date.
Contact Information:
James E. Berry, P.E.
President
Technical Associates of Charlotte, PC
Phone: 704-333-9011
Fax: 704-333-1728
Web: http://www.technicalassociates.net